From Factory to Foxhole: Improving the Army’s Supply Chain
MARK Y.D. WANG
RAND Corporation
Santa Monica, California
At first glance, the end-to-end supply chain by which repair parts are procured and moved to support U.S. Army troops worldwide looks similar to commercial supply chains. Both have suppliers, wholesale distribution centers, retail suppliers, customers, and transportation carriers that move parts from point to point. The main differences between military and commercial supply chains relate, not surprisingly, to the challenges the military faces and the way those challenges must be met.
In 1999, a team of RAND analysts was awarded Al Gore’s Hammer Award for support of the Army’s Velocity Management Initiative, which dramatically improved ordering and shipping times (OST) for repair parts. Current efforts are now focused further upstream in the supply chain to improve the Army’s purchasing and supply management (PSM), integrate supplier management to increase stock availability, and lower total cost. As shown in Figure 1, these initiatives span the entire Army supply chain from factory to foxhole.
MILITARY VERSUS TRADITIONAL SUPPLY CHAINS
Traditional commercial supply chains focus on physical efficiency, with the emphasis on operating at the lowest possible cost, minimizing investment in inventory, and maximizing capacity utilization. Supply chains that support just-in-time manufacturing (e.g., the Toyota production system) smooth the flow of material from supplier to manufacturing line (Liker, 2003). Management of
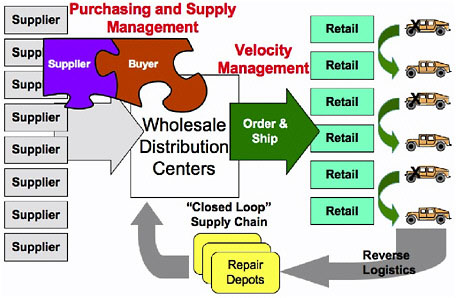
FIGURE 1 The Army’s factory-to-foxhole supply chain and how velocity management and purchasing and supply management can improve support for warfighters. Source: Wang, 2000.
physically efficient supply chains may include active management of demand, (e.g., “everyday low prices”) to minimize surges and spikes and address inaccuracies in forecasting.
In contrast, military supply chains focus on responsiveness and surge capabilities. The Army must be able to deploy quickly anywhere in the world, and its supply chain must be able to adapt and respond to unpredictable demands and rapidly changing environments. In preparation for Operation Iraqi Freedom, the equivalent of more than “150 Wal-Mart superstores” was moved to Kuwait to support 250,000 soldiers, sailors, airmen, and marines (Walden, 2003).
The nature of commodities, functional or innovative, dictates whether supply chains must be physically efficient or demand responsive (Fischer, 1997). Thus, industries that produce innovative products with very uncertain forecasts (e.g., high-tech, high-fashion, or even toy/entertainment industries) rely on demand-responsive supply chains (Sheffi, 2005). The nature of the military mission requires a demand-responsive supply chain. In addition, the characteristics of Army repair parts add to the challenge.
Repair parts are not only highly specialized and weapon-system-specific, but are also often produced by sole-source suppliers who have no commercial market to fall back on. Many parts, such as engines and transmissions, are “repa-
rable” and must be overhauled as a source of future supply (Diener, 2004). Thus, the military not only has to manage a forward logistics pipeline, but must also manage an equally big reverse logistics, or “retrograde,” pipeline in a “closed-loop” supply chain (Blumberg, 2004). For every engine, transmission, or rotor blade replaced in the field, a carcass must be moved back to an Army repair depot or national maintenance program location. When you take into account the commodity characteristics and a mission that must respond to unpredictable surges and spikes in demand, the differences between the Army’s supply chain and the supply chains of commercial companies become readily apparent.
VELOCITY MANAGEMENT TO SPEED UP FLOW
The purpose of the Army’s Velocity Management Initiative, begun in 1995, was to improve the responsiveness, reliability, and efficiency of a logistics system based on massive stockpiles of supplies and weapon systems, many of them prepositioned “just in case” (Dumond et al., 2001). Although this was a world-class system for supporting a Cold War army, it has become increasingly less effective and unaffordable for the current force-projection army.
To measure the Army’s logistics performance, the velocity-management team developed a percentile bar-chart presentation of OST that takes into account not only times for peak distribution, but also times for the tail end of the distribution. Figure 2 shows the time distribution of OST for moving in-stock
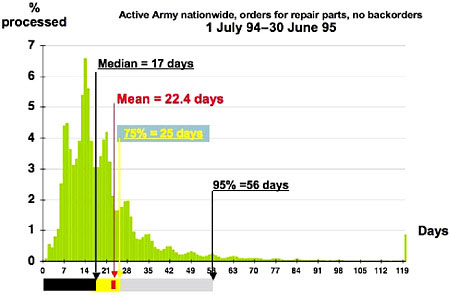
FIGURE 2 In 1994–1995, lengthy OST times were combined with long, variable distribution times. Source: Wang, 2000.
materiel from wholesale defense distribution centers to the Army’s retail supply locations. The horizontal axis shows OST measured in days, and the vertical axis shows the percentage of total requisitions. On the lower horizontal bar, the black region represents the time it took to receive half the requisitions for repair parts (17 days during the baseline period). The light (intermediate) and gray (final) regions show the time it took to receive 75 percent and 95 percent of the requisitions, respectively. The square marker shows the mean time (22.4 days during the baseline period). As this figure shows, the difference between the average time and the 95th percentile varied by a factor of two or three. Thus, soldiers waiting for repair parts could not plan repair schedules or maintain the combat readiness of their weapons systems. They simply had to wait, frustrated customers of an unreliable and unresponsive distribution system.
The velocity-management team used a define-measure-improve methodology to “walk the process,” following the flow of requisitions and materiel. An excellent example of a win-win solution was the optimization of truck deliveries, which was accomplished by replacing a mix of delivery modes with a reliable, high-volume, high-performing distribution system based on scheduled deliveries. The Army now has premium-level service that is faster, better, and cheaper. Other improvements include better coordinated requisition processing and financial reviews, the adoption of simple rules to “clear the floor” daily, and the establishment of a high-level governance structure to measure performance and ensure continuous improvement.
As Figure 3 shows, through velocity management, the Army dramatically
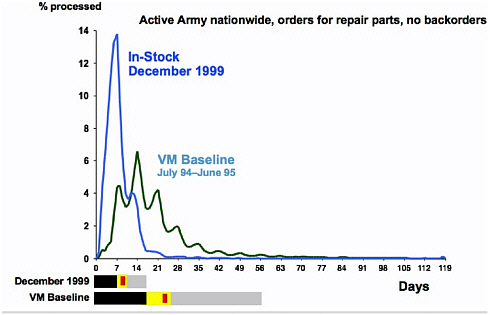
FIGURE 3 Army OST dropped dramatically during the implementation of velocity management. Source: Wang, 2000.
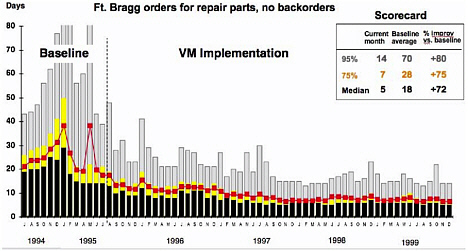
FIGURE 4 Improvements in OST have been most dramatic at major FORSCOM installations, such as Fort Bragg. Source: Wang, 2000.
streamlined its supply process, cutting OST for repair parts by nearly two-thirds nationwide (Wang, 2000). The greatest improvements, which cut OST by more than 75 percent, were achieved at the major forces command (FORSCOM) installations and other installations in the active Army (Figure 4). Today, Army customers nationwide and worldwide routinely receive the same quick, dependable service expected from a high-performing commercial supply chain.
IMPROVING PURCHASING AND SUPPLY MANAGEMENT
Distribution improvements achieved through velocity management were focused on moving in-stock parts. More recent efforts have been focused on improving the Army’s PSM processes to ensure that parts are kept in stock. During Operation Iraqi Freedom, when both the operating tempo and demand for repair parts were consistently high, requisition backorders of Army-managed items at the national wholesale level skyrocketed, reaching 35 percent for the active Army (Peltz et al., 2005). Backorder rates are a key performance metric because they indicate longer customer waiting times for parts, longer repair-cycle times, and, ultimately, adverse impacts on the availability of weapons systems and unit readiness (Folkeson and Brauner, 2005).
Many factors were contributors to the Army’s stock-availability challenges. Besides the contingency surge, they included financial delays and the under-funding of war-reserve inventory prior to the war. The implementation of best PSM practices, such as reducing lead times and total costs, could greatly improve future supply performance. In the commercial world, there has been a
paradigm shift from managing items and contracts to managing suppliers and supplier capacity. This has greatly reduced the “bullwhip effect”—wide variations in demand caused by a lack of coordination and information that cascade back through a supply chain (Lee et al., 1997). Best PSM practices call for collaborative planning, forecasting, and replenishment by buyers and suppliers, which leads to better supplier management and more integrated supplier relationships. As the Army’s supply chain becomes more responsive to demand, it continues to move toward these PSM goals.
RAND is currently performing high-level analyses of the Army’s spending for goods and services, more than $300 billion in FY05, to identify opportunities for improving purchasing (e.g., aggregating requirements when there are many contracts or many suppliers for the same commodity). Another important step toward rationalizing the Army’s supply base will be the development of improved supply strategies. As long-term agreements are made with the best suppliers, overall supplier performance will improve, and the Army and suppliers can work together to integrate business processes. Army Materiel Command, the headquarters organization responsible for PSM, is planning to conduct several pilot tests of PSM principles in the coming year.
SUMMARY
The Army’s supply chain faces unique challenges because it must operate in and provide support for highly unpredictable contingencies. As a result, it must be demand-responsive, that is, able to surge and adapt as conditions and demand change. Dramatic reductions in the Army’s OST have accelerated flow and streamlined the Army’s supply chain. The current challenge is to leverage the distribution improvements achieved by velocity management with higher and more robust wholesale stock availability. Efforts are under way to improve the Army’s PSM by adopting best practices in commercial PSM to improve the management of suppliers and supplier capacity.
REFERENCES
Blumberg, D. 2004. Introduction to Reverse Logistics and Closed-Loop Supply Chain Processes. Boca Raton, Fla.: CRC.
Diener, D. 2004. Value Recovery from the Reverse Logistics Pipeline. RAND MG-238-A. Santa Monica, Calif.: RAND Corporation.
Dumond, J., M.K. Brauner, R. Eden, J. Folkeson, and K. Girardini. 2001. Velocity Management: The Business Paradigm That Has Transformed U.S. Army Logistics. RAND MR-1108-A. Santa Monica, Calif.: RAND Corporation.
Fischer, M. 1997. What is the right supply chain for your product? Harvard Business Review 75(2): 105–116.
Folkeson, J., and M.K. Brauner. 2005. Improving the Army’s Management of Reparable Spare Parts. RAND MG-205-A. Santa Monica, Calif.: RAND Corporation.
Lee, H., V. Padmanabhan, and S. Whang. 1997. The bullwhip effect in supply chains. Sloan Management Review 38: 93–102.
Liker, J. 2003. The Toyota Way: Fourteen Management Principles from the World’s Greatest Manufacturer. New York: McGraw-Hill.
Peltz, E., H.J. Halliday, M.L. Robins, and K.J. Girardini. 2005. Sustainment of Army Forces in Operation Iraqi Freedom: Major Findings and Recommendations. MG-342-A. Santa Monica, Calif.: RAND Corporation.
Sheffi, Y. 2005. The Resilient Enterprise: Overcoming Vulnerability for Competitive Advantage. Cambridge, Mass.: MIT Press.
Walden, J. 2003. The Forklifts Have Nothing to Do: Lessons in Supply Chain Leadership. Lincoln, Nebr.: iUniverse.
Wang, M. 2000. Accelerated Logistics: Streamlining the Army’s Supply Chain. RAND MR-1140-A. Santa Monica, Calif.: RAND Corporation.