Advanced Nuclear Reactor Technologies
JOHN F. KOTEK
Argonne National Laboratory-West
Idaho Falls, Idaho
For more than a decade, when energy experts considered which technologies would be used to meet future U.S. energy needs, nuclear power was largely ignored. This has changed in the last five years, as improved performance at existing plants has shown that well run nuclear plants can be a very low-cost source of baseload electrical generation. Increasing concerns about the effects of human activity on climate, coupled with a growing desire to ensure the security of U.S. energy supplies, have led to a renewed interest in nuclear power. Other countries, including Japan, China, South Korea, Russia, and Finland are pressing ahead with plans to add new nuclear generating capacity. However, before new nuclear plants can gain a foothold in the U.S. market, the economics of constructing new plants must be improved. In addition, the standing of nuclear energy in public consciousness would be elevated if new plants offered improved nuclear-waste management strategies and were demonstrably safer than existing plants. Finally, the expansion of nuclear energy to developing countries would be greatly facilitated if stronger intrinsic barriers to proliferation were built into new nuclear energy systems.
HOW NUCLEAR REACTORS WORK
A nuclear reactor produces electricity by harnessing the energy released during the splitting, or fission, of a heavy isotope, such as uranium-235 or plutonium-239. Fission can be induced when the nucleus of one of these isotopes absorbs a free neutron. When the isotope fissions, it generally splits into two smaller isotopes (referred to as fission products) and releases two or three neutrons and about 200 MeV of energy, about 20 million times the energy released
in a typical chemical reaction. The released neutrons can go on to fission another uranium or plutonium atom or can be captured in or escape from the reactor core. Power reactors are designed so the fraction of captured or escaped neutrons increases as the core temperature increases; the rate of fission reactions adjusts to maintain a nearly constant temperature, leading to a stable, self-sustaining chain reaction.
The core of a typical water-cooled reactor contains the fuel, usually uranium oxide pellets sealed in zirconium alloy cladding tubes. About 290 of these tubes are contained in a fuel assembly, and a typical core of a light-water reactor contains about 200 of these 3.5 m-long assemblies. The uranium or plutonium in the fuel is allowed to fission, and the energy released during fission is used to heat water. The heated coolant is then used, either directly or after one or more heat-transfer steps, to generate steam to drive a turbine, which generates electricity. A typical fuel assembly contains about 500 kg of uranium; if electricity sells for around 3 cents per kilowatt-hour, about $6 million of electricity would be generated over the life of the fuel assembly.
A SECOND LOOK AT NUCLEAR POWER
Several attractive features of nuclear power have aroused renewed interest in the United States. First, of course, nuclear fuel is very inexpensive compared to coal or natural gas. The nuclear fuel needed to power a 1,000 MWe plant costs about $40 million per year; the fuel for a similar-sized coal plant costs about $110 million and for a natural gas plant about $220 million (Reliant Energy, 2001). The low fuel cost more than offsets the higher operations and maintenance costs of nuclear plants. The average operations, maintenance, and fuel cost in 1999 for the 103 U.S. nuclear power plants was 1.83 cents per kilowatt-hour, lower than for coal plants (2.07 cents) and natural gas-fired plants (3.52 cents) (Utility Data Institute, 2001). Another attractive feature is that nuclear plants do not release air pollutants or carbon dioxide. Today nuclear plants provide 20 percent of U.S. electrical generation without burning fossil fuels or causing air pollution or an increase in greenhouse gases. These and other benefits, such as a small footprint per unit energy and a secure fuel supply, have put nuclear power back on the drawing board. To get beyond the drawing board, however, new nuclear power plants must overcome several hurdles.
The most challenging hurdle is the high capital cost of nuclear power plant construction. According to a 2001 report by the U.S. Department of Energy, overnight capital costs for a project must be contained at $1,500 per kWe or less (DOE, 2001). Capital costs for nuclear power plants completed in the 1980s and 1990s were in many cases several times higher, although a large fraction of the costs was interest that accumulated during construction delays. By comparison, capital costs for combined-cycle natural gas plants are currently about $500 per kWe.
Another hurdle, probably less important to the future deployment of new plants in the United States, but still significant, is the very small, but non-zero potential, for serious accidents. A third hurdle is the need for a repository to store used nuclear fuel. Finally, before nuclear power can be deployed on a wide scale, it may be necessary to reduce the potential for proliferation from civilian nuclear fuel cycles and to find better ways of managing used nuclear fuel.
NEAR-TERM PROSPECTS
No new nuclear power plants have been ordered in the United States since the 1970s, and no new plants have come on line since 1996. Despite this hiatus, work has continued on the development of more economical and safer reactor designs. Recent interest in new plants has been focused on two classes of new designs—water-cooled reactors and gas-cooled modular reactors.
Because of extensive experience in the construction and operation of water-cooled reactors and the relative maturity of the technology, advanced water reactors are, in my view, the most likely to be constructed in the United States in the near term. One promising design is the Westinghouse AP1000, an evolution of the AP600 pressurized light-water reactor plant that received U.S. Nuclear Regulatory Commission (NRC) design certification in 1999. The AP600 is a 600 MWe plant that incorporates several passive safety features (i.e., safety systems that work without requiring operator action), including passive safety injection, passive residual heat removal, and passive containment cooling. These passive systems are designed to improve safety and reduce the need for operator response in the event of an accident.
On April 2, 2002, Westinghouse submitted an application to the NRC for design certification of the AP1000 (Westinghouse hopes design certification can be achieved by the end of 2004). Westinghouse reports that more than 90 percent of the design for the plant has already been completed and that more than 80 percent of the AP600 Safety Analysis Report will remain unchanged for the AP1000. The thermal efficiency of the plant is about 32 percent, similar to existing pressurized-water reactors (Matzie, 1999).
The second class of reactors under consideration for near-term deployment is gas-cooled modular reactors. The two designs of this type that have elicited the most industry interest are the gas-turbine modular helium reactor (GT-MHR) under development by General Atomics and the pebble-bed modular reactor (PBMR), which is being designed by a team that includes British Nuclear Fuels Ltd., the parent company of Westinghouse. Instead of using the steam cycle to generate electricity, these reactors couple the reactor directly to a gas turbine. By using a direct Brayton cycle, efficiencies approaching 50 percent can be achieved. The units are small enough (300-600 MWt) to be mass produced in standardized units, which reduces capital costs while retaining safety character
istics. The small reactor and power-conversion units can be housed below ground, reducing the risk of man-made and natural hazards.
The fuel for a gas reactor uses tiny particles of uranium or plutonium oxide coated with carbon and silicon carbide. The particles create a barrier to the release of fission products and can withstand maximum attainable accident temperatures. The GT-MHR has a three-year operating fuel cycle—half of the fuel in the reactor core is replaced every 18 months while the reactor is shut down. By contrast, the PBMR has continuous refueling with the reactor in operation. Both designs use inert helium gas as a coolant.
LONG-TERM PROSPECTS
The U.S. Department of Energy is leading a 10-country effort to develop the next generation of nuclear energy systems. This program, known as Generation IV, will be guided by a technology roadmap being prepared by representatives of the 10 countries. The roadmap technical teams have evaluated many innovative concepts, including integral pressure-vessel water reactors and liquid metal-cooled fast-spectrum reactors.1
In integral pressure-vessel water reactors, the integral vessel houses reactor core and support structures, the core barrel, control-rod guides and drivelines, steam generators, a pressurizer, and reactor coolant pumps. This arrangement eliminates the need for separate steam generators, as well as a separate pressurizer, connecting pipes, and supports. Although the vessel is large (~18 m height and 4.4 m outside diameter), it is well within state-of-the-art fabrication capabilities. A 300-MWt reactor has 21 fuel assemblies inside a 2.6 m core barrel. Each assembly has about 440 pins in a square lattice. Integral-vessel reactors have lower power densities than light-water reactors, which allows for higher safety margins and longer core life, although they also have larger vessels and other structures. Projected system efficiencies are on the order of 36 percent.
The second class of innovative concepts is liquid metal-cooled fast-spectrum reactors (“fast-spectrum” refers to the energy of the neutrons in the reactor core). In a typical reactor, a moderator (usually water, which pulls double-duty as both neutron moderator and reactor coolant) is used to slow down neutrons because slower neutrons are more efficient at causing fission in U-235. In a fast-spectrum reactor, there is no moderator. Instead, it relies on higher energy neutrons, which are less effective at causing uranium to fission but are more effective at causing fission in plutonium and other heavy elements. For this reason, these reactors are not ideal for a uranium-based fuel cycle; but they are quite suitable for use with a fuel cycle based on plutonium and the other heavy
1 |
An overview of the roadmap was released in September 2002, and can be found at http://nuclear.gov. |
elements that accumulate in spent fuel. Therefore, fast reactors could play a vital role in a long-term nuclear energy system that recycles used fuel to minimize long-lived waste.
Most fast-spectrum reactors operated around the world use liquid sodium metal as a coolant. Future fast-spectrum reactors may use lead or a lead-bismuth alloy, or even helium, as a coolant. One of the attractive properties of metals as coolants is that they offer exceptional heat-transfer properties; in addition, some (but not all) metal coolants are much less corrosive than water. However, because sodium is reactive with air and water, fast-spectrum reactors built to date have a secondary sodium system to isolate the sodium coolant in the reactor from the water in the electricity-producing steam system. The need for a secondary system has raised capital costs for fast reactors and has limited thermal efficiencies to the range of 32 to 38 percent. Novel steam-generator designs, direct gas cycles, and different coolants are options that may eliminate the need for this secondary sodium loop and improve the economics of fast reactors (Lake et al., 2002).
The Generation IV group is looking at complete nuclear energy systems, not just reactors, which are only one part of the nuclear fuel cycle (the path of uranium from the mine through fuel fabrication and use and disposal or recycling). Because of concerns about proliferation, recycling of spent nuclear fuel was banned in the United States in April 1977; spent fuel is recycled in France, Japan, the United Kingdom, Russia, and elsewhere. The U.S. strategy for managing used nuclear fuel is to isolate it from the environment in canisters placed in a deep geologic repository; Yucca Mountain in Nevada has just been approved for this purpose. In an attempt to keep options for the long term open, Generation IV is revisiting the issue of recycling used fuel.
Nuclear fission produces a lot of heat, which can be used for more than making electricity. Several nuclear power plants around the world also provide heating for homes or for desalinating water. In the future, nuclear power plants may make a larger contribution toward meeting nonelectrical energy needs by supplying heat for industrial processes and by producing hydrogen. The advantages of hydrogen as an energy carrier have been widely publicized, but we must find ways of producing enough hydrogen to meet our needs. Currently, more than 95 percent of the hydrogen produced for refineries and chemical plants comes from the cracking of natural gas, a process that releases carbon dioxide. In the near term, nuclear-generated electricity could be used to drive electrolyzers that split hydrogen from oxygen, which would release almost no carbon dioxide. In the long term, higher temperature reactors could be used to produce heat to drive thermochemical water-cracking cycles, a process that could be nearly twice as efficient as electrolysis.
CONCLUSION
Existing nuclear power plants are a cost-effective and nonemitting contributor to the world energy system. Advanced nuclear energy systems can make a large contribution to meeting future energy needs, but the economics of these systems must be improved without compromising safety. In the long term, next-generation systems could contribute not only to our electricity needs, but also to our need for clean fuels for transportation and industry. The successful deployment of new nuclear energy systems could be a key part of a sustainable energy system.
REFERENCES
DOE (U.S. Department of Energy). 2001. A Roadmap to Deploy New Nuclear Power Plants in the United States by 2010. Washington, D.C.: U.S. Department of Energy.
Lake, James A., R.G. Bennett, and J.F. Kotek. 2002. Next generation nuclear power. Scientific American 286(1): 72-79.
Matzie, Regis. 1999. Westinghouse’s advanced boiling water reactor program. Nuclear Plant Journal Editorial Archive. Available online at: <http://npj.goinfo.com/NPJMain.nsf> (October 30, 2001).
Reliant Energy. 2001. Reliant Energy HL&P’s Nuclear Plant Has Lowest Fuel Costs of All Power Plants in the U.S. Available online at: <http//www.reliantenergy.com/news/pressreleases/press_release_225.asp> (July 25, 2001).
Utility Data Institute. 2001. Nuclear Energy Surpasses Coal-Fired Plants as Leader in Low-Cost Electricity Production. Available online at: <http://www.nei.org/doc.asp?catnum=4&cat-id=304> (January 9, 2001).
Licensing and Building New Nuclear Infrastructure
PETER S. HASTINGS
Duke Energy
Charlotte, North Carolina
Electricity demand is outpacing supply growth, and experts have calculated that the United States will need new baseload power generation (including nuclear power generation) by 2010 (NEI, 2002a). As part of the Nuclear Power 2010 Initiative, the U.S. Department of Energy (DOE) established the Near-Term Deployment Group (NTDG) to examine prospects for new nuclear plants in the United States in the next decade. According to a recent study by NTDG, a resurgence of the nuclear industry will be influenced by many factors, including economic competitiveness; deregulation of the energy industry; regulatory efficiency; existing infrastructure; the national energy strategy; safety; management of spent fuel; public acceptance; and nonproliferation (DOE, 2001). NTDG also noted that the nuclear industry is experiencing current shortfalls in several important areas (DOE, 2001):
-
Qualified and experienced personnel in nuclear energy operations, engineering, radiation protection, and other professional disciplines.
-
Qualified suppliers of nuclear equipment and components [including] fabrication capability and capacity for forging large components such as reactor vessels.
-
Contractor and architect/engineer organizations with personnel, skills, and experience in nuclear design, engineering, and construction.
Nuclear industry infrastructure can be defined in terms of technologies, facilities, suppliers, and regulatory elements; design and operational engineering and licensing tools; and (perhaps most important) human capital to sustain the
industry in the near and long terms. NTDG concluded that, although the industry has adequate industrial and human infrastructure today to build and operate a few new nuclear plants, we cannot be sure that this infrastructure can be expanded quickly enough to achieve the goal of 50 GWe in new nuclear plant installed capacity as laid out in the industry’s strategy for the future, Vision 2020 (NEI, 2002a).
The nuclear industry faces infrastructure challenges, untested implementation of new Nuclear Regulatory Commission (NRC) regulations, and uncertainties about the economic competitiveness of new nuclear plants. The near-term deployment of new nuclear-power generation will be a good litmus test of the viability of a larger expansion in nuclear production. According to NTDG, even though the level of additional capacity in the industry goals in Vision 2020 is meager in terms of overall U.S. energy needs, achieving the goal presents major challenges (DOE, 2001).
INDUSTRY AND GOVERNMENT INITIATIVES
Various initiatives have been undertaken by the U.S. nuclear industry and DOE to encourage the domestic development of additional nuclear facilities. In 1998, DOE chartered the Nuclear Energy Research Advisory Committee (NER-AC) to advise the agency on nuclear research and development (R&D) issues. NERAC released the Long-Term Nuclear Technology R&D Plan in June 2000 (NERAC, 2000); NERAC is also responsible for overseeing the development of plans for both NTDG and Generation IV, a project to pursue the development and demonstration of one or more “next-generation” nuclear energy systems that offer advantages in economics, safety, reliability, and sustainability and that could be deployed commercially by 2030 (DOE, 2002). In 1999, DOE initiated the Nuclear Energy Research Initiative (NERI), an R&D program to address long-term issues related to nuclear energy; in 2000, the Nuclear Energy Plant Optimization Program was initiated to focus on the performance of currently operating nuclear plants.
In 2000, NEI formed the industry-wide New Nuclear Power Plant Task Force to identify the market conditions and business structures necessary for the construction of new nuclear power plants in the United States. In April 2001, the task force published the Integrated Plan for New Nuclear Plants, which includes a discussion of nuclear infrastructure (NEI, 2001). More recently, NEI announced Vision 2020, an initiative with a goal of adding 50,000 MW of new nuclear generating capacity by 2020, along with increases in efficiency power uprates at existing plants equal to an additional 10,000 MW of generating capacity (NEI, 2002b).
DOE funding has recently been allocated to advanced reactor development, specifically for the exploration of government/industry cost sharing for the demonstration of early site permitting as part of new NRC licensing processes (which
also include provisions for combined licenses and design certifications) and for national laboratory activities associated with fuel testing, code verification and validation, and materials testing associated with new reactor designs (DOE, 2001).
TECHNOLOGICAL INFRASTRUCTURE
A number of elements are required to support a new or existing nuclear plant. Suppliers and fabricators of nuclear fuel and safety-related components are clearly essential, as are suppliers of balance-of-plant equipment, construction materials, electronics and instrumentation, and countless other components.
The U.S. fuel-cycle industry has undergone significant changes in the past few years. Future fluctuations in uranium prices, the deployment of new enrichment technologies, significant consolidation of fuel-cycle supply companies, and the possible recycling of spent fuel could all affect the supply chain for nuclear fuel (i.e., mining/milling, conversion and enrichment, and fabrication into ceramic fuel pellets). The NTDG study recognized the sensitivity of new reactor deployment to these factors. NTDG solicited designs for nuclear plants that could be deployed by 2010 and attempted to identify generic issues that could impede their deployment. Proposals were received from reactor suppliers identifying eight candidate reactor designs. NTDG evaluated these designs to determine the prospects for deployment of a new nuclear plant in the United States by 2010. Candidate reactor technologies were required to demonstrate how they would operate “within credible fuel-cycle industrial structures” assuming a once-through fuel cycle using low-enriched uranium fuel and to “demonstrate the existence of, or a credible plan for, an industrial infrastructure to supply the fuel being proposed.” NTDG’s design-specific evaluations concluded that the candidates that would use existing fuel-cycle infrastructure could be built by 2010. However, NTDG also concluded that infrastructure expansion to achieve the industry’s goal of 50 GWe of new installed capacity by 2020 was a “generic gap” that warrants government and industry action (DOE, 2001).
Siting for new reactors will be greatly influenced by how efficiently 10 CFR Part 52 (the NRC regulation for early site permits, standard design certifications, and combined nuclear plant licenses) can be implemented. NTDG concluded that the federal commitment to cost sharing via government/industry partnerships should include a demonstration of the NRC’s early site permit process for a range of likely scenarios. Recently a partnership to evaluate sites for new nuclear plants was announced, and DOE selected three utilities to participate in joint government/industry projects to pursue NRC approval for sites for new nuclear power plants. These projects, the first major elements of DOE’s Nuclear Power 2010 Initiative, are intended to “remove one more barrier to seeing the nuclear option fully revived” in the United States. All three companies intend to seek early site permit approvals that would enable them to locate new, advanced-
technology nuclear plants at sites owned by the utilities that currently host commercial nuclear power plants (i.e., Dominion Energy’s North Anna site in Virginia, Entergy’s Grand Gulf site in Mississippi, and Exelon’s Clinton site in Illinois). According to a press release on June 24, 2002, DOE expects applications to be submitted by late 2003.
Design concepts for the waste-management component of fuel-cycle infrastructure were also evaluated by NTDG. Each design concept addressed the on-site storage of spent nuclear fuel; but the current lack of a national system for high-level waste disposal is a programmatic gap common to all new technologies. The Nuclear Waste Policy Act (first passed in 1983, amended many times, and still the subject of heated debate) provides for the development of the Yucca Mountain site in Nevada as a mined, geologic repository for high-level waste and the development of a transportation system linking U.S. nuclear power plants, an interim storage facility, and the permanent repository (NEI, 2002c).
The recycling of spent fuel to recover fissile material and long-lived heavy elements would reduce the heat generation and volume of final waste products. When most existing U.S. nuclear plants were built, the industry—encouraged by the federal government—planned to recycle used nuclear fuel by recovering plutonium. In 1979, however, the United States deferred the reprocessing of all commercial used nuclear fuel because of concerns about the possible proliferation of nuclear weapons. Thus, the industry was forced to adopt a once-through, single-use fuel cycle. Reprocessing and recycling are not currently cost effective in the United States, and most of the discussion about recycling is now focused on increasing the capacity of waste repositories and the transmutation of actinides.
The domestic supply of certain reactor components is another long-term concern. Over time, U.S. capacity for fabricating large components with long lead times (e.g., reactor vessels and steam generators) has diminished. NTDG concluded that in most cases, other countries have the necessary capacity and could support the early expansion of nuclear plant construction in the United States, but domestic capabilities will also have to be reestablished (DOE, 2001). General Electric, for example, has indicated that many of the components and much of the hardware (including pumps, heat exchangers, nuclear fuel, control rods, and some internal reactor components, as well as most balance-of-plant equipment) for its advanced boiling water reactor (ABWR) can be produced in the United States. However, the reactor pressure vessel and the large internal components (the same components used for Japanese and Taiwanese ABWRs) will have to be fabricated by foreign suppliers that have maintained their capacity and expertise for fabricating and machining these large components. Foreign suppliers can and do meet U.S. codes and regulations; most foreign countries follow identical or similar codes, such as ASME Section III, IX, and XI, as well as U.S. NRC-imposed regulations and guidelines. NTDG concluded that this area of infrastructure will have to be reconstituted in the United States for eco
nomic reasons and that, for some components (particularly reactor vessels), the existing worldwide capacity may not be adequate to support a large expansion of reactor capacity.
REGULATORY INFRASTRUCTURE
NRC is perhaps best known for regulating reactor construction and operation. The agency also regulates nuclear fuel-cycle operations, including the mining, milling, conversion, enrichment, and fabrication of fuel and waste-management facilities. A number of proposed licensing actions and regulatory initiatives are currently under way at the NRC. The most important in terms of near-term continuity in the nuclear industry and adequate energy supply is the renewal of reactor licenses. NRC regulations limit commercial reactor licenses to an initial 40 years (based on economic and antitrust considerations) but also allow licenses to be renewed (NRC, 2002). The license renewal process involves confirmation that structures, systems, and components can continue to perform safely beyond the original term of the operating license.
License renewal is important for maintaining a significant portion of existing energy production. Currently licensed nuclear reactors generate approximately 20 percent of the electric power produced in the United States. The first plant will reach the end of its original license period in 2006; approximately 10 percent will reach 40 years by the end of 2010; and more than 40 percent will reach 40 years by 2015. As of June 2002, 10 license renewal applications had been granted, and 14 applications were under NRC review; 23 more applications are expected by 2005. License renewal also provides an important collateral benefit by keeping the industry and workforce energized and engaged, thus helping to preserve the institutional and human capital that will be necessary for the near-term deployment of new reactors.
Other high-profile licensing actions related to nuclear industry infrastructure include: an application for a license for a spent-fuel storage facility currently before the NRC and in hearings submitted by Private Fuel Storage (a group of eight electric utility companies in partnership with the Skull Valley Band of Goshute Indians); two pending applications (one from the United States Enrichment Corporation and one from Urenco) for deploying new gas-centrifuge enrichment technologies in the United States; and an application for the construction and subsequent operation of a facility to convert surplus weapons material into commercial fuel as part of an agreement between the United States and Russia to dispose of more than 60 metric tons of surplus plutonium.
A key aspect of regulatory development for near-term deployment is the efficient implementation of 10 CFR Part 52. Created in 1989, this regulation established three new licensing processes for future plants: early site permitting (i.e., NRC approval of a site before a decision has been made to build a plant); design certification (i.e., NRC approval of a standard design); and combined
licenses (i.e., a combined construction permit and operating license). These processes could provide a dramatic improvement over the two-step process used for existing U.S. plants. NRC has stated that an application for a combined license that references an early site permit and a certified reactor design could result in an operating license being granted in as little as one year (Jeffrey S. Merrifield, NRC commissioner, remarks to American Nuclear Society Conference, June 7, 1994). In actuality, however, only the design certification process has been demonstrated thus far, and it has taken as long as 10 years.
Not surprisingly, NTDG has called the efficient implementation of 10 CFR Part 52 a high priority for short-term deployment and a matter that requires the attention of industry and government. NTDG recommends that four actions be taken: the expediting of the design certification process; the demonstration of the early site permit and combined license processes; the development of generic guidelines to ensure the efficient, safety-focused implementation of key Part 52 processes; and a demonstration of progress toward a new risk-informed, performance-based regulatory framework (DOE, 2001).
DOE’s recently announced plans to work in partnership with industry to evaluate sites for new nuclear plants will test the early site permitting component of this regulation. DOE proposes that near-term investments be made as part of the Nuclear Power 2010 Initiative, in part to “demonstrat[e] this key NRC licensing process” (DOE press release, June 24, 2002).
Another evolving area of regulatory infrastructure is NRC’s effort to “risk-inform” their regulatory processes. The intent is to improve the regulatory process by incorporating risk insights into regulatory decisions, thereby conserving agency resources and reducing unnecessary burdens on licensees. The risk-informed approach combines risk insights and traditional considerations to focus regulatory and licensee attention on the design and operational issues that are most important to health and safety (NRC, 2001).
In the context of the efficient implementation of 10 CFR Part 52, NTDG calls for a new regulatory framework that is fully risk-informed and performance-based and “go[es] beyond the ongoing efforts to risk-inform 10 CFR Part 50 for current plants” to improve the protection of public health and safety, eliminate regulatory burdens that do not contribute to safety, and “increase the confidence of prospective applicants in the regulatory environment for new plants and encourage business decisions to proceed with new nuclear projects” (DOE, 2001).
ENGINEERING AND LICENSING TOOLS
The skills necessary for the development of new infrastructure are largely the same as those necessary for the maintenance of existing facilities. In fact, efforts to continue improving existing facilities not only provide a performance benefit to facility stakeholders, they also help ensure that human and technolog
ical resources will be available for the development of new facilities. Thus, ongoing improvements to existing facilities are extremely important. From 1990 to 2000, for instance, improved efficiency at U.S. nuclear power plants provided the production equivalent of constructing 22 new 1,000-MW power plants— enough power to provide 22 percent of new electricity demand during that decade (NEI, 2002d). So, not only are there ample economic reasons for continuing to pursue improvements, there are also substantial collateral benefits, such as ensuring the ongoing development of technological tools and the engagement of human capital in nuclear technologies.
COMPUTER TECHNOLOGY
The most dramatic contributor to changes in design tools in the last 25 years has been computer technology. With today’s computational speeds, optimization and simplification of new plant design and construction seems to be limited only by the imagination. One has only to compare modern development tools to historical methods to appreciate the change.
Core physics simulations provide a good example. In the 1970s, a typical simulation used a lattice-cell code that modeled a single fuel pin (or rod) surrounded by an infinite array of homogenized media created to look like the adjacent pins. Approximations were used to model assembly-averaged thermal-hydraulic effects and axial representations, and in-core fuel management was performed by trial-and-error shuffle schemes, using manual iterations until cycle length and power peaking requirements were met.
Modern design software typically uses a two-dimensional code that models a full fuel assembly and uses advanced ray tracing, collision probability, or Monte Carlo techniques. The core simulator is a three-dimensional advanced nodal code with pin reconstruction techniques and explicit thermal-hydraulic modeling and is capable of three-dimensional space-time calculations. Core-loading pattern development has been automated, using advanced nodal codes coupled with simulated annealing techniques to develop core-loading patterns that meet predetermined limits on pin peaking, cycle length, and other attributes to minimize fuel cost within applicable core physics limits.
Another dramatic example of the benefits of increased computer power is the advent of computer-aided design (CAD) and engineering, which not only have enabled the development of increasingly complex and sophisticated civil/ structural models, but have also significantly eased the burden of physical-interference modeling and facility-configuration control. Designs in the 1970s were modeled primarily on paper and required hundreds of individual drawings. Plastic and wooden scale models were often painstakingly fabricated and maintained (see Figure 1 ) to help identify costly interferences between electrical, mechanical, and structural components that could be missed in two-dimensional drawings and to assist with the visualization of designs and changes to those designs.
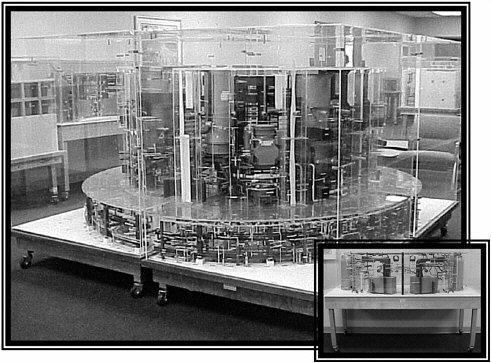
FIGURE 1 Scale model for the McGuire Nuclear Station Reactor fabricated to help identify interferences. Source: Photo courtesy of Duke Energy.
In the last decade or so, the development of more and more sophisticated models (see Figure 2) as the basis of design has improved the coordination of drawings, accelerated the communication of design alternatives, and significantly reduced the requirements for field reworking (Bernstein, 2001).
Using a central data representation results in improved integration and coordination among various design documents and between design disciplines. In addition, procurement, construction, and subsequent ongoing configuration-management of the facility—a key aspect of the design, licensing, operation, and maintenance of a nuclear facility—have been greatly facilitated (Bernstein, 2001).
HUMAN INFRASTRUCTURE
One of the most important aspects of nuclear infrastructure, particularly for a domestic resurgence of the industry, is the development of human resources. The nuclear industry faces the dual challenge of an aging workforce and a growing gap between its employment needs and the number of graduating students. Replacement of the aging workforce is essential for both existing plants and new facilities.
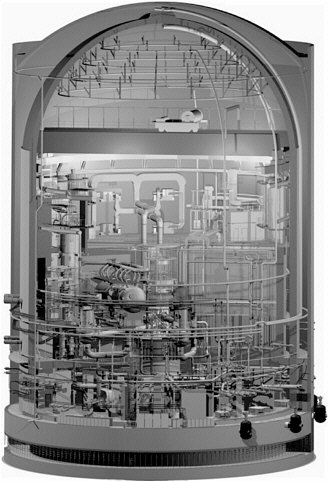
FIGURE 2 Model of 1,000-MW reactor (Lianyungang Unit 1), Elias Mayer, Fortum Engineering, Ltd., Vantaa, Finland. Source: Graphic courtesy of Intergraph Process, Power & Offshore.
NTDG cited key initiatives dealing with human resources at DOE, the Nuclear Energy Institute (NEI), and the American Nuclear Society and recommended that these initiatives be maintained and strengthened (DOE, 2001). On June 10, 2002, DOE announced the establishment of a new program, Innovations in Nuclear Infrastructure and Education, that offers several million dollars in awards to university consortia to encourage investments in programs on research reactors and nuclear engineering and in strategic partnerships with national laboratories and industry. At the same time, DOE announced that it would award more than 100 scholarships, fellowships, and grants to nuclear science/engineering institutions and students.
Other public and private efforts to bolster the educational infrastructure for
the nuclear industry are under way throughout the United States. As a result, almost every university and national laboratory associated with nuclear science and engineering now offers scholarships and fellowship programs.
CONCLUSION
The potential for a resurgence of the nuclear industry in the United States is a function of many factors. New technologies continue to be developed, but key areas of infrastructure to support expansion must be maintained and (in many cases) expanded for a future nuclear option to be sustainable. Although significant challenges lie ahead, a number of government, industry, and joint public/ private efforts are under way to facilitate this expansion. The reestablishment of the industrial infrastructure that supplies materials and components, the continued improvement and demonstration of effective regulatory processes, and the development of essential human resources are all critical factors to the future of the nuclear industry in the United States.
ACKNOWLEDGMENTS
The author gratefully acknowledges the support and assistance of Dr. Per Peterson (University of California, Berkeley), Richard Clark (Duke Energy), and the Process, Power, and Offshore Division of Intergraph Corporation.
REFERENCES
Bernstein, P. 2001. 2D to 3D Challenge: Autodesk on Architectural Desktop. London: CADDesk.
DOE (U.S. Department of Energy). 2001. A Roadmap to Deploy New Nuclear Power Plants in the United States by 2010. Washington, D.C.: U.S. Department of Energy.
DOE. 2002. Generation IV website. Available online at: <http://gen-iv.ne.doe.gov>.
NEI (Nuclear Energy Institute). 2001. Integrated Plan for New Nuclear Plants. Washington, D.C.: Nuclear Energy Institute.
NEI. 2002a. Vision 2020 Booklet. Available online at: <www.nei.org/documents/Vision2020Booklet.pdf>.
NEI. 2002b. Industry Projects to Build New Nuclear Plants. Available online at: <www.nei.org>.
NEI. 2002c. National Used Nuclear Fuel Management Program. Available online at: <www.nei.org>.
NEI. 2002d. Plant Improvement Programs. Available online at: <www.nei.org>.
NERAC (Nuclear Energy Research Advisory Committee). 2000. Long-Term Nuclear Technology R&D Plan. Washington, D.C.: Nuclear Energy Research Advisory Committee.
NRC (Nuclear Regulatory Commission). 2001. Risk-Informed Regulation Implementation Plan. Washington, D.C.: Nuclear Regulatory Commission.
NRC. 2002. Reactor License Renewal Overview. Available online at: <www.nrc.gov/reactors/operating/licensing/renewal/overview.html>.
Sustainable Energy from Nuclear Fission Power
MARVIN L. ADAMS
Department of Nuclear Engineering
Texas A&M University
College Station, Texas
Increases in world population and per-capita energy demand in the next few centuries are expected to cause a substantial rise in world energy use. The World Energy Council predicts a doubling of consumption to 800 EJ/yr (EJ = exaJoule = 1018 J) by 2050 (WEC, 2002). For energy production to be sustainable, input requirements (including construction materials) must be available at reasonable financial and environmental cost, and the waste stream must have acceptably low economic and environmental impacts. No production option has yet demonstrated the ability to meet a substantial fraction of projected demand sustainably: every option needs further research and development. In this paper, I summarize options for sustainable energy production, discuss the need for a significant contribution from nuclear fission and its potential for providing such a contribution, and identify some challenges that must be met to achieve that potential.
OPTIONS
In the following discussion of the relative merits of energy technologies hundreds of years into the future, we draw seemingly reasonable conclusions based on some fundamental truths. However, the possibility of unforeseen technological developments over such a long period of time introduces considerable uncertainty. With that caveat in mind, let us boldly proceed.
The vast majority of the world’s energy in the coming centuries will come from a few sources: fossil fuels, the sun, biomass, wind, geothermal sources, nuclear fission, and (potentially) nuclear fusion. Table 1 provides an overview of the general suitability of each of these sources for sustainable energy produc
TABLE 1 Comparison of Energy Sources
Source |
EJa/yr today |
Reservesa |
Use of other resources |
Waste |
Comments |
Oil / natural gas liquidsb |
140 |
> 6 ZJ |
|
CO2 and other emissions |
Not considered sustainable |
Natural gas |
85 |
> 5 ZJ |
|
CO2 and other emissions |
Not considered sustainable |
Coal |
90 |
30 ZJ |
Land = moderate (mines) |
CO2 and other emissions |
Reserves greater than oil or gas, but much less than fission |
|
|
|
Construction = 0.7c |
|
|
Biomass |
55 |
Up to 270 EJ/yr sustainable |
Land = high |
Particulates and other emissions |
R&D may help somewhat |
Nuclear fission |
28 |
> 600 ZJ |
Land = low |
Long life |
Small waste volume |
|
|
|
Construction = 0.7 |
Repository space Proliferation |
Space is political issue, not technical |
Hydroelectric power |
9 |
30 EJ/yr sustainable |
Land = high (lakes) |
|
Inherently small role |
Solar energy |
Small |
|
Land = high |
|
R&D may help somewhat |
|
|
|
Construction = 30−80 |
|
|
Wind |
Small |
|
Land = high |
|
Inherently diffuse source |
|
|
|
Construction = 5−15 |
|
|
Geothermal energy |
Small |
<100 EJ/yr sustainable |
|
|
|
Nuclear fusion |
0 |
Enormous |
|
|
Not yet demonstrated |
|
tion. Because the anticipated demand is high and because different technologies are better for different applications, it is likely that all of these sources will be tapped.
Economically recoverable oil and natural gas will probably be depleted within a century or two, and both have attractive applications besides energy production. Thus, I will not consider them as sustainable energy sources. The burning of coal produces a great deal of carbon dioxide (CO2), a greenhouse gas. For coal to be a sustainable long-term energy option, either we must find a way to economically sequester the CO2 (300 kg/s from each 1-GWel power plant) or the world must decide that the addition of vast quantities of CO2 to the atmosphere is environmentally acceptable. The burning of biomass also releases CO2, but the same CO2 is then captured by the growth of new matter. Thus, biomass does not add to atmospheric CO2 levels. The greatest drawbacks of biomass are its large land use (according to the World Energy Council estimate, a sustainable 270 EJ/yr would require a crop area larger than the continental United States) and its high level of particulate and other emissions. Hydroelectric power is renewable and emission-free but limited to 30 EJ/yr, at most, by the availability of sites for dams. The sun seems to offer an almost limitless emission-free source of energy, and the role of solar power in the future energy supply will surely be significant, especially for small-scale local applications. However, solar energy is a diffuse source that requires large land areas, and its use of engineering materials is high per unit of energy produced. Technological advances will help, but the low energy density of solar radiation is a fundamental limitation that will be difficult to overcome for large-scale generation. Wind power is less material intensive than solar energy and will play an increasingly important role, but wind is also limited by its low energy density and relatively high land use. Other renewables, such as geothermal energy, have similar limitations. The technology for large-scale generation from nuclear fusion appears to be decades away, and its costs are uncertain. Although fusion has enormous potential, it is not yet clear how its advantages and disadvantages will compare to those of other options, including nuclear fission.
Each of these options has drawbacks, and each has positive features. Most of the drawbacks of any option can be overcome if we are willing to pay enough (in dollars, land, materials, etc.). It is reasonable to conclude that we should continue to develop all options and that all of them will be needed to some extent to meet the energy demand in the coming centuries.
SUSTAINABLE FISSION ENERGY
Potential
The known economically recoverable 3.3 million metric tons of uranium (WEC, 2001) and 4 to 6 million metric tons of thorium (UNDP, 2000) could
produce 250 ZJ (zettaJoule) and 350 to 500 ZJ, respectively, if used to their full potential. Thus, more than 600 ZJ of potential nuclear fission energy—1,500 times the current total worldwide annual energy consumption—is readily available. Much more easily recoverable thorium will surely be found if a demand develops (Rubbia et al., 1995). An additional 7 million metric tons of uranium is estimated but not yet proven to be economically recoverable (WEC, 2001). Fission power uses little land and requires modest construction inputs (mainly concrete and steel) per unit of energy produced—lower than the construction inputs for wind and solar energy by factors of 10 and 100, respectively (AWEA, 1998). Thus, as far as inputs are concerned, fission power has the potential to provide a large fraction of the world’s energy for many, many centuries. However, tapping the full potential energy of uranium and thorium resources will require changes from current fission-energy practice, including the use of “high-conversion” reactors and the recycling of fissionable isotopes.
The output from fission power includes modest amounts of chemical and low-level radioactive wastes, which are relatively easy to handle, as well as used (“spent”) fuel, which is the main disposition challenge. Spent fuel from today’s power reactors contains approximately 5 percent fission products (atoms produced by splitting another atom or by radioactive decay of another fission product), 2 percent “fissile” material (including 235U, 239Pu, and 241Pu), and 1 percent other actinides (including 238Pu and 241Am), with 238U comprising most of the remaining mass. (“Fissile” means the atom is likely to fission after absorbing any neutron, including a low-energy neutron.) Note that fission power produces a very small volume of spent fuel. With current technology, six years of operation of a 1-GWel plant yields spent fuel that could fit inside a 4-meter cube, and the vast majority of this material is recyclable. If we recycle, which is essential for the substantial use of uranium and thorium resources, then much less material will require disposal, and most of it will have a much shorter half-life.
Tapping the Energy
In the current “once-through” fission fuel cycle in the United States, uranium fuel that is enriched to 3 to 5 percent in the 235U isotope remains in a power reactor for four to six years, after which it is treated as waste. In the enrichment process, each kilogram (kg) of natural uranium (which is 0.7 percent 235U) is typically converted to 0.85 kg of “depleted” uranium (0.2 percent 235U) and 0.15 kg of low-enriched uranium (3.5 percent 235U). Thus, only 15 percent of the mined uranium reaches a reactor. During its four to six years in the reactor, approximately 5 percent of the atoms in the uranium fuel fission. Thus, current practice releases only 0.75 percent (5 percent of 15 percent) of the potential energy of the mined uranium; a great deal of the energy-storing material is treated as waste.
Essentially all natural thorium is 232Th, and 99.3 percent of natural uranium
is 238U. These isotopes are not fissile—they do not fission when they absorb low-energy neutrons—and neither can fuel a reactor by itself. Both are fissionable (absorption of MeV-range neutron can cause fission) and fertile (capture of a neutron leads to a new fissile atom). To unlock the energy from uranium and thorium resources, the abundant fertile isotopes (238U and 232Th) must be converted into fissile isotopes (239Pu and 233U, respectively). This is simple: if either 238U or 232Th captures a neutron, it quickly converts via beta decay:

(1)

(2)
The conversion ratio of a reactor is the production rate of fissile atoms (by conversion of fertile atoms) divided by the consumption rate of fissile atoms (by fission or other neutron-induced destruction). A reactor with a conversion ratio greater than unity is sometimes called a breeder reactor. Unlocking all of the potential energy in 238U and 232Th will require high-conversion reactors.
High-conversion reactors have been demonstrated for both 239Pu/238U and 233U/238Th cycles; however, this technology is not as mature as the technology used in current commercial reactors. There are opportunities for innovation in many aspects of the design of high-conversion reactors, including materials (for higher-temperature operation and improved resistance to corrosion and radiation damage), fuel form (e.g., oxide, metal, molten salt), and coolant (e.g., liquid metals, helium). Innovations will undoubtedly improve the technology, but even today it is clear that high-conversion reactors can be designed and operated for sustainable fission power.
To take advantage of high-conversion reactors that convert fertile material to fissile material, we must recycle the new fissile material into new fuel. In fact, to maximize the energy and minimize the waste from uranium and thorium, all actinides (not just fissile isotopes) should be recycled so that as many heavy atoms as possible can fission. This will require reprocessing spent fuel, separating out the desired elements, and using reactors that can cause most of the actinides to fission. Reprocessing is a commercial practice in England and France, as is highly efficient (> 99.8 percent) extraction of uranium and plutonium. Efficient extraction of other actinides has been demonstrated on a laboratory scale, and research and development are under way to improve these technologies and move them to commercial scale.
Because of the mix of fissile and fissionable isotopes that develops after several recycling steps, fuel from multiple recycling steps is best suited for fast-spectrum reactors. In a fast-spectrum reactor, neutrons retain relatively high energy from birth (via fission) to death (via absorption or escape). Fast-spec
trum reactors can cause nonfissile actinides to fission, whereas other reactors have trouble doing so. High-conversion reactors can be fast-spectrum reactors, and thus could be both creators of fissile material and burners of nonfissile actinides.
Handling the Waste
If a substantial majority of the actinides are recycled and made to fission in fast-spectrum reactors, the remaining waste will be mainly fission products. Most fission products decay with half-lives of decades or shorter, and after 300 years the total fission-product inventory decays to a radiotoxicity level lower than that of the original ore (OECD, 1999). Fission products can be immobilized in glass; this is done commercially in England and France. The waste-containing borosilicate glass is so insoluble that if it were immersed in water, only 0.1 percent would dissolve in 10,000 years. Thus, it is not difficult to immobilize fission products for several hundred years, after which they are no more harmful than the original ore that nature placed underground. The waste-containing glass can be isolated, for example, in stable underground geologic formations.
If we wanted to reduce the radiotoxicity of fission products even further, we would need to address the fission products with long half-lives. The fission products that contribute most to long-term radiotoxicity are 99Tc and 129I, which have half-lives of 2.1×105 and 1.6×107 years, respectively. These isotopes could conceivably be separated from other fission products and transmuted (by absorption of neutrons from accelerators, reactors, or accelerator-driven subcritical assemblies) into shorter-lived isotopes (NRC, 1996; OECD, 2002). A recent study concludes that both of these isotopes could be transmuted so that their products would decay with 51-year half-lives (OECD, 2002). This would eliminate them as potential long-term hazards.
No separation technology is 100 percent efficient; thus, even with actinide recycling, some fraction of the actinides will remain with the fission products for disposal. The efficiency of the separations will determine the long-term (> 1,000 years) radiotoxicity of the waste from fission power. For example, if 99.9 percent of the plutonium and 99 percent of the americium (Am), curium (Cm), and neptunium (Np) were separated, with all other actinides remaining with the waste, then it would take 10,000 years for radiotoxicity to decay to ore levels—a substantial increase over the 300 years required if 100 percent of all actinides were separated out (OECD, 1999). Increasing the separation efficiency to 99.9 percent of Am, Cm, and Np would reduce this to less than 1,000 years. Thus, the efficiency of separation of actinides has a significant impact on the waste-isolation time and thus on the difficulty of the waste-isolation problem. Economical separation of > 99.8 percent of plutonium has been demonstrated on a commercial scale (Cogema’s La Hague plant), and 99.9 percent separation of Am has been demonstrated on a laboratory scale. Research and development continues
to improve the technology for actinide separation; thus, it seems reasonable to expect that highly efficient (≈99.9 percent) separation of key actinides will be economically achievable eventually. This raises the possibility of a relatively short waste-isolation time (a few hundred years), which would greatly simplify waste disposal.
The 233U/232Th cycle creates fewer transuranic atoms per unit of energy produced and, thus, in some sense creates less of a long-term waste problem (Rubbia et al., 1995). However, it also makes recycling somewhat more difficult, largely because the daughters of the recycled 233U are more highly radioactive than 239Pu and its daughters, which means hands-on operations must be replaced by remote-controlled operations.
In summary, if a substantial majority of actinides are recycled (which will be necessary for us to tap the majority of the potential energy of uranium and thorium resources), then the waste stream from fission power will consist of a very small volume of fission products along with a small fraction of lost actinides. This waste can be readily immobilized in an insoluble material, such as borosilicate glass. The efficiency of actinide-separation technology will determine whether this waste inventory will decay to ore-level radiotoxicity in hundreds of years or thousands of years. Thus, improvements in separation technology may have a significant impact on the waste-isolation time and on public acceptance of fission power.
One disadvantage of actinide recycling is that recycled fuel costs approximately 10 to 20 percent more than fresh fuel. Another is that recycling technology could conceivably enable countries or groups to develop nuclear weapons— the proliferation issue.
Proliferation
Nuclear weapons use highly concentrated fissile material, such as uranium that is highly enriched in 235U or plutonium that is mostly 239Pu. Highly enriched 235U can be obtained by the same process that produces low-enriched 235U for reactor fuel—the process is simply carried farther. (This is the process that North Korea recently acknowledged using in their weapons program.) 239Pu is generated in every reactor that contains 238U (see Eq. (1)); however, if fuel stays in a reactor for more than a few months, significant quantities of other plutonium isotopes are also created, which makes the plutonium more difficult to use for weapon design and fabrication. Nevertheless, a National Research Council report has concluded that a credible weapon could be made from plutonium of almost any isotopic composition (NRC, 1995).
The 232Th/233U cycle may be more proliferation-resistant than the 238U/239Pu cycle, because 233U daughter products generate heat and radiation that could make it difficult to design, build, and maintain weapons. Nevertheless, it is technically possible to create weapons from separated 233U.
Every country that has developed nuclear weapons has obtained its concentrated fissile material from dedicated military programs, not by co-opting power-reactor technology. Nevertheless, there is a concern that if recycling technology is developed and widely used in the power industry, it could be used by some nations or groups to produce plutonium for a weapons program. A challenge, therefore, is to develop an economical, practical, proliferation-resistant fission-fuel cycle. This is one goal of the Generation-IV Reactor Development Program (Kotek, 2003). One example of a proliferation-resistant technology that includes recycling of valuable actinides is the integral fast-reactor concept (Till et al., 1997). With this technology, Pu is never separated from U during reprocessing, and thus no weapons-usable material ever exists at any stage of the process.
NEAR-TERM ISSUES
Achieving sustainable fission energy will require changes in current practices, especially in the United States. Current U.S. policy is for all spent fuel to be shipped to a geologic repository (recently identified as Yucca Mountain, Nevada) with no reprocessing. This is a once-through, or “open,” fuel cycle. There are several adverse consequences of not reprocessing spent fuel:
-
More than 99 percent of the potential energy in the uranium is lost.
-
Some actinides have long half-lives (24,000 years for 239Pu), which leads to stringent long-term requirements for disposal technologies.
-
Some actinides generate heat, which limits repository capacity.
The first consequence is significant for the very long term. The second affects public acceptance of nuclear power and public acceptance of any given repository site (people wonder how anyone can know that the material will remain sufficiently isolated for tens of thousands of years) and poses significant technical challenges. The third affects the capacity of a given repository. The latter two effects are very important for the near term (i.e., the next few decades).
From a technical point of view, repository space is not an issue. There appear to be more than enough suitable stable geologic formations in the world to handle waste from millennia of fission reactors, especially if fissionable materials (actinides) are recycled. However, because of the political picture today, repository space is a precious commodity. After 20 years of study, more than $4 billion of expenditures, and several political battles, the Yucca Mountain site has very recently been selected by the U.S. Department of Energy and Congress as the repository location for which the DOE will attempt to obtain a license. If licensing proceeds as quickly as possible, the first spent fuel will not be delivered until 2010 or later. Given the current once-through, no-reprocessing fuel strategy, the current U.S. fleet of reactors will produce enough spent fuel by 2040 to fill the Yucca Mountain repository to its estimated technical capacity
(DOE, 2002). The addition of new reactors would of course hasten this date. Clearly, in the near term in the United States, repository capacity must be increased for fission power to achieve its potential. It seems equally clear that finding a second repository site would be challenging, especially politically.
The capacity of Yucca Mountain is limited by the thermal load it can accommodate (radioactive decay releases energy that heats the material). If the waste produced lower W/kg, more mass could be accommodated (DOE, 2002). With the current once-through fuel strategy, the main thermal load after a few decades will come from the decay of the isotopes 238Pu and 241Am, with half-lives of 88 and 432 years, respectively. If plutonium and americium were removed from the spent fuel, the heat load would be dominated by isotopes with 30-year half-lives; thus, the thermal load of a given mass of spent fuel would be halved every 30 years (P.F. Peterson, University of California-Berkeley, personal communication, June 2002). In other words, half of the repository capacity would effectively be regenerated every 30 years. It is easy to imagine that this might be more achievable politically than obtaining approval for another repository site.
SUMMARY AND CONCLUSIONS
Worldwide energy use is likely to increase in the foreseeable future, and sustainable energy sources are not abundant. It seems likely that many different sources will be tapped to meet energy needs. Nuclear fission could potentially provide a significant fraction of the world’s energy for millennia: its inputs (fuel and construction materials) are readily available and its waste stream (fission products and lost actinides) is very small and not technically difficult to handle. Realizing the potential of fission energy will require high-conversion reactors and the recycling of fissionable atoms, which in turn will require that some technical and political challenges be met.
In the short term, especially in the United States, waste-repository capacity is a significant issue. The long-term capacity of the Yucca Mountain repository could be increased significantly by separating plutonium and americium from spent reactor fuel.
ACKNOWLEDGMENTS
I thank Per Peterson and Harold McFarlane for their helpful comments, information, and insights.
REFERENCES
AWEA (American Wind Energy Association). 1998. How Much Energy Does It Take to Build a Wind System in Relation to How Much Energy It Produces? Available online at: <http://www.awea.org/faq/bal.html>.
DOE (U.S. Department of Energy). 2002. Yucca Mountain Site Suitability Evaluation. DOE/RW-0549. Washington, D.C.: U.S. Department of Energy. Also available online at: <http://www.ymp.gov/documents/sse_a/index.htm>.
Kotek. J. 2003. Advanced Nuclear Reactor Technologies. Frontiers of Engineering: Reports on leading-Edge Engineering from the 2002 NAE Symposium on Frontiers of Engineering. Washington, D.C.: The National Academies Press.
NRC (National Research Council). 1995. Management and Disposition of Excess Weapons Plutonium: Reactor-Related Options. Washington, D.C.: National Academy Press. Also available online at: <http://www.nap.edu/catalog/4754.html>.
NRC. 1996. Nuclear Wastes: Technologies for Separations and Transmutation. Washington, D.C.: National Academy Press. Also available online at: <http://www.nap.edu/catalog/4912.html>.
OECD (Organization for Economic Cooperation and Development). 1999. Status and Assessment Report on Actinide and Fission Product Partitioning and Transmutation. Nuclear Development Report No. 1507. Paris, France: Nuclear Energy Agency of the Organization for Economic Cooperation and Development. Also available online at: <http://www.nea.fr/html/trw/docs/neastatus99/>.
OECD. 2002. Accelerator-Driven Systems (ADS) and Fast Reactors (FR) in Advanced Nuclear Fuel Cycles. Nuclear Development Report No. 3109 (2002). Paris, France: Nuclear Energy Agency of the Organization for Economic Cooperation and Development. Also available online at: <http://www.nea.fr/html/ndd/reports/2002/nea3109.html>.
Rubbia, C., J.A. Rubio, S. Buono, F. Carminati, N. Fieter, J. Galvez, C. Geles, Y. Kadi, R. Klapisch, P. Mandrillon, J.P. Revol, and C. Roche. 1995. Conceptual Design of a Fast Neutron Operated High Power Energy Amplifier. CERN-AT-95-44ET. Geneva, Switzerland: European Organization for Nuclear Research.
Till, C.E., Y.I. Chang, and W.H. Hannum. 1997. The integral fast reactor: an overview. Progress in Nuclear Energy 31: 3−11.
UNDP (United Nations Development Programme). 2000. World Energy Assessment: Energy and the Challenge of Sustainability. New York: United Nations Development Programme. Also available online at: <http://www.undp.org/seed/eap/activities/wea/>.
WEC (World Energy Council). 2001. Survey of Energy Resources. Part I: Uranium. Available online at: <http://www.worldenergy.org/wec-geis/publications/reports/ser/uranium/uranium.asp>.
WEC. 2002. Global Energy Scenarios to 2050 and Beyond. Available online at: <http://www.worldenergy.org/wec-geis/edc/scenario.asp>.
Stretching the Boundaries of Nuclear Technology
JAMES P. BLANCHARD
Department of Engineering Physics
University of Wisconsin-Madison
Most people are well aware that nuclear power can be used to produce electricity, but few are aware that it can be used to provide power in many other situations. Radioisotopes have been used for decades in commercial applications, such as pacemakers and smoke detectors, and recent trends indicate that other applications are on the horizon. Two technologies being actively investigated are space nuclear power and nuclear energy for microelectromechanical systems (MEMS).
SPACE NUCLEAR POWER
In 1989, a national space policy was approved that included the goal of putting a man on Mars by 2019. By most accounts, meeting this goal will require nuclear propulsion in order to shorten the mission time, thereby reducing exposure to zero gravity conditions and cosmic rays. Hence, nuclear propulsion will play a major role in space travel beyond the moon. This year, NASA announced a five-year, $1-billion program to develop nuclear reactors to power the next generation of spacecraft.
History
Early work on nuclear propulsion was primarily focused on nuclear-thermal technologies, in which a fission reactor is used to heat a gas and accelerate it through a nozzle. Research activity in this area began in 1944 and peaked in the 1960s. A typical design uses hydrogen as a propellant and graphite-moderated carbide fuel in the reactor core. One design, called Phoebus, achieved 5,000
MW of thermal power and 1 MN of thrust, which is about half the thrust of a space-shuttle engine (Bower et al., 2002).
Another early concept for nuclear propulsion was Project Orion, which relied on a series of nuclear blasts behind the payload to create shock waves that accelerated the device (Schmidt et al., 2002). Although this technology looked promising, it was abandoned in the 1960s because of a ban on nuclear testing.
Fuel Efficiency and Mission Length
The efficiency of the fuel used for propulsion is measured by a parameter called the specific impulse, which is defined as the ratio of the thrust produced to the rate at which fuel is consumed. The units of this parameter, typically seconds, are determined by dividing force by weight of fuel consumed per unit time. Hence, a specific impulse of N seconds can be interpreted as a capability for providing a unit thrust with a unit weight of fuel for N seconds. By comparing the specific impulses for different propulsion technologies, one can assess their advantages and disadvantages. Increased fuel efficiency is manifested in several ways—shorter trips, larger payloads for a fixed total launch weight, and flexibility for scientific activities at the destination.
The specific impulses for several propulsion options are shown in Table 1. The specific impulse for nuclear fuels can be many times that of chemical fuels, while the thrust is correspondingly lower and the run time longer. Electrostatic thrusters have relatively low thrust but can run virtually continuously and, therefore, can provide short trip times and low launch weights for a given payload. In
TABLE 1 Propulsion Parameters for Several Propulsion Technologies
Technology |
Specific Impulse (sec) |
Thrust per Engine (N) |
Run Time (duration) |
Chemical |
150–450 |
0.5–5 million |
A few seconds to hundreds of minutes |
Nuclear Thermal |
825–925 |
5,000–50,000 |
A few minutes to several hours |
Electromagnetic |
2,000–5,000 |
10–200 |
A few seconds to several hundred hours |
Electrostatic |
3,500–10,000 |
1–10 |
A few minutes to several days or months |
Source: Niehoff and Hoffman, 1996. Reprinted with permission of the American Astronautical Society. |
contrast, chemical rockets tend to run at high thrust for short times, accelerating rapidly as the rocket fires and then coasting between necessary adjustments in trajectory.
Nuclear-Electric Propulsion
There are three basic types of electric propulsion systems: electrothermal, electrostatic, and electromagnetic. In electrothermal propulsion, the propellant is heated either by an electric arc or a resistance heater. The hot propellant is then exhausted through a conventional rocket nozzle to produce thrust. Electrostatic propulsion uses electric fields to accelerate charged particles through a nozzle. In electromagnetic propulsion, an ionized plasma is accelerated by magnetic fields. In all three types, electricity from a nuclear source, such as a fission reactor, is used to power the propulsion device (Allen et al., 2000; Bennett et al., 1994). The power flow for a typical nuclear-electric propulsion scheme is shown in Figure 1.
The most mature of the electric propulsion concepts is electrostatic propulsion. NASA’s Deep Space 1 device (Figure 2), launched in 1998, relies on an ionized xenon gas jet for propulsion (Brophy, 2002). The xenon fuel fills a chamber ringed with magnets, which control the flow; electrons emitted from a
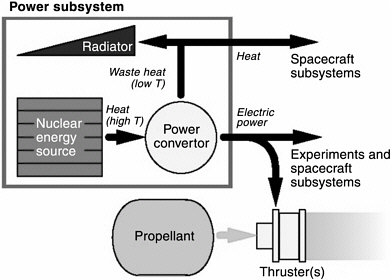
FIGURE 1 Schematic drawing of power flow for a typical nuclear-electric propulsion device. Heat is produced in the nuclear source (typically a fission reactor core) and converted to electricity in the power converter. The electricity is then used to power the thruster. The radiator dissipates the waste heat. Source: NASA, 2001.
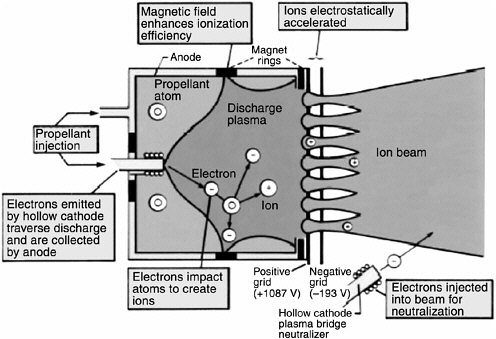
FIGURE 2 Schematic drawing of the Deep Space 1 ion thruster. Source: NASA, 2002.
cathode ionize the gas. The ions pass through a pair of metal grids at a potential of 1,280 volts and are thus accelerated out the back. A second electrode emits electrons to neutralize the charge on the device. The engine is capable of producing 90 mN of thrust while consuming 2,300 W of electrical power. This device is solar powered, but future designs anticipate using a fission reactor to produce the electricity.
All electric propulsion systems require supplies of electricity, and fission reactors, which have high power density, are an excellent choice for meeting this need. Numerous projects are under way to develop fission reactors with low weight, high reliability, long life without refueling, and safety during launch. A wide variety of heat-transport and energy-conversion technologies are being investigated. One example of a fission reactor is the safe, affordable fission engine (SAFE-400), a 400-kW (thermal) reactor that is expected to produce 100 kW of electric power using heat pipes for energy transport and a Brayton cycle for energy conversion (Poston et al., 2002). The core consists of 381 uranium-nitride fuel pins clad with rhenium. The uranium-nitride fuel was chosen because of its high uranium density and high thermal conductivity. Molybdenum/ sodium heat pipes are used for heat transport to provide passive safety features in case of an accident.
Plasma Propulsion
An approach related to electric propulsion is the plasma rocket, exemplified by the variable specific impulse magnetoplasma rocket (VASIMR) (Diaz, 2000). Like an ion thruster, a VASIMR injects a propellant (usually hydrogen) into a cell and ionizes it. The resulting plasma is heated using radio-frequency injection and a magnetic nozzle that accelerates the gas to provide the propulsion. A second example is the gas dynamic mirror, a long, slender device in a magnetic mirror configuration. This device is powered by fusion reactions in the plasma; the thrust is produced by plasma ions exiting the end of the device. Accelerated by the mirror’s magnetic-field gradients, the ions provide efficient propulsion. One concept features a 50-m long, 7-cm radius plasma and produces 50,000 N of thrust at a specific impulse of more than 100,000 seconds (Kammash et al., 1995).
SMALL-SCALE RADIOISOTOPE POWER
MEMS have the potential to revolutionize many technologies, and the number of commercial applications is increasing rapidly. Many applications, such as pumps, motors, and actuators, can be improved with onboard power supplies, and various technologies are being explored to provide such power. Obvious choices, such as chemical batteries, fuel cells, and fossil fuels, show some promise, but none of them can match radioisotope power for long, unattended operation (Blanchard et al., 2001). This is because of the larger energy density available with nuclear sources.
Radioisotopes can be used to produce power in a variety of ways. Thermo-electric and thermionic technologies convert the heat generated by the decay to electricity; other approaches make more direct use of the released energy. Thermoelectric conversion uses a thermal gradient between two different materials to create a current via the Seebeck effect. Thermionic conversion creates a current by boiling electrons off a cathode (at high temperature) and catching them at an anode. Techniques for more direct methods include simple collection of the emitted charged particles, ionization near a P-N or P-I-N junction in a semiconductor, and conversion of the decay energy to light and subsequent conversion to electricity in a photovoltaic.
History
Radioisotopes have been used as power sources for decades. Early pace-makers were powered by approximately 0.2 grams (3 Ci) of 238Pu, producing about 0.2 mW and delivering about 0.05 mW to the heart muscle (Parsonnet, 1972). Whereas pacemakers powered by chemical batteries have lives of less than 10 years and thus require replacement in most patients, the half-life of 238Pu
(approximately 86 years) permits radioisotope-powered devices to last the life of the patient.
Although a smoke detector is not strictly a power source, many smoke detectors contain radioisotopes (usually 1 to 5 microcuries of 241Am). The source ionizes air between a pair of parallel plates, and a chemical battery (or house current) is used to collect these charges and thus measure the degree of ionization in the gap. When smoke enters the gap, the increased ionization trips the sensor.
Radioisotope thermoelectric generators (RTGs) are used in many applications, including underwater power and lighting in remote locations, such as the Arctic (Lange and Mastal, 1994). RTGs were also used to provide power for the Cassini and Voyager missions. Much like the pacemakers mentioned above, RTGs create power by thermoelectric conversion. Most RTGs are modular, with each module containing approximately 2.7 kg of Pu (133 kCi) and measuring approximately 42 cm in length and 114 cm in diameter. The modules produce 276 W of electric power at the beginning of life and, despite decay of the isotope, will produce approximately 216 W after 11 years of unattended operation.
Current research is focused mostly on the miniaturization of RTGs for many applications, such as MEMS; in addition, efforts to improve the efficiency of existing RTGs are ongoing.
Nuclear Microbatteries
Thermal devices, such as RTGs, are difficult to reduce to the microscale because, as the size is decreased, the surface-to-volume ratio increases, thus increasing the relative heat losses and decreasing the efficiency of the device. Hence, microbattery designs have tended to focus on direct methods of energy conversion. For example, one can construct a diode from silicon using a layer of P-type silicon adjacent to a layer of N-type silicon and a radioactive source placed on the top of the device. As the source decays, the energetic particles penetrate the surface and create electron-hole pairs in the vicinity of the P-N junction. This creates a potential across the junction, thus forming a battery. Figure 3a is a schematic drawing of such a device, and Figure 3b is a photograph of one concept created at the University of Wisconsin. The device shown in Figure 3b is fairly large, measuring approximately 0.5 cm on each side, but one can easily imagine using a single pit from the device as a power source. This would provide a microbattery measuring approximately 400 microns by 400 microns by 50 microns; using a beta emitter (63Ni), it could produce approximately 0.2 µW of electrical power. An early prototype of the device pictured in Figure 3b, loaded with a weak source (64 microcuries of 63Ni), produced approximately 0.07 nW of power. Given that the thermal energy of 64 microcuries of 63Ni is 6.4 nW, this device is about 1 percent efficient. Placing a second diode on top of the source would nearly double the efficiency (because the decay
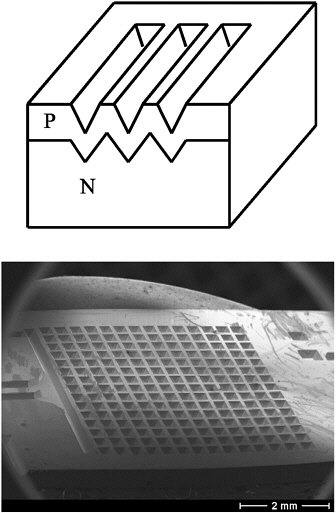
FIGURE 3(a) A schematic drawing of a simple device using a P-N junction and radioactive source to produce the potential. (b) Photograph of a device using pits rather than trenches to hold the source.
products are produced isotropically). Work is also under way to improve the efficiency by optimizing the design.
When an alpha source is used in such a battery, the available energy for a fixed activity level is increased by several orders of magnitude. Unfortunately, the high-energy alpha particles damage the silicon lattice as they pass through and quickly degrade the power. Attempts are being made to overcome this limitation by using materials that are resistant to damage. Materials being considered include wide-band-gap semiconductors, such as gallium nitride, which might improve radiation stability and device efficiency (Bower et al., 2002).
Thermoelectric devices are another approach to using alpha sources. These devices use the heat from the source to produce a temperature gradient across the thermoelectric device to produce power. Thus, there is no risk of radiation damage, and alpha particles could be used. Hi-Z Technology, Inc. (San Diego), developed a 40 mW device using a radioisotope heater unit (RHU) that was produced by NASA several years ago. The RHU uses about 2 grams of 238Pu to produce 1 W of thermal power. Using this as a heat source, Hi-Z produced a thermoelectric device that established a temperature difference of approximately 225°C throughout the device and provided 40 mW of power. The efficiency of the device was approximately 4 percent. Some improvement can be gained through improved insulation and thermoelectrics.
A third approach to creating a micropower device uses radioisotopes to excite phosphors that emit photons, which can then be collected in a standard or modified solar cell. This protects the photovoltaic from damage but increases losses in the system. In addition, the phosphor may be damaged. Typical organic scintillators have energy-conversion efficiencies of 1 percent, whereas inorganic crystals can achieve efficiencies of up to 30 percent. TRACE Photonics, Inc. (Charleston, Illinois), has built a scintillation glass using sol-gel processes with high light-conversion efficiency under radiation exposure (Bower et al., 2002). Current overall efficiencies are approximately 1 percent, but device integration can probably be improved because of the low weight and direct conversion.
Applications of Micropower Sources
All current MEMS devices sold commercially are passive devices. Hence, there is no existing market for micropower sources. Nevertheless, one can envision many future applications of MEMS devices with onboard micropower sources, such as small drug dispensers placed directly into the bloodstream and laboratories-on-a-chip that can carry out real-time blood assays. Researchers at UCLA and UC Berkeley have been investigating so-called “smart-dust” concepts for using wireless communications to create large-scale sensor networks (Kahn et al., 1999). This approach involves distributed sensors that can communicate with each other through a network and thus “provide a new monitoring and control capability for transportation, manufacturing, health care, environmental monitoring, and safety and security” (Asada et al., 1998). These devices will require power for data collection and storage, as well as for the delivery of information between neighboring devices.
A new application of nuclear power is the self-powered cantilever beam produced at the University of Wisconsin (Li et al., 2002). This device, shown in Figure 4, places a conducting cantilever beam in the vicinity of a radioisotope, in this case 63Ni. As the beam collects the electrons emitted from the source, it becomes negatively charged, and the source becomes positively charged. The
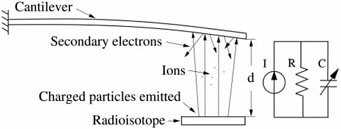
FIGURE 4 Schematic drawing of a self-oscillating cantilever beam. Devices can be modeled as capacitors in parallel with leakage resistors, with most of the leakage resulting from ionization in the gap.
beam is thus attracted to the source until contact is made and the device discharges. This causes the beam to be released and return to its original position. The process then repeats itself. Hence, the beam undergoes a repetitive bending and unbending; the period of the oscillation is determined by the strength of the source, the beam stiffness, and the initial separation between the beam and the source. Work is ongoing to produce wireless communication devices based on this design.
CONCLUSIONS
Nuclear power is the best, perhaps the only, realistic power source for both long-distance space travel and long-lived, unattended operation of MEMS devices. Much more research will have to be done to optimize the currently available technologies for future applications, but nuclear technologies will clearly provide viable, economic solutions, and they should be given continued attention and support as they approach commercialization
REFERENCES
Allen, D.T., J. Bass, N. Elsner, S. Ghamaty, and C. Morris. 2000. Milliwatt Thermoelectric Generator for Space Applications. Pp. 1476-1481 in Proceedings of Space Technology and Applications International Forum-2000. New York. American Institute of Physics Press.
Asada, G., T. Dong, F. Lin, G. Pottie, W. Kaiser, and H. Marcy. 1998. Wireless Integrated Network Sensors: Low Power Systems on a Chip. Pp. 9-16 in Proceedings of the 1998 European Solid State Circuits Conference. Paris: Seguir Atlantica.
Bennett, G., H. Finger, T. Miller, W. Robbins, and M. Klein. 1994. Prelude to the Future: A Brief History of Nuclear Thermal Propulsion in the United States. Pp. 221-267 in A Critical Review of Space Nuclear Power and Propulsion, 1984–1993, edited by M. El-Genk. New York: American Institute of Physics Press.
Blanchard, J., R.M. Bilboa y Leon, D.L. Henderson, and A. Lai. 2001. Radioisotope Power Sources for MEMS Devices. Pp. 87-88 in Proceedings of 2001 ANS Annual Meeting. Washington, D.C.: American Nuclear Society.
Bower, K., X. Barbanel, Y. Shreter, and G. Bohnert. 2002. Polymers, Phosphors, and Voltaics for Radioisotope Microbatteries. Boca Raton, Fla.: CRC Press.
Brophy, J. 2002. NASA’s Deep Space 1 ion engine. Revue of Scientific Instruments 73(2): 1071-1078.
Diaz, F. 2000. The VASIMR rocket. Scientific American 283(5): 90-97.
Kahn, J.M., R.H. Katz, and K.S.J. Pister. 1999. Mobile Networking for Smart Dust. Pp. 271-278 in Proceedings of the ACM/IEEE International Conference on Mobile Computing and Networking. New York: ACM Press.
Kammash, T., M. Lee, and D. Galbraith. 1995. High-Performance Fusion Rocket for Manned Space Missions. Pp. 47-74 in Fusion Energy in Space Propulsion, edited by T. Kammash. Progress in Astrophysics and Aeronautics 167.
Lange, R., and E. Mastal. 1994. A Tutorial Review of Radioisotope Power Systems. Pp. 1-20 in A Critical Review of Space Nuclear Power and Propulsion 1984–1993, edited by M. El-Genk. New York: American Institute of Physics Press.
Li, H., A. Lal, J. Blanchard, and D. Henderson. 2002. Self-reciprocating radioisotope-powered cantilever. Journal of Applied Physics 92(2): 1122-1127.
NASA (National Aeronautics and Space Administration). 2001. The Safe Affordable Fission Engine (SAFE) Test Series. Available online at: <http://www.spacetransportation.com/ast/presentations/7b_vandy.pdf>.
NASA. 2002. DS1: How the Ion Engine Works. Available online at: <http://www.grc.nasa.gov/WWW/PAO/html/ipsworks.htm>.
Niehoff, J., and S. Hoffman. 1996. Pathways to Mars: An Overview of Flight Profiles and Staging Options for Mars Missions. Pp. 99-125 in Strategies for Mars: A Guide for Human Exploration, edited by C.R. Stoker and C. Emmart. Paper no. AAS 95-478. Science and Technology Series Vol. 86. San Diego, Calif.: Univelt. (Copyright © 1996 by American Astronautical Society Publications Office, P.O. Box 28130, San Diego, CA 92198; Website: <http://www.univelt.com>. All Rights Reserved. This material reprinted with permission of the AAS.)
Parsonnet, V. 1972. Power sources for implantable cardiac pacemakers. Chest 61: 165-173.
Poston, D., R. Kapernick, and R. Guffee. 2002. Design and Analysis of the SAFE-400 Space Fission Reactor. Pp. 578-588 in Space Technology and Applications International Forum. New York: American Institute of Physics Press.
Schmidt, G., J. Bonometti, and C. Irvine. 2002. Project Orion and future prospects for nuclear propulsion. Journal of Propulsion Power 18(3): 497-504.