4
Physical Integrity
This chapter focuses on physical integrity—the ability of the distribution system to act as a physical barrier that prevents external contamination from affecting the quality of the internal, drinking water supply. Water distribution system engineers have defined the physical integrity of the distribution system to be its ability to handle external and internal stresses such that the physical material of the system does not fail (Male and Walski, 1991). Here failure is interpreted more broadly to encompass the absence of a critical component, the improper installation of a component, or the installation of an already contaminated component.
The physical integrity of the distribution system is always in a state of change, and the aging of the nation’s distribution systems and eventual need for replacement are growing concerns. Maintaining such a vast physical infrastructure is a challenge because of the complexity of individual distribution systems, each of which is comprised of a network of mains, fire hydrants, valves, auxiliary pumping or booster disinfection substations, storage reservoirs, standpipes, and service lines along with the plumbing systems in residences, large housing projects, high-rise buildings, hospitals, and public buildings. This is further complicated by factors that vary from system to system such as the size of the distribution network for the population served, the predominant pipe material and age of pipelines, water pressure, the number of line breaks each year, water storage capacity, and water supply retention time in the system. When considering the replacement of a given component of the distribution system, decision makers must weigh its potential remaining life versus the potential that the component will fail, which could result in costly consequences and compromise the water utility’s service.
The physical integrity of the distribution system, from the entry point to the customer’s tap, is a primary barrier against the entry of external contaminants and the loss in quality of the treated drinking water. This barrier includes such materials as the pipe wall and reservoir cover as well as physical connections to nonpotable water sources. The barrier must be non-permeable since contaminants can enter through breaks or failures in materials as well as through the materials themselves. Table 4-1 gives examples of the infrastructure components that constitute this physical barrier, what they protect against, and the materials of which they are commonly constructed.
A variety of components and materials make up this physical barrier. Four major component types are delineated and referred to repeatedly in this chapter: (1) pipes including mains, services lines, and premise plumbing; (2) fittings and appurtenances such as crosses, tees, ells, hydrants, valves, and meters;
TABLE 4-1 Infrastructure Components, What They Protect Against, and Common Materials
Component |
External Contamination the Barrier Protects Against |
Materials Used |
Pipe |
Soil, groundwater, sewer exfiltration, surface runoff, human activity, animals, insects, and other life forms |
Asbestos cement, reinforced concrete, steel, lined and unlined cast iron, lined and unlined ductile iron, PVC, polyethylene and HDPE, galvanized iron, copper, polybutylene |
Pipe wrap and coatings |
Supporting role in that it preserves the pipe integrity |
Polyethylene, bitumastic, cement-mortar |
Pipe linings |
Supporting role in that it preserves the pipe integrity |
Epoxy, urethanes, asphalt, coal tar, cement-mortar, plastic inserts |
Service lines |
Soil, groundwater, sewer exfiltration, surface runoff, human activity, animals, insects, and other life forms |
Galvanized steel or iron, lead, copper, chlorinated PVC, cross-linked polyethylene, polyethylene, polybutylene, PVC, brass, cast iron |
Premise plumbing |
Air contamination, human activity, sewage and industrial nonpotable water. |
Copper, lead, galvanized steel or iron, iron, steel, chlorinated PVC, PVC, cross-linked polyethylene, polyethylene, polybutylene |
Fittings and appurtenances (meters, valves, hydrants, ferrules) |
Soil, groundwater, sewer exfiltration, surface runoff, human activity, animals, insects, and other life forms |
Brass, rubber, plastic |
Storage facility walls, roof, cover, vent hatch |
Air contamination, rain, algae, surface runoff, human activity, animals, birds, and insects |
Concrete, steel, asphaltic, epoxy, plastics |
Backflow prevention devices |
Nonpotable water |
Brass, plastic |
Liquids |
Not applicable |
Oils, greases, lubricants |
Gaskets and joints |
Soil, groundwater, sewer exfiltration, surface runoff, human activity, animals, insects, and other life forms |
Rubber, leadite, asphaltic, plastic |
(3) storage facilities including reservoirs (underground, open, and covered), elevated storage tanks, ground level storage tanks, and standpipes; and (4) backflow prevention devices. The materials used by the water industry for these components, particularly pipes, have changed significantly over time (AWWA, 1986; Von Huben, 1999). For example, cast iron pipe (lined or unlined) has been largely phased out due to its susceptibility to both internal and external corrosion and associated structural failures. Ductile-iron pipe (with or without a cement lining) has taken its place because it is durable and strong, has high flexural strength, and has good resistance to external corrosion from soils. It is, however, quite heavy, it might need corrosion protection in certain soils, and it requires multiple types of joints. Concrete, asbestos cement, and polyvinyl chloride (PVC) plastic pipe have been used to replace metal pipe because of their relatively good resistance to corrosion. Polyethylene pipe is growing in use, especially for trenchless applications like slip lining, pipe bursting, and directional drilling (Morrison, 2004). High-density polyethylene pipe is the second most commonly used pipe. It is tough, corrosion resistant both internally and externally, and flexible. The manufacturer estimates its service life to be 50 to 100 years (AWWA, 2005a). Chapter 1 discusses the rate of pipe replacement in the United States and notes that much of the current infrastructure is nearing the end of its usable lifetime.
FACTORS CAUSING LOSS OF PHYSICAL INTEGRITY
Losses in physical integrity are caused by an abrupt or gradual alteration in the structure of the material barrier between the external environment and the drinking water, by the absence of a barrier, or by the improper installation or use of a barrier. These mechanisms are summarized in Table 4-2.
Infrastructure components break down or fail over time due to chemical interactions between the materials and the surrounding environment, eventually leading to holes, leaks, and other breaches in the barrier. These processes can occur over time scales of days to decades, depending on the materials and conditions present. For example, plastic pipes can be very rapidly compromised by nearby hydrophobic compounds (e.g., solvents in the vadose zone that result from surface or subsurface contamination), with the resulting permeation of those compounds into the distribution system through the pipe materials. Both internal and external corrosion can lead to structural failure of pipes and joints, thereby allowing contaminants to infiltrate into the distribution system via leaks or subsequent main breaks. Materials failure can be hastened if the distribution system water pressure is too high, from overburden stresses on pipes, and during natural disasters. Indeed, hurricanes and earthquakes have caused extensive sudden damage to distribution systems, including broken service lines and fire hydrants, pipes disconnected or broken by the uprooting of trees, cracks in cement water storage basins, and seam separations in steel water storage tanks (Geldreich, 1996).
TABLE 4-2 What Causes a Loss in Physical Integrity?
Component |
Mechanism of Integrity Loss |
||
Alteration in material structure leading to failure |
Absence of the barrier or material |
Improper application or installation of the barrier |
|
Pipe |
|
|
|
Fitting and appurtenance |
|
|
|
Storage facility wall, roof, cover, vent, hatch |
|
|
|
Backflow prevention device |
|
|
|
A second major contributor to the loss of physical integrity is when certain critical components are absent, either by oversight or due to vandalism. For example, the absence of backflow prevention devices and covers for storage facilities can allow external contaminants to enter distribution systems. For the purposes of this discussion, pipes are assumed to always be present.
Finally, human activity involving distribution system materials can allow contamination to occur such as through unsanitary repair and replacement practices, unprotected access to materials, or the improper handling of materials leading to unintentional damage. One must even consider the installation of flawed materials, which might, for example, be brought about because of a lack of protection of materials during storage and handling.
Structural Failure of Distribution System Components
Metallic pipe failures are divided generally into two categories: corrosion failures and mechanical failures. Common types of failures for iron mains include (Male and Walski, 1991; Makar, 2002):
-
Bell splits or cracks that require cutting out the joint and replacing it with a mechanical fitting; these are typical for leadite joints
-
Splits at tees and offsets and other fittings that require replacement
-
Circumferential cracks or round cracks and holes, more typical in smaller diameter pipe (< 10 in.). These can result from a lack of soil support, causing the pipe to be called upon to act as a beam
-
Splits or longitudinal cracks or spiral cracks that will blow out. Longitudinal cracks are more common for larger pipe (> 12 in.) and can result from crushing under external loads or from excessive internal pressure
-
Spiral failures in medium diameter pipe
-
Shearing failures in large diameter pipe
-
Pinholes (corrosion hole) caused by internal corrosion
-
Tap or joint blowout
-
Crushed pipe
A simpler categorization can be found in Romer et al. (2004), who summarized three types of pipe failures as weeping failures, pipe breaks, and sudden failures. A weeping failure is where a leak allows an unnoticeable exchange of water to and from the surrounding soil. A pipe break includes a hole in the pipe or a disengagement of a bell-and-spigot joint. A sudden failure is the bursting of a pipe wall or shear of the pipe cross section, as would occur for a concrete pipeline, or a blow out, which refers to a complete break in a pipe.
Pipe breaks can occur for a myriad of reasons such as normal materials deterioration, joint problems, movement of earth around the pipe, freezing and thawing, internal and external corrosion, stray DC currents, seasonal changes in internal water temperature, heavy traffic overhead including accidents that dam-
age fire hydrants, changes in system pressure, air entrapment, excessive overhead loading, insufficient surge control (such as with water hammer and pressure transients), and errors in construction practices (Male and Walski, 1991). This last factor is especially troubling since it should be entirely preventable. Nonetheless, there is evidence that poor quality workmanship during initial pipe installation can lead to early structural failure of pipes (Clark and Goodrich, 1989). Burlingame et al. (2002) reported on premature (within one year of installation) failures in service lines that resulted from the combination of using hard copper tubing and poor workmanship during cutting and flaring of the ends. AwwaRF (1985) has also reported that failures with copper tubing can be due to poor workmanship. One of the goals of proper installation of water mains is to account for and circumvent these issues; unfortunately, failure to do so translates into a substantial number of unnecessary main breaks.
One overriding factor in determining the potential for pipe failure is the force exerted on the water main. Contributors to this force include changes in temperature, which cause contraction and expansion of the metal and the surrounding soil, the weight of the soil over the buried main, and vibrations on the main caused by nearby activities such as traffic. An important consideration in this regard is the erosion potential of the supporting soil beneath the buried main. In the construction of a main, special sand and soil can be laid beneath it to help it bear external forces. But the movement of water in the ground beneath the main can wash away the finer material and create small or large caverns under the pipe. The force now bearing down on top of the pipe must be taken by the pipe itself, without the help of supporting material underneath. If these forces exceed the strength of the pipe, the main breaks. Most often these breaks occur at the weakest part of the main, i.e., the joint.
The factors that cause pipe failures can compound one another, hastening the process. For example, if a main develops small leaks because of corrosion, water within the distribution system can exfiltrate into the area surrounding the pipe, eroding away the supporting soil. Leakage that undermines the foundation of a water main can also occur from nearby sewer lines, go on essentially unnoticed, and eventually lead to water main collapse (Morrison, 2004).
Table 4-3 summarizes common problems that lead to pipe failures for pipes of differing materials. These are some of the principal factors, but they are not the only factors that act individually or in combination to lead to a main break. Other factors could include a street excavation that accidentally disturbs a water main and the misuse of fire hydrants. At most utilities, overall pipe break rates have been relatively low and stable (Damodaran et al., 2005) even though the infrastructure is aging.
Other components of distribution system also experience structural failure, although they have not historically received the attention afforded to pipes. For storage facilities, structural failure is less of a problem than external contamination due to the absence or failure of an essential component such as a cover or vent. Fittings and appurtenances can suffer from the effects of corrosion and permeation.
TABLE 4-3 Most Common Problems that Lead to Pipe Failure for Various Pipe Materials
Pipe Material (common sizes) |
Problems |
PVC and Polyethylene (4–36 in.) |
Excessive deflection, joint misalignment and/or leakage, leaking connections, longitudinal breaks from stress, exposure to sunlight, too high internal water pressure or frequent surges in pressure, exposure to solvents, hard to locate when buried, damage can occur during tapping |
Cast/Ductile Iron (46–4 in,) (lined and unlined) |
Internal corrosion, joint misalignment and/or leakage, external corrosion, leaking connections, casting/manufacturing flaws |
Steel (4–120 in.) |
Internal corrosion, external corrosion, excessive deflection, joint leakage, imperfections in welded joints |
Asbestos-Cement (4–35 in.) |
Internal corrosion, cracks, joint misalignment and/or leakage, small pipe can be damaged during handling or tapping, pipe must be in proper soil, pipe is hard to locate when buried |
Concrete (12–16 to 144–168 in.) (prestressed or reinforced) |
Corrosion in contact with groundwater high in sulfates and chlorides, pipe is very heavy, alignment can be difficult, settling of the surrounding soil can cause joint leaks, manufacturing flaws |
SOURCES: Morrison (2004) and AWWA (1986). |
Corrosion as a Major Factor
Corrosion is the degradation of a material by reaction with the local environment. In water distribution systems, the term corrosion refers to dissolution of concrete linings and concrete pipe, as well as to the deterioration of metallic pipe and valves via redox reactions (e.g., iron pipe rusting). Degradation originating from the inside of the pipe via reactions with the potable water is termed internal corrosion. Degradation originating outside the pipe on surfaces contacting moist soil is referred to as external corrosion. Both internal and external corrosion can cause holes in the distribution system and cause loss of pipeline integrity. In some cases holes are formed directly in pipes by corrosion, as is the case with pinholes, but in many other instances corrosion weakens the pipe to the point that it will fail in the presence of forces originating from the soil environment.
The type of corrosion and mode of failure causing loss of physical integrity are highly system specific. External corrosion can be exacerbated by a low soil redox potential, low soil pH, stray currents, and dissimilar metals or galvanic corrosion (Von Huben, 1999; Szeliga and Simpson, 2002; Romer et al., 2004; Bonds et al., 2005). The life of the pipe is also influenced by the material used, thickness of the pipe wall, use of protective outer wraps or coatings, application of cathodic protection, and backfill materials and techniques. Internal corrosion
is influenced by pH, alkalinity, disinfectant type and dose, type of bacteria present in biofilms, velocity, water use patterns, use of inhibitors, and many other factors.
Corrosion is not well understood, particularly at the level of the local water utility, such that insufficient attention has been given to its control (see a later section in this chapter). Some utilities have tried to avoid the issue by using plastic pipe. Even so, unprotected metal materials are regularly used at the present time, illustrating the water industry’s lack of attention to the problem. According to Romer et al. (2004), “approximately 72 percent of the materials reported in use for water mains are iron pipe, approximately two-thirds of the reported corrosion is in corrosive soils, and approximately two-thirds of the corrosion is on the pipe barrel.” In addition, metallic or cementitious pipe are often designed on the basis of their hydraulic capabilities first and foremost, and corrosion resistance is often a secondary consideration. The annual direct costs of corrosion are estimated to be $5 billion (Romer et al., 2004) for the main distribution system (not counting premise plumbing).
Issues with Service Lines
Recent evidence indicates that service lines (the piping between the water main and the customer’s premises) and their fittings and connections (ferrules, curb stops, corporation stops, valves, and meters) can account for a significant proportion of the leaks in a distribution system (AWWA Water Loss Control Committee, 2003). However, much less is known about what causes structural failures in service lines compared to distribution mains and other system components. Possibilities include improper techniques used during installation that damage materials, improper tapping and flaring to make connections, lack of corrosion prevention or use of corrosive backfill material, damage during handling to plastic tubing, and kinks in copper tubing, and excessive velocity. The Uniform Plumbing Code and International Plumbing Code do not clearly address these issues, and local plumbing codes may not either.
Many galvanized and lead pipe service lines are being replaced with copper or plastic pipe (chlorinated polyvinyl chloride or CPVC) (Von Huben, 1999). CPVC and copper each have their benefits and weaknesses. Installation of CPVC requires less skill compared to installation of copper, although if workers are not careful installation can result in cracking and damage to CPVC pipe. CPVC is better for corrosive soils and waters, while copper is more resistant to internal biofilm growth. Buried CPVC pipe is difficult to locate compared to metal or copper pipe because it does not conduct electrical current for tracing. CPVC can impart a “plastic” flavor to water while the copper pipe can impart a “metallic” flavor. With CPVC, low levels of vinyl chloride can leach into the water. If manufacturers follow American Society for Testing and Materials (ASTM) standards and are ISO 9002 certified, and certification includes NSF
International standards 14 and 61, the adverse conditions above can be minimized.
Permeation
Permeation refers to a mechanism of pipe failure in which contaminants external to the pipe materials and non-metallic joints compromise the structural integrity of the materials and actually pass through them into the drinking water. Permeation is generally associated with plastic pipes and with chemical solvents such as benzene, toluene, ethylbenzene, and xylenes (BTEX) and other hydrocarbons associated with oil and gasoline, all of which are easily detected using volatile organic chemical gas chromatography analyses. These chemicals can readily diffuse through the plastic pipe matrix, alter the plastic material, and migrate into the water within the pipe. Such compounds are common in soils surrounding gasoline spills (leaking storage tanks), at abandoned industrial sites, and near bulk chemical storage, electroplaters, and dry cleaners (Glaza and Park, 1992; Geldreich, 1996). Permeation incidents have occurred at high-risk sites, such as industrial sites and near underground chemical storage tanks, as well as at lower risk residential sites (Holsen et al., 1991). In some cases the integrity of the pipe has been irreversibly compromised, requiring the complete replacement of the contaminated section.
Common pipe materials such as PVC, polybutylene, and polyethylene differ in their chemical and physical structure, and thereby differ in their susceptibility to being altered upon exposure to solvents and in permeation rates. In studying BTEX and 1,3-dichlorobenzene, PVC pipe was found to be more permeable than polyethylene pipe unless the polyethylene pipe was altered by the solvents in contact, after which it can become more permeable to the pollutants (Burlingame and Anselme, 1995).
Human Activities that Lead to Contamination
A second major cause of physical integrity loss is human activity surrounding construction, repair, and replacement that can introduce contamination into the distribution system. Any point where the water distribution system is opened to the atmosphere is a potential source of contamination. This is particularly relevant when laying new pipes, engaging in pipe repairs, and rehabilitating sites. For example, a Midwestern water utility experienced a noticeable increase in the heterotrophic bacterial population of water from a newly installed pipe and identified Pseudomonas fluorescens, Ps. Maltophilia, and Ps. putida as the bacteria responsible for the increase (Geldreich, 1996). The same strains of Pseudomonas were recovered from the sand used as an aggregate in making the concrete lining for the new ductile iron pipe, implicating contamination during construction and installation. More recently, workers in Camden, New Jersey,
were cleaning and lining a 30-inch water main when a parallel sewer line from the post-Civil War era broke. Because of the proximity of the sewer line and the possibility of contamination, officials decided to issue a boil-water alert until water quality testing could show that no external contamination had entered the main. Between 1997 and 1999, the Philadelphia water supply measured elevated turbidity (>1 NTU) in about 12 to 14 percent of the samples that were collected from newly installed water mains. This turbidity, or the particulate debris captured on filters, was found to be largely iron oxides and rust (from the existing water mains still in service), vegetable material such as plant roots, and backfill sand.
Incidents like these are not uncommon, as revealed in a survey by Pierson et al. (2002), who point out that pipe repair and installation have not been accomplished using the best available sanitary practices. This is captured generally in Table 4-4, which summarizes the survey of distribution system workers at three different utilities (eastern U.S., western U.S., and western Canada) on the potential for external contamination to occur during water main repair and replacement activities. Given that the average number of main repairs a year for a single utility ranges from 66 to 901 (which corresponds to 7.9–35.6 repairs per 100 miles of pipe per year) (Clark and Goodrich, 1989), it is clear that exposure of the distribution system to contamination during repair is an inescapable reality.
Unsanitary activity during construction, replacement, or repair can also lead to the contamination of fittings and appurtenances. The use of inappropriate or inferior materials, and the contact between dissimilar metals within fittings, can also cause failures where they should not occur. Appurtenances can be improperly installed in a flooded meter or valve pit which can allow contaminants to enter under intrusion or can create corrosive conditions.
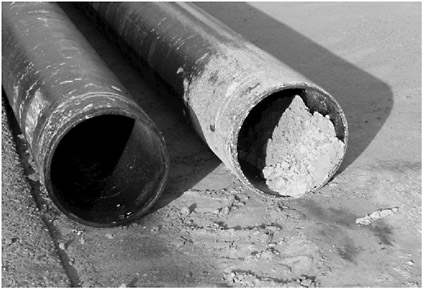
Backfill sand contaminating a new pipe at a water main construction site. Photo courtesy of Bureau of Laboratory Service, Philadelphia Water Department.
TABLE 4-4 Potential for Contaminant Entry during Water Main Activities
Activity |
Percent of Responses from Workers at 3 Different Utilities (A, B, C) |
|||||
Occurs Often |
Occurs Sometimes |
|||||
A |
B |
C |
A |
B |
C |
|
Broken service line fills trench during installation |
46 |
75 |
56 |
39 |
25 |
33 |
Pipe gets dirty during storage before installation |
53 |
75 |
22 |
43 |
25 |
33 |
Trench dirt gets into pipe during installation |
24 |
100 |
39 |
37 |
0 |
44 |
Rainwater fills trench during installation |
20 |
25 |
5 |
60 |
75 |
83 |
Street runoff gets into pipe before installation |
30 |
0 |
11 |
61 |
38 |
67 |
Pipe is delivered dirty |
4 |
25 |
17 |
33 |
63 |
22 |
Trash gets into pipe before installation |
24 |
0 |
0 |
56 |
50 |
11 |
Vandalism occurs at the site |
15 |
0 |
0 |
35 |
0 |
5 |
Animals get into pipe before installation |
0 |
0 |
0 |
11 |
0 |
11 |
SOURCE: Reprinted, with permission, from Pierson et al. (2002). © 2002 by American Water Works Association. |
New pipe materials are not sterile, whether they have been kept well protected or not. Indeed, according to a survey (Geldreich, 1996) about 18 percent of new pipe, irrespective of pipe material and size, failed upon testing the water to approve it for release. In one case, Geldreich reported the finding of a piece of wood construction material embedded in a new main that contributed to coliform contamination. Thus, new materials need inspection and some form of disinfection before they are exposed to drinking water. The physical cleanliness of new pipe is important to guarantee that post-installation disinfection will be successful (Geldreich, 1996). The installation or rehabilitation of facilities such as storage reservoirs with floating covers must include water quality checks for health and aesthetic considerations and not assume that new materials and their installation will be free of contaminants (Krasner and Means, 1986).
The installation process for buried pipe is not the only place where contamination can occur. The storage of pipe, pipe fittings, and valves along roadways or in pipe yards prior to installation can expose them to contamination from soil, stormwater runoff, and pets and wildlife. Damage to pipes prior to their installation is also possible, such as during pipe storage and handling or actual manufacturing defects such as surface impurities or nicks.
Regardless of where and how materials become contaminated, the hope is that post-installation disinfection will be sufficient to kill any introduced bacteria. This is not always the case, however, as evidenced by a coliform event in Florissant, Missouri in 1984 (Geldreich, 1996). The coliforms detected in a storage tank were thought to be the result of inadequate disinfection following new pipe installation or repair. Unfortunately, contaminated water subsequently passed into the distribution network. No direct public health outcome was reported; however, the “repeated reissuance of boil-water orders caused a loss of confidence” in the water utility by the public (Geldreich, 1996).
It is unclear how often faulty materials are installed or good materials are improperly installed because most utilities do not keep records that would facilitate the evaluation of this problem. Sufficient standards exist for materials quality and for the certified testing of materials quality. Water utilities can incorporate existing standards into contracts and specifications for materials and materials installations, and most if not all water utilities already do this. Water utilities can also certify and decertify manufacturers and contractors.
Absence of a Barrier
Points in a plumbing system where nonpotable water comes into contact with the potable water supply are called cross connections, and a backflow event occurs when nonpotable water flows into the drinking water supply through a cross connection. The use of backflow prevention devices can be extremely effective in eliminating this type of contamination event. The absence of such devices, which is widespread given the highly variable nature of cross-connection control programs across the country, constitutes a potential threat to the physical integrity of distribution systems. Backflow protection devices are seldom installed on domestic service lines and even on many small business service lines. Operational failure of devices that are in place is akin to having the device not be present.
Similar issues surface for storage facilities that do not have adequate protection to prevent their contamination. There are 154,000 treated water storage facilities in the United States (AWWA, 2003) encompassing a variety of types including elevated tanks, standpipes, open and covered reservoirs, underground basins, and hydropneumatic storage tanks. Storage facilities are susceptible to external contamination from birds, insects, other animals, wind, rain, and algae. Indeed, coliform occurrences have been associated with birds roosting in the vent ports of covered water reservoirs (Geldreich, 1996). This is most problematic for uncovered storage facilities, although storage facilities with floating covers are also susceptible to bacterial contamination due to rips in the cover from ice, vandalism, or normal operation. Even with covered storage facilities, contaminants can gain access through improperly sealed access openings and hatches or faulty screening of vents and overflows. Four reported waterborne disease outbreaks have been associated with covered storage tanks, in particular, a Salmonella typhimurium outbreak due to a bird contamination of a covered municipal water storage tank (Clark et al., 1996). Such events can be aggravated by the loss of disinfectant residual that storage tanks typically experience with increasing water age.
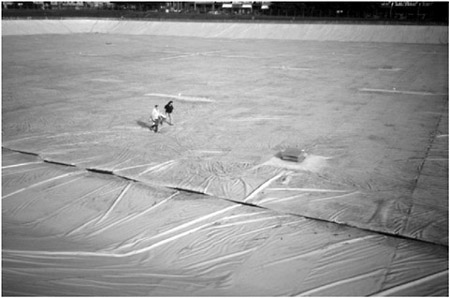
Preparing to sample stored drinking water from the access hatch of a floating cover on a distribution system reservoir. Photo courtesy of Bureau of Laboratory Service, Philadelphia Water Department.
CONSEQUENCES OF A LOSS IN PHYSICAL INTEGRITY
A loss of physical integrity implies a breakdown in the barrier that prevents contact between the external, unsanitary environment and the internal, drinking water environment. The water quality effects that can result include the introduction into the distribution system of microbial and chemical contaminants, debris, and particulate matter, sometimes accompanied by changes in water color, turbidity, taste, and odor. Whether a breach in physical integrity results in exposure of the public to contaminants at levels posing an unacceptable risk is dependent on site-specific conditions. As revealed in Chapter 3 and Appendix A, most documented cases of waterborne disease outbreaks that can be attributed to distribution systems have been caused by breaches in physical integrity. For example, a review of 619 reported waterborne disease outbreaks in the U.S. between 1971 and 1998 found that over one-half of the outbreaks in distribution systems were due to cross connections and backflow (Craun and Calderon, 2001). Of the 12 largest outbreaks, seven were associated with cross connections, three with contaminated storage tanks, and two with water main contamination during installation or repair. Overall, in community water systems, cross connections were the number one cause of distribution system-related outbreaks, contaminated mains were number two, and contaminated storage facilities were number three. In non-community water systems, contaminated storage facilities were the second leading cause. The contaminants
involved have ranged from pathogens such as Giardia, Norwalk virus-like agents, hepatitis A virus, Campylobacter, Salmonella, Shigella, and E. coli 0157:H7 to chemical contaminants such as copper (the most commonly reported chemical), chlordane, nitrite, ethylene glycol, and oil (Craun and Calderon, 2001).
Not all of what can enter a distribution system from a failure in a physical barrier will have a known or direct health impact. Particulate matter and other debris can gain entry during main breaks; reservoir cover, hatch, or vent failures; and during repair, installation, and maintenance activities. Utilities have reported particulates in distribution system water that included such things as sand, patina, pipe joint materials, rubber gasket chunks, insect pieces, plant fibers, and glass chips, many of which are likely to have no direct health impacts (Booth and Brazos, 2005).
Changes in taste and odor, turbidity, and color typically provoke customers to complain (Burlingame, 1999a,b; McGuire et al., 2004), but may present little direct public health risk. This is because aesthetic problems often occur at contaminant concentrations far below the known health effects levels. For example, color problems derived from iron or manganese introduced into drinking water during a backflow event from a fire service connection or a heating system are unlikely to pose a health risk. On the other hand, color problems can also indicate backflow events that have health risks associated with them such as with ethylene glycol or corrosion inhibitors from HVAC and fire service connections. The sections below discuss the typical consequences of the loss of physical integrity in pipes, fittings and appurtenances; storage facilities; and backflow prevention devices.
Contamination of Mains, Fittings, and Appurtenances
Pipe interior, appurtenances, and related materials can be exposed to microbial and chemical contaminants in the external environment (1) during water main failures and breaks and (2) due to human activities to install new, rehabilitate old, or repair broken mains and appurtenances. When a pipe break or failure occurs, there is immediate potential for external contamination from soil, groundwater, or surface runoff to enter the distribution system or come into contact with the pipe interior in the area of the failure. Other less dramatic types of structural failure, such as the development of cracks or leaks in pipe, pipe joints, or appurtenances, can also provide avenues for distribution system contamination during periods of low pressure or a pressure transient—an event known as intrusion. Intrusion refers to the flow of nonpotable water into drinking water mains through leaks, cracks, submerged air valves, faulty seals, and other openings resulting from low or negative pressures. Discussed in greater detail in the next chapter, intrusion can exist undetected for long periods of time. A prominent example of a waterborne disease outbreak being caused by a main break and intrusion is presented in Box 4-1.
BOX 4-1 Waterborne Disease Outbreak Associated with Main Breaks and Intrusion: Cabool, Missouri In the winter of 1989–1990, Cabool, Missouri, a town of approximately 2,100 people, experienced a large outbreak of E. coli O157:H7. A total of 243 cases were reported, with 32 hospitalizations and four deaths. This was the first documented waterborne outbreak of E. coli O157:H7 and the largest waterborne outbreak of E. coli O157:H7 before the 2000 outbreak in Walkerton, Canada. The town’s water system (untreated groundwater) was implicated in the outbreak. Two of the town’s four wells were operating at the time of the outbreak: one was 305 meters deep and the other was 396 meters deep. Both wells had protected wellheads, and the monitoring data from the ten years before the outbreak indicated that no coliforms had been detected in either well. Investigation of the outbreak indicated that the distribution system was not well maintained and was vulnerable to sewage contamination at several points. Approximately 35 percent of the total flow was lost in the system—suggesting leaks, inaccurate meters, or unmetered connections. The town sewer system was also in poor condition and operating beyond capacity, resulting in regular sewage back-ups and overflows. As with most waterborne disease outbreaks, a constellation of risk factors contributed to this outbreak. In mid-December 1989, unusually cold weather caused two large water mains and 45 in-ground water meters to fail (Figure 4-1). Ten cases of bloody diarrhea were reported to the local health department on January 4, 1990. A boil-water order was issued on January 5, and water chlorination was initiated on January 12. Analyses of the temporal distribution of the cases indicated that the first cases occurred seven days before the first water main break (December 23), and the last case occurred three days after the implementation of water chlorination (Figure 4-2). The early cases may have been due to leaks and holes that developed prior to the main break. There was a small increase in the incidence of diarrhea after the first main break and a large increase in diarrhea cases about four days after the second main break on December 26. ![]() FIGURE 4-1 Map of Cabool, Missouri with sites of water main breaks. SOURCE: Reprinted, with permission, from Swerdlow et al. (1992). © 1992 by American College of Physicians. |
The storage, installation, rehabilitation, and repair of water mains, fittings, and appurtenances provide another opportunity for microbial and chemical contamination of materials that come into direct contact with drinking water. Pierson et al. (2001) noted that this was particularly prevalent during the handling and storage of distribution system materials and during their installation in the trench. Indeed, a survey of water utilities found that about 14 percent experienced positive coliform samples from 1 to 10 percent of the time that new mains are checked before they are released (Haas et al., 1998).
Studies have demonstrated that the soil surrounding buried pipe can be contaminated with fecal indicator microorganisms and pathogens (Kirmeyer et al., 2001). Besides contaminated soil, runoff from streets and agricultural land can be highly concentrated with microbiological and chemical contaminants (Makepeace et al., 1995), and this runoff can contaminate pipes during a main break, during the unprotected storage of pipe materials, and even during pipe installation in the trench. One of the culprits in this regard are sewer lines that run in close proximity to distribution system mains. Leaking sewers can contaminate the soil and groundwater in the area of a water main or a trench where main activity will take place. The general rule is that there should be a horizontal separation of at least 10 ft (3 m) between water and sewer lines, and that the water line should be at least 1 ft (0.3 m) above the sewer (although variations to this general rule may occur from state to state). This rule, however, is fairly recent in comparison to the average age of the nation’s buried infrastructure.
A second major mechanism of pipe failure is permeation, where contaminants external to the pipe materials and non-metallic joints compromise the structural integrity of the materials and actually pass through them into the drinking water. Taste and odor events are common consequences of permeation of plastic pipe given the types of contaminants involved. For example, in one case solvents trapped beneath a polyethylene wrap and soil migrated through plastic pipe and pipe connections to contaminate the drinking water in the service lines (Burlingame and Anselme, 1995). Because the solvents were derived from a hot-butyl rubber coating applied to the external surface and ferrules of a ductile iron main, they included toluene, indan, indene, naphthalene, xylene, and benzofuran. The event was initially detected first by customer complaints about off odors. In addition to the taste and odor issues, continued exposure to solvents can change a pipe’s integrity and eventually lead to pipe failure.
Although there is the potential for water quality degradation as a result of the permeation of plastic pipe, the health impacts associated with such permeation are not well documented nor are they expected to be significant. In some permeation incidents, the concentrations of certain chemicals have been shown to reach levels in the low parts per million, which are well above their respective maximum contaminant levels (MCLs) (AWWA and EES, Inc., 2002). However, these MCLs are based on long-term exposure, and the short-term risk levels for these chemicals are generally much higher. In the case of permeation by gasoline components, the taste or odor thresholds of the majority of these chemicals are below the levels that would pose a short-term risk (EPA,
2002a,b,c,d), such that customers would notice an objectionable taste or odor in the water before significant exposure. In addition, these high concentrations would be expected to occur during worst case situations where water has been in contact with the affected pipe for a considerable length of time. During periods of normal water use, these concentrations would be expected to be much lower. It should be noted that the taste and odor thresholds for some contaminants may be above the MCL, in which case permeation of these chemicals could result in undetected long-term exposure if monitoring of these chemicals in the distribution system is not conducted.
Contamination of Storage Facilities
Although they may suffer from structural failures, storage facilities are most susceptible to external contamination due to the absence or failure of an essential component, such as a cover, vent, hatch, etc. The complete absence of a cover or vent on a storage facility can allow birds access to the tank and subsequently introduce microbial pathogens such as bacteria and parasites to the water within. For example, in the winter of 1993 a waterborne disease outbreak of salmonellosis in Gideon, Missouri, was traced back to the contamination by birds of the public water supply’s distribution system storage tank (see Box 4-2; Clark et al., 1996). Indeed, one water storage tank connected to the distribution system was found to have holes in the top and bird feathers floating in the water. Two other storage tanks were found to be in similar need of maintenance, and pigeons were found roosting on the tanks. Birds, and consequently bird excrement, are probably the biggest concern for storage tanks and reservoirs with floating covers. Sea gulls, for example, can be found roosting at storage facilities. Open reservoirs also offer the opportunity for detrimental changes in water quality because of exposure to the atmosphere or sunlight, such as changes in pH, dissolved oxygen, and algal growth.
Even when covered, storage facilities can suffer from algal growth on the tops of floating covers that can gain entry into the tank through rips and tears or missing hatches. Algae can also be airborne or carried by birds and gain entry into storage tanks through open hatches and vents. Algae increase the chlorine demand of the stored water, reduce its oxygen content upon their degradation, affect taste and odor, and in some cases release byproducts.
Chemical contaminants gain access to storage facilities via air pollution and surface-water runoff into open storage reservoirs. For example, accidental spills of chemicals during truck transport on highways adjacent to reservoirs are a potential threat, and can be very serious if the chemicals are present in a concentrated form and highly toxic (Geldreich, 1996). Surface-water runoff into open reservoirs can also introduce pesticides, herbicides, fertilizers, silt, and humic materials from nearby land. The potential for chemical contamination of storage facilities continues to be overlooked in regulations in comparison to microbial
BOX 4-2 Waterborne Disease Outbreak Associated with Contamination of Water Storage Tanks: Gideon, Missouri In 1993, the town of Gideon, Missouri (pop. 1,100) suffered from an outbreak of salmonellosis that affected more than 650 people and caused seven deaths. The Gideon water system consisted of two deep wells (396 meters) with no treatment or disinfection and a water distribution system that dated to the 1930s. In early November 1993, a cold snap caused a thermal inversion in the water storage tanks that resulted in taste and odor problems. In response, the water system was systematically flushed on November 10. The first cases of acute gastroenteritis were reported on November 29 and diagnosed as Salmonella typhimurium. However, the outbreak investigation later revealed that diarrhea cases in Gideon started around November 12 with a peak incidence around November 20. By early December, there was a 250 percent increase in absenteeism in the Gideon schools and a 600 percent increase in anti-diarrheal medication sales. Over 40 percent of nursing home residents suffered from diarrhea and seven people died. The outbreak was not linked to the water system until December 15 when the water system samples were reviewed and investigative water sampling was initiated. A boil-water advisory was issued on December 18. On December 22nd, emergency chlorination was added to the production well and the two municipal storage tanks were superchlorinated. The last reported cases occurred on December 28. Water samples collected from a hydrant in the distribution system on December 16, 17, 20, and 21 were positive for total coliforms, and the samples from December 20 and 21 were also positive for fecal coliforms. Inspection of the two municipal water storage tanks suggested that the outbreak was probably caused by bird feces in one or more of the tanks. The larger of the tanks was in disrepair and had birds roosting on the roof. A third private storage tank had an unscreened overflow pipe and a hole at the top of the tank that was large enough for birds to enter. This private tank had been drained on December 30, but tJhe outbreak strain of S. typhimurium was detected in samples of sediment collected on January 5, 1994. The remaining water on the bottom of the tank was described as black |
contamination. For example, the Long Term 2 Enhanced Surface Water Treatment Rule requires that water systems with uncovered finished water storage reservoirs cover the reservoir or treat the reservoir discharge to the distribution system to achieve a 4-log virus, 3-log Giardia, and 2-log Cryptosporidium inactivation, the latter of which would not protect against chemical contamination. However, it should be noted that EPA has published a Guidance Manual on Uncovered Finished Water Reservoirs (EPA, 1999) that addresses chemical contamination. Although the actions contained in the manual are not mandated, some states (such as California) are requiring water systems to implement them.
Contamination Due to the Absence or Operational Failure of Backflow Prevention Devices
Backflow events via unprotected domestic, commercial, industrial, and fire connection services can introduce contaminants into the potable water supply, with potentially profound health implications. A recent survey (USC, 2002) found that more than 95 percent of sampled homes had direct or indirect cross
and very turbid, with rust, suspended particles, and bird feathers floating on the top. Initially attention was focused on the private tank as the source of the outbreak as reported by Skala (1994). However, an in-depth hydraulic analysis of the Gideon system, conducted as part of the outbreak investigation, raised questions about the possibility of the private tank being the source of the outbreak. A subsequent review of as-built drawings of the Gideon system by Missouri Department of Natural Resources personnel revealed that the private tank was separated from the municipal system by a functioning backflow prevention valve. In a subsequent hydraulic analysis the private tank was eliminated as a contamination source for the outbreak, which led to results that were consistent with the behavior of the system as observed during the outbreak scenario. This analysis also pointed to the largest municipal tank as the most likely source of the outbreak. A visual inspection of the large municipal tank revealed broken and rusted hatches and bird parts and feathers on the top of the tank and floating on the surface of the tank water. Both Clark et al. (1996) and Angulo et al. (1997) concluded that the large municipal tank was the source of the outbreak. In the end, the outbreak investigation concluded that the cold weather in early November caused a thermal inversion in the water storage tanks that mixed the contaminated upper layers of stored water with the water entering the distribution system. The widespread flushing program on November 10 served to draw more contaminated storage tank water into the distribution system than under normal operation. The large discharge of the stored water over a short period of time may also have stirred up sediments in the tank and introduced them into the distribution system. Hydraulic modeling indicated that the part of the distribution system that served the school and the contaminated fire hydrant would have received water from the problem municipal tank within the first six hours of flushing. Other contributing factors included late recognition of the outbreak by the public health authorities, late recognition that the outbreak was linked to the public water supply, and a low rate of compliance with the boil-water order. SOURCES: Skala (1994), Clark et al. (1996), Angulo et al. (1997), Hrudey and Hrudey (2004). |
connections (“direct” meaning a cross connection subject to both backpressure and backsiphonage while an “indirect” cross connection is subject to backsiphonage only). Because of the enormous range of contaminant sources involved, as well as the number of unprotected cross connections, backflow events collectively constitute the greatest potential health risk from distribution system contamination. Whether an individual backflow event poses a risk depends on the type of the contamination, the length of an individual’s exposure to the contaminated water, and other factors. A survey of water utilities in North America found that 28.8 percent of cross connections resulted in bacteriological contamination whereas 26.1 percent resulted in chemical contamination, and 29.8 percent resulted in both bacteriological and chemical contamination (Lee et al., 2003).
Although their potential to occur is high in all systems, backflow events are a particular concern in dual distribution systems where one line carries a nonpotable water source that may become connected with a potable source in the other line. Generally, the nonpotable line is a substantial health risk because it carries
reclaimed water containing chemicals and microbial pathogens at levels exceeding water quality standards.
One of the most well known backflow events affected two Chicago hotels in 1893 during the World’s Fair (Columbian Exhibition). A loss in water pressure in the distribution system caused backsiphonage through cross connections which contaminated the hotels’ drinking water. An amoebic dysentery outbreak resulted in over 1,400 illnesses and at least 98 deaths (Von Huben, 1999). It is likely that the frequency and magnitude of contamination events due to cross-connections is underreported, especially where premise plumbing is involved. Box 4-3 describes a waterborne disease outbreak associated with an unprotected cross connection.
DETECTING LOSS OF PHYSICAL INTEGRITY
In some cases, a loss in physical integrity might actually be observed, such as a hole or tear in a reservoir cover, a missing vent or hatch on a storage facility, or a flooded meter or valve pit. Other structural failures, such as pipe leaks, tend to be much less obvious. The ability to predict and detect a failure in a material barrier is a desired capability for any water supplier. Structural failure is predictable for all major infrastructure components given information about materials composition and age and the surrounding environment. Structural integrity and operational performance should be confirmed on a regular basis via testing and inspections, particularly for backflow devices and storage facilities. The lack of standards and proper training can be predictive of a loss of physical integrity due to the improper installation, repair, or replacement of infrastructure components.
Predictions of structural failure can often be made based on historical information. For example, much is known about iron pipe based on years of actual experience. Cast iron pipe has been shown, under the right conditions, to last 100 years and more. When first introduced, cast iron pipe had no internal lining or external coatings to protect it from corrosion. After 1860, most pipes were lined with a molten tar pitch, and after 1922 some pipes were lined with a cement-mortar lining which in turn is sometimes protected by an asphaltic sealcoat. By the mid 1950s, ductile iron pipe came into use that has about twice the strength as cast iron but with a reduced wall thickness. This thinner wall pipe is more forgiving during installation and is more resistant to damage (AWWA, 2005b). It can be protected from external corrosion by a polyethylene wrap. AWWA/ANSI standards exist for pipes, joints, wraps and epoxy coatings, and fittings, and they provide information on the lifetimes of these materials.
The drive to predict and prevent failures varies depending on the consequence of the failure (Makar and Kleiner, 2002). For example, a branched distribution system has greater consequences associated with failure compared to a grid/looped system. There has been much attention given to predicting pipe failures, and more attention is needed in order to better predict overall system
reliability (Grigg, 2005). Most useful would be a user-friendly guidance manual for utilities regarding the failure mechanisms of different types of pipes and how to use the various types of information on the current condition of the pipe to determine its expected lifetime.
Table 4-5 summarizes common methods used to detect a failure in a material barrier based on the types of failures that can occur. Inspection, direct testing, and consumer complaints play a significant role. Water quality testing may be the least effective means for detecting a loss in physical integrity, and thus is not discussed extensively.
The sections below discuss the role of inspections, condition assessment of infrastructure, leak detection, main break monitoring, and water quality monitoring for both prediction and detection of physical integrity. It is hoped that water utilities will embrace these activities and keep appropriate records in order to identify those factors that lead to failures, recognize early warning conditions, and improve their overall prediction capabilities. Integrating all of these data streams in order to plan how and where to rehabilitate, repair, or replace infrastructure is a significant challenge for water utilities and yet essential to being proactive in deterring contamination events that would pose a risk to public health (Martel et al., 2005). This chapter does not focus on failure analysis, which is the systematic investigation into the causes of pipe failure by visual
TABLE 4-5 Examples of Ways to Detect a Loss in Physical Integrity
Component |
Mechanism of Integrity Loss |
Detection by |
Pipe |
Permeation |
VOC testing, investigate customer complaints about taste/odor |
Structural failure (leak) |
Leak detection, investigate customer complaints |
|
Structural failure (break) |
Investigate customer complaints, pressure monitoring |
|
Improper installation |
Inspection |
|
Unsanitary activity |
Inspection, water quality testing |
|
Fitting and appurtenance |
Structural failure |
Inspection, pressure monitoring, investigation of customer complaints, leak detection, detection of operational failures |
Improper installation |
Inspection |
|
Unsanitary activity |
Inspection |
|
Storage facility wall, roof, cover, vent, hatch |
Structural failure (crack, hole) |
Inspection, water quality testing |
Absence of |
Inspection, water quality testing |
|
Improper installation |
Inspection |
|
Unsanitary activity |
Inspection, water quality testing |
|
Backflow prevention devices |
Absence of |
Inspection, investigate customer complaints |
Improper installation |
Inspection, investigate customer complaints |
|
Operational failure |
Inspection, investigate customer complaints |
BOX 4-3 Waterborne Disease Outbreak Associated with a Cross-Connection in the Water Distribution System: The Netherlands A new housing development in the central part of the Netherlands was built with a dual distribution system. One set of pipes carried drinking water and a second set of pipes carried water from the same source that received partial treatment and was designed to be used for toilet flushing, laundry, and garden irrigation (“economy water”). Both the drinking water and the economy water originated from a surface water source and were treated by coagulation, flocculation, sedimentation, and rapid sand filtration. The drinking water was further treated by dune filtration. Approximately 30,000 households were served by this dual distribution system. On December 3, 2001, the water utility received complaints from two people living in one neighborhood of the development that the drinking water had an unusual taste and odor. Drinking water samples collected on December 4 indicated unusually high coliform levels. On December 5 and 6, the water utility issued a boil-water advisory. On December 6, a local physician informed the public health service that he had seen an unusually number of cases of gastroenteritis with nausea, vomiting, and diarrhea in his clinic over the past few days. Further investigation of the water system revealed that when maintenance work was done on November 29, the drinking water system had been connected to the economy water system in order to flush and clean it, and that the workers had failed to remove the cross-connection when the economy water system was put on-line again. In addition, the economy water supply lines were under higher pressure than the drinking water lines, which forced the economy water to enter the drinking water distribution system. This cross-connection was removed on December 6, E. coli concentrations in the drinking water system dropped to below detection limits on December 12, and the boil-water advisory was lifted on December 17. A 1,000-liter sample of the economy water collected on December 20 was found to contain approximately 1.6x103 PCR-detectable units of norovirus. Southern blot hybridization identified the norovirus isolate as a genogroup I virus. Two retrospective studies were conducted to determine the effect of this cross-connection on the rates of gastroenteritis in the housing development. The first was a retrospective cohort study that compared the incidence of gastrointestinal symptoms and other health symptoms during the period of November 29 through December 9 among 412 households in the area exposed to the cross-connection to the incidence of symptoms among 486 households in an adjacent control area that also had the dual distribution system but was not affected by the cross-connection. Data on symptoms and normal daily water consumption were collected by a one-time questionnaire that was mailed out to over 900 households in the exposed area and over 1,600 households in the control area. In addition, over 400 stool collection kits were mailed to randomly selected households equally divided between the exposed neighborhood and the adjacent control neighborhood, and the households were asked to provide a stool specimen from one member of the household who had recently experienced gastroenteritis. The results of this study indicated that during the period of November 29 through December 9, households in the exposed area experienced significantly higher illness rates than households in the adjacent control area. In the exposed area, the rates of diarrhea, vomiting, nausea, abdominal pain, and chills were twice as high (38–54 percent of exposed households) as the rates reported from the control area (19–28 percent). The reports of blood in stool were about four times higher, and the reports of itching were over six times higher in the exposed neighborhood compared to the control neighborhood. However, these symptoms were rare (1–3 percent blood in stool, 1–5 percent itching). Households in the exposed area were 1.5 times more likely to seek medical care during the period of November 29 to December 9 than households in the control area. There was no |
significant difference in the reported rates of coughing and sneezing in both neighborhoods or in the reports of symptoms that occurred after December 9. Interestingly, the distribution of symptom reports over time indicated that a peak in gastroenteritis symptoms occurred in both communities around December 3–5, but the peak was lower and shorter in the control community. Although the adjacent control community experienced a lower incidence of gastrointestinal symptoms, the rates during this time were still higher than normal. Also, there was clear evidence of a dose-response effect in both communities with significantly higher rates of households with diarrhea in those who reported higher water consumption (chi square for trend of 51.26 for the exposed area and 23.47 for the adjacent control area, p<0.01 for both communities). Analyses of the 53 stool samples that were sent from 31 exposed households and 22 households in the adjacent control area yielded one norovirus genogroup I strain and one Giardia lamblia isolate from the exposed neighborhood and one norovirus genogroup II strain from the control neighborhood. The second norovirus strain came from a household that reported gastroenteritis symptoms after December 9. The second retrospective investigation was a survey of two health care facilities for cases of gastroenteritis during the period of November 26 – December 12, 2001. One health facility served both the exposed (pop. 1,866) and adjacent control (pop. 2,875) areas in the cohort study. The other health facility was farther away and served a different part of the housing development (pop. 5,788) that was not exposed to the cross-connection incident in the distribution system but was still served by the dual distribution system. Based on the computer database of date of visit, patient address, and diagnosis codes, the incidence of gastroenteritis cases seeking medical care was compared between the three communities. Residents in the exposed area had a rate of 19.8 cases per 1,000 inhabitants compared with 7.0 cases per 1,000 in the adjacent control area and 3.3 cases per 1,000 in the more distant control area. The rate of gastroenteritis cases seeking medical care increased markedly in the exposed area and moderately in the adjacent control area on December 3 –5 and again on December 10–11 (weekdays). There was no change in the rate of diagnosed cases of gastroenteritis in the distant control area during this time period. Taken together, the results of these two retrospective studies suggest that an outbreak of gastroenteritis, probably due to noroviruses, occurred shortly after the cross connection between the economy water distribution system and the drinking water distribution system was created. It is notable that there appeared to be an increased risk of gastroenteritis in the adjacent control community that reportedly was not affected by the cross-contamination incident. This may have been due to secondary transmission from the exposed community to the adjacent control community by other routes (food, person-to-person) because these two communities shared several facilities located in the control community (schools, health center, supermarket) or consumption of contaminated water by visitors from the control community to the exposed community. Studies of the surface water source in the spring of 2001 indicated high concentrations of noroviruses of up to 1.4×104 PCR detectable units per liter, and it is unlikely that these viruses would have been completely eliminated by the treatment processes used for the economy water. Noroviruses (1.6×103 PCR detectable units per liter) were also detected in the economy water on December 20. It is possible that exposure to the economy water in this system through aerosols from toilets, laundry, or garden irrigation may have posed some risk to the inhabitants in this development even without the cross-connection incident. SOURCE: Cooperative Research Centre for Water Quality and Treatment (2003). |
means and other inspection tools in order to determine the point where the failure started and the specific type of failure. Makar et al. (2005) discusses the actors that can cause failure such as flaws in the material (inherent to its manufacture or produced afterwards), forces that exceeded the design strength, design that did not account for normal operating loads, or some combination of the above.
Inspections
Regular inspections of the distribution system, either visual examination of the various structures or via acoustic leak detection and pressure monitoring (discussed below), provide the most direct way to detect a failure in the material barrier. Storage facilities need to be inspected on a routine basis for vandalism, settling, cracking and spalling, seepage, leakage at seams and joints and in the roof, missing hatches and vents, rust and corrosion, cathodic protection, and failing structures (AWWA, 1986). A second critical type of inspection is to check both the material integrity and the cleanliness of pipe prior to installation. Even though it is often assumed that pipe is inspected before it leaves the factory, damage to the spigot end of the pipe, the exterior, and the internal lining can occur during pipe storage and handling. Another reason to inspect pipe prior to installation is to detect manufacturing defects such as surface impurities or nicks, which are likely to induce corrosion and pitting once installed (Von Huben, 1999). Finally, pipe should be examined before installation for oil, dirt, grease, animals, and foreign matter; if found, the pipe should be cleaned out with a strong hypochlorite solution.
An important opportunity in this regard is the sanitary survey, which is a broad review and inspection program for a water utility that occurs once every three to five years. The survey might reveal an absence of (1) training and certification, (2) use of standards, and (3) routine inspections, all of which could be predictive of a loss of physical integrity. This is because a lack of training, certification, inspection, and standards often lead to the improper installation and application of materials (for example, using the wrong backflow prevention device or installing plastic pipe in contaminated soils).
Monitoring the Condition of Buried Infrastructure
The various tools available for locating buried pipe include ground-probing radar, metal detectors, magnetic locators, and radio transmission units for metallic pipe (Von Huben, 1999). Similar methods can be used to detect non-metallic pipe if metallic tapes or tracer wire was installed with the pipe. Locating pipe is the first step of condition assessment. A condition assessment is based on the assumption that materials or infrastructure components deteriorate, with the goal of gathering information to predict the need for repair, rehabilitation, or re-
placement (Grigg, 2005). The three steps of condition assessment are (Morrison, 2004):
-
Develop an up-to-date inventory of assets. With pipes, a Geographic Information System (GIS) can be used to collect the following data: diameter, material, classification/grade, wall thickness, joint type, installation date, lining and coating types, corrosion protection system, depth of burial, soil conditions, groundwater level, bedding classification, and history of problems (Shamsi, 2005).
-
Inspect the internal pipe condition, pipe wall condition, pipe environment condition, and leakage (which can be difficult and costly to accomplish for buried, in-use pipe).
-
Rate the condition of the asset.
There are five categories of pipe rating used during condition assessment (Morrison, 2004):
Rank 5. In danger of immediate failure, requires emergency repair or replacement as soon as possible to avoid jeopardizing public health and safety.
Rank 4. Severely deteriorated and in need or repair, renewal, or replacement. Should be addressed immediately.
Rank 3. Mildly deteriorated, short-term performance just adequate; however, will require renewal or replacement soon. Capital improvement plans are needed with more frequent inspections.
Rank 2. Minor deterioration, performance adequate. An inspection or assessment plan should exist.
Rank 1. Little to no deterioration, performance more than adequate.
Condition assessment requires information from existing pipe to help predict the lifetime of pipe still in use. To make the exercise more economically feasible, it might be done for selected pipes that represent a cross section of installed pipe materials and installation dates. Within some utilities, condition assessment is conducted whenever pipe repairs are made or new pipe is installed, because existing pipe is exposed, which facilitates the assessment. Other utilities carry out a regularly scheduled assessment program independent of other activities. Whatever the final outcome, how and when condition assessments will be conducted should be determined and standardized at each utility.
The technologies available to carry out condition assessment are varied and mature. Destructive testing includes the use of coupons or cuts from actual sections of pipe and spot condition assessment. Nondestructive testing include magnetic, electromagnetic, sonic, acoustic, infrared thermography, and ground-penetrating radar equipment for locating pipe; global positioning system (GPS)/GIS databases for managing information; and ultrasonics, acoustic emission, magnetic flux leakage, and remote field eddy current for assessing pipe. Finally, closed-circuit television has been used in some situations. For the most
part there are sufficient tools available to allow utilities to conduct condition assessments and to utilize the data that are collected to guide decisions. What is needed is for these tools to be utilized more uniformly as well as fine-tuned for use in small systems that have more limited capabilities. It would be extremely useful for the results of condition assessments to be shared among utilities, and even benchmarked, so that utilities can build upon shared experience and knowledge.
Future tools for assessing the condition of buried pipe include real-time tools that travel through pipe and collect information; small chips set in pipe; sensors to record sounds of breaks; fiber optics to record breaks in light; and improved metering to identify leaks (Grigg, 2005). These tools are in development and likely show promise for specific situations rather than globally for all materials in all circumstances. For example, different sensors are needed for plastic pipe than for iron or concrete pipe.
Leak Detection
The early detection of leaks and their remediation is a goal for water utilities. Leak detectors include listening devices, such as an aquaphone or a more complicated amplified detection kit that detects sound caused by flowing or escaping water (Von Huben, 1999). Another way of detecting leaks is to conduct a water audit which uses flow meters around smaller districts of a system at night when water use should be low. Acoustic methods are easy to use and widely applied on metallic pipes, with improvements being made for use on plastic pipes (Lange, 2002). Morgan et al. (2005) recently used a fixed-based acoustic monitor system called MLOG to scan the distribution system at night for leaks. The system was highly effective, detecting 17 previously unknown leaks within the first three months of use.
In addition to improvement in leak detection, water meters have been developed to detect and record backwards flow through the meter in order to determine the magnitude and frequency of backflow events (Neptune Technology Group, 2005). Although the majority of this flow may simply be service line water, the use of advance meter reading can detect these backflows in real time. The ability to detect and track backflow events will allow more focused monitoring to determine their impact on drinking water quality.
Main Break Monitoring
Main break monitoring consists of utilities recording responses to water main breaks such as time and date of response, location of break, valves operated to shut down the main, properties affected by the shut down, repaired or replaced portion of main, and shut-down time. Transmission mains are given a higher priority for main break monitoring and the prevention of failure than
smaller size distribution mains, given their potential seriousness (for example, destruction to local structures such as roadways, bridges, and buildings or interruption of automobile traffic and the evacuation of residences).
If main break monitoring data are maintained in a computerized database, then quarterly, annual, or five-year historical evaluations can be done, trends can be predicted, and both can be compared to changes in related practices (such as replacing cast iron with ductile iron pipe). If the utility can also collect data on leaks and repairs leading up to a break, as well as failure analysis results during the break, it becomes possible to develop better predictive models for the distribution system’s pipe infrastructure. Water utilities have successfully trended water main break rates and have adjusted their practices to minimize the occurrence of failures for various types of pipe in their systems. The trending of water main breaks and leaks along with condition assessment provide an important tool to minimize public health risk. Not only will a water utility reduce its risk of serious consequences from an unexpected failure, but in reducing the seriousness of such failures the water utility will gain control in minimizing the potential for water quality contamination. This will happen in two ways, because the severity of any single failure is reduced, and because the frequency of failure is reduced.
Water Quality Testing
Much of the monitoring needed to assess the physical integrity of a distribution system is accomplished by other means than water quality monitoring, such as by leak detection, customer complaint response, inspections, or the exercising of valves and hydrants. However, water quality testing can play a role. Typically, water quality analyses are limited to common chemical parameters (total chlorine residual, pH), physical parameters (turbidity, color), and biological parameters (heterotrophic plate count, total coliform count) (see Chapter 6 for a more thorough discussion). For those parameters that are routinely monitored under the Safe Drinking Water Act, a detection of a change in a parameter would not in itself identify the occurrence of a loss in physical integrity that resulted in contamination, since water quality changes could be from internal conditions in the system or from a treatment breakthrough or failure. However, a thorough follow-up response to a change in water quality (such as high turbidity, colored water, or non-detectable chlorine residual) could include valve checks, hydrant flushing, and other techniques that might identify the cause of the loss in water quality as being an external contamination event.
Water quality data can also be useful in identifying problems with physical integrity when integrated with others sets of data, such as customer complaints, water main break occurrences, timing of newly installed water mains, cleaning of storage facilities, or backflow events (see Chapter 7 for more discussion of data integration). Water quality testing is particularly useful if it can be correlated with customer complaints. For example, consumer complaints of chemi-
cal-type odors along with the utility’s detection of volatile organic chemicals (VOCs) could signal that permeation of plastic pipe has occurred, which could be further studied through groundwater and soil testing for the same VOCs. Once remediation is put in place, the same water quality parameters could be used to gauge the success of the remediation. Backflow events are another example of where customer complaints used in conjunction with water quality monitoring may be informative. Depending on the contaminants present, backflow events can affect the color of water, can introduce debris and particles, and can cause an off-odor or taste.
As with any environmental sampling, increasing the frequency of water quality monitoring, for example going to on-line monitoring of storage facility effluent as opposed to daily or weekly grab sampling, will make it more likely that a contamination event will be detected. For example, when doing water quality sampling on a new water main prior to its release for use, a typical number of samples would be four to five. If this new addition or replacement involved 100 feet of 6-inch pipe, the total volume would be around 150 gallons (568 liters), such that four water quality samples of about 250 mL would only test 1/568th of the potentially contaminated water. Clearly, the approval of a new water main should not rely solely on the final water quality check, but also on inspections at every stage of the process guaranteeing that materials were handled in a sanitary manner and protected from exposure to contamination. Thus, in isolation water quality data are not sufficient to identify failures in physical integrity. But combined with other data, they may be useful for detecting external contamination events.
MAINTAINING PHYSICAL INTEGRITY
Every water supplier’s goal is to develop the means by which to better maintain the physical integrity of its distribution system so that a failure or loss rarely occurs, or when it does occur its impact is minimized. Table 4-6 summarizes some common measures used to prevent a loss of physical integrity in the distribution system.
The maintenance issues for pipes, fittings and appurtenances, storage facilities, and backflow prevention devices are similar in a general sense. Materials selection must meet standards and best practices. Installations of all components must be followed up with routine inspections. A regular program of valve operation and maintenance must be in place so that shut downs can be effective when needed. Many valves and hydrants are unused for a number of years, and debris within the distribution system may cause hydrants to become heavily encrusted leading to a significant reduction in discharge flow and fire protection. Furthermore, valves and hydrants should be carefully manipulated to maintain positive pressures and mitigate pressure transients that could result in pipe breakage. Good construction practices, conducted by those with training and certification and that follow standards and specifications, are essential. Standard
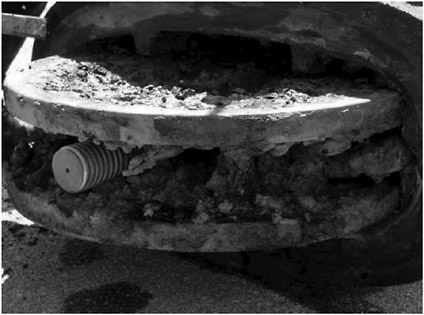
Valves should be inspected and operated on a regular basis to prevent rust and encrustation from interfering with their performance. Photo courtesy of Bureau of Laboratory Services, Philadelphia Water Department.
parts should be used to ensure consistency in repairs, and they should be stored in a sanitary fashion. Designing the distribution system to minimize sections of pipe and appurtenances that cannot be adequately tested, flushed, and disinfected would be beneficial (Pierson et al., 2002). Finally, funding and staffing must support all of these activities. These and other preventive measures are discussed below. It should be noted that maintaining the appropriate operating pressure to prevent main breaks and intrusion is discussed more thoroughly in Chapter 5.
Materials Quality
Materials that make up drinking water infrastructure range in type and value. Pumps have various components from pipe to valves to impellers, all made of differing materials. System piping includes valves and fittings, ferrules, and hydrants. Storage facilities range in their composition from concrete to steel with linings of cement, asphaltic, and epoxy. Customer premise plumbing includes meters, backflow prevention devices, valves, fittings, tubing, and faucets made of a plethora of materials. Rubber gaskets and plastic seats can be found
TABLE 4-6 Examples of Ways to Maintain Physical Integrity
Component |
Mechanism of Integrity Loss |
Prevention by |
Pipe |
Permeation |
Standards on pipe applications, local assessments of soil and groundwater for contamination |
Structural failure (leak or break) |
Better design and installation, early leak detection with rehabilitation and repair, optimized scheduling of pipe renewals, optimized placement of valves for effective shut-offs and isolations |
|
Improper installation |
Standards and certification for installation, followed by inspection |
|
Unsanitary activity |
Strict requirements and inspection during repair, rehab, installation |
|
Fitting and appurtenance |
Structural failure |
Improved materials quality as well as quality in the operating components of valves and hydrants, periodic valve exercising followed by maintenance or replacement as needed |
Improper installation |
Strict requirements on installation and design |
|
Unsanitary activity |
Strict requirements during repair, rehab, installation and inspection |
|
Storage facility wall, roof, cover, vent, hatch |
Structural failure (crack, hole) |
Better design and installation, early leak detection with rehabilitation and repair |
Absence of |
Inspection and better design with inspection |
|
Improper installation |
Strict requirements on installation and design |
|
Unsanitary activity |
Strict requirements during repair, rehab, installation and inspection |
|
Backflow prevention device |
Absence of |
Inspection and certification |
Improper installation |
Strict requirements on installation and design |
|
Operational failure |
Annual testing and maintenance |
in valves and meters and in the joints of mains. In addition to these solid materials there are greases, lubricants, fluxes, and coatings. The diversity, complexity, and value of materials used in drinking water infrastructure are important to distribution system management, especially given the increasing emphasis on system reliability and more stringent water quality demands. The following factors should be considered when choosing distribution system materials:
-
health effects of the material when in contact with drinking water;
-
hazards and safety in working with the materials;
-
structural capabilities of the material;
-
water quality impacts of the material;
-
cost and availability of the material;
-
compatibility of the material with other materials in the system and with the conveyed water and surrounding soils;
-
environmental effects of the material;
-
whether the manufacturers of the material are ISO certified and meet NSF and ASTM standards; and
-
future changes that could impact on the above.
Not all of these factors have been given equal weight. Materials selection is typically based on tensile strength, flexural strength, durability, corrosion resistance, roughness coefficient (Hazen Williams C value), and economy (e.g., the cost of materials and installation lifetime value) (AWWA, 1986). Indeed, economic considerations and the availability of the material can weigh in heavily and may dominate the choice of material.
As shown in Table 2-3, 30 of 34 responding states have some basic requirements for the types of pipe materials allowed in distribution systems. Indeed, a variety of standards and guidelines are available to help utilities choose the correct materials for their infrastructure, including the ASTM Annual Book of Standards, standards from NSF International, AWWA standards, and other publications (Nayyar, 1992). In practice, the larger water utilities tend to apply material standards and test whether they are being met, but small water utilities likely have no way to test for compliance. Furthermore, water suppliers in the United States have underutilized the services that materials engineering can provide such as manufacturer and supplier certification, development of materials specifications for procurement, and evaluation of materials (chemical and physical) according to specifications after procurement (Burlingame et al., 2002). Testing of materials to ensure they meet the standards used for procurement should be a broader practice within the water industry, and not limited to only the largest water utilities.
In addition to making an informed choice of materials, water utilities should strive to protect the quality of the materials after initial purchase. This includes inspections during materials manufacture; proper storage, handling, and transport of the material to the utility; inspection and testing of the material upon delivery; protection during onsite storage; inspection during and after installation; failure analysis to detect early failures; and finally replacement of the material when its lifetime is exceeded (see section below on asset management). Failure analysis involves using a standard approach to record events around material failures; take soil and pipe samples and collect background records; conduct a preliminary investigation to determine the type of failure; and conduct structural analyses, visual examinations, metallographic and mechanical testing, and inspections for graphitization and manufacturing flaws on pipe surfaces (Makar, 2002). Because failure analysis has not been widely embraced by the water community, there is limited information on many of the materials in common use today. Thus, additional support is needed for technology transfer about materials, funding of materials testing programs, better materials development and information management, better training, and better cross-industry networking. For example, there have been no studies to date on the conse-
quences of material failures due to workmanship/installation errors or manufacturer variability.
Another consideration is that many materials still in use today were not originally designed to meet the system reliability and water quality standards expected today and for the near future. Existing materials standards may not be complete and up-to-date for all applications. Furthermore, manufacturers are not always responsive to customer or end-user needs, especially as these needs change due to water quality regulations. Although improvement is needed in many areas, a substantial first step would be to improve installation workmanship. This could be accomplished by requiring that all trades people who work with materials being installed or repaired that come in contact with potable water be trained and certified for the level of sanitary and materials quality that their work demands.
Corrosion Control
The historical use of metallic pipes and the many environmental conditions they come in contact with have made both external and internal corrosion an issue for the water industry for some time. Although most utilities use some form of internal corrosion control to minimize color and turbidity problems and to meet the Lead and Copper Rule requirements, not all utilities practice external corrosion control, even though it is important for maintaining the physical integrity of their distribution systems, as acknowledged by 14 of 34 responding states (see Table 2-3). There is no regulatory motivation for external corrosion control in the water utility industry as there is in the oil and gas pipeline industry where corrosion control such as cathodic protection of its pipelines is mandated (Romer et al., 2004). Nonetheless, understanding the conditions that lead to corrosion and implementing a consistent corrosion control methodology can result in significant operation and maintenance savings because of the longer pipeline life.
As mentioned previously, the extent of external corrosion depends on soil conditions such as resistivity, pH, and water content; the occurrence of stray currents; contact between dissimilar metals; and bacterial activity in the environment surrounding the pipe. The testing and GIS mapping of soil conditions can help water utilities predict and plan for corrosive problems and design corrosion control (Romer et al., 2004). Unfortunately, the tools for analyzing soils prior to making water main construction decisions require further development. In addition, there is no standardized corrosivity testing method used by all water utilities. The Ductile Iron Pipe Research Association has promoted a qualitative corrosion evaluation system based on soil conditions of resistivity, pH, redox potential, the presence of sulfides, and site drainage conditions, which has been found to be dependable and accurate for determining when external corrosion control should be applied for buried iron pipe (Bonds et al., 2005). The American Concrete Pressure Pipe Association provides recommendations based on
soil chloride and resistivity. In general, methods for the analysis of corrosion include a soil corrosivity survey, a close-interval potential survey, a cell-to-cell potential survey, ultra-sonic measurements, pit depth analysis, visual inspection, corrosion rate measurements, acoustic monitoring, and failure analysis (Szeliga and Simpson, 2002).
External corrosion control methods include determining the soil conditions and then (1) selecting the appropriate distribution system materials, such as plastic pipe for use in very corrosive soils; (2) applying external metallic corrosion prevention materials at the time of manufacture, such as concrete, mortar, or asphaltic shop coat; (3) applying barrier coatings and polyurethane encasements in the field; (4) using galvanic cathodic protection or impressed cathodic protection; and (5) mitigating stray currents (Szeliga and Simpson, 2002; Romer et al., 2004). For example, Edmonton, Alberta proactively reduced the impacts of external corrosion using cathodic protection and nondestructive testing of their cast iron mains (Seargeant, 2002). Proactive measures are also important, since a variety of design options (such as using rubber-gasket bell-and-spigot joints) can affect the extent of external corrosion (Romer et al., 2004). Transmission mains are more frequently engineered for external corrosion control than distribution mains because of the greater need to prevent catastrophic failures in the larger diameter water mains.
Internal corrosion of pipe is caused by distribution system water that is corrosive to the materials with which it comes into contact. Internal corrosion is common in unlined cast-iron and steel mains and also occurs inside steel water tanks, metal service lines, and premise plumbing and appliances. Concrete pipe and cement mortar are also vulnerable to corrosion from low alkalinity, low hardness waters. Internal corrosion is generally controlled by feeding corrosion inhibitors, such as phosphates, to the water in combination with pH adjustment and alkalinity control. The mechanism of action is generally one of forming a stable scale on the pipe surface from corrosion products and water constituents that both inhibits corrosion and reduces the release of metals from scale dissolution. Inhibitors and water quality control procedures need to be tested at each site of use because of differences in source water quality, pipe materials, and pipe condition. Ductile-iron and steel pipe are generally lined with a cement mortar lining to prevent internal corrosion or contact with water. Linings can reduce the frequency of small leaks in pipes and pipe connections as a result of the high resistance of cement mortar to pressure, enhance the hydraulic characteristics of the mains, and prevent further internal corrosion damage. Finally, steel water tanks are protected by internal coatings and cathodic protection.
External and internal corrosion control practices need to be used more consistently, universally and uniformly. A manual of practice for the industry should be developed as an aid to implementing best practices. At present the best defense against corrosion relies on site-specific testing and practical experience gained at individual utilities, given the variation in materials, soils, and water quality from utility to utility. There is also a need for research to develop new materials and corrosion science to better understand how to more effec-
tively control both external and internal corrosion, and to better match distribution system materials with the soil environment and the quality of water with which they are in contact.
Permeation Prevention
Appropriate measures can be taken to minimize the occurrence of permeation, such as issuing regulations or guidelines that define the conditions under which plastic pipe should be used. The proper selection and use of PVC, polybutylene, and polyethylene plastic pipe, such as according to the soil or potential soil conditions in which the pipe will be buried, limits the potential for permeation. For example, California precludes the use of plastic pipe in areas subject to contamination by petroleum distillates (California Code of Regulations, Title 22, Division 4, Chapter 16, Article 5, Section 64624f). In addition to the pipe material, the environmental conditions around the buried pipe are also important. Utilities that install plastic water mains need to maintain an up-to-date knowledge base of the locations of underground storage tank sites, industrial spills, other developments that could discharge solvents, and their associated solvent plumes so as to avoid the contact of such contaminants with the pipe. In general, if this information can be gathered prior to laying new pipe, most if not all permeation incidents can be avoided.
Maintaining Storage Facilities
Storage facility issues are similar to other distribution system components in that materials selection, system design following standards and specifications, installation inspection, and good construction practices by those with training and certification all play a role. Many states do have some standards for storage tank design and construction, the use of vents, screens, hatches, and overflows, and they even encourage tank inspection and maintenance (see Table 2-4). However, perhaps because of their perceived peripheral role in water supply, storage tanks have not historically received the attention afforded to pipe maintenance.
Storage facilities have many purposes (see Chapter 1), such that a disciplined storage facility management program is critical to water utilities. Such a program includes developing an inventory and background profile on all tanks, developing an evaluation and rehabilitation schedule, developing a detailed tank evaluation process, performing tank evaluations, making rehabilitations and replacements when needed, and performing a one-year warranty inspection for all tanks (Wallick and Zubair, 2002). More specifically, storage tanks should be inspected for needed repairs, barrier screen replacements, and painting. Depending on the nature of the water supply chemistry, such detailed inspections should be made every three to five years, and consist of tanks needing to be
drained, sediment removed, and appropriate rust-proofing applied to the metal surfaces (such as where the water level rises and falls more frequently) (Kirmeyer et al., 1999). These inspections are in addition to daily or weekly inspections for vandalism, security, and water quality purposes (such as identifying missing vents, open hatches, leaks, and so forth).
In one of the rare documents that addresses storage facilities, Von Huben (1999) summarizes the use of air vents to allow air to enter and exit as the water level rises and falls. These vents must be screened to keep out birds and insects. In general, preventing access to the tank interior by wildlife and sediment removal are important deterrents to possible pathogen contamination and coliform colonization that should be undertaken for every tank.
Asset Management
Asset management refers to a strategy of operating, maintaining, rehabilitating, and replacing infrastructure in order to sustain a cost-effective level of service to customers. For a water utility, asset management requires collecting and analyzing data and information about all functions of the utility (customer service and support, financial, engineering, operations, maintenance) in order to make strategic decisions about the infrastructure (Paralez and Muto, 2002; Schwarzwalder, 2002; Allbee, 2004; Lockridge, 2004; Cagle, 2005). When thought of with respect to maintaining physical integrity, it refers to developing an inventory of distribution system components and determining when repair should give way to rehabilitation or replacement (EPA, 2004). Table 4-7 gives some of the typical life expectancies for pipe, storage, valves, hydrants and service lines, although it is expected that properly installed and well maintained pipes should have a service life much longer than their design lives (Morrison, 2004).
TABLE 4-7 Material Life Expectancies
Distribution System Component |
Typical Life Expectancies |
Concrete and metal storage tanks |
30 years |
Transmission pipes |
35 years |
Valves |
35 years |
Mechanical valves |
15 years |
Hydrants |
40 years |
Service lines |
30 years |
SOURCE: EPA (2004). EPA’s Note: These expected useful lives are drawn from a variety of sources. The estimates assume that assets have been properly maintained. The adjusted useful life will be equal to or less than the typical useful life. |
In order to do asset management, the water supplier needs to have condition assessment data (see earlier discussion) and management tools (such as funding, planning, and modeling tools) (Grigg, 2004). The goal of asset management is to determine the time to failure and vulnerability of individual components (like pipes) under varying scenarios. As mentioned previously, determining the condition of in-use buried pipe is currently difficult and costly to accomplish because the pipe is usually still in use, the inside needs to be assessed, and the assessment can only look at one small area of one pipe out of many associated pipes. Thus, a water utility typically lumps pipes into classes and assigns to them average failure information, and, using statistics about the system, then predicts investment needs to maintain the assets.
Beyond maintaining physical integrity, there are many important reasons for utilities to engage in asset management, including (Morrison, 2004):
-
To maintain assets at a predetermined level of service, which requires inspection and assessment in order to ascertain whether the assets are capable of providing this level of service;
-
To uncover performance issues that might hinder a utility’s ability to meet customer service expectations, or potentially lead to a catastrophic failure endangering public health and safety;
-
To control costs of rectifying or mitigating a problem, which are always much less just after inspection than after a rupture or other emergency event;
-
To tailor maintenance practices to the actual condition of the asset, and not merely base them on habit, resulting in an overall reduction in expenditure;
-
To properly plan for the retirement and/or replacement of the asset, which, if done over a period of time, will avoid any unexpected surprises.
Westerhoff et al. (2004) found that most utilities engage in asset management, although it ranges from simple maintenance programs to complicated b5usiness planning processes. Indeed, terminology, data collection, reporting, mapping, inventory control, records, and operational parameters are largely defined on a utility-by-utility basis (Grigg, 2005).
Cross-Connection Control
Proven technologies and procedures are available to mitigate the impact of cross connections on potable water quality. Well-known backflow control devices include air gaps, reduced-pressure-zone backflow preventors, double check valves, vacuum breakers, and complete isolation. Lists of approved backflow prevention assemblies can be found with the University of Southern California (USC), the American Society of Sanitary Engineering (ASSE), Underwriters Laboratories, the International Association of Plumbing and Mechanical
Officials, Factory Mutual, and the Canadian Standards Association, while the three most commonly used guidance manuals are the USC Manual of Cross-Connection Control (USC, 1993), AWWA’s Manual M14 (AWWA, 2004), and
EPA’s Cross-Connection Control Manual (EPA, 2003). The application of backflow prevention devices is based largely on the degree of hazard thought to be present. A potential threat from chemical and biological contaminants that pose a human health risk would constitute a high hazard. A low hazard would include incidents that alter the water’s aesthetic properties but do not constitute a health threat. Higher hazards are also related to the type of facility from which the threat emanates, such as hospitals, funeral homes, chemical manufacturing plants, laboratories, film processing facilities, commercial laundromats, among many others. Low hazard facilities include apartment complexes, warehouses, office buildings, and public buildings. Table 4-8 gives the recommended applications of various backflow protection devices according to the degree of hazard and whether those hazards are due to either back-siphonage (negative pressure or suction on the supply side of the device) or back-pressure (high pressure on the service side of the device).
There are generally two types of cross-connection control programs: one is a service-protection program and the other is an internal protection program (AWWA, 2004). The service-protection program is the most common one for water utilities to undertake, given their typical enforcement capabilities. This program is one of “containment,” in that any backflow incident would be contained within the customer’s facility and prevented from entering the public distribution system. This is accomplished by installing a backflow prevention device at the water meter. Water utilities are typically effective with this type of program because they readily have enforcement capability in the shut-off of the water service at the curb stop. The internal protection program is based on “elimination” or getting rid of the cross connection where it exists within a customer’s plumbing. Because water utilities typically have no authority within the premises of their customers, it is more likely that other agencies such as the local health department or plumbing code agency would maintain such a program.
Lee et al. (2003) found that more than 80 percent of responding water utilities require approved backflow protection devices and field testing of their proper operations. However, little if any information exists on whether these devices are present in customers’ premises, where 83 percent of cross connections are known to exist (Lee et al., 2003). It is probable that they are absent for a very large percentage of cross connections nationwide or not functioning properly for a small percentage of cross connections. Clearly, their increased use and regular inspection would do much to reduce public health risks from drinking water distribution systems. Indeed, for utilities operating dual distribution systems, the need for an effective cross-connection control program is paramount.
TABLE 4-8 Use of Backflow Prevention Devices by Degree of Hazard and Mechanism
Device |
Degree of Hazard |
|||
Low Hazard |
High Hazard |
|||
Back-siphonage |
Back-pressure |
Back-siphonage |
Back-pressure |
|
Air Gap (AG) |
X |
|
X |
|
Atmospheric vacuum breaker (AVB) |
X |
|
X |
|
Spill-resistant pressure-type vacuum-breaker assembly (SVB) |
X |
|
X |
|
Double check valve assembly (DC or DCVA) |
X |
X |
|
|
Pressure vacuum-breaker assembly (PVB) |
X |
|
X |
|
Reduced-pressure principle assembly |
X |
X |
X |
X |
Reduced-pressure principle detector assembly |
X |
X |
X |
X |
Double check valve detector check assembly |
X |
X |
|
|
Dual check device (internal protection only) |
X |
X |
|
|
Dual check with atmospheric vent device (internal protection only) |
X |
X |
|
|
SOURCE: Adapted from Table 3-1 in AWWA (2004). |
Basically, every state has some requirement for cross connection control (see Tables 2-3 and 2-6), and state plumbing codes define the type of cross-connection control devices that are approved for use. Unfortunately, as discussed in Chapter 2, the elements of such programs, their implementation, and oversight vary widely, partly because of the variation in available resources. In a few states, local jurisdictions are responsible for implementing a cross-connection control program. In most states, testing of cross-connection control devices is the responsibility of the customer while inspection of the devices is the responsibility of the water system or the local jurisdiction. Given this variability, Chapter 2 recommends that EPA explicitly define what an acceptable cross-connection control program should be.
RECOVERING PHYSICAL INTEGRITY
It is impossible for a distribution system of any significant size to be managed in such a way as to prevent any loss of physical integrity over time. Even a water utility with a good program of corrosion control and pipe replacement can experience an annual pipe break rate of around 750 to 850 breaks per year (Fa-
larski, 2002). Damodaran et al. (2005) gave an industry average of 0.1 to 0.3 breaks per mile of pipe per year, such that a low break rate would cause 1 to 3 breaks per year per 1,000 people served. Philadelphia tracks the number of breaks experienced for each 1,000 miles of main using a five-year moving average to smooth out the effect of weather variations. Based on historical information dating back to 1930, the average for 2001 was 212 breaks for every 1,000 miles of main—the lowest total in over 45 years and better than the national average of 240 to 270 breaks per 1,000 miles. Nonetheless, even with a water main replacement program that appears to be successful compared to the national average, every year over 600 water main breaks occur. Therefore, procedures need to be in place by which to recover from a failure in a material barrier and minimize the effects on water quality.
Table 4-9 summarizes some of the common methods used today to recover from a failure in a material barrier in order to prevent or minimize contamination of the water supply. There are several categories of recovery efforts. First, compromised materials can be cleaned, repaired, rehabilitated, or replaced. For example, leaks and small breaks can be repaired by repair sleeves or by joint sealing compounds. Storage facilities might have to be drained and cleaned following potential contamination. Another form of restoration is to treat the contaminated water. Chlorine and other disinfectants have been used to protect pipes and storage facilities against external microbial contamination, prevent
TABLE 4-9 Ways to Recover from a Loss in Physical Integrity
Component |
Mechanism of Integrity Loss |
Recovery by |
Pipe |
Permeation |
Reline or replace and conduct water quality testing |
Structural failure (leak) |
Replace or repair or rehab |
|
Structural failure (break) |
Replace or repair, flush or disinfect, conduct water quality testing |
|
Improper installation |
Replace, reinstall |
|
Unsanitary activity |
Disinfect, flush, and water quality testing |
|
Fitting and appurtenance |
Structural failure |
Replace, repair, rehab and disinfect |
Improper installation |
Reinstall |
|
Unsanitary activity |
Disinfect and flush |
|
Storage facility wall, roof, cover, vent, hatch |
Structural failure (crack, hole) |
Repair or rehab or replace, disinfect |
Absence of |
Install |
|
Improper installation |
Reinstall |
|
Unsanitary activity |
Disinfect, flush, and water quality testing |
|
Backflow prevention device |
Absence of |
Install |
Improper installation |
Reinstall |
|
Operational failure |
Replace or repair |
regrowth of nuisance organisms in response to intruded chemicals, prevent further contamination from the installation of a dirty main, and alleviate customer complaints. Both continuous disinfectant residual maintenance throughout the distribution system and dosing a section of the system with disinfectant are common. Third, recovery is often brought about by flushing the contaminated water from the system rather than treating it, generally using hydrant flushing. Although flushing is mentioned sporadically here because it accompanies many of the other recovery techniques, it is treated more comprehensively in Chapters 5 and 6 where hydraulic and water quality integrity are the focus, respectively.
In those situations where the absence of a component was the cause for the lack of physical integrity, then simply installing the component is the recovery effort. For example, the installation of backflow prevention devices or changing covers on reservoirs (say from floating to hard covers) should restore integrity. Finally, where operational failure is the problem, devices may also need to be entirely replaced, along with instituting inspections to ensure that failure does not recur.
Repairing, Rehabilitating, and Replacing Pipe
Common types of repair activities include cutting and plugging the portion of pipe associated with a leak, installing a repair sleeve or clamp, eliminating dead end mains, replacing and repairing valves, adding ferrules, and repairing or replacing hydrants. These activities are discussed extensively in Grigg (2004) and not considered further here. Improvements are being made in locating buried failure sites, excavation, and repair. For example, trenchless methods are being developed and applied, although the technology development is slow.
Rehabilitation of pipe involves the recycling and reinforcing of the existing infrastructure in order to prolong its useful life. For example, structural lining can be used to improve the structural integrity of existing pipes and involves placing a watertight structure in immediate contact with the inner surface of a cleaned pipe (Selvakumar et al., 2002; Ellison et al., 2003). The most commonly used structural lining techniques include conventional slip lining (where new PE pipe is structurally able to replace the existing pipe), cured-in-place rehabilitation or inversion lining (which inserts a non-structural material) (Hughes and Conroy, 2002), fold-and-form pipe, and close-fit slip lining (which can use a structural or non-structural replacement material). Selvakumar et al. (2002) provide a detailed description of all these methods along with their costs, benefits, and limitations. Nonstructural rehabilitation of water mains, which does not focus on recovering the physical integrity of distribution systems, includes chemical dosing for corrosion control, cement mortar lining, epoxy resin lining, and thin-walled PE lining (Hughes and Conroy, 2002; Grigg, 2004; Damodaran et al., 2005). Such rehabilitation should be internally inspected to ensure that it is done to standards.
Pipes are candidates for replacement when the pipe is severely deteriorated (e.g., the pipe has suffered a series of breaks), or when additional hydraulic capacity is needed. Box 4-4 discusses the economic considerations that play into the decision to replace a pipe rather than rehabilitate or repair it. Historically, pipeline replacement involved the construction of a new pipeline normally parallel to the one being replaced. Once constructed, the new pipeline was connected to the pipe network and the old pipeline abandoned. This approach normally involved digging a trench, installing the new pipe, backfilling the trench, and final surface restoration. This construction can be very disruptive in built-up areas plus it may be very difficult to find a location to construct a new waterline. As a result, new trenchless technologies have developed which can result in cost savings over the conventional construction methods. Horizontal directional drilling has seen considerable growth as an alternative to open trench construction, especially at crossings of waterways, rail lines, and highways. A drilling bit bores a horizontal hole that is kept open using drilling fluid. Once a predetermined length of hole is completed, a new pipe is pulled back through the horizontal hole. This method is far less disruptive than open trench construction, and in most cases would not interfere with business or residential property access.
Another type of trenchless technology that is most useful in areas where it is difficult to install new pipe is pipe-bursting. This technology is similar to horizontal directional drilling, but with pipe-bursting a new pipe is pulled in the same location as the old pipe. A burster is pulled through the old pipe, breaking it apart and making room for the new pipe. The only openings required are at the two ends and at all active service locations. The equipment can install pipe of the same size that is being replaced or a size or two larger. Selvakumar et al. (2002) give a detailed description of pipe bursting, microtunneling, and horizontal directional drilling methods along with their costs, benefits, and limitations.
BOX 4-4 Decision-making regarding Replacement vs. Ongoing Repair There now exist fairly good models for making decisions about ongoing repair vs. replacement of infrastructure pipe components (Damodaran et al., 2005), although they do not incorporate public health risk and water quality deterioration. The traditional economic life of a component is the point at which the cost of keeping it in use equals the cost of replacing it. The “cost”, though, has been expanded beyond the utility’s internal costs to include external costs, like the public’s costs associated with the failure of a component (loss of water and business, traffic disruptions, etc.). Expectations for customer service are rising at the same time that repair and replacement costs are rising. Decisions based on internal costs alone often favor ongoing repair over replacement. When external costs (such as the number of households affected by a failure) are counted, replacement begins to be favored over repair. When the break rate for a 20-ft long pipe exceeds once per year then it can become more economical to replace the pipe than repair it (Damodaran et al., 2005). Utilities need guidance on including external costs along with internal costs, and the advantages and disadvantages of replacement methods, so that they can make up-to-date and sound decisions in a timely manner. |
Regardless of whether the situation requires repair, rehabilitation, or replacement, there are practices that can minimize the contamination potential, such as maintaining a positive pressure until the repair site is unearthed and cleared. Trench water should be removed before work is done, and street drainage should be provided to keep water and runoff out of the trench. New materials and repaired materials can be sprayed or swabbed with chlorine or appropriate sanitizing agents, as specified in ANSI/AWWA standards C600-99 for the installation of ductile iron mains and C651-99 for the disinfection of mains. During these activities, inspectors or engineers managing the site need to be aware of all issues related to water quality including the type of pipe that can be laid in soils suspected of contamination, the means by which to protect materials during storage, the methods for working in trenches to prevent contamination of materials, and what to do if materials do become contaminated.
Prior to the release for use of a new or replaced water main or facility, a water utility will typically conduct water quality testing. Total coliform bacteria have been the most common indicator that the new material is sanitary and did not become contaminated during storage or installation. In addition to total coliform testing, the water utility can also test for turbidity, HPC bacteria, total chlorine residual, pH, and odor, as unsanitary and improper installation practices can affect these parameters.
As documented in Table 2-3, 16 of 34 responding states address the storage and handling of pipes, while 29 of 34 address the need for disinfection and water quality testing following installation. Experience has shown, unfortunately, that sanitary practices vary widely. Even well-run utilities can experience a 30 percent failure rate in the approval of new mains based on water quality testing (Burlingame and Neukrug, 1993). Pipe design and construction is usually focused on existing codes (such as depth of installation to prevent freezing) and corrosion protection (such as using plastic pipe or metallic pipe with protective wrap in corrosive soils) but not on sanitary practices and rarely on permeation concerns. Pierson et al. (2001) found that although the ANSI/AWWA standards, particularly C600-99, attempt to address installation or construction practices, there is a general lack of training and the use of requirements for sanitary practices. It is possible for trenches where pipe is being laid or repaired to fill partially with water from broken lines or from precipitation or groundwater. This water can mobilize soil-related contaminants as well as carry contamination itself. Clearly, during emergency repairs or repairs made under less than favorable conditions, it becomes even more difficult to prevent the exposure of materials to environmental contamination. This could be addressed in part by requiring foremen or managers of construction sites to be certified on a regular basis, as it is for the certification of backflow installers and testers. Such training and certification can be provided through third-party organizations (non-water utility agencies) such as the New England Water Works Association and American Society of Sanitary Engineers. Not only would foremen or managers have to know the engineering requirements, but they would also have to record and un-
derstand the issues related to protecting the sanitary condition of the materials and the water supply.
Disinfection
Haas et al. (1998) reported that interior pipe surfaces are not free of microbial contaminants even under best case conditions. Furthermore, the lack of adequate distribution system maintenance (which includes flushing, disinfecting, and coliform testing of all pipe repairs and pipe replacement activities) has been found to contribute to higher coliform occurrence rates (Clement et al., 2003). Thus, when a new main is installed or a valve is repaired, it is advisable to act as if some level of contamination has occurred to both the water and the materials and to address potential contamination before the affected portion of the water system is returned to use. When the interior of pipe has become contaminated or needs cleaning due to unsanitary activities, disinfection becomes necessary.
Pipes can have a significant chlorine demand which reduces the effectiveness of disinfection (Haas et al., 1999). Fortunately, there is a current AWWA standard (C652) governing new pipe disinfection, which sets forth two options. The first is to flush followed by filling the facility/pipe with a strong (> 25 mg/L) chlorine solution and maintaining it for 24 hours providing that a residual of 10 mg/L remains. The second option is contacting the pipe or facility with a 100 mg/L free chlorine solution for at least three hours so that the residual remaining is at least 50 mg/L. The chlorine used for these disinfection operations may be supplied either as solid calcium hypochlorite powder dissolved in water, sodium hypochlorite (liquid bleach) dissolved in water, or gaseous chlorine dissolved in water.
These guidelines basically require that a “CT” (product of disinfectant and contact time) of 14,000 (first option) or 9,000 (second option) mg-min/L be achieved. Tests on actual mains indicate that these guidelines are sufficient to yield four logs (99.99 percent) inactivation of heterotrophic plate count (HPC) bacteria (Haas et al., 1998). Where unusually high levels of contamination are suspected, the design “CT” for facility disinfection should be increased.
After disinfection, the chlorinated water must be flushed from the system and the adequacy of disinfection checked by microbiological testing. In flushing the heavily chlorinated water, attention must be paid to (1) preventing leakage into the active distribution system if the newly disinfected pipe is connected to the system, (2) the potential impacts on the sewer system if the water is discharged to a sewer, or (3) dechlorinating the water (using sulfur dioxide, sulfite, or bisulfite) if the water is discharged to a surface waterbody so as to minimize adverse impacts to aquatic life.
CONCLUSIONS AND RECOMMENDATIONS
The loss of physical integrity of the distribution system—in which the system no longer acts as a physical barrier that prevents external contamination from deteriorating the internal, drinking water supply—is brought about by physical and chemical deterioration of materials, the absence or improper installation of critical components, and the installation of already contaminated components. When physical integrity is compromised, the drinking water supply becomes exposed to sources of contamination that increase the risk of negative public health outcomes. The following primary conclusions and recommendations for maintaining and restoring physical integrity to a distribution system are made.
Storage facilities should be inspected on a regular basis. A disciplined storage facility management program is needed that includes developing an inventory and background profile on all facilities, developing an evaluation and rehabilitation schedule, developing a detailed facility inspection process, performing facility inspections, and rehabilitating and replacing storage facilities when needed. Depending on the nature of the water supply chemistry, every three to five years storage facilities need to be drained, sediments need to be removed, appropriate rust-proofing needs to be done to the metal surfaces, and repairs need to be made to structures. These inspections are in addition to daily or weekly inspections for vandalism, security, and water quality purposes (such as identifying missing vents, open hatches, and leaks).
Better sanitary practices are needed during installation, repair, replacement, and rehabilitation of distribution system infrastructure. All trades people who work with materials that are being installed or repaired and that come in contact with potable water should be trained and certified for the level of sanitary and materials quality that their work demands. Quality workmanship for infrastructure materials protection as well as sanitary protection of water and materials should go hand-in-hand considering the increasing costs of infrastructure failure and repair and the increasingly stringent water quality standards. Training and certification can be provided through third-party organizations (non-water utility agencies) such as the New England Water Works Association and American Society of Sanitary Engineers.
Although it is difficult and costly to perform, condition assessment of buried infrastructure should be a top priority for utilities. Every water utility should maintain a complete, up-to-date inventory of all infrastructure components from storage facilities to pipes to valves to hydrants, including their current condition. Because failure analysis has not generally been embraced by the water community, there is limited information on many of the materials in common use today. Most useful would be a user-friendly guidance manual for utilities regarding the failure mechanisms of different types of infrastructure
materials and how to use the various types of information on the current condition of the pipe to determine its expected lifetime. Finally, as an essential part of condition assessment, every water utility should have in place a leak detection program that includes checking service lines as well as transmission mains.
External and internal corrosion should be better researched and controlled in standardized ways. There is a need for new materials and corrosion science to better understand how to more effectively control both external and internal corrosion, and to match distribution system materials with the soil environment and the quality of water with which they are in contact. At present the best defense against corrosion relies on site-specific testing of materials, soils, and water quality followed by the application of best practices, such as cathodic protection. Indeed, a manual of practice for external and internal corrosion control should be developed to aid the water industry in applying what is known. Corrosion is poorly understood and thus unpredictable in occurrence. Insufficient attention has been given to its control, considering its estimated annual direct cost of $5 billion for the main distribution system (not counting premise plumbing).
Cross-connection control should be in place for all water utilities. Every utility should have a uniform and consistent cross-connection control program along with adequate support such as regulations or codes, and staffing. The program should at the least provide for service-protection or containment (i.e., making sure that customers cannot backflow contaminants into the public distribution system), and when possible should attempt to eliminate cross connections on customer’s premises. Most if not all technical and administrative information already exists upon which to institute a cross-connection control program.
REFERENCES
Allbee, S. 2004. A center of excellence—a sensible step on the pathway to excellence in water utility infrastructure management. Underground Infrastructure Management (Nov/Dec.):27–29.
American Water Works Association (AWWA). 1986. Introduction to Water Distribution Principles and Practices of Water Supply Operations. Denver, CO: AWWA.
AWWA. 1999. Water Audits and Leak Detection, Manual M36, 2nd edition. Denver, CO: AWWA.
AWWA. 2003. Water Stats 2002 Distribution Survey CD-ROM. Denver, CO: AWWA.
AWWA. 2004. Recommended Practice for Backflow Prevention and Cross-Connection Control, Manual M14, 3rd edition. Denver, CO: AWWA.
AWWA. 2005a. Flexible, lightweight PE gaining ground. Opflow (July):24–25.
AWWA. 2005b. Ductile-Iron Pipe—Iron and Icon for Durability, Reliability. Opflow (February):14–15.
AWWA and EES, Inc. 2002. Permeation and leaching. Available on-line at http://www.epa.gov/safewater/tcr/pdf/permleach.pdf. Accessed May 5, 2006.
American Water Works Association Research Foundation (AwwaRF). 1985. Internal Corrosion of Water Distribution Systems. Cooperative report with DVGW Forschungsstelle. Denver, CO: AWWA Research Foundation.
AWWA Water Loss Control Committee. 2003. Committee report: applying worldwide BMPs in water loss control. J. Amer. Water Works Assoc. 95(8):65–80.
Angulo F. J., S. Tippen, D. J. Sharp, B. J. Payne, C. Collier, J. E. Hill, T. J. Barrett, R. M. Clark, E. E. Geldreich, H. D. Donnell, Jr., and D. L. Swerdlow. 1997. A community waterborne outbreak of salmonellosis and the effectiveness of a boil water order. American Journal of Public Health 87(4):580–584.
Bonds, R. W., L. M. Barnard, A. M. Horton, and G. L. Oliver. 2005. Corrosion and corrosion control of iron pipe: 75 years of research. J. Amer. Water Works Assoc. 97(6):88–98.
Booth, S., and B. Brazos. 2005. Qualitative Procedures for Identifying Particles in Drinking Water. Denver, CO: AwwaRF.
Burlingame, G. A. 1999a. Solving customers’ taste and odor complaints—part 1: the importance of the first response. Opflow 25(10):10–11.
Burlingame, G. A. 1999b. Solving customers’ taste and odor complaints—part 2: tracking odors to their source. Opflow 25(11):6–7.
Burlingame, G. A., and C. Anselme. 1995. Distribution system tastes and odor. Pp. 281–319 In: Advances in Taste-and-Odor Treatment and Control. Denver, CO: AwwaRF.
Burlingame, G. A., and H. M. Neukrug. 1993. Developing proper sanitation requirements and procedures for water main disinfection. Pp. 137–146 In: Proceedings of AWWA Annual Conference. Denver, CO: AWWA.
Burlingame, G. A. 2001. A balancing act: distribution water quality and operations. Opflow 27(7):14–15.
Burlingame, G. A., J. Rahman, E. Navera, and J. E. Durrant. 2002. Pp. 83–101 In: Assessing the Future: Water Utility Infrastructure Management. D. M. Hughes (ed.). Denver, CO: AWWA.
Cagle, R. F. 2005. Daddy, are we there yet? Underground infrastructure management. Jan/Feb:43–46.
Clark, R. M., and J. A. Goodrich. 1989. Developing a database on infrastructure needs. J. Amer. Water Works Assoc. 81(7):81–87.
Clark, R. M., Geldreich, E. E., Fox, K. R., Rice, E. W., Johnson, C. H., Goodrich, J. A., Barnick, J. A., and Abdesaken, F. 1996. Tracking a Salmonella serovar typhimurium outbreak in Gideon, Missouri: Role of contamination propagation modeling. Journal of Water Supply Research and Technology—Aqua 45(4):171–183.
Clement, J., C. Spencer, A. J. Capuzzi, A. Camper, K. V. Andel and A. Sandvig. 2003. Influence of Distribution System Infrastructure on Bacterial Regrowth. Denver, CO: AwwaRF.
Cooperative Research Centre for Water Quality and Treatment. 2003. Setback for Netherlands Dual Supplies. Health Stream 30:5.
Craun, G. F., and R. L. Calderon. 2001. Waterborne disease outbreaks caused by distribution system deficiencies. J. Amer. Water Works Assoc. 93:9:64–75.
Damodaran, N., J. Pratt, J. Cromwell, J. Lazo, E. David, R. Raucher, C. Herrick, E. Rambo, A. Deb, and J. Snyder. 2005. Customer acceptance of water main structural reliability. Denver, CO: AwwaRF.
Donahue, E. J., III. 2002. GASB 34 and water utilities: deferred maintenance and contributed capital. In: Assessing the Future: Water Utility Infrastructure Management. D. M. Hughes (ed.). Denver, CO: AWWA.
Ellison, D., S. J. Duranceau, S. Ancel, G. Deagle, and R. McCoy. 2003. Investigation of pipe cleaning methods. Denver, CO: AwwaRF.
Environmental Protection Agency (EPA). 1999. Uncovered Finished Water Reservoirs Guidance Manual. EPA 815-R-99-011. Washington, DC: EPA Office of Water. Available on-line at http://www.epa.gov/safewater/mdbp/pdf/uncover/ufw8p.pdf.
EPA. 2002a. Technical fact sheet on: Benzene. Available on-line at http://www.epa.gov/OGWDW/dwh/t-voc/benzene.html. Accessed on May 8, 2006.
EPA. 2002a. Technical fact sheet on: Xylenes. Available on-line at http://www.epa.gov/OGWDW/dwh/t-voc/xylenes.html. Accessed on May 8, 2006.
EPA. 2002c. Technical fact sheet on: Toluene. Available on-line at http://www.epa.gov/OGWDW/dwh/t-voc/toluene.html. Accessed on May 8, 2006.
EPA. 2002d. Technical fact sheet on: Ethylbenzene. Available on-line at http://www.epa.gov/ OGWDW/dwh/t-voc/ethylben.html. Accessed on May 8, 2006.
EPA. 2003. Cross-Connection Control Manual. Washington, DC: EPA. Available online at http://www.epa.gov/safewater/crossconnection.html. Accessed on May 8, 2006.
EPA. 2004. Taking stock of your water system—a simple asset inventory for very small drinking water systems. EPA 816-K-03-002. Washington, D.C.: EPA.
Falarski, M. R. 2002. East Bay Municipal Utility District’s Pipeline Replacement Program. In: Assessing the Future: Water Utility Infrastructure Management. D. M. Hughes (ed). Denver, CO: AWWA.
Geldreich, E. E. 1996. Microbial Quality of Water Supply in Distribution Systems. Boca Raton, FL: CRC Press, Inc.
Glaza, E. C., and J. K. Park. 1992. Permeation of organic contaminants through gasketed pipe joints. J. Amer. Water Works Assoc. 84(7):92–100.
Government Accounting Standards Board. 1991. GASB Statement 34: basic financial statements and management’s discussion and analysis for state and local governments issued in 1991.
Grigg, N. S. 2004. Assessment and Renewal of Water Distribution Systems. Denver, CO: AwwaRF.
Grigg, N. S. 2005. Assessment and Renewal of Water Distribution Systems. J. Amer. Water Works Assoc. 97:2:58–68.
Haas, C. N., M. Gupta, G. A. Burlingame, R. B. Chitluru, and W. O.Pipes. 1999. Bacterial levels of new mains. J. Amer. Water Works Assoc. 91(5):78–84.
Haas, C. N., R. B. Chitluru, M. Gupta, W. O. Pipes, and G. A. Burlingame. 1998. Development of disinfection guidelines for the installation and replacement of water mains. Denver, CO: AwwaRF.
Holsen, T. M., Park, J. K., Bontoux, L., Jenkins, D. and Selleck, R. E. 1991. The effect of soils on the permeation of plastic pipes by organic chemicals. J. Amer. Water Works Assoc. 83(11):85–91.
Hrudey, S. E., and E. J. Hrudey. 2004. Safe Drinking Water: Lessons from Recent Outbreaks in Affluent Nations. London: IWA Publishing.
Hughes, D. M., and P. J. Conroy. 2002. Matching deteriorating main conditions to replacement/rehabilitation options. In: Assessing the Future: Water Utility Infrastructure Management. D. M. Hughes (ed.). Denver, CO: AWWA.
Kirmeyer, G. J., L. Kirby, B. M. Murphy, P. F. Noran, K. D. Martel, T. W. Lund, J. L. Anderson, and R. Medhurst. 1999. Maintaining and operating finished water storage facilities. Denver, CO: AwwaRF.
Kirmeyer, G. K., M. Freidman, K. Martel, D. Howie, M. LeChevallier, M. Abbaszadegan, M. Karim, J. Funk, and J. Harbour. 2001. Pathogen Intrusion into the Distribution System. Denver, CO: AwwaRF.
Krasner, S. W., and E. G. Means, III. 1986. Returning newly covered reservoirs to service: health and aesthetic considerations. J. Amer. Water Works Assoc. 78(3):94– 100.
Lange, G. 2002. Locating leaks in plastic water pipes. Opflow 28(7):1,4,5,10.
Lee, J. J., P. Schwartz, P. Sylvester, L. Crane, J. Haw, H. Chang, and H. J. Kwon. 2003. Impacts of Cross-Connections in North American Water Supplies. Denver, CO: AwwaRF.
Lockridge, R. 2004. The four C’s of asset management. Underground Infrastructure Management Nov/Dec.:39–41.
Makar, J. 2002. Investigating large gray cast-iron pipe failures: a step-by-step approach. In: Assessing the Future: Water Utility Infrastructure Management. D. M. Hughes (ed.). Denver, CO: AWWA.
Makar, J., and Y. Kleiner. 2002. Maintaining water pipeline integrity. In: Assessing the Future: Water Utility Infrastructure Management. D. M. Hughes (ed.). Denver, CO: AWWA.
Makar, J., R. Rogge, S. McDonald, and S. Tesfamariam. 2005. The effect of corrosion pitting on circumferential failures in grey cast iron pipes. Denver, CO: AwwaRF.
Makepeace, D. K., D. W. Smith, and S. J. Stanley. 1995. Urban stormwater quality: summary of contaminant data. Critical Reviews in Environmental Science and Technology 25(2):93–127.
Male, J. W., and T. M. Walski. 1991. Water Distribution Systems: A Troubleshooting Manual. Chelsea, MI: Lewis Publishers, Inc.
Martel, K., A. Hanson, G. J. Kirmeyer, M. Besner, A. Carrier, M. Prevost, A. Lynggaard-Jensen and N. Bazzurro. 2005. Data Integration for Water Quality Management. Denver, CO: AwwaRF.
McGuire, M., N. Graziano, L. Sullivan, R. Hund, and G. Burlingame. 2004. Water Utility Self-Assessment for the Management of Aesthetic Issues. Denver, CO: AwwaRF.
Morgan, W., R. Titus, and D. M. Hughes. 2005. Simultaneous Communication of Acoustic Data and Meter Readings Automatically. In: Proceedings from the International Water Association Water Loss Task Force Conference, Halifax, Nova Scotia.
Morrison, R. 2004. Condition assessment—back to the basics. Underground Infrastructure Management Nov/Dec.:51–55.
Nayyar, M. L. 1992. Piping Handbook, Sixth Edition. New York: McGraw-Hill, Inc.
Neptune Technology Group. 2005. E-Coder. Available on-line at http://www.neptunetg. com/uploadedFiles/E-Coder%20Press%20Release.pdf. Accessed May 8, 2006.
Paralez, L. L., and D. Muto. 2002. Creating an asset management strategy: an asset management template. In: Assessing the Future: Water Utility Infrastructure Management. D. M. Hughes (ed.). Denver, CO: AWWA.
Pierson, G. L., G. Burlingame, and K. Martin. 2002. Establishing a tradition of contamination prevention. Opflow 28(7):6,7,11.
Pierson, G., K. Martel, A. Hill, G. Burlingame, and A. Godfree. 2001. Methods to prevent microbiological contamination associated with main rehabilitation and replacement. Denver, CO: AwwaRF.
Propato, M., and J. G. Uber. 2004. Vulnerability of water distribution systems to pathogen intrusion: how effective is a disinfectant residual? Environ. Sci. Technol. 38(13):3713–3722.
Romer, A. E., G. E. C. Bell, S. J. Duranceau, and S. Foreman. 2004. External Corrosion and Corrosion Control of Buried Water Mains. Denver, CO: AwwaRF.
Schwarzwalder, R. 2002. Asset management for the new millennium: strategic approaches for water utilities. In: Assessing the Future: Water Utility Infrastructure Management. D. M. Hughes (ed.). Denver, CO: AWWA.
Seargeant, D. 2002. Using new technology to optimize management of cast iron pipe assets. In: Assessing the Future: Water Utility Infrastructure Management. D. M. Hughes (ed.). Denver, CO: AWWA.
Selvakumar, A., R. M. Clark, and M. Sivaganesan. 2002. Costs for water supply distribution system rehabilitation. Jour. Water Resources Planning and Management ASCE 128(4):303–306.
Shamsi, U. M. 2005. GIS Applications for Water, Wastewater and Stormwater Systems. Boca Raton, FL: CRC Press.
Skala, M. F. 1994. Waterborne salmonella outbreak in southeastern Missouri. Missouri Epidemiologist 17(2):1–2.
Swerdlow, D. L., B. L. Woodruff, R. C. Brady, P. M. Griffin, S. Tippen, H. D. Donnell, Jr., E. Geldreich, B. J. Payne, A. Meyer Jr., J. G. Wells, K. D. Greene, M. Bright, N. H. Bean, and P. A. Blake. 1992. Waterborne outbreak in Missouri of Escherichia coli O157:H7 associated with bloody diarrhea and death. Annals of Internal Medicine 117(10):812–819.
Szeliga, M. J., and D. M. Simpson. 2002. Evaluating the conditions of existing water mains. In: Assessing the Future: Water Utility Infrastructure Management. D. M. Hughes (ed.). Denver, CO: AWWA.
University of Southern California (USC). 2002. Prevalence of cross connections in household plumbing systems. Available on-line at http://www.usc.edu/dept/fcchr/epa/hhcc.report.pdf. Los Angeles, CA: USC Foundation for Cross-Connection Control and Hydraulic Research.
USC. 1993. Manual of Cross-Connection Control, 9th Edition. Los Angeles, CA: USC Foundation for Cross-Connection Control and Hydraulic Research.
Von Huben, H. (Tech. Ed). 1999. Water Distribution Operator Training Handbook, 2nd edition. Denver, CO: AWWA.
Wallick, P. C., and M. Zubair. 2002. Tank evaluation, rehabilitation, and replacement decisions for water storage tanks. In: Assessing the Future: Water Utility Infrastructure Management. D. M. Hughes (ed.). Denver, CO: AWWA.
Westerhoff, G., P. Fahy, and S. Robinson. 2004. On the pathway to improved asset management. Underground Infrastructure Management Nov/Dec:35–37.