3
MATERIALS PROPERTIES AND LIFE PREDICTION
The characteristics that make composites, especially glass fiber-reinforced and wood/epoxy composites, suitable for wind turbine blades are low density, good mechanical properties, excellent corrosion resistance, tailorability of material properties, and versatility of fabrication methods. Although glass/vinylester and glass/polyvinyl composites based on hand lay-up have been the most widely used materials so far, many more types of fibers and resins have become available recently. The new carbon fibers are stronger and stiffer, while the new resins provide higher toughness and shorter process cycle time. A number of handbooks are now available to the designers of composites (Lubin, 1982; Engineered Materials Handbook, 1987; Composites & Laminates, 1987).
FIBERS
The most commonly used and lowest-priced fiber is E-glass fiber. Over the past several years, however, many new fibers have become available. The commercially available fibers and their typical properties are listed in Table 3-1.
While E-glass fiber is most widely used in wind turbine rotor blades mainly because of its low cost, carbon fibers are the fibers of choice in many aerospace applications. Although more expensive, they provide higher specific modulus and specific strength than glass fibers. The advantage of carbon fibers is further enhanced in fatigue. However, carbon fibers are electrical conductors, and their contact with metals may lead to corrosion of the latter. Polymeric fibers such as aramid and high-density polyethylene are the toughest of all the available fibers and hence can be used where high-impact resistance and toughness are required. These polymeric fibers, however, are weak in compression because of the fibrillar nature of their microstructure. Recently, a variety of ceramic fibers such as alumina and silicon carbide have emerged mainly as reinforcements for metal and ceramic matrices. These ceramic fibers have better oxidation resistance in high-temperature applications than carbon fibers. However, they are still more expensive than most carbon fibers. Mechanical properties of epoxy matrix composites made with the four most widely used fibers--aramid, carbon, E-glass and S-glass--are shown in Table 3-2. Tensile fatigue behaviors of the first three composites are compared in Figure 3-1.
Since one type of fiber does not have all the desired properties, different fibers can be mixed to make a hybrid composite. For example, in a glass/carbon hybrid composite the glass fiber can improve the impact resistance while keeping the cost down, and the carbon fiber can provide the required strength and stiffness with less weight. The weight savings resulting from the use of a hybrid composite reduces the load on the blade and hence will lead to a longer lifetime. Furthermore, the material savings realized can also compensate partially for the higher cost of the carbon fiber.
TABLE 3-1 Typical Properties of Fibers
Fiber |
Diameter, µm |
Specific Gravity |
Modulus, GPa* |
Tensile Strength, GPa |
Failure Strain, % |
CTE, 10-6/°C |
|||||
E-glass |
3-20 |
2.4 |
72.4 |
3.45 |
|||||||
S2-glass |
10-20 |
2.4 |
86.9 |
4.59 |
|||||||
Boron |
142 |
2.5 |
400 |
2.80 |
0.7 |
||||||
Carbon, PAN based |
|||||||||||
High strength |
1.8 |
230 |
2.5 |
1.1 |
-0.4 |
||||||
High modulus |
1.9 |
370 |
1.0 |
0.5 |
-0.5 |
||||||
Ultra-high modulus |
2.0 |
520 |
1.0 |
0.2 |
-1.1 |
||||||
High strain |
1.8 |
230-260 |
3.0-4.8 |
1.6-2.0 |
|||||||
Intermediate modulus |
1.8 |
290 |
5.2 |
1.8 |
|||||||
Carbon, pitch based |
|||||||||||
P25 |
10 |
1.8 |
140 |
1.4 |
1.0 |
-0.9 |
|||||
P55 |
10 |
2.02 |
380 |
1.4 |
0.4 |
-1.3 |
|||||
P75 |
10 |
2.00 |
520 |
1.4 |
0.3 |
-1.6 |
|||||
P100 |
10 |
2.15 |
700 |
1.4 |
0.2 |
-1.6 |
|||||
P120 |
|
|
820 |
1.4 |
0.2 |
-1.6 |
|||||
P140 |
|
|
960 |
1.4 |
0.2 |
-1.8 |
|||||
Silicon carbide |
|||||||||||
SCS |
140 |
3.0 |
430 |
3.4 |
0.8 |
||||||
Nicalon |
15 |
2.6 |
180-210 |
2.5-3.3 |
1.5 |
3.1 |
|||||
AVCO |
6-10 |
|
300 |
2.8 |
|||||||
MPDZ |
10-15 |
2.3 |
180-210 |
1.8-2.1 |
|||||||
HPZ |
10 |
2.35 |
140-175 |
2.1-2.5 |
|||||||
MPS |
10-15 |
2.6-2.7 |
175-210 |
1.1-1.4 |
|||||||
Alumina |
|||||||||||
FP |
20 |
3.9 |
345-380 |
1.4 |
0.36-0.4 |
||||||
Sumitomo |
9-17 |
3.2 |
210-260 |
1.8-2.6 |
0.86 |
||||||
Saffil |
3 |
3.3 |
300 |
2.0 |
0.67 |
||||||
PRD-166 |
|
4.2 |
385 |
2.1-2.5 |
|||||||
Alumina-silica |
|||||||||||
Fiberfrax |
|
2.7 |
100 |
1.0 |
|||||||
Fibermax |
|
3.0 |
150 |
0.8 |
0.5 |
||||||
Alumina-boria-silica |
|||||||||||
Nextel 312 |
11 |
2.7 |
150 |
1.4-1.7 |
|||||||
Mextel 440 |
10-12 |
3.1 |
200-240 |
1.4-2.0 |
0.9 |
||||||
Nextel 480 |
10-12 |
3.1 |
224 |
2.3 |
0.9 |
||||||
Si, Ti, C, O |
|||||||||||
Tyranno |
8-10 |
2.3-2.5 |
200 |
3.0 |
1.5 |
||||||
Aramid |
|||||||||||
Kevlar 49 |
12 |
1.44 |
124-131 |
3.6 |
2.8 |
-2.0 |
|||||
Kevlar 29 |
12 |
1.44 |
83 |
3.6 |
4.0 |
||||||
Kevlar 149 |
12 |
1.47 |
186 |
3.4 |
2.0 |
||||||
HM-50 |
12 |
1.3 |
81 |
3.1 |
4.4 |
||||||
Polyethylene |
|||||||||||
Spectra 900 |
38 |
0.97 |
117 |
2.6 |
3.5 |
||||||
Spectra 1000 |
27 |
0.97 |
172 |
3.1 |
0.7 |
||||||
Tungsten |
13 |
19.4 |
410 |
4.0 |
|||||||
* 1 GPa = 1.45 × 105 psi. |
TABLE 3-2 Typical Properties of Unidirectional Composites
|
E-Glass/Resin |
KEVLAR Resin |
Graphite/Resin |
S-Glass/Resin |
||
Fiber Direction |
||||||
Modulus, GPa |
44.8 |
75.8 |
145 |
56 |
||
Strength tension, MPa |
1124 |
1241 |
1517 |
1980 |
||
Strength compression, MPa |
896 |
276 |
2068 |
626 |
||
Coefficient of thermal expansion, microstrain/K |
8.8 |
-4.0 |
-0.45 |
5.5 |
||
Transverse Direction |
||||||
Modulus, GPa |
11.0 |
5.52 |
10.3 |
11.4 |
||
Strength tension, MPa |
31 |
14 |
48 |
31 |
||
Strength compression, MPa |
138 |
55 |
138 |
138 |
||
Coefficient of thermal expansion, microstrain/K |
22.1 |
57.6 |
25.2 |
23.3 |
||
Shear (Inplane) |
||||||
Modulus, GPa |
4.14 |
2.41 |
5.52 |
4.48 |
||
Strength, MPa |
71.7 |
34.5 |
82.7 |
71.7 |
||
Poisson Ratio |
||||||
Axial-Transverse |
0.27 |
0.34 |
0.30 |
0.27 |
||
Thickness Direction |
||||||
Modulus, GPa |
11.0 |
5.5 |
10.3 |
11.4 |
||
Poisson ratio |
0.44 |
0.38 |
0.55 |
0.44 |
To further illustrate the cost differences based on fibers, consider a hybrid composite with a carbon/glass volume ratio vc/g. The ratio of the cost of the hybrid composite to an all-glass composite to provide the same structural stiffness is given by

The parameters in Equation (1) are defined as follows: $, price per unit mass; s, specific gravity; E, Young's modulus; g, glass; and c, carbon. On the other hand, the weight ratio, defined as the weight of the hybrid composite divided by that of the all-glass composite, is given by

E-glass fiber costs around $2/lb; a high-strength carbon fiber costs about $30/lb. Thus, an all-carbon fiber composite costs 3.5 times more than an all-glass fiber composite to provide the same structural stiffness at a weight savings of 76 percent. When a 50/50 glass/carbon hybrid composite is used, however, the calculated cost ratio is reduced to 2.9 with a weight savings of 58 percent.
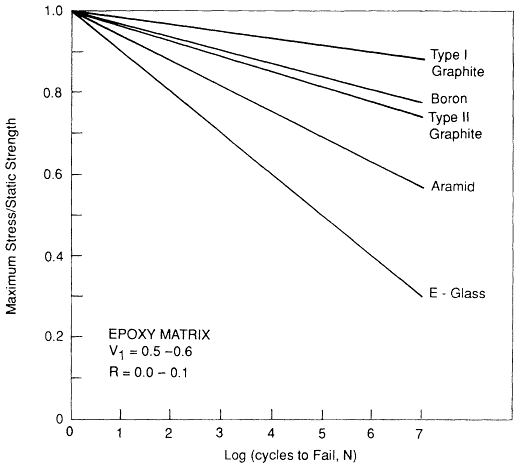
Figure 3-1
Trends of longitudinal tensile fatigue S-N data for unidirectional composites with various fibers.
Source: Mandell (1990).
As can be inferred from Table 3-2, the in situ tensile failure strain of E-glass fiber is as high as 2.5 percent, whereas it is only 1 percent for carbon fiber. However, E-glass fiber has a much lower fatigue ratio than carbon fiber, that is, 0.3 versus 0.75 at 10 million cycles (Figure 3-1). Therefore, both fibers have the same fatigue strain of 0.75% at 10 million cycles. Beyond 10 million cycles, however, the carbon fiber is expected to outlast the glass fiber. The cost ratio to obtain the same long-term fatigue strength is then at least the same as that needed to obtain the same stiffness. An additional benefit is that a hybrid composite blade will have a longer lifetime because of the reduced fatigue load resulting from the weight savings. Thus, a careful study is needed to explore the full benefits of a hybrid composite blade from a life-cycle point of view.
Fibers are used in various forms. The commonly used fiber preforms include unidirectional tow, woven cloth, knitted fabric, continuous strand mat, chopped strand mat, and braid as well as chopped fibers in sheet and bulk molding compounds. Depending on the application and manufacturing process used, one fiber preform may be preferred to others. The various fiber preforms are shown schematically in Figure 3-2.
Where high strength is required, unidirectional bundles of fibers known as tows should be used. Woven cloths and knitted fabrics are easier to use, especially over complex contours. Woven cloths have disadvantages in that
high fiber volume content cannot be attained and the inherent fiber cross-overs are susceptible to premature fatigue damage. The fiber cross-overs also result in low compressive strength. While continuous strand mats provide good strength, chopped strand mats are weaker because of the fiber discontinuity. Where delamination is a prime concern and strengthening is required in the thickness direction, braids can work well.
MATRIX MATERIALS
The matrix resins commonly used in wind turbine blades are divided into three major classes of thermosetting polymers: unsaturated polyesters, epoxies, and vinyl esters (Lee and Neville, 1967; Launikitis, 1978; Strong, 1989). The unsaturated polyester resins, typically based on the orthophthalic or isophthalic acid, are most widely used because of short cure time and low cost. Despite the long cure time required and higher cost, epoxy resins are gaining greater acceptance due to their superior chemical resistance, good adhesion, low cure shrinkage, good electrical properties, and high mechanical strength. A reasonably good compromise between cost, cure time, and the above-mentioned physical properties is achieved in epoxy-based vinyl ester resins, which have especially shown very rapid growth over the past few years by filling the gap between polyesters and epoxies. The use of all these resins as composite matrices is generally subjected to a temperature limit around 150° to 200°C. The upper temperature limit is lower than the glass transition temperature Tg because above Tg the resin becomes soft and rubbery, thus losing most of the load-carrying capability.
Polyesters, as their name implies, are resins in which recurring ester linkages are an integral part of polymer chain backbone. The most commonly used system--isophthalic polyester resins--is more expensive but is chemically more stable and a little less brittle than orthophthalic resins. The term unsaturated comes from the presence of carbon-carbon double bonds in the polyester chain backbone that provide the location for cross-linking, thereby eventually leading to a tight network. The most common type of cross-linking agent is styrene. The styrene also lowers the initial viscosity of the polyester resin to improve processing of the composite by facilitating impregnation and wetting of fibers. The cross-linking reaction, which is addition polymerization, is triggered by an initiator (sometimes erroneously called a catalyst), such as organic peroxide, that produces free radicals.
Many polyester resins are cured at room temperature with a rise in temperature due to the exothermic nature of the reaction. In this case, the typical cure time is several hours or overnight. However, with a proper selection of initiator, the cure reaction can be carried out at an elevated temperature in an extremely short time. Experience in automotive composites has shown that the curing of an unsaturated polyester can be completed in 2 to 3 minutes at 150°C with the use of a tert-butyl perbenzoate initiator.
Epoxy resins derive their name from the epoxide ring structure that serves as the principal cross-linking site. Although various types of epoxy resins are produced commercially, so-called diglycidyl ether of bisphenol-A (DGEBPA)-type resins (e.g., Shell EPON828), have achieved the widest market acceptance and demonstrated versatility. For applications requiring special properties such as high modulus or higher use temperature, other types of epoxy resins with higher functionality are used in place of difunctional DGEBPA-type resins. For instance, tetrafunctional epoxy resins of tetraglycidyl methylene dianiline (TGMDA) (e.g., Ciba-Geigy MY720) exhibit improved properties at elevated temperature. Greater strength and improved properties at elevated temperature are also achieved in the resins of epoxidized phenolic novolacs (e.g., Dow DEN438) or tetraglycidyl ether of tetrakis hydroxyphenyl ether (e.g., Shell EPON103). All these resins tend to have lower fracture toughness than DGEBPA-type resins.
For polyfunctional epoxy resins, cross-linking or cure is effected by use of polyfunctional curing agents or hardeners. The use of a hardener with higher functionality (e.g., tertiary amine versus primary amine) allows a greater cross-link density of cured resins, which generally improves their physical properties. Lewis acids, such as BF3, are catalytic curing agents
that promote the cure reaction but do not themselves serve as direct cross-linking agents. These catalytic curing agents have the advantage of very long shelf life and require significant heat to initiate the reaction. The resultant structure of Lewis acid-cured resin is very tightly cross-linked. Curing of most epoxy resins and composites is done at 120° or 177°C with a typical cycle time of 2 to 3 hours under the molding pressure of up to 1.4 MPa.
The term vinyl ester can be applied to any number of chemical compounds comprising an ester linkage and terminal unsaturation. There are several types of vinyl esters based on epoxy resins as well as nonepoxy resins. However, to the composites industry, the vinyl ester resins usually mean methacrylate esters of epoxy resins (Launkitis, 1978). Unlike polyesters, vinyl esters do not possess internal unsaturation. However, vinyl esters and polyesters are similar in that they both utilize a coreactant or cross-linking agent, such as styrene, and free radical-producing initiators, such as peroxides, to effect cure. As a result, vinyl ester resins can be cured in a very short time like polyesters, but their static strength and modulus properties are similar or comparable to those of epoxy resins.
Typical mechanical properties of polyesters, epoxies, and vinyl esters are shown in Table 3-3. While epoxy resins are at the top of the scale as far as mechanical properties are concerned, they require the longest cure time and are the most expensive. For example, epoxy resins cost about $1.80/lb, whereas unsaturated polyesters cost only $1.00/lb. Vinyl ester resins fall in between these two resins, costing about $1.60/lb. Thus, the final selection of a resin should consider the material cost as well.
The fatigue crack propagation rates of these resins vary with the stress intensity factor range ΔK in the case of other plastics for structural use (Hertzberg and Manson, 1980). In amine-cured DGEBA epoxy resins, the values for exponent m in the equation for the crack growth per fatigue cycle, da/dN = const.(ΔK)m, range from 7.7 to 20, which are higher than those for other plastics. In general, a lower fatigue crack growth rate and a higher fracture toughness are observed with increasing molecular weight between cross-links.
As discussed previously, all of these resins suffer the problem of brittleness. A brittle resin results in premature matrix cracking in the composite, which in turn facilitates moisture ingress. Although fracture toughness of the resin systems can be raised by increasing Mc or adding diluents, these approaches result in lowering of modulus and temperature resistance (Hertzberg and Manson, 1980; Owen, 1974; Christensen and Rinde, 1979). At present, many commercially available resins utilize toughening agents in the form of discrete particles of elastomers or ductile
TABLE 3-3 Properties of Cast Resins
|
Polyester |
Vinyl Ester |
Epoxy |
Specific gravity |
1.10-1.46 |
1.1-1.2 |
1.2-1.3 |
Flexural strength, MPa |
60-160 |
120-140 |
110-215 |
Tensile strength, MPa |
40-90 |
70-90 |
50-130 |
Compressive strength, MPa |
90-200 |
- |
110-210 |
Tensile elongation, % |
<5 |
<6 |
<9 |
Modulus, GPa |
2-4 |
3-4 |
3-4.5 |
Source: Lee and Neville (1967), Bucknall (1977), Lubin (1982). |
thermoplastics. In this case the increase of fracture toughness is achieved with a relatively small change of modulus and temperature resistance.
Toughening of epoxy resins by the inclusion of elastomer particles is well established. Although several different types of liquid or solid elastomers or their hybrids can be used, the most effective way of increasing resin toughness is by using a liquid rubber with specific terminal functional groups (Lee, Riew, and Moulton, 1980; Bucknall, 1977; Riew, Rowe, and Siebert, 1976; Scott and Phillips, 1975; McGarry and Sultan, 1969; Bascom, Bitner, Moulton, and Siebert, 1980; Moulton and Ting, 1981; Lee, 1986). Examples are butadiene acrylonitrile copolymers with carboxyl, amine, or vinyl groups at both ends of the chain which are selected depending on the type of curing agent and curing mechanisms.
When carboxyl-terminated butadiene acrylonitrile copolymer (CTBN) is mixed in liquid state with an amine-cured DGEBPA epoxy resin, their initial compatibility in liquid state followed by phase separation in the solidification process leads to the formation of submicron-sized elastomer particles that are well bonded to the surrounding resin. As a result, adding as small as 5 wt% of CTBN to Epon 828 resin increases the fracture toughness G1c from 350 to 5260 J/m2. Yet the accompanying decrease of tensile modulus is only 2.5 to 2.8 GPa (Riew, Rowe, and Siebert, 1976). A similar type of elastomer toughening in extremely brittle TGMDA resins (G1c = 80 J/m2) is less effective: a maximum twofold increase with considerable reduction of modulus (Lee, Riew, and Moulton, 1980).
The use of elastomer-toughened epoxy resins as matrix materials has been shown to improve the interlaminar fracture toughness of fiber-reinforced composites, particularly those with woven fabric reinforcement with resin-rich areas between the plies (Bascom, Bitner, Moulton, and Siebert, 1980). Despite a high level of constraint on thin films of resin matrix by densely packed surrounding fibers (Scott and Phillips, 1975), toughening of epoxy matrices also increases the resistance of composites against local damage initiation and accumulation (McGarry and Sultan, 1969; Bascom, Bitner, Moulton, and Siebert, 1980; Moulton and Ting, 1981; Lee, 1986). However, their effects on fatigue lifetime or fatigue endurance limit of composites have not been fully confirmed.
In the case of toughening of unsaturated polyester resins, both liquid elastomers with terminal functional groups and ductile thermoplastics are utilized as a secondary phase (McGarry, Rowe, and Riew, 1978; Lee, Howard, and Rowe, 1983). Examples are vinyl- or epoxy-terminated butadience acrylonitrile elastomers, hydroxyl- or vinyl-terminated epichlorohydrin elastomers, and polyvinylacetate. Compared with elastomer-toughened DGEBPA epoxy resins, the size of elastomer particles formed in situ during cure is much bigger (micron level) because of lower compatibility of the reactive mixture. As a result, the effectiveness of elastomer toughening of polyester resins is much lower than that of DGEBPA epoxy resins. For instance, by adding 8 wt% of vinyl-terminated polyepichlorhydrin elastomer, the fracture toughness G1c of isophthalic polyester resin is increased from 60 to 110 J/m2 with a 23 percent reduction of tensile modulus. However, the use of elastomer-toughened unsaturated polyester resins in short fiber-reinforced composites increases the local damage resistance under impact and, in certain cases, that of tensile strength as well (McGarry, Rowe, and Riew, 1978; Lee, Howard, and Rowe, 1983).
In addition to thermosetting resins, many engineering thermoplastics are available now as matrix resins. Table 3-4 lists those new high-performance thermoplastic resins developed mainly for aerospace applications (Witzler, 1988). Compared with thermosetting resins, the thermoplastic resins offer advantages in prepreg (pre-impregnated laminate) stability and short processing cycle. However, they tend to be weak in solvent resistance and fiber impregnation. Trade-offs between thermosets and thermoplastics as matrices are shown in Table 3-5.
Unidirectional prepregs also are available with commodity thermoplastics such as nylon and PET. Although they are cheaper than the high-performance thermoplastic prepregs, their full potential has not been realized because of the lack of low-cost manufacturing techniques.
TABLE 3-4 High-Performance Thermoplastics Used as Matrix Resins
Polymer |
Type |
Trade Name |
Manufacturer |
Tga, °F |
Processing Temperature, °F |
Polyetheretherketone (PEEK) |
Semicrystalline |
APC-2b |
ICI |
290 |
650 |
Polyphenylene sulfide (PPS) |
Semicrystalline |
Ryton |
Phillips |
185 |
630 |
Polyarylene ketone |
Semicrystalline |
HTX |
ICI |
400 |
700-789 |
Polyarylene sulfide |
Amorphous |
PAS-II |
Phillips |
410 |
625-650 |
Polyetherimide (PEI) |
Amorphous |
Ultem (resin) |
GE |
Varies |
Varies |
|
|
Cypacb |
American Cyanamid |
|
|
|
|
Cypac 7000/7005 |
|
450 |
575-650 |
|
|
Cypac 7156 |
545 |
650-700 |
|
Polyarylether |
Amorphous |
Radel C |
Amoco |
476 |
650 |
Polyethersulfone |
Amorphous |
HTA |
ICI |
510 |
575 |
Polyamide-imide |
Amorphous |
Torlon |
Amoco |
470 |
650 |
Polyimide |
Pseudothermoplastic |
Avimid |
Du Pont K-III |
480 |
680 |
|
|
LaRC-TPI |
Mitsui Toatsu, Rogers Corp. |
482 |
660 |
|
|
2080 |
Lenzing |
536 |
660 |
|
|
9725 |
Ciba-Geigy |
536 |
660 |
a Tg is the glass transition temperature, the temperature at which a polymer changes from a rigid glassy solid to a soft rubbery solid. b Prepreg. Source: Johnston and Hergenrother (1987). |
TABLE 3-5 Trade-offs Between Thermosets and Thermoplastics as Matrices
Property |
Thermosets |
Thermoplastics |
Formulations |
Complex |
Simple |
Melt viscosity |
Very low |
High |
Fiber impregnation |
Easy |
Difficult |
Prepreg tack |
Good |
None |
Prepreg drape |
Good |
None to fair |
Prepreg stability |
Poor |
Excellent |
Processing cycle |
Long |
Short to long |
Processing temperature/pressure |
Low to moderate |
High |
Fabrication cost |
High |
Low (potentially) |
Mechanical properties |
Fair to good |
Fair to good |
Environmental durability |
Good |
Unknown |
Solvent resistance |
Excellent |
Poor to good |
Damage tolerance |
Poor to excellent |
Fair to good |
Data base |
Very large |
Small |
The difficulty associated with fiber impregnation has led to the development of commingled yarns and fabrics as well as powder-coated yarns and fabrics. A commingled yarn consists of both reinforcing fibers and thermoplastic fibers. During processing the thermoplastic fibers melt and impregnate the reinforcing fibers (Lynch, 1989). Thermoplastic powder is smaller in diameter than the corresponding thermoplastic fiber and hence is more evenly distributed in the yarn, which facilitates a more uniform fiber impregnation (Hartnes, 1988).
E-GLASS/PLASTIC COMPOSITES
E-glass/plastic composites, commonly called glass-reinforced plastics (GRPs), have been widely used in the manufacture of blades of various sizes. Typical resins used in GRPs are polyester, vinyl ester, and epoxy. Although polyester resins can be cured in the shortest time, they show large shrinkage and hence may not be appropriate for use in a hot, dry environment such as California, where moisture-induced swelling would be minimal (Windpower Monthly, 1987). Vinyl ester resins have good environmental stability and are widely used in marine applications. Epoxy resins have good mechanical properties and dimensional stability. Their drawback is longer cure time and higher cost; however, new epoxy resins are now available for pultrusion and resin transfer molding, which require fast curing.
GRP is the main structural material for a number of blades of large machines and is also used as cladding over steel load-bearing frames in others (Phillips et al., 1987). GRP is the most popular blade material used in medium-size machines in Denmark and The Netherlands. As of January 1987, approximately 81 percent of 15,059 wind turbines in the California wind farms had fiberglass rotor blades (Stoddard, 1989; Modern Power Systems, 1986).
Typical properties of a unidirectional E-glass/epoxy composite are compared with those of other unidirectional composites in Table 3-2. For all the composites in the table, the stress-strain behavior is usually quite linear except in transverse compression and in-plane shear. Another exception is thearamid/epoxy composite, which is quite nonlinear in longitudinal compression also. Elastic properties of multidirectional laminates can be calculated from unidirectional properties using laminated plate theory (Tsai, 1989; Jones, 1975).
Tensile stress-strain relationships of several representative E-glass/epoxy laminates are shown in Figure 3-3. When a multidirectional
laminate, such as the quasi-isotropic laminate in the figure, is subjected to tension, cracks appear first in the matrix and fiber/matrix interfaces of off-axis plies (Tsai and Hahn, 1975; Reifsnider, 1980). Most of these cracks, called ply cracks, are entirely through the thickness of individual off-axis plies. The crack density increases with increasing load until some of the cracks grow as delamination between plies with different fiber orientations. Further increase of load breaks the fibers in the on-axis plies, leading to failure of the laminate as a whole. When the load is along the 0° direction, 90° plies may fail at a strain as low as 0.3 percent, although the laminate does not fail until 2.3 percent strain is reached. Thus, failure of a multidirectional laminate is preceded by matrix/interface cracking in the off-axis plies and also by delamination between plies with different fiber orientations.
The ply cracking in general does not lead to immediate failure of the laminate. However, it facilitates moisture diffusion through the cracks, thereby reducing the durability of the laminate. Even in the absence of cracks, epoxy resins can absorb as much as 7 percent moisture by weight. The absorbed moisture plasticizes the resin, thereby reducing its glass transition temperature. When fully saturated, the glass transition temperature of epoxy resins can be reduced by as much as 100°C (Vinson, 1977).
At room temperature, absorbed moisture has a rather minimal effect on mechanical properties. When combined with elevated temperature, however, it can seriously degrade mechanical properties through interfacial debonding and matrix plasticization. The worst combination is thermal spiking to a temperature above the glass transition temperature in the presence of moisture. The thermally spiked specimens show increased moisture absorption and lower strengths (Springer, 1981).
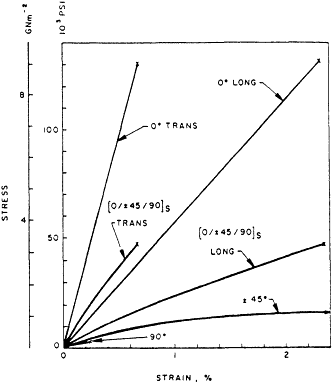
Figure 3-3 Stress-strain relationships of glass/epoxy laminates under uniaxial tension (50 vol%). (LONG: strain parallel to loading direction; and TRANS: strain [magnitude] normal to loading direction)
To provide a smooth surface and also to prevent moisture diffusion, a gel coat is frequently applied on the surface of the blade. However, moisture still can diffuse through the gel coat and collect at the gel coat/composite interface, resulting in blistering. Thus, the benefits of a gel coat as a means of preventing moisture infusion are not clear (Phillips et al., 1987). Also, it has been found that E-glass/epoxy blades are prone to crazing in the surface finish. In some blades, several small delaminations have been found under the outer covering of Nexus cloth, and voids were present under the outer layer of fiberglass roving. Although these damages are not critical immediately, they may facilitate water ingression, accelerating deterioration of the composite.
The tensile fatigue stress-lifetime (S-N) data of various types of composite laminates can be represented by an equation of the form (Mandell, 1990),

where S is the maximum fatigue stress, UTS is the ultimate tensile strength, and N is the number of cycles to failure. This is the form of the curve in Figure 3-1. The parameter B represents the fraction of UTS lost per decade of fatigue cycles. For E-glass/epoxy laminates, B is about 0.1 regardless of whether the laminate is unidirectional or multidirectional when the fatigue stress ratio R = 0.1 (Mandell, 1990). Since very little fatigue data exist beyond I million cycles, fatigue strength at 100 million cycles, which is a minimum requirement for wind turbine blade design, is estimated to be 20 percent of the ultimate strength. In terms of strain the fatigue strain at 100 million cycles is only 0.5 percent although the static ultimate strain is as high as 2.5 percent. In comparison, aramid fiber/epoxy composites lose about 6 percent of UTS per decade, while carbon fiber composites lose only 3 to 4 percent of UTS. Thus, a carbon fiber composite enjoys a higher fatigue strain of 0.7 percent, although it has a much lower ultimate tensile strain than glass/epoxy composites.
The failure sequence of multidirectional laminates under fatigue is quite similar to that under static tension when the load is replaced by the number of fatigue cycles. As schematically shown in Figure 3-4, the damage is initiated in the form of cracking of off-axis plies across their thickness. As fatigue proceeds, the crack density grows rapidly, reaching a plateau. Thereafter, the ply cracks grow along the ply interfaces, leading to delamination. Much of the fatigue life is spent in the delamination stage between the ply cracking and fiber failure stages (Reifsnider et al., 1983). The ply cracking stage is especially short in glass composites because the transverse failure strain is much lower than the longitudinal failure strain.
The ply cracking and delamination degrade compressive strength more than tensile strength when the fibers used in the composite are not so fatigue sensitive. Delamination facilitates buckling and hence reduces compressive strength substantially. This is the reason that composite laminates fail in compression under fully reversed tension-compression fatigue. In fact, the maximum fatigue stress at R = -1 is only about half the maximum fatigue stress at R = 0.1 (Ven Delft et al., 1987; Bach, 1988). Also, composite laminates are weaker in compression-compression fatigue than in tension-tension fatigue, especially in the low-cycle region.
Another consequence of ply cracking and delamination in multidirectional laminates is reduction in stiffness. For example, the fatigue failure of a quasi-isotropic glass/epoxy laminate at 10 million cycles (R = 0.1) can be accompanied by a stiffness reduction as large as 35 percent (Zweben et al., 1989). Thus, design for fatigue may have to be based on stiffness reduction rather than strength reduction if maintaining sufficient stiffness is more critical.
FATIGUE LIFE PREDICTION
The prediction of fatigue lifetime of a rotor blade starts with the determination of loads applied on the blade. The loads are induced not only by steady winds and turbulence but also by starts and shutdowns of the turbine (Murtha-Smith, 1985). For metallic blades the resulting fatigue load cycles
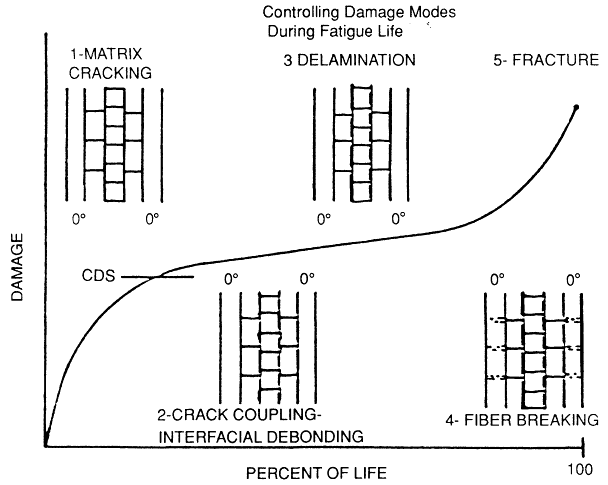
Figure 3-4
Modes of damage growth in composite laminate under fatigue.
Source: Reifsnider et al. (1983).
may be determined using a rainflow counting algorithm, with each cycle being characterized by a mean fatigue stress and an alternating stress (Murtha-Smith, 1985; Downing and Socie, 1982; Morgan et al., 1989). Once the fatigue cycles are defined, the lifetime is predicted by using a combination of Miner's rule and constant-amplitude fatigue data or a crack growth law (Sutherland, 1989).
It is difficult, however, to predict lifetimes of composite wind turbine blades because their failure modes are complex and no sufficient database exists. Fatigue failure of a composite laminate depends on the specific lay-up and style of material used. Therefore, the existing data are not likely to be directly applicable to the chosen laminate. Furthermore, although the blade is subjected to multiaxial, variable-amplitude loading that involves several different fatigue stress ratios, most available data are for uniaxial, constant-amplitude tensile fatigue. Therefore, the current fatigue design practice is to generate constant-amplitude fatigue data for a laminate
simulating the actual blade lay-up and then use the metals methodology to predict the lifetime under operational loading (Murtha-Smith, 1985).
Several unique characteristics of composite laminates should be recognized in applying the metals life prediction methodology. First, composite laminates exhibit different hysteresis loops than metals. While the unloading modulus does not change much with fatigue cycles in metals, it decreases with increasing fatigue cycles in composite laminates as a result of ply cracking and delamination. Also, since composite laminates are weaker in compression, especially under fatigue, the maximum alternating stress on a Goodman curve tends to be located in the positive mean-stress quadrant. Implications of these differences in the application of the metals life prediction methodology have not been examined in detail.
The first appearance of ply cracking in a laminate can be predicted from the fatigue behavior of constituent plies using the laminated plate theory together with a failure criterion (Zweben et al., 1989). After a ply fails, the state of stress changes. This stress redistribution is taken into account when the next failure event is predicted using another failure criterion. This process continues until the laminate fails as a whole.
Although this life prediction procedure is straightforward conceptually, its implementation is rather difficult because of the complex stress analysis involved and the lack of sui criteria for various failure events. An alternate approach is to use residual strength to describe the overall degradation of the composite. Basically, the rate of change of residual strength is postulated as a function of fatigue stresses, similar to a crack growth law. Fatigue failure is then assumed to occur when the residual tensile/compressive strength is reduced to the maximum/minimum fatigue stress. The parameters involved are determined by fitting the model prediction to the experimental S-N data. The scatter in fatigue life is related to the scatter in static strength through the assumption of similitude that a specimen with a higher static strength also has a longer fatigue lifetime. Variations of this residual strength approach have been used by several investigators to analyze laboratory fatigue data (Hahn, 1979; Sendeckyj, 1981; Yang and Shany, 1983; Reifsnider, 1980; Hwang and Han, 1989). These residual strength models can predict lifetimes under spectrum loading on the basis of constant-amplitude fatigue data. Thus, they can be used instead of Miner's rule, which has been found to be inaccurate for some composites (Bowen et al., 1984).
While the prediction of final failure is mostly phenomenological, ply cracking and delamination, which are two of the major subcritical failure modes, have been analyzed mechanistically. A damage growth law similar to the crack growth laws for homogeneous materials can be used to describe the multiplication of ply cracks (Han and Hahn, 1989) and the delamination growth (Johnson, 1985) under controlled conditions of loading and specimen geometry. The subcritical damages may degrade the strength of the main load-bearing plies, thereby accelerating the final failure and reducing the stiffness (Reifsnider and Stinchcomb, 1986). Reduced stiffness may change the loading on the blade and eventually cause premature failure. Thus, successful design of blades requires the ability to predict not only the final failure but also the growth of subcritical damages and the resulting stiffness reduction.
Composite structures are sensitive to out-of-plane loads, which can cause delamination (Whitehead, 1990). These loads are present especially at joints and impact-induced damage areas. While in-plane loads are effectively carried by fibers, out-of-plane loads place an unexpectedly heavy burden on the matrix-controlled strength. Unfortunately, the matrix-controlled strength is sensitive to the presence of defects such as porosity and delamination. Since geometrically complex regions tend to contain a high level of porosity while being subjected to out-of-plane loads, these regions of the blade must be identified and tested for long-term fatigue performance under realistic loading conditions and environments. At the same time, realistic impact energy levels should be established, and their effect on fatigue lifetime should be investigated.
As mentioned earlier, carbon fibers, unlike glass fibers, are almost insensitive to fatigue degradation. Experience has shown that fatigue is not a problem in aircraft wings and fuselage structures, where carbon fiber composites are used, if the maximum strain is kept below 0.6 percent.
Therefore, the same static knockdown factor can be used as well for fatigue strength to account for the effect of defects (Whitehead, 1990). It is suggested that the current unfavorable economics should not preclude the use of carbon fibers together with glass fibers in wind turbine blades to avoid fatigue problems.
TOUGHNESS CONSIDERATIONS
Wind turbine blades are expected to benefit from the use of tougher composites in several ways. One obvious benefit is the reduction in matrix cracking and hence a better protection of fibers from moisture degradation. Another benefit is the reduction in stress concentration and hence more efficient mechanical joining. In fact, one of the main causes for the hub failure in Aerostar blades is believed to be the crushing of the brittle polyester resin used. Last but not least, benefit is found in higher-impact resistance.
During their lifetime, wind turbine blades are subjected to impact by foreign objects such as rain drops, flying debris, and other objects. Since most impact occurs on the leading edge, proper protection of that leading edge can minimize the impact problems.
Composites are more susceptible to rain erosion than metals. Upon localized impact by rain drops, the matrix resin can be chipped away, exposing fibers. Impact by larger foreign objects can break the fibers, crack the matrix and interface, and induce delamination between plies. Impact damage may also occur during shipping and handling. Unfortunately, even an invisible damage caused by impact can substantially reduce compressive strength (Williams and Rhodes, 1981). Therefore, a low compressive strength after impact has been one of the main obstacles to wider application of composites.
Reduction of impact damage requires the use of tougher resins; yet, too tough a resin may inadvertently transfer too much load to the fibers during impact, resulting in unwanted fiber fracture. A compromise should be made between matrix/interface cracking and fiber break through proper selection of resin toughness. Nevertheless, a tough resin usually yields a higher compressive strength after impact than a brittle resin does.
As discussed earlier, much progress has been made lately in the development of toughened thermosetting resins for composites. As a result, there are a variety of toughened resins available at present. In addition, the high-performance thermoplastic resins in Table 3-4 all exhibit high toughness.
In general, a tougher resin yields a tougher composite. The relationship between the neat resin fracture energy and the composite interlaminar fracture energy appears to be bilinear (Hunston, 1987). When the resin is brittle, the composite has a higher interlaminar fracture energy than the resin fracture energy, mainly because of the fiber bridging. As the resin becomes tougher, however, not all the resin toughness is translated to the composite toughness. In fact, the composite fracture energy is only close to the rule-of-mixtures estimate.
There are other ways of improving the impact resistance of composite laminates. One method is to place a tough resin interleaf between plies to arrest ply cracks and to accommodate large, local shear stains induced by impact. The other is to provide reinforcements in the thickness direction by stitching (Hunston, 1990). These methods can be implemented without incurring too high a cost.
Glass fibers are more resistant to impact damage than carbon fibers. Thus, any scheme of composite toughening is expected to work better with glass fibers than with carbon fibers.
WOOD/EPOXY COMPOSITES
When the first wood/epoxy blades were designed for the 38-m (125-foot) diameter NASA MOD 0A wind turbine, the available material properties data were limited. A survey of the compression, shear, and bending strength of many
wood species was available in the U.S. Forest Products Wood Handbook (1974), along with equations to correct the base values to different moisture levels. Values for along-the-grain modulus of elasticity and across-the-grain tension and compression strength were also available in these s. These data were valuable in assessing which species would likely be best suited to wind turbine use and in estimating the weight, stiffness, and static strength of a candidate design. However, only minimal guidance concerning the effects of fatigue, load duration, and component size on long-term allowable strength was given.
Some research on wood fatigue was available from long-term, constant-deflection, bending tests performed in the 1940s by W. J. Kommers (1943a, 1943b). These tests did not cover a wide range of R ratios or allow a clean separation of tension, compression, and shear strength, but they did provide lower bounds for those properties and showed that the base wood material had potentially attractive high-cycle fatigue capability. The effect on strength of the epoxy, or of the butt joints that would be needed to assemble a blade from individual veneer sheets, was simply unavailable, for either static or fatigue conditions. Questions of how moisture and temperature variations would interact with the above in high-cycle fatigue to determine long-term allowable strength were also unanswered. Engineering judgment to extrapolate from a few sources of available test data plus conservative design to cover areas of material property ignorance were, therefore, a requirement for the initial design work.
When the initial design studies began to reveal considerable promise for wood/epoxy as a wind turbine blade material, testing of a few key strength features quickly followed. For the base material, this meant some strength testing of fir/epoxy laminate, both with and without typical butt joints. For the critical blade-to-hub connection, it meant both static and fatigue testing of the bonded steel stud load takeoff system, as the earliest versions of these studs did not have the strength required for the MOD 0A application, and rapid design evolution was needed to gain a demonstrated margin against the design loads (Faddoul, 1981). Static and fatigue performance was further demonstrated by a 20-foot test article that was in essence the inboard one-third of the full size blade. While a great deal was still unknown about the fundamental material and joint properties at this point, factors critical to this particular design were well enough known that the resulting blades served successfully in the field for the duration of the DOE/NASA MOD 0A program (Lark et al., 1983; Faddoul, 1983).
Smaller blades for the Enertech 13.4-m (44-foot) diameter and ESI 16.5-m (54-foot) diameter machines were designed with about the same level of basic knowledge and also served successfully in the field, with one such machine now having over 25,000 operating hours (Clark et al., 1985). Of the thousands of such blades built and used, none has been retired because of fatigue. Only failures from lightning strikes, storms, machine runaways, or similar incidents have been reported.
While the economics of small blades and early wind machines could tolerate some design margin to cover incomplete materials data, larger machines aiming for more cost-effective energy production did not possess as much weight tolerance. This became most evident in the DOE MOD 5A program, which was a teetered, two-bladed upwind design that eventually grew to 122 m (400 feet) in rotor diameter and over 7 MW in rated power. Steel, GRP, and wood/epoxy were all assessed in the initial rotor trade-off studies, and it became quite clear that the gravity-induced stresses from rotor weight were a significant design driver and that high-cycle material allowables had a big impact on rotor weight and cost. Wood/epoxy was eventually selected for this project, as it showed the lightest weight and least cost. But it was known that major gaps in the material and joint properties data would have to be filled to use the material efficiently and confidently, and so a major test program was initiated to support this design effort. The eventual testing included tensile tests of specimens 9.1 m (30 feet) long, with a 61-cm (24-inch) by 15-cm (6-inch) cross-section, that took over I million pounds to fail in static tension. Both static testing and fatigue testing of planks up to 5 cm (2 inches) by 20 cm (8 inches) by 9.1 m (30 feet) were performed. In addition, a great many lab-size specimens were tested. Materials with butt
joints, scarf joints, and without joints were compared to quantify the effect of joints. Shear testing at joints, both with and without bonding voids, was performed both in fatigue and static loading. While the MOD 5A was never built, the legacy of that program was a vast improvement in the depth and breadth of wood/epoxy material property data, only part of which has been mentioned here.
In 1986, Gougeon Brothers, Inc., under a DOE/SBIR (Small Business Innovative Research) award, carried out a study to advance the performance of jointed veneer laminate. This was followed by a Phase II grant to extend the initial joint investigations with more fatigue tests (including micromechanical study of crack propagation at joint sites) and to study a range of other material property topics, such as cross-grain tension (σy, σz) and rolling shear (τyz) strength (see Figure 3-5) in both static and fatigue loading as a function of size and the mechanical and cost performance of graphite fiber augmentation between the veneer layers for high-stress applications.
The work covering the MOD 5A experience has been prepared by NASA and was recently released (Spera et al., 1990). The experimental data from these extensive research efforts, along with in-house work at Gougeon Brothers, and material research published as part of the British wood/epoxy wind turbine blade efforts (Ansell et al., 1987; Bonfield and Ansell), have tremendously advanced current knowledge of these material properties, even though some gaps in the data still remain. A discussion of some of the main features of these data follows to outline a number of the major lessons learned, some of which may also be applicable to GRP or other candidate blade materials.
The static tension and compression strengths of wood/epoxy laminate are distinctly different and respond differently to various factors. For instance, loss of along-the-grain strength with increasing size is much more severe in tension than in compression.
This reduction of strength with increasing size is called size effect. It is a stochastic process due to the accumulation of material defects as item size/volume increases. The worst such defect in the stressed volume limits strength in a statistical fashion. A tiny specimen of fir may show static tensile strength nearly twice its static compression strength, but for laminated members the size of large wind turbine blades, the static tension and compression strength will be about equal. This is due to a much more rapid loss of strength with size for tension than for compression. Early tests of size effect relied on beams in bending (Bohannan, 1966), but due to the nonlinearity of stress through the thickness resulting from crushing on the compression side, it was difficult to cleanly separate the tension and compression stresses at failure. This nonlinear effect is why a stick snaps on the tension side when bent, despite its greater tension strength capability. For adequate stress design of large wind turbine blades, this ''size effect'' must be separated, understood, and accounted for, as the strength correction relative to small laboratory samples can easily reach a factor of 2 in tension. Fortunately, size effect is now reasonably well quantified for static tension in wood/epoxy, although the less severe static compression case is still not well quantified.
While size effects along the grain (σx) are design drivers because they directly affect the allowables in the primary structure of the wind turbine blade, across the grain strength (σy and σz) (analogous to through the ply strength σz for GRP) (Figure 3-5) shows far bigger static strength differences and size effect (Barrett, 1974; Barrett et al., 1975; Weibull, 1939). For typical wood/epoxy laminates, across the grain tensile strength may be only one-fourth of the across the grain compression strength, and perhaps one-twentieth of the along the grain tensile strength (Table 3-6). Making matters worse is the fact that size effect in cross-grain tension is much more severe than along the grain, and differences between strength levels measured with small samples in the laboratory and those for large structures in the field could exceed a factor of 5. The upshot of this is that cross-grain tension stresses that may seem so modest as to be of little concern to the unwary designer could in fact lead to fracture initiation and eventual failure of large, expensive blades in the field.
TABLE 3-6 Typicala Static Strength, Type 110 Laminate
Laminate Augmentation: |
None |
||||
Typical Density: |
0.23 1b/in3 (0.637 g/cc) |
||||
Nominal Test Temperature: |
66°-73°F (19°-23°C) |
||||
Veneer Specification: |
GMS-003, BG-2+, transverse butt joints, 3-in stagger |
||||
Test Method: |
Modified ASTM Standard D198-76. Specimens tested under load control to achieve constant rate of load increase from zero load to maximum load in approximately 5 minutes. |
||||
|
|
Maximum Stress at 8% w.m.c.d |
Maximum Stress at 12% w.m.c.d |
||
Test Directionb |
Type of Testb |
psi |
MPa |
psi |
MPa |
Longitudinal |
Compression |
9000 |
62.05 |
7200 |
49.64 |
Longitudinal |
Tension |
10,000 |
68.95 |
9400 |
64.81 |
Longitudinal |
Shear, type 4c |
1700 |
11.72 |
1600 |
11.03 |
Longitudinal |
Shear, type 5c |
1600 |
11.03 |
1500 |
10.34 |
Longitudinal |
Elastic modulus |
2.2 × 106 |
15.17 × 103 |
2.0 × 106 |
13.79 × 103 |
Tangential |
Compression |
2000 |
13.79 |
1600 |
11.03 |
Tangential |
Tension |
500 |
3.45 |
470 |
3.24 |
NOTES a These typical properties represent a composite of laboratory test data from specimens having various moisture contents and uniformly stressed volumes ranging from 19.5 in3 to 194.0 in3 (319.5 to 3179 cc). Properties are representative of structures similar to small wind turbine blades. Larger structures are characterized by lower mechanical properties. Adjustments in properties due to size effects and other conditions are considered by Gougeon Brothers in engineering each application. b See Figure 3-5 for illustration of stress directions. c See Figure 3-5 for laminate shear orientations. d Assumed wood moisture content. |
In contrast to the potentially dangerous cross-grain tension case, across the grain "rolling" shear has been found to exhibit a very modest size effect, and lab data can be safely applied to large static structures with very little correction. This also appears to be the case for cross-grain compression, although the data are rather incomplete for that case.
It has been known for some time that both temperature and moisture have a direct effect on the static strength of timber, and this holds true for the derivative wood/epoxy laminate as well, with some adjustments. Temperature effects are essentially those of the wood species used since it carries the bulk of the stress, and, given that temperature is relatively constant throughout a thick laminate, laboratory samples can be used to predict laminate effects (Figure 3-6). On balance, temperature effects are modest and fairly well understood, and, like GRP, it is the upper temperature extreme that must be accounted for in design. Ten to 30 percent strength reductions would not be unusual in a computation of worst-case static strength compared to room temperature.
Moisture effects are modified for wood/epoxy laminate to the extent that the epoxy seals out liquid water entirely and is a fairly effective barrier to the passage of moisture in the form of water vapor. As a result, a large structure will not respond to the short-term moisture fluctuations in its environment, but will instead come to equilibrium with the average humidity over a period of months to years (Figure 3-7). Static tension strength shows a much more modest effect from moisture in the normal outdoor range than does compression strength (Figure 3-8), but accurate design may require taking both into account depending on which property limits a specific design. If typical 12 percent wood moisture content reference data are used in design, most use environments are already covered, but a 10 or 20 percent strength credit may be available for dry environments, such as the California wind farms.
It has long been known that duration of load has a direct effect on the static strength of timber beams1 (Gerhards, 1977; Barrett and Foshi, 1978). For a 10-year steady load duration, the maximum load would be about 60 percent of that which could be carried in a test whose duration was only minutes. Limited test data confirm that duration and associated rate of loading effects exist in wood/epoxy laminates as well, but at present these data cannot be used to make accurate predictions for long field exposure. Separate data for tension and compression over a sufficiently long time span simply are not available. Also, there is reason to suspect that stabilization of the moisture level within the laminate due to the epoxy will retard the creep rupture mechanism compared to the unprotected timbers of earlier tests. However, no theory for estimating this, or reliable data for engineering use, is currently available, so the rather large traditional strength reduction must still be used until better information becomes available.
All of the above effects continue to play a role in determining the safe fatigue strength of wood/epoxy laminate, but their description, interaction, and quantification become more complicated for fatigue compared to static strength. To provide a logical separation of tension from compression fatigue effects, Department of Energy (DOE) laminate testing has concentrated on three primary loading cases: R = 0.1 tension (Figure 3-9), where the load is always tension and the least tensile stress is one-tenth of the largest; R = 0.1 compression (Figure 3-10), where the load is always compressive and the least compressive stress is one-tenth of the largest; and R = -1 reversed axial (Figure 3-11), where the stress alternates between equal levels of tension and compression on each fatigue cycle. As is seen, the first two cases are pure tension and pure compression, and the last involves both tension and compression to reveal interaction effects. These cases correspond reasonably well to major design-driving stresses in many wind turbine blade designs. The nonreversing R = 0.1 tension and compression loads are similar to those found in the upwind and downwind blade structures due to aerodynamic lift in the
blade, while loads that are nearly fully reversing will be found near the blade's leading and trailing edges due to the deadweight gravity bending moment.
Testing (both with and without joints in the laminate) shows the lowest strength levels and most rapid loss of strength with increasing cycles for the reversed load R = -1 case. Strength levels for R = 0.1 tension fatigue can be 50 to 100 percent higher than for reverse axial, but the rate of strength loss with cycles is similar. Depending on size, compression strength will generally be somewhat lower than tension at low cycles, but its strength loss rate is only about two-thirds of that for tension, so it can cross over and exceed tensile strength at higher cycles, particularly for large blades. These strength loss rates tend to be s for each type of loading over a wide range of cycles. Consequently, the data plot as a straight line on a log-log stress versus number of cycles (S-N) plot. This linear trend certainly holds valid up to 107 cycles; there are not enough data beyond that to determine where or if a fatigue endurance limit exists. That knowledge could be valuable for better assessment of very high cycle strength and life, but the appropriate data are expensive and time consuming to obtain. Current life and strength assessments are forced to assume that the loss of strength shown at lower-cycle levels continues at the same rate to arbitrarily high cycles.
The effect of size on strength varies dramatically with the type of loading. While size effect for static tensile strength along the grain shows strength loss that can be a factor of 2 between laboratory samples and large blades, it becomes worse for tension fatigue where it can reach roughly a factor of 3. For fully reversed R = -1 fatigue, the size effect drops back about to the 2:1 level of static tension. Size effect data for compression fatigue and static compression strength are minimal, but size effect appears to drop further to perhaps 1.5:1 for R = 0.1 compression fatigue and to some lesser but ill-defined value for static compression (Spera et al., 1990).
Recent research work in size effect in the secondary material properties of cross-grain tension and rolling shear was not able to cover the range of R ratios needed to draw conclusions similar to the above, but it revealed a new phenomenon due to carefully controlled sample design and test structure, namely that size effect is more severe for higher-cycle levels. While rolling shear showed very little loss of strength with size in static tests, that was no longer true at 106 cycles; and while cross-grain tension did show substantial size effect in static tests, it again became considerably greater at 10 6 cycles. An associated effect is that the fatigue curve slope, the rate of strength loss with cycles, is larger for the larger specimens. So not only do larger specimens start out with a lower initial static strength, that strength is lost faster on a fractional basis in fatigue than it is for smaller samples (Bertelsen and Zuteck, 1991).
These lessons in size effect are important and will be increasingly so as wind turbines grow larger for economic reasons. There is good reason to suspect that size effect will occur in all materials currently contemplated for future wind turbine rotors, including GRP and metals, particularly for high-cycle fatigue. We now have experimental proof that low levels of size effect in static tests are no assurance of its absence in high-cycle fatigue, and designs undertaken in ignorance of these effects could lead to expensive or even dangerous failures in future large-scale machines.
The interaction of long-term environmental effects with the fatigue process has been partially addressed in wood/epoxy design by running fatigue tests at a range of temperature and moisture levels. However, it was found that the cycle rates typical for long-duration tests drove substantial moisture from the test specimens, thereby elevating their strength and fatigue performance. This may not occur in the same way at the lower-cycle rates and intermittent use that occurs in the field, so caution must be exercised lest the elevated performance of laboratory samples lead to excessive high-cycle fatigue expectations in the field.
The effect of veneer splice joints on strength is much more pronounced in fatigue than in static strength. Early work quickly highlighted this and showed that 10 to 20 percent strength loss could easily occur owing to these tiny joints distributed throughout the laminate. The effects were particularly apparent in tension and in high-cycle fatigue. The first
attempts to combat this by using beveled scarf joints between the veneers met with only limited and frustratingly intermittent success. In the large-scale fatigue specimens, performance was decidedly poor, and zipper-like failures through large numbers of joints often occurred. This puzzling state of affairs has been investigated at length in the recent Small Business Innovative Research (SBIR) research work and was traced to expanding gas driving resin from the joints during the vacuum molding process (Bertelsen and Zuteck, 1991). The path to higher-performance joints through mitigating this effect now seems clear in principle, but a practical manufacturing method has yet to be proven. The important general lesson is that defect-driven failure modes that are hard to spot in small specimens tested in static or low-cycle loading may emerge as major issues in bulk specimens tested to moderately high cycles. It is difficult to see how the high-cycle fatigue performance of large structures can be assured without at least a few tests of large-volume specimens to elevated cycles. Fortunately, considerable data of this sort now exist to support the most critical design areas of large wood/epoxy wind turbine blades. However, those data are by no means complete, and comparable data for design in GRP are unavailable.
Practical limits to the amount of materials data available will always exist, and perfect knowledge is not necessary to execute a successful design. The benefit of improved materials knowledge is that a more appropriate design that sidesteps pitfalls without undue cost can be provided and can be put into service with a much lower uncertainty as to its operating envelope and expected life. The record of wood/epoxy blades in the field has been excellent despite early materials data limitations due to confining the design window to stay within available knowledge. A wider design window is now available due to knowledge accumulated over the past decade. This will be needed in addressing the larger, more cost-effective designs that are needed in the future. A still broader design window can be opened by addressing the known shortfalls in the existing data and any additional ones that may be revealed as further advanced blade design occurs.
RECOMMENDATIONS
When designed and manufactured properly, glass/polymer and wood/epoxy rotor blades can provide tens of thousands of hours of operating time. The recent advances in composites technology, however, may provide an excellent opportunity to further improve the blade cost/performance. The knowledge base gained over the past two decades in the aerospace industry can now be used to assess these more efficient blade designs using advanced composites. What is needed is a focused research to refine the design along with improved materials knowledge in certain key areas. Specific recommendations for further research are described below, in the order of priority:
-
Long-term fatigue data should be generated to at least 100 million cycles for the most useful composite laminates and critical elements containing manufacturing defects, under appropriate environmental conditions. Separate tension and compression fatigue data should be generated so that independent lifetime projections for upwind and downwind portions of blade skin can be made. Fully reversed fatigue data should also be obtained for the projection of life against edgewise gravity loads. Moderate-cycle R ratio data may be needed to fully define material fatigue response. The data should include documentation on the modes and growth of damage as well as the effect of damage on properties.
-
At least a few large specimens of the favored composite laminates should be tested in moderate- to high-cycle fatigue to quantify the fatigue size effect allowance that must be made for large rotors in the primary loading regimes. All loading cases are needed for GRP. For wood/epoxy, size effect in static compression and compression fatigue is not yet quantified. Sui tests comparing small and large specimens of matched parent material are needed to fill this gap in the data.
-
Spectrum loading data to assess the available cumulative damage models are not yet available but are needed to fully quantify high-cycle life predictions. A life prediction methodology should be developed to predict
-
blade lifetimes based on constant-amplitude fatigue data. It should also be able to predict the modes and growth of damage.
-
A database should be established for wind turbine blade materials. It should include mechanical properties on fibers, matrix resins, and composites, including wood/epoxy. An extensive search of all fatigue data on both GRP and wood/epoxy should be conducted and the results included in the database.
-
Benefits of hybrid composites should be explored through design and limited testing. Design studies should investigate savings on blade weight and life-cycle cost. The best hybrid reinforcement appears to be carbon for either GRP or wood/epoxy.
-
Duration of load and creep effects are incompletely understood for wood/epoxy laminate. It appears that epoxy stabilization of moisture levels reduces creep rate and magnitude, but data to verify and quantify this for design are needed. Furthermore, moisture correction for laminate in the 5 to 12 percent operating range is still based primarily on old literature data. A better database would improve life predictions.
-
Promising fiber preforms should be identified and examined under fatigue. Low-cost processability should be taken into consideration.
-
Environmental effects, including ultraviolet exposure, moisture absorption, and temperature fluctuations, should be delineated for the candidate composites and surface coatings.
-
Tough new resins should be examined for their applicability to rotor blades.
REFERENCES AND BIBLIOGRAPHY
Ansell, M. P. 1987. Layman's Guide to Fatigue. The Geoff Pontin Memorial Lecture, sponsored by British Tradewinds. Wind Energy Conversion, ed. by J. M. Galt, Mechanical Engineering Publications Ltd., London.
Ansell, M. P., P. W. Bonfield, and K. T. Tsia. Fatigue Testing of Laminated Wood for Generator Blades. School of Materials Science, University of Bath, England.
Bach, P. W. 1988. High Cycle Fatigue of Glassfiber Reinforced Polyester. Presented at the IEA Workshop on Fatigue in Wind Turbines in Harwell, United Kingdom.
Barrett, J. D. 1974. Effect of Size on Tension Perpendicular to Grain Strength of Douglas-Fir. Wood and Fiber.
Barrett, J. D., and R. O. Foschi. 1978. Duration of Load and Probability of Failure in Wood . Part II. Constant, Ramp, and Cyclic Loadings, Canadian Journal of Civil Engineering, Vol. 5.
Barrett, J. D., R. O. Foschi, and S. P. Fox. 1975. Perpendicular to Grain Strength of Douglas-Fir. Canadian Journal of Civil Engineering, Vol. 2.
Bascom, W. D., J. L. Bitner, R. J. Moulton, and A. R. Siebert. 1980. The Interlaminar Fracture of Organic Matrix, Woven Reinforcement Composites.
Bertelsen, W. D., and M. D. Zuteck. 1991. Investigation of Fatigue Failure Initiation and Propagation in Wind-Turbine-Grade Wood/Epoxy Laminate Containing Several Veneer Joint Styles. U.S. DOE Phase II Report, in preparation.
Bohannan, B. 1966. Effect of Size on Bending Strength of Wood Members. U.S. Forest Service Research Paper, FLP 56, May.
Bonfield, P. W., and M. P. Ansell. Fatigue Testing of Wood Composites for Aerogenerator Rotor Blades. School of Materials Science, Bath University, England.
Bowen, D. H., C. W. A. Maskell, D. C. Phillips, T. W. Thorpe, G. M. Wells, and N. J. M. Wilkins. 1984. Materials Aspects of Large Aerogenerator Blades. Proceedings of the European Wind Energy Conference, Hamburg, West Germany, October 22-26, p. 281.
Bucknail, C. B. 1977. Toughened Plastics. Applied Science Publishers.
Chou, T.-W., R. L. McCullough. and R. B. Pipes. 1986. Composites. Scientific American, Vol. 254, October, p. 193.
Christensen, R. M., and J. A. Rinde. 1979. Transverse Tensile Characteristics of Fiber Composites. Polymer Engineering Science, Vol. 19, 506.
Clark, R. N., F. C. Vosper, R. G. Davis, and W. E. Pinker. 1985. Operational Data From Bushland Wind Turbines. Final Report. U.S. Department of Agriculture (USDA), Agricultural Research Service, USDA Conservation and Production Research Laboratory, Bushland, Texas. Prepared for Electric Power Research Institute, Palo Alto, California.
Composites & Laminates. 1987. Edition 1. D.A.T.A., Inc.
Downing, S. D., and D. F. Socie. 1982. Simple Rainflow Counting Algorithms. International Journal of Fatigue, Vol. 4, p. 31.
Engineered Materials Handbook. 1987. Vol. 1. Composites. ASM International.
Faddoul, J. R. 1981. Test Evaluation of a Laminated Wood Wind Turbine Blade Concept. DOE/NASA/20320-30, NASA TM 81719, May.
Faddoul, J. R. 1983. Examination, Evaluation, and Repair of Laminated Wood Blades After Service on the Mod-0A Wind Turbine. DOE/NASA/20320-53, NASA TM-83483, October.
Garrad, A. D., and U. Hassan. 1986. Dynamic Analysis of Wind Turbines for Fatigue Life Prediction. Presented at the 8th BWEA Meeting in Cambridge, United Kingdom.
Gerhards, C. C. 1977. Effect of Duration and Rate of Loading on Strength of Wood and Wood-Based Materials. USDA Forest Service Research Paper, FLP 283.
Gougeon Brothers, Inc. 1985. Engineered Laminates. Technical Bulletin #1, Bay City, Michigan, April.
Hahn, H. T. 1979. Fatigue Behavior and Life Prediction of Composite Laminates. Composite Materials: Testing and Design (5th Conf.), ASTM STP 674, p. 383.
Han, Y. M., and H. T. Hahn. 1989. Design of Composite Laminates with Ply Failure. Proceedings of the 34th International SAMPE Symposium, p. 529.
Hartness, T. 1988. Thermoplastic Powder Technology for Advanced Composite Systems. Proceedings of the 33rd International SAMPE Symposium, p. 1458.
Hertzberg, R. W., and J. A. Manson. 1980. Fatigue of Engineering Plastics . Academic Press, New York, p. 124.
Hunston, D. 1987. ASTM STP 937.
Hunston, D. 1990. Advanced Materials and Material Forms. Presented at the NRC Workshop on Assessment of Research Needs for Wind Turbine Rotor Materials Technology, Washington, D.C., January 22-23.
Hwang, W. B., and K. S. Han. 1989. Fatigue of Composite Materials - Damage Model and Life Prediction. Composite Materials: Fatigue and Fracture, 2nd Vol., ASTM STP 1012, p. 87.
Johnson, W. S. 1985. Delamination and Debonding of Materials. ASTM STP 876.
Johnston, N. J., and P. M. Hergenrother. 1987. High-Performance Thermoplastics, Proceedings of the 32nd International SAMPE Symposium, SAMPE, p. 1412.
Jones, R. M. 1975. Mechanics of Composite Materials. Scripta Book Co.
Kinloch, A. J., and R. J. Young. 1983. Fracture Behavior of Polymers. Applied Science Publishers.
Kommers, W. J. 1943a. Fatigue Behavior of Wood and Plywood Subjected to Repeated and Reversed Bending Stresses. U.S. Forest Products Laboratory Report No. 1327.
Kommers, W. J. 1943b. The Fatigue Behavior of Douglas-Fir and Sitka Spruce Subjected to Reversed Stresses Superimposed on Steady Stresses. U.S. Forest Products Laboratory Report No. 1327-A.
Lark, R. F., M. Gougeon, G. Thomas, and M. D. Zuteck. 1983. Fabrication of Low-Cost Mod-0A Wood Composite Wind Turbine Blades. DOE/NASA/20320-45, NASA TM-83323, February.
Launikitis, M. B. 1978. Chemically Resistant FRP Resins. Technical Bulletin of Shell Chemical Company.
Lee H., and K. Neville. 1967. Handbook of Epoxy Resins. McGraw-Hill, New York.
Lee, B. L., C. K. Riew, and R. J. Moulton. 1980. Rubber Toughening of Tetrafunctional Epoxy Resin. 12th National SAMPE Technical Conference.
Lee, B. L., F. H. Howard, and E. H. Rowe. 1983. Effect of Matrix Toughening on the Crack Resistance of SMC Under Static Loading. 38th Annual Conference of SPI, Session 9-A.
Lee, S. M. 1986. Compression After Impact of Composites with Toughened Matrices. SAMPE Journal, March/April.
Lubin, G., Ed. 1982. Handbook of Composites. Van Nostrand Reinhold, New York.
Lynch, T. 1989. Thermoplastic/Graphite Fiber Hybrid Fabrics. SAMPE Journal, Vol. 25, p. 17.
Mandell, J. F. 1990. Fatigue Behavior of Glass Fiber Composites. Presented at the NRC Workshop on Assessment of Research Needs for Wind Turbine Rotor Materials Technology, Washington, D.C., January 22-23.
McGarry, F. J., and J. N. Sultan. 1969. Crack Phenomena in Cross-Linked Glassy Polymers. ASTM STP 460, ASTM.
McGarry, F. J., E. H. Rowe, and C. K. Riew. 1978. Improving the crack resistance of BMC and SMC. Polymer Engineering Science, Vol. 18, p. 78.
Modern Power Systems, July, 1986, p. 19.
Morgan, C. A., A. D. Garrad, and U. Hassan. 1989. Measured and Predicted Wind Turbine Loading and Fatigue. Presented at the EWEC Conference in Glasgow, 1989.
Moulton, R. J., and R. Y. Ting. 1981. Effects of Elastomeric Additives on the Mechanical Properties of Epoxy Resins and Composite Systems. International Conference on Composite Structure.
Murtha-Smith, S. 1985. Loads and Fatigue Evaluation of Hamilton Standard WTS-4 Wind Turbine. Proceedings Wind Power '85, San Francisco, August 27-30, p. 136.
Owen, M. J. 1974. Fatigue Damage in Glass Fiber-Reinforced Plastics. In Composite Materials, Vol. 5, ed. by L. J. Broutman, Academic Press, New York.
Phillips, D. C., J. McCarthy, A. G. Davis, and J. E. P. Stott. 1987. The Use of Glass Reinforced Plastics and Advanced Composites for Wind Turbine Blades. A Review of Experience in Their Use and of Relevant Design Procedures and Codes. Department of Energy, United Kingdom, June.
Properties of Epoxy Resins, Hardeners, and Modifiers. 1982. Adhesive Age, April.
Reifsnider, K. L., Ed. 1980. Damage in Composite Materials. ASTM STP 775.
Reifsnider, K. L., E. G. Henneke, W. W. Stinchcomb, and J. C. Duke. 1983. Damage Mechanics and NDE of Composite Laminates. Mechanics of Composite Materials. Recent Advances. Pergamon, New York, p. 399.
Reifsnider, K. L., and W. W. Stinchcomb. 1986. A Critical Model of the Residual Strength and Life of Fatigue-Loaded Composite Coupons. Composite Materials: Fatigue and Fracture, ASTM STP 907, ed. by H. T. Hahn, p. 298.
Riew, C. K., E. H. Rowe, and A. R. Siebert. 1976. Rubber Toughened Thermosets. In Toughness and Brittleness of Plastics, ed. by R. D. Deanin and A. Crugnola, American Chemical Society, Washington D.C.
Rosato, D. V., and C. S. Grove, Jr. 1964. Filament Winding. John Wiley & Sons, New York.
Scott, J. W. and D. C. Phillips. 1975. Carbon Fiber Composites with Rubber Toughened Matrices. Journal of Materials Science. Vol. 10, p. 551.
Sendeckyj, G. P. 1981. Fitting Models to Composite Materials Fatigue Data. Test Methods and Design Allowables for Fibrous Composites, ASTM STP 734, ed. by C. C. Chamis, p. 245.
Spera, D. A., J. B. Esgar, M. Gougeon, and M. D. Zuteck. 1990. Structural Properties of Laminated Douglas Fir/Epoxy Composite Material. NASA Reference Publication 1235, Report No. DOE/NASA/20320-76, May.
Springer, G. S., Ed. 1981. Environmental Effects on Composite Materials. Technomic Publishing Co.
Stoddard, F. S. 1989. Field Problems with Wind Turbine Rotors. Presented at the First Meeting of the NRC Committee on Assessment of Research Needs for Wind Turbine Rotor Materials Technology, Washington, D.C., November.
Strong, A. B. 1989. Fundamentals of Composites Manufacturing. Society of Manufacturing Engineers.
Sutherland, H. J. 1989. Analytical Framework for the LIFE2 Computer Code. Sandia Report SAND 89-1937 UC-905.
Tsai, S. W. 1989. Composites Design, Think Composites.
Tsai, S. W., and H. T. Hahn. 1975. Failure Analysis of Composite Materials. Inelastic Behavior of Composite Materials, ed. by C. T. Herakovich, AMD-Vol. 13, ASME, p. 73.
Van Delft, D. R. V., F. Hagg, and P. A. Joosse. 1987. The Influence of Fatigue Design Line Criteria on the Rotor Blade Design. Wind Energy Conversion 1987, ed. by J. M. Galt, Mechanical Engineering Publications Ltd., London.
Vinson, J. R., Ed. 1977. Advanced Composite Materials--Environmental Effects. ASTM STP 658.
Weibull, W. 1939. A Statistical Theory of the Strength of Material, Royal Swedish Academy of Engineering Sciences, Proc. 151.
Whitehead, R. S. 1990. Damage Tolerance of Composites. Presented at the NRC Workshop on Assessment of Research Needs for Wind Turbine Rotor Materials Technology, Washington, D.C., January 22-23.
Wilkins, N. J. M. 1984. Materials Aspects of Large Aerogenerator Blades . Proceedings of the European Wind Energy Conference. Hamburg, West Germany, October 22-26, p. 281.
Williams, J. G., and M. D. Rhodes. 1981. The Effect of Resin on the Impact Damage Tolerance of Graphite/Epoxy Laminates. NASA TM 83213, October.
Windpower Monthly. 1987. June, p. 10.
Witzler, S. 1988. High-Temperature Thermoplastics: A Progress Report. Advanced Composites, March/April, p. 56.
Wood Handbook. 1974. Wood as an Engineering Material. U.S. Forest Products Laboratory, Agriculture Handbook No. 72.
Yang, J. N., and D. Shanyi. 1983. An Exploratory Study into the Fatigue of Composites Under Spectrum Loading. Journal of Composite Materials, Vol. 17, p. 511.
Zweben, C., H. T. Hahn, and T.-W. Chou. 1989. Mechanical Behavior and Properties of Composite Materials, Vol. 1. Technolmic Publishing Co.