7
AERODYNAMICS
INTRODUCTION
Future progress in aeronautics will be based on the coupling of advanced tools with new understandings of fluid mechanics and interactions between the various aeronautical disciplines. New interdisciplinary computational tools and new experimental capabilities will play increasingly important roles in aeronautical technology progress. These new methods will profoundly affect the cost and speed of aircraft design processes as well as the efficiency and utility of future aircraft. This vision for the future of U.S. aeronautical technology can be realized only through investment in computational and experimental infrastructure and in the development and precompetitive validation of selected technologies. For the United States to compete more effectively in technology development in the future, science and engineering efforts that support industry must be reinvigorated. This reinvigoration will require an increased level of investment as well as careful assessment of investment strategy. A strong need exists to strengthen the weakest link in the technology development chain: namely, technology validation for risk minimization.
In recent years, the National Aeronautics and Space Administration (NASA) has recognized the importance of technology development needs for high-speed civil transports (HSCTs), advanced subsonic transports, and hypersonic vehicles of all types, as well as the need to maintain its facility capabilities through the Wind Tunnel Revitalization Program. In each of these areas, however, overall constraints have limited NASA's ability to establish the kind of aggressive research efforts needed to maintain U.S. competitiveness in aeronautics. This chapter charts a course for NASA, industry, and academia to pursue toward the specific aerodynamics goals needed to achieve competitiveness. The boxed material summarizes the primary recommendations that appear throughout the chapter, with specific recommendations given in order of priority, and the benefits that can be gained through aerodynamics research and development.
Although discussion of individual technical disciplines is facilitated by categorization, progress in technical fields is enhanced by an interdisciplinary approach rather than by the more traditional sequential application of various technical skills. In the past, the disciplines of
Recommendations General NASA must continue to provide the necessary resources for aerodynamics research and validation, including resources focused on specific key technologies, resources to maintain and enhance ground and flight test facilities, and resources for enhanced analytical and design capabilities. Specific The following research topics should serve as the focus of NASA's research effort in aerodynamics:
The following should be the focus of a program to enhance NASA's ground-based experimental facilities:
The following should be the focus of a program to enhance NASA's experimental flight facilities:
|
aerodynamics, structures, and controls were largely exercised sequentially in the design process. Propulsion system analysis proceeded independently and was integrated later into the design. Such a process requires several cycles of iteration to converge on a suitable design, and
Benefits of Research and Technology Development in Aerodynamics Aircraft Operations Reduced fuel consumption Decreased cruise drag Increased climb and descent lift-to-drag ratios Reduced takeoff and landing noise Aircraft Design and Development Shortened development cycle Improved computational capabilities Improved testing facilities Technology validation |
consumed considerable time and money. Also, not only does this procedure not guarantee an optimum configuration satisfying multiple design constraints, it almost precludes such a configuration because the efforts devoted to the initial steps in the design process become progressively harder to change. In some cases, cost and time constraints preclude more than one or two iterations.
The increasing maturity of computational approaches in the various design disciplines provides new opportunities to couple the disciplines more tightly earlier in the design process. Routinely treating aerodynamics, structures, propulsion, and controls virtually simultaneously and continuously throughout each step of design has very large payoffs that fall into several categories. First of all, the resulting design is truly optimized and is, therefore, superior to those derived through the older, sequential approach. A second major payoff is a significant reduction in the time required to evolve a final design. Attainment of this goal is critical to the success of the transport aircraft industry.
NASA has recognized the potential advantages of multidisciplinary analyses and plans to focus considerable attention on this in the Computational Aerosciences portion of the national High Performance Computing and Communications program, which was initiated in fiscal year 1991. The goal for the 1990s is to develop the capability to computationally couple aerodynamics, structural response, propulsion system effects, and active controls into a single computation and to structure the resulting codes to take advantage of massively parallel computational system architectures that are expected to be in widespread use after the mid-1990s.
These NASA efforts are highly endorsed by the Committee and complement similar industry activities that will include manufacturing considerations in the trade-off decision-making process. The impact of rapid design processes that allow time for examining the trade-offs between various disciplines was evident in the design of the folding wing tip of the Boeing 777.
Three configuration options were examined: an external hinge, an internal hinge retaining the original wing surface contours, and an internal hinge with a local thickening of the wing. An early wind tunnel test provided some baseline aerodynamic information, but the subsequent design iterations and final design decisions were made rapidly by using computational fluid dynamics (CFD). A final verification wind tunnel test could be performed only after the design was frozen.
This use of computational aids is being extended into multidisciplinary analyses coupling aeroelastic effects with structural analyses. The use of CFD for preliminary aerodynamic load predictions early in an airplane development program will significantly shorten the development cycle. Use of CFD to permit flutter prediction early in the design process will reduce reliance on traditional after-the-fact remedies such as mass balancing.
Early in this study the Committee decided not to address the hypersonic flight regime and to set the upper limit of vehicle speeds to encompass the HSCT. This section of the report, therefore, does not address the aerodynamics of hypersonic flight. Before moving to the areas considered, however, some comments on the state of hypersonic research in the United States are appropriate.
Current U.S. capabilities in hypersonic research have their roots in research efforts that were concluded more than 20 years ago with the culmination of the X-15 program. Today, the nation's hypersonic capability is largely applied to the National Aerospace Plane (NASP) program, which is focused on the specific objective of the technologies necessary to design and build the X-30 aerospace plane capable of single stage to orbit. As a consequence, few resources are available for generic hypersonic research that does not support NASP.
The key aerodynamics technologies have been divided into the following categories, each of which is discussed in corresponding sections of this chapter:
-
Low speed and high lift for subsonic configurations: This portion of the chapter examines the approach and takeoff flight phases for subsonic aircraft, encompassing high lift system performance in detail and overall takeoff and landing performance in general. Noise is included because this is the flight phase in which it is most troublesome.
-
Subsonic aircraft propulsion/airframe integration: Aerodynamic interaction effects between a subsonic airframe and its propulsion system has significant effects on the economics of aircraft cruise performance. In addition, the integration must also recognize the need for low noise emission during takeoff and landing.
-
Aerodynamic cruise performance: Efforts to maximize lift-to-drag ratio (L/D) and minimize cruise drag are critical to the economic success of most commercial aircraft. Lower drag relates directly to lower fuel costs and higher profits for the air carrier.
-
Low speed and high lift for supersonic configurations: Supersonic aircraft shapes are strongly influenced by the need for economical supersonic cruise performance. Virtually all the design decisions to improve performance in this
-
flight phase have deleterious effects on the approach and takeoff flight performance. The requirements for improving the technology base for the design of supersonic aircraft are discussed in this section.
-
Supersonic aircraft propulsion/airframe integration: The integration of the propulsion system with the airframe is a very important factor for all categories of aircraft. For supersonic designs in particular, aerodynamic interaction between the airframe and the propulsion system is a critical task, made more difficult by the need to minimize takeoff engine noise.
-
Aerodynamics of rotorcraft: Aerodynamics of rotorcraft and tiltwing aircraft are especially complex, because they require investigations of exceptionally wide speed ranges and varying angles of airflow.
-
Test facilities: The numerous new or updated flight and ground test facilities that will be required to accomplish various technical goals set forth in the report are discussed in this section. The use of computational tools and associated computers that can predict complex flow fields around aircraft in all speed ranges is also of growing importance. Specific applications of CFD are discussed in detail in the preceding categories, but this section of the chapter contains a more general summary.
A generally recognized and acceptable measure of aerodynamic efficiency is the lift-to-drag ratio. Table 7-1, prepared by the McDonnell Douglas Aircraft Company, lists subsonic L/D improvements achievable for the time period of this study if the recommendations in this chapter are implemented.
TABLE 7-1 Potential L/D Improvements
Application |
Potential L/D Increase |
Aspect ratio increase (11–17.5%) |
15% |
Laminar flow control (upper wing/tail surface) |
10–12% |
Airfoil development |
2–3% |
Turbulence control (fuselage/lower wing) |
2–3% |
Induced drag |
3–4% |
Total |
~35% |
Source: McDonnell Douglas Aircraft Company |
LOW SPEED AND HIGH LIFT FOR SUBSONIC CONFIGURATIONS
The efficiency and effectiveness of the low-speed, high-lift systems employed by subsonic jet transports for takeoff and landing have a major impact on overall economic performance. The need is to develop design technology that will produce high-lift systems that provide high L/D in climb-out, high lift coefficient during landing approach, acceptable performance in icing conditions, and acceptable levels of airframe noise, and that are also amendable to low-cost manufacture and maintenance.
The payoff from continued improvements in high-lift systems is large. For an airplane the size of the forthcoming Boeing 777, a small increase in lift coefficient, 0.10, at a fixed angle of attack of 8.0 degrees, allows a 14.0-inch reduction in landing gear length and a 1,400-pound reduction in empty weight. A 0.035 (approximately 1 percent) improvement in maximum lift coefficient equates to a 1-knot change in approach speed, a 6,600-pound increase in payload (at constant approach speed), or a 60-foot reduction in landing distance. Simplifying the geometry of the flap system while maintaining aerodynamic performance yields large benefits in terms of cost and maintainability. One of the stated goals for subsonic transport design is the reduction of acquisition and maintenance costs by 25 percent relative to current production airplanes. Future advances in high-lift system technology can contribute significantly to the achievement of this goal.
Because of the complex physics and complex geometries associated with low-speed flight, CFD has not had a major impact on the technology of high-lift system design. The primary design tool has remained the wind tunnel, with some design guidance from CFD. Work over the past decade has verified the strong influence of Reynolds number on aerodynamic performance of high-lift systems—aerodynamic performance of high-lift systems in many cases does not scale predictably with Reynolds number. Figure 7-1 shows the experimentally measured maximum lift coefficient of a simple swept wing over a range of Reynolds numbers, which displays large and unpredictable variations in maximum lift with Reynolds number. Such experiments demonstrate that the best aerodynamic performance and lowest risk can be achieved only by carrying out the aerodynamic design and validation at flight Reynolds numbers. Because of this, airframe companies do their development work in high Reynolds number wind tunnels—which, for the design of the new Boeing 777, meant extensive development work in European wind tunnels.
The following developments in the technology for advanced high-lift system designs are needed:
-
Improved understanding and measurement of the detailed flow physics at wind tunnel and flight Reynolds numbers: A better understanding is needed of turbulence and its modeling; of boundary layer transition, laminar bubbles, turbulent reattachment and relaminarization phenomena; and of merging boundary layers and wakes, including the detailed behavior of the viscous layers and wakes in the high adverse pressure gradient region above the training edge flaps. Some progress is being made in the United States in this area of research. In contrast, the Europeans have greatly exceeded U.S. technology in high-lift systems,
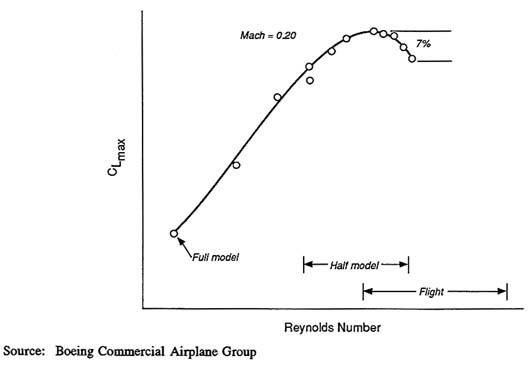
FIGURE 7-1 Variation of CLmax with Reynolds number for a simple swept wing.
-
principally through their concerted efforts over several years to understand the detailed flow physics associated with high lift. For the United States to compete in this area, greater investment is needed in the experimental capabilities and flow physics studies that lead to breakthroughs in high-lift capabilities.
-
Improved CFD: The challenge is formidable in view of the complex physics, complex geometries, and numerous length scales that must be resolved numerically. Pacing items are the flow models (modeling of turbulence, transition, bubbles and reattachment, merging sheer layers, and relaminarization); the sheer size of the computational problem, including proper numerical resolution of all the important length scales of the physics; and code validation, particularly at flight Reynolds numbers where few data exists. What is needed is a CFD development program that is closely coordinated with other key elements of flow physics and high Reynolds numbers testing, and which is constrained to be economically viable and run able in a timely manner when hosted on today's computers. Although the United States leads in certain respects in CFD, at current investment levels, U.S. research efforts will not provide for the experimental validation of CFD capabilities necessary to maintain this lead. The need for such validation has been recognized for some time as critical to the maturation of such computational capabilities for ultimate use in design method applications.
-
Experimental research and developmental testing at the highest achievable Reynolds numbers: There is a major need for a low-speed, low-disturbance testing facility in the United States, one that produces the highest reasonable Reynolds numbers at the right Mach numbers and closely simulates the freestream environment of flight with levels of productivity that are needed to support developmental testing. It is no longer acceptable to develop a candidate design at low Reynolds numbers and validate it at high Reynolds numbers. There is also a strong need for obtaining aerodynamics measurements at flight Reynolds numbers on full-scale flight vehicles. Nonintrusive, highly accurate, and responsive instrumentation is urgently needed to make detailed measurements of various flow conditions on and away from the surfaces of a test article. The current level of U.S. high-lift research efforts will not provide the advanced measurement technologies needed for rapid, competitive progress in this research area. In 1989, NASA developed a broad plan for research in advanced aeronautics measurement technology; unfortunately, the plan was never implemented. In comparison, the European competitors, in their BRITE EURAM program, have committed to significant levels of investment in measurement technology.
Other phenomena associated with high-lift systems are airframe noise and wake vortex prediction and alleviation. Continuing advances in engine noise reduction will mean that the airframe is responsible for a growing portion of the overall noise profile of an airplane. Reducing airframe noise requires an understanding of the detailed sources and mechanisms of its production. The design challenge is to develop solutions that reduce airframe noise but retain high-lift aerodynamic performance.
Airplanes that meet the Federal Aviation Regulation (FAR-36) Stage 3 noise limits have provided substantial noise reductions relative to older airplanes. Nevertheless, many airports impose additional noise restrictions that penalize payload or range by requiring operations at reduced takeoff weight or that prohibit night operations. It is clear that pressure to further reduce noise will continue to increase.
To advance the state of the art to significantly reduce noise, concerted and continuing research and development efforts are required. NASA should lead the basic research to substantially improve the sophistication and technical strength of noise analysis/design computational tools. The agency should also lead the development of novel noise reduction concepts. The Committee recommends that NASA:
-
conduct and sponsor fundamental research to understand and reduce high-speed jet and turbomachinery noise;
-
conduct and sponsor fundamental research to understand human response to noise and vibration in aircraft cabins, flight decks, and crew rest areas;
-
develop the technology for predicting and measuring long-range ground-to-ground and in flight-to-ground sound propagation for airport and en route noise assessment;
-
develop technology for the prediction and control of vibroacoustic responses of aircraft structures and materials;
-
develop prediction and suppression technology for near- and far-field noise;
-
develop experimental techniques and facilities to permit acquisition of accurate acoustic, aerodynamic/structural dynamic, and psychoacoustic data in support of aircraft acoustic technology development; and
-
develop signal processing technology to improve analysis and utilization of data from acoustic wind tunnel testing.
Unless the United States mounts concerted efforts to augment the development of advanced computational and experimental capabilities, it will not be possible to achieve technology parity with similar European efforts. In particular, U.S. acoustic research facilities are not as capable as those in Europe (particularly DNW in The Netherlands). In the absence of these acoustic research facility capabilities in the United States, our industry and government research and development efforts typically utilize foreign facilities. In order to compete, it is necessary for the United States to support the development of appropriate facilities.
Many airports around the world are reaching capacity operations, limited in part by wake vortex separation requirements on landing and takeoff. Continued growth of the air transport system will require increases in airport capacities. Finding ways to reduce airplane separation requirements would contribute to that goal. Studies of wake vortices, prediction methods, means of vortex detection and avoidance, and means for promoting rapid dissipation of wake vortices should be continued and expanded. Wake vortex research program plans have been developed jointly by NASA and the Federal Aviation Administration (FAA). Unfortunately, work has not begun on carrying out this plan.
NASA should play a leading role in the development of the enabling technologies in these areas. There should be a combined program of flow physics and CFD, which together will increase understanding of the complex flow physics and impart an ability to predict and compute such flows. Comprehensive programs that address the issues and opportunities in noise research, wake vortices, and airplane separation requirements are needed. NASA is the appropriate organization to develop the technology and means for testing at the highest Reynolds numbers, which includes advanced flow diagnostic instrumentation development, innovative wind tunnel circuit components, the possible use of heavy gas, moderate cryogenics, and other options for high Reynolds numbers, half-model testing techniques, and wind tunnel wall interference minimization.
The resources required in particular for the development of a very high Reynolds number wind tunnel are large, but investment for that purpose is essential if the U.S. competitive edge is not to be further eroded.
Investments by NASA in the technology areas described above will benefit all segments of the industry, not just large commercial transports. Commuter and short-haul aircraft will benefit from advances in the enabling technologies of flow physics, CFD, and experimental research.
SUBSONIC AIRCRAFT PROPULSION/AIRFRAME INTEGRATION
The technology of integrating propulsion systems and airframes involves the ability to assess and control the development of wave drag, induced drag, and profile drag. Advances in CFD over the past decade have contributed greatly to this technology. It is anticipated that ongoing CFD developments will lead to even further refinements.
Two areas remain in which technology improvements are needed. One is the development of wind tunnel test techniques and powered propulsion simulators to better represent installed power effects of the forthcoming generations of very high bypass ratio engines in wind tunnel testing. The other is the need to predict the installed characteristics of thrust reversers, both computationally and with wind tunnel testing techniques. These are areas in which NASA can make important contributions.
AERODYNAMIC CRUISE PERFORMANCE
Although the fundamental physical principles of subsonic and supersonic airflow around aircraft are the same, design approaches to minimizing drag are greatly affected by the cruise speed. This section of the report discusses cruise performance in the two speed ranges separately.
Subsonic Aircraft Cruise Performance
Long-haul subsonic transports are now, and will be for the foreseeable future, the major product of the civilian aviation industry and infrastructure. As noted in Chapter 2, from 1975 to 1995, aerodynamic efficiency will have increased by approximately 10 percent, and if the current rate of improvement is maintained, another 5–10 percent is projected by the year 2020. However, ordinary development or evolution alone will not keep the United States at the forefront in the world market. Although continued evolutionary advances in methods and processes (experimental, theoretical, and computational) are needed to provide continued improvement of aerodynamic design technologies, demonstrated innovative technologies are necessary in the longer term to provide opportunities for significant improvements in performance
Laminar Flow Control
The flow on most of the surfaces of an aircraft is turbulent. Laminar flow control (LFC), hybrid laminar flow control, and natural laminar flow are promising sources of skin-friction drag reduction on aerodynamic surfaces. Laminar flow nacelles are also being studied by NASA. Laminar/turbulent transition of the airflow next to the aircraft surface is delayed through a combination of pressure gradient tailoring of the wing and control such as suction through the skin. If full-chord laminar flow can be maintained in this fashion, fuel savings of up to 25 percent could be realized.
Transition is extremely sensitive to freestream conditions (e.g., freestream turbulence and acoustics) and surface roughness (e.g., rain and ice crystals, insect debris, surface finish, and fasteners); lack of confidence in these issues has hindered the use of this concept on vehicles. Also, of perhaps greater significance have been the questions of fabrication cost and operational cost and maintainability.
Engineering and optimization tools have outpaced the state of the art in transition prediction theory.1 Thus, the design of LFC, hybrid laminar flow control, and natural laminar flow systems depends on empirical bases to determine transition. This method is also limited because it cannot account for the effects of surface roughness and freestream disturbances.
Knowledge of transition—so very important to the success of LFC techniques—is, in general, limited to the simplest of geometries. Efforts to better understand the transition flow physics are under way to provide valuable guidance for the surface roughness and freestream disturbance problems.
Only a limited number of flight tests have been flown since the original and successful X-21 program of the 1960s;2 these are the JetStar (NASA/Langley) and Boeing 757 (NASA/Boeing). In both cases, extensive laminar flow was successfully achieved on the upper surface of the swept wing through the use of suction. Very low suction levels were required, with power penalties of the order of 1 percent. Studies with engine noise indicated no effect. The use of a Krueger nose flap eliminated a potential buildup of insect debris on the leading edge.
The remaining challenges to the implementation of laminar flow technology in large subsonic transport designs include validation of the technology in actual airline service operating environments and exploration of the technical issues associated with making laminar flow operate effectively on the inboard portion of the wings of very large aircraft. Recognizing the challenges, during 1990 NASA and the industry developed a cooperative research plan; however, these efforts have been delayed by overall program constraints. Meanwhile, the Europeans have rapidly advanced their laminar flow efforts. Airbus plans for laminar flow technology validation include extensive large-scale testing, targeting technology validation as early as 1993.
Turbulent Drag Reduction
The most promising technique demonstrated thus far has been passive control by riblets, tiny streamwise grooves on the aircraft surface. This device is useful for surfaces on which laminar flow is very difficult to achieve (e.g., the fuselage). The approach was used
successfully on the U.S. entry in an America's Cup Race and then flight-tested on a portion of a business jet,3 achieving a reduction in local skin-friction drag of 8 percent.
The state of the art in turbulence predictions depends on empirical correlations and models, usually developed for one set of flow conditions or a very simplified model. Here also, efforts at understanding the basic physics of turbulent flow are under way. Prediction and control have been hindered by the lack of reliable, efficient models of turbulence for complex geometries.
Advanced Supercritical Airfoils
Advanced supercritical airfoils, which reduce the shock strength on transonic airfoils, have contributed to drag reduction and have been used on all commercial transport aircraft developed since 1975. Further modifications4 with reduced moments and weaker shock waves are under study by NASA for use with LFC systems.
Improved understanding of shock/boundary-layer interactions has led to new opportunities to greatly improve airfoil design concepts and procedures.
Wing Design
The improvement of theoretical analysis tools and CFD, coupled with a better understanding of flow physics, has enabled the design of more aerodynamically efficient wings with greater thickness and reduced sweep. This allows a wing weight reduction or higher aspect ratio. Substantial improvements in cruise Mach number and critical Mach number have also been realized. New opportunities exist to significantly improve the design optimization procedures for wings that incorporate laminar flow systems along with advanced high-lift systems.
Winglets
Winglets, or wingtip extensions, which first appeared on business jets, are now used on various versions of commercial transports (e.g., the Boeing 747-400 and MD-11). These effectively increase the aspect ratio of the wing. Advancements in understanding of the ''nonlinear'' effects of wing-wake deflection and roll-up have created opportunities to improve the design optimization procedures for winglets and other wingtip devices for drag reduction. In each of these technology topics, significant opportunities have developed to advance the state of the art; however, constraints on the aeronautics program have limited NASA's ability to
support the needed advancements in experimental or computational capabilities and in ground and flight validation of these technologies.
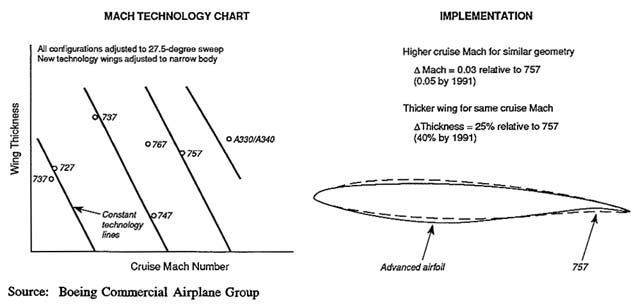
FIGURE 7-2 Improvements in transonic wing technology.
Status of Subsonic Technology
As noted earlier, the past decade has seen large improvements in wing design technology, the successful demonstration of laminar flow control on a Boeing 757, the successful demonstration of riblets on a business jet, the successful demonstration of natural laminar flow on a business jet, and the use of supercritical airfoils and winglets on transports in everyday commercial service.
Advances in computer and quiet-tunnel/instrumentation capabilities have allowed details of the fundamental flow physics of transition and turbulence to be studied. Computational time for these efforts, however, is too long for extensive use in the design process at present.
NASA should play a leading, but not exclusive, role in the development of enabling technologies. There should be a cooperative effort among NASA, industry, and academia to research complicated flow physics with the goal of predicting, modeling, and controlling such flows. Research should combine theory, careful experiments, and CFD; duplication of the
results by another technique or in another facility, as recommended by the U.S. Transition Study Group, is also desirable. NASA is an appropriate organization to encourage flight testing of enabling technologies and the development of advanced diagnostic instrumentation for nonintrusive testing. NASA is also an appropriate organization to provide high Reynolds number, quiet testing opportunities, as well as the most current computational facilities and techniques.
To implement the above concepts, a better understanding of flow physics is required. Intensified efforts to develop useful, accurate engineering models that can be used for design are particularly necessary. This work, although seemingly basic in nature, must be actively pursued and must include companion theoretical, computational, and experimental efforts conducted under careful, well-documented conditions. A better understanding of flow physics will also afford the opportunity for effective use of flow control. Issues to be addressed should include implementation, reliability, and maintenance of the mechanical systems, as well as implications of the loss of the system in flight. Continuing advances in CFD, as well as high Reynolds number, low-disturbance experimental capabilities, are also needed in support of the evaluation and design of these concepts.
NASA needs the following resources to accomplish the foregoing:
-
high Reynolds number facilities (simulate flight)
-
low-disturbance freestream facilities (simulate flight)
-
full-scale Reynolds number flight research capability,
-
nonintrusive instrumentation,
-
faster and bigger computers for flow physics (model development),
-
more efficient CFD, faster algorithms and grid setups,
-
companion theory/computation/experiment efforts (validation and guidance), and
-
NASA/industry/university cooperation on approximately equal levels. NASA's role in the university training of future engineers through research funding must never be overlooked.
The Europeans are using much of the technology described above—particularly LFC—even though by U.S. standards the technology is often untested or unproven. On an overall technical basis, current European offerings are equal to those of the United States. However, because Europeans are incorporating the technology faster than the United States is, their rate of improvement is significantly greater. In particular, within the BRITE EURAM consortium involving government, industry, and academia in Europe, a highly organized effort has been developed to advance the state of the art for laminar flow engineering design capabilities. Their efforts combine the best talent and facilities in all of Europe to develop and validate transition prediction tools for integration with industry engineering design methods. (BRITE EURAM efforts address all other aeronautical disciplines as well.) Although progress is being made in the United States on understanding boundary-layer transition physics, no similar design-tool-focused effort is being funded here. The problem in this country is not lack of opportunities, but rather the lack of priorities on resources.
Supersonic Aircraft Cruise Performance
U.S. expertise in supersonic aircraft performance stems from the earlier Supersonic Transport (SST) program, the ongoing Phase I High-Speed Research Program, and various high-speed fighters. In cruise, the recognized promising technologies for the HSCT are the same as for the subsonic case: hybrid laminar flow control by suction and pressure gradient. Unlike the subsonic speed regime, this technology has not been demonstrated in flight. The benefits of lower drag (as described in subsonics) and thermal requirements associated with laminar flow can be realized in this flight range as well. In addition, technology advances in the fundamental understanding of high Reynolds number effects on leading-edge vortex formation and the ability to eliminate unacceptable characteristics, such as low speed pitch-up, could allow the utilization of highly swept, high-performance wing planforms. This would provide substantial increases in cruise lift-to-drag ratios over the currently favored planform concepts.
Laminar Flow Control
At present, our knowledge of high-speed transition is even less developed than our knowledge of subsonic flows; designs depend on existing theories that are not compatible with design and optimization tools (as described in subsonics). In the supersonic range, however, the effects of freestream conditions (e.g., freestream turbulence and noise) and surface roughness may be more severe than in subsonic flows. Efforts are under way to understand and predict the transition behavior in supersonic flight. The exciting progress that has been made in subsonic laminar flow technology required nearly four decades of concentrated, if not continuous, effort. Although some of the subsonic lessons learned may apply to supersonic laminar flow challenges, it would be overly optimistic to expect supersonic laminar flow technology to mature after a few years of effort. The United States should prepare for a long-term commitment to supersonic laminar technology development in order to lead in this area. Currently, U.S. research and development resources in this area, while not inconsequential, will not support a long-term effort to achieve technology maturation and validation.
The single low-disturbance, supersonic, experimental facility available for this basic work in the United States is the Mach 3.5 Quiet Tunnel at NASA/Langley,5 which is just beginning to contribute invaluable information. Large-scale, low-disturbance, supersonic wind tunnels are needed to support aircraft development. The existing infrastructure of government facilities and capabilities that support the U.S. subsonic airframe industry was built up over many years. If this nation is to compete successfully in a future class of supersonic aircraft, investment in the facility infrastructure must begin soon. These investment requirements are relatively large because of the unique facility needs and the needs for flight capabilities.
Turbulence Models
The art of turbulence modeling is very young and depends on very limited experimental data (often at low temperature). Here also, efforts at understanding the basic physics of turbulent flow are under way. CFD is being used for flow physics studies.
Sonic Boom
It is very unlikely that the HSCT would ever be allowed to fly supersonically over land if the problem of sonic boom is not resolved. Efforts are under way to tailor the shape of the airplane so as to modify the sonic boom to acceptable levels, although with some degradation of performance. The economics and performance of a combination of operational modes for missions over land and over water, including subsonic/supersonic, low/high supersonic modes, and different single supersonic cruise Mach numbers, are being analyzed.
Subsonic Cruise
If a vehicle must also fly subsonically over land, the configuration designed to best utilize supersonic LFC may not perform well at lower speeds. Here, again, trade-offs are needed between supersonic and subsonic flight design to optimize overall economy and performance.
Status of Supersonic Technology
A major step in the last decade has been the successful correlation of transition prediction theory with experimental results in the NASA/Langley Mach 3.5 Quiet Tunnel. This has established the standard for future supersonic and hypersonic facilities as well. It is strongly recommended that all future facilities have the same features for noise control as the Mach 3.5 Quiet Tunnel.
To demonstrate LFC design methodologies and develop 50–60 percent chord laminar flow, plans are under way for an F-16 XL flight test at Mach 2. These efforts to validate existing ground facilities and methodologies with actual flight are important. Plans are under way at NASA/Langley for the development and fabrication of a series of low-disturbance facilities at various Mach numbers.
The biggest challenge is to achieve good overall cruise economics with acceptable community noise and emissions levels.
The challenges for L/D enhancement include LFC, turbulent drag reduction, reduction of drag due to lift, volume wave drag reduction, and the development of design optimization methods. The following ideas appear promising, but studies in the past have proved inconclusive:
-
improvement of conventional shapes;
-
flying yawed wing (Mach number 1.6);6
-
extreme arrow wing, strut bracing, multiple bodies, extensive LFC; 7 and
-
enhanced favorable wave interaction (e.g., optimized parasol wing, multiple bodies).
More speculative approaches for supersonic drag reduction include:
-
increased lift from upper surface via flow separation control (reduced sonic boom?); increased leading-edge thrust; increased fuselage lift/camber and reduced wave drag due to lift; control of shock/boundary-layer interactions (e.g., by passive porous walls); improved isentropic compression surfaces/inlets;
-
multistage aircraft (e.g., separate subsonic takeoff and landing carrier);
-
thrust vectoring for lift augmentation;
-
mission-adaptive wings (subsonic/supersonic);
-
application of conventional takeoff and landing aircraft vortex drag due to lift reduction approaches (other than aspect ratio); and
-
engine exhaust flow tailoring for partial shock reflection/favorable interference wave drag reduction.
To implement the above concepts, a better understanding of flow physics is required. Only in this way can useful, accurate engineering models be developed for design. This work, although seemingly basic in nature, must be actively pursued and must include companion theoretical, computational, and experimental efforts conducted under careful, well-documented conditions.
Continuing advances in CFD, as well as large-scale, low-disturbance experimental capabilities, are also needed in support of the evaluation and design of these concepts.
LOW SPEED AND HIGH LIFT FOR SUPERSONIC CONFIGURATIONS
High-speed configurations present a particular challenge for takeoff and landing performance as a result of the usually high wing sweep and slender designs required for supersonic performance. Supersonic aircraft must be designed to operate from existing international airport surfaces; therefore, operation for an 11,000-foot runway at maximum takeoff weight is a requirement. High-lift capability significantly affects the approach speed, field length, and time to climb—which in turn, affect the noise footprint. FAR 36 measurement locations are illustrated in Figure 7-3. Aerodynamic L/D improvements for takeoff reduce community noise levels by reducing climb-out time or permitting reduced thrust levels. Landing
requirements include high-lift generation at high drag while maintaining pilot visibility for approach. In addition, slender configurations usually require stability and control features to delay the pitch-up tendencies and to increase lateral control effectiveness. In addition, high-lift devices must work in harmony with other advanced concepts such as supersonic laminar flow control that are beneficial to supersonic cruise efficiency. These requirements result in ample opportunity for innovative and aggressive aerodynamic development.
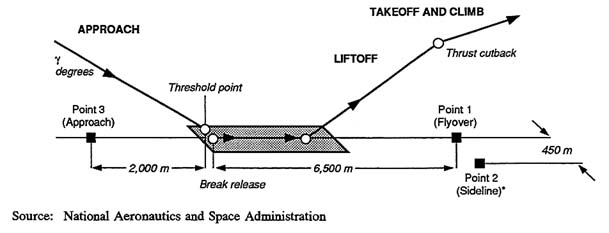
FIGURE 7-3 FAR 36 measurement locations.
First-generation supersonic transports, such as the Concorde and Tupolev 144, do not meet current environmental requirements at most locations. The Concorde relies on vortex lift at a large angle of attack to achieve its lift for takeoff and landing. The result is a very high-drag situation with strong trailing vortices and landing visibility that must be augmented by a hinged nose section. There is significant room for improvement in developing low-speed, high-lift operation and control. Since the configurations are slender, much of the flow is separated at high-lift conditions. There has been significant progress over the last decade in finding new ways to avoid separation, as well as to take advantage of separated flows by controlling the vortices and positioning them to achieve maximum benefits. Vortex flaps have been used to significantly improve the lift-to-drag ratio and maintain a larger extent of attached flow. A lower noise footprint may be achieved for climb-out improving the climb-out angle. The effect of lift-to-drag ratio on climb-out noise footprint is illustrated in Figure 7-4. Because of the very large levels of noise suppression required, HSCT noise suppression devices installed on engine or airframe are quite heavy. Increasing high-lift system performance also entails significant weight increases. NASA should intensify its efforts to develop more efficient HSCT high-lift system devices having minimum weight increments; such devices could provide very significant economic benefits to an HSCT vehicle.
Technology challenges for the future revolve around ways to find the low-noise, high-L/D solution to the takeoff problem. Vortex control becomes an important way to achieve these results by enhancing leading-edge suction and maximizing the attached flow in the wing
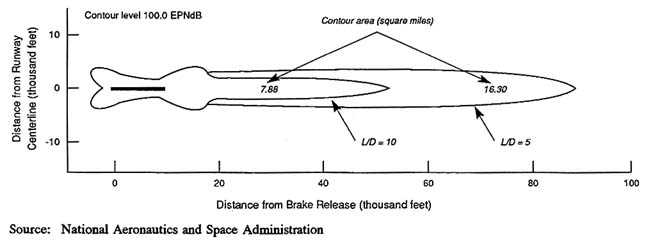
FIGURE 7-4 Takeoff noise contours.
at high angles of attack, thus improving the effectiveness of the wing.
CFD can provide a useful tool in dealing with the separated and vertical flows. However, since Reynolds number dependency may be significant, complete validation of CFD must be accomplished before design application can be made. The Reynolds number uncertainties lead to a need for high Reynolds number facilities that can provide large-scale testing of the supersonic configurations at low speeds. Blending of propulsion systems by vectoring or directing bleed air may be useful in finding an optimal solution to the overall control and lift drag balance for the aircraft. Because supersonic laminar flow control may play an important part in the supersonic cruise efficiency of high-speed vehicles, careful attention must be paid to the interrelationships of the high-lift system and the suction system used for laminar flow control.
SUPERSONIC AIRCRAFT PROPULSION/AIRFRAME INTEGRATION
With increasing cruise flight speeds, the achievement of close aerodynamic coupling between the propulsion system and the airframe becomes more and more important. One seeks favorable aerodynamic interference between the two systems so as to minimize overall drag and optimize engine performance. NASA has conducted extensive interference tests involving variations in Mach number, angle of attack, nacelle position, and nacelle mass flow on configurations from isolated nacelles to wing-body-nacelles up to Mach number 1.4. These tests showed considerable interference drag near sonic speed and also showed that interference effects were dependent on angle-of-attack and mass flow variations. NASA is presently extending these tests to a Mach number of 2.5.
The development of an HSCT will require a large effort in integrating engine and airframe and in minimizing engine noise. This area is also receiving much attention in Europe for large commuters as well as a second-generation supersonic transport. European expenditures on propulsion/airframe integration are rapidly growing.
Inlets
Inlets of air-breathing engines for supersonic aircraft up to Mach 3.5 can presently be designed to provide high pressure recovery and minimum inlet flow distortion and drag.8 This capability demands close coupling of the inlet with the forebody of the fuselage or the wing. The latter is designed to provide effective initial compression and reasonable uniformity of the incoming air flow. To achieve this condition, the design includes a bleed to prevent the retarded flow of the fuselage forebody or wing boundary layer from being ingested in the inlet. Engines for supersonic aircraft should also be designed with variable geometry inlets to reduce sensitivity to flight conditions and, in particular, to enable efficient operation at takeoff and landing, as well as in cruise flight. Such inlets will require sophisticated boundary-layer control systems. It is expected that such variable geometry inlets can be developed to operate efficiently from subsonic speeds up to Mach 6.
Nozzles
The data base for axisymmetric nozzles is substantial, and the data base for nonaxisymmetric nozzles of the two-dimensional type of moderate aspect ratios is increasing. In the design of high-performance nozzles, emphasis has been placed on achieving a reduction in transonic drag and a reduction in the complexity of the system.
Future efforts need to focus on development of multifunctional nozzles with reduced drag levels over a wide range of Mach numbers, providing significant increases in cruise performance at supersonic speeds. These efforts will be greatly enhanced by the availability of powerful new numerical techniques.
Consideration also needs to be given to the potential of vectored thrust for both cruise and maneuvering operations.
Noise
For supersonic aircraft, reducing engine noise generated by the very high jet velocities requires major efforts. The Concorde, which represents the current state of the art for SSTs, generates noise that is approximately 20 EPNdB9 higher than Stage 3 subsonic airplanes of the
same takeoff weight. To be fully acceptable for commercial use, future supersonic transports will have to be designed to the same noise limits as subsonic airplanes. These results present an extraordinary challenge currently being addressed by industry and NASA. Such schemes as ejector-suppressor nozzles will help reduce the main contributors to jet noise, which are turbulent mixing and shock cell noise.10 Very little is known about airframe noise of the delta wing planform of supersonic airplanes.
AERODYNAMIC ASPECTS OF CONVENTIONAL TAKEOFF AND LANDING FLIGHT DYNAMICS
Advances in the prediction of flight dynamics characteristics of conventional takeoff and landing aircraft have not kept up with advances in other fields of aerodynamics. The following two sections discuss problems that must be addressed for subsonic and supersonic conventional takeoff and landing aircraft.
Subsonic Aircraft
Stability and control testing is addressed early in flight test of a new aircraft configuration and is usually a large and expensive part of the development process. However, extraction of the aerodynamic coefficients from flight test data is still largely a trial-and-error process requiring many iterations. Parameter identification techniques have been attempted but have not been universally accepted as a standard method for flight data analysis by the commercial transport industry. Prediction of aerodynamic damping for conventional subsonic aircraft, for example, has not progressed much beyond the work done by the National Advisory Committee on Aeronautics in the 1950s. Also, the possible role of dynamic wind tunnel testing for commercial transports has not been explored.
Ground effects are also not well predicted. A major portion of simulator crew training is in ground effects, and many man-hours are required to achieve an adequate match with flight test data. Autoland certification is also a problem because systems based on wind tunnel data and predicted aerodynamic characteristics often require corrections derived from expensive flight testing. Furthermore, little work has been done in recent years to correlate dynamic characteristics with pilots' opinions. Failures of stability augmentation systems and the presence of sophisticated flight control system modes must be studied for their effects on minimum safe handling qualities.
The use of laminar flow control techniques may also lead to further departures from familiar characteristics, as well as generating the need for a priori modeling of the feedback loops required to modulate the laminar flow.
In general, then, all of the aerodynamic coefficients are obtained through theoretical means, with empirical adjustments. Flight regimes in which the aerodynamics are nonlinear, at transonic speeds or at high angles of attack, for instance, have been especially troublesome. Greater application of computational aerodynamics could provide more accurate predictions and better consistency but, at present, there is no sound body of data to correlate the empirically derived derivatives used in the early design process.
In the past the lack of complete knowledge of dynamic flight characteristics has been tolerable because the undesirable dynamic characteristics could usually be compensated with electronic feedback control systems. However, there remains the risk that significant problems requiring design modifications will be uncovered late in the testing process. This is particularly true for advanced aircraft configurations. The later the problems are found, the more difficult and expensive they are to fix. Thus, it is important that sufficiently accurate techniques be applied to predict dynamic characteristics from the beginning of the design effort.
A better technical base is clearly needed to address stability and control considerations with theoretically explicit analytical methods and with validated model testing techniques in the early stages of design. NASA is uniquely qualified to address this situation based on its extensive work on dynamic stability of military aircraft and other exotic configurations that represent radical departures from past practice.
NASA should undertake a systematic, in-depth review of current practice in the dynamics and control of aircraft, initiate a program to extend the applications of CFD methods to a priori analysis, and include an extension of model wind tunnel testing to dynamic derivatives. The final goal is to develop methods for systematic correlation of the predicted characteristics with flight test data.
Supersonic Aircraft
The problem of predicting dynamic characteristics prior to the full-scale test phase is particularly critical for the HSCT. The HSCT will have a very wide speed range, will require large angles of attack for takeoff and landing to develop the required lift, and will have strong aeroelastic interactions with highly nonlinear aerodynamic forces. It will be necessary for the designers to rethink the theoretical and experimental methods that are used to predict dynamic characteristics.
Although flight dynamics is not as critical an issue for the HSCT as its environmental compatibility, it is nonetheless prudent even at this early stage to begin incorporating flight dynamics into the iterative design process, and to begin refining the predictive capability for various flight regimes. It should be possible, for example, to first develop methods by using subsonic aircraft designs, since extensive flight correlation is possible, and then extend those methods to the special needs of the HSCT. It might be possible to take advantage of the SR-71 for a selective look at flight conditions unique to a supersonic transport once the subsonic flight dynamics technology is better established.
Because this whole area has received little attention in prior dialogue concerning opportunities for NASA research, it is recommended that NASA take appropriate steps to
specifically address the issue and establish where efforts can best be focused. Such a step should, among other things, review the degree to which flight dynamic technology now employed for subsonic and supersonic military aircraft can be applied to large transports.
AERODYNAMICS OF ROTORCRAFT
For rotorcraft it is frequently difficult to separate the contribution of the conventionally defined disciplines. In particular, aerodynamics and dynamics are so closely coupled in the flexible rotor blades that most research and development on rotors must integrate both disciplines. The discussion that follows contains, therefore, considerable overlap—particularly with regard to vibration. In the sections that follow, the state of the art and recent progress on rotorcraft, including helicopters and tiltrotors, will be addressed jointly, followed by individual sections addressing the challenges and opportunities for conventional helicopters and convertible rotorcraft.
State of the Art and Recent Progress
Analytical Methods
Semiempirical methods are generally adequate for conventional configurations with regard to performance and low-frequency flight dynamic phenomena; noise prediction codes are reasonably good where aerodynamic loads are known, but the inability to predict those loads is severely limiting for critical conditions such as approach and high-speed cruise. Flight dynamic codes, while serviceable for simulation of moderately stabilized systems, are inadequate to predict stability limits of high-gain feedback systems and to adequately forecast tolerable levels of relaxed stability in systems designed to take advantage of active control, especially for larger aircraft in which airframe structural coupling is significant. For less conventional configurations, such as bearingless rotor helicopters and tiltrotors, the ability to extrapolate existing codes is even more questionable.
First-Principle CFD Codes
First-principle CFD codes are not yet in general use by the helicopter industry, although some are beginning to be available for the study of discrete phenomena such as the flow around rotor tips at specific azimuth positions. Most industry hover performance codes continue to use empirically derived wake geometries (or geometries derived from model wind tunnel tests), which appear to be adequate for rotors that do not depart radically from prior experience. However, these codes tend to break down with large variations in twist disk loading or tip geometry. Another gap in predictive capabilities relates to the interaction of rotor and airframe.
This becomes particularly critical for tiltrotors. An extensive wind tunnel test on this problem as experienced by conventional helicopters has just been completed using a Bell 412 rotor in the 40' × 80' wind tunnel, and some experimental work has been done on the rotor wing
interference of tiltrotors, but analytical backup of this work to allow generalization to other design configurations is not yet available.
Test Methodologies and Facilities
Techniques for the testing of model-scale rotors and helicopter airframes are well developed for performance and low-frequency stability phenomena. Wind tunnels adequate for 10-foot model rotors are generally available for the achievable envelope of modern helicopters, including tunnels with moving ground planes to enhance their low-speed-in-ground-effect fidelity, and the Ames facility extends this capability to full-scale helicopters up to the 10,000- to 20,000-pound class. The major gap is the lack of any U.S. tunnel for model-scale acoustic testing, for which only the DNW tunnel in Europe is truly adequate (and very expensive for U.S. industry). Flight test techniques that can truly separate the individual contributions of the rotor and airframes into performance, vibratory load, and flight dynamic phenomena, are also needed.
Design Concepts for Conventional Rotorcraft
Concepts have been pretty well developed that allow the design of reasonably efficient helicopters with payloads up to 20 tons, operational ranges to about 400 miles, and cruise speeds from 150 to 180 knots. Somewhat larger helicopters could certainly be designed at some increase in program risk; the range could be extended if range is made a primary trade-off factor in the design; and higher dash speeds are achievable with a significant sacrifice in efficiency and payload (most easily by utilization of auxiliary propulsion and stub wings to provide some degree of high-speed maneuverability). The current speed record for a pure helicopter is 216 knots. Virtually all helicopters of any size use a significant degree of electronic stabilization (essential for instrument flight), and the most recent models have relaxed inherent longitudinal stability to take advantage of the potential for active control to provide larger center-of-gravity ranges and to reduce empennage requirements. Civil designs have been able to meet current FAA civil rotorcraft noise certification requirements, but these are still considered too noisy to encourage heliport use in all but relatively noise-insensitive areas.
Design Concepts for Convertible Rotorcraft
After years of superficial exploration of a wide spectrum of configurations and in-depth exploration of the tiltwing in the XC-142 program and the tiltrotor through the V-22 program, a good basis now exists for defining the potential of each. The tiltrotor, because of its lower disk loading, appears to show the most promise for extending the speed and range of rotorcraft with the least compromise in the low-speed capabilities essential for confined area vertical takeoff and landing (VTOL) operations. Speeds to 300 knots have been demonstrated, and a reasonable payload fraction appears to be within reach.
Potential for Advancement and Major Challenges—Helicopters
External Noise
The major rotorcraft challenge for NASA is the reduction of external noise. The ability to predict whether a proposed new helicopter can meet noise certification requirements is critical. Both a priori codes and a methodology to extrapolate scale-model acoustic data to full-scale are needed. The external noise problem remains particularly elusive, partly because the aerodynamic source of the noise varies radically from one flight condition to another. Again, much progress has been made on code development, and the time has come to put the emphasis on correlation and the acquisition of high-quality flight (or full-scale) data for correlation.
Secondly, criteria must be established to provide a noise level target that is reasonable to the communities in which heliport locations are proposed. Current criteria reflect more what can be achieved with current technology than what is required to gain community acceptance. These criteria should probably be defined in terms of noise footprint for terminal operations.
Because noise footprint is the critical factor in community heliport acceptance, control developments to allow steeper-gradient landings and takeoffs can play a major role in reducing the external noise problem. This is an excellent example of using advanced control technology to mitigate an aerodynamic problem.
Finally, and most important, technology to reduce rotor noise must be addressed. There are a number of approaches to quiet rotor tip noise that deserve evaluation. With a better understanding of tip vortex geometry to identify what factors may be manipulated to reduce the ''blade slap'' noise, more ideas should be forthcoming.
Rotor aerodynamic technology and transmission design technology that will allow reduction in rotor tip speed without unacceptable efficiency loss offer other attractive options.
Vibration
External noise is followed closely on the priority list by vibration. Vibration problems have probably been the largest cause of major delays and overruns on derivative as well as new aircraft programs. Also, many of the mechanical failures that have occurred on rotorcraft have been traceable to the high vibration levels. Because cabin vibration results from a combination of the periodic aerodynamic loads and the structural dynamic response of the rotor and airframe, the vibration problem must be attacked on an interdisciplinary basis. The analytical tools required are thus a comprehensive rotor/airframe and aerodynamic/structural dynamic modeling effort. Considerable work in this area by NASA, the U.S. Army, and the helicopter industry has been under way for a number of years and is reaching maturity. What is needed now is a program to correlate these new integrated codes. The data base for such a correlation effort is about to be acquired on the UH-60, but a program to meticulously bring together the modeling codes and the data in order to verify the individual elements of these codes and their collective prediction capabilities must now be initiated.
Because a good part of the helicopter vibration and noise problem derives from the drastic variations in blade element angle of attack that occur as the blade rotates in forward flight, the potential benefits of introducing some variation in local blade angle of attack beyond that achievable with the conventional swash plate have been recognized for some time. The possibilities of individual blade control (operating on the rotating coordinates) and higher harmonic control introduced below the swash plate have been investigated, but the former demands excessive power and the latter, although of some benefit, is limited by the harmonics that can be introduced. What really has not been investigated is the possibility of introducing, at specific spanwise stations and azimuth positions, discrete, nonharmonic perturbations of the effective blade element angle of attack. Beyond mechanical blade element actuation, there are a number of novel ways in which this might be accomplished, for example, by the use of piezoelectric structures or by the application of pneumatic jet flap or circulation control technology. The extensive work on circulation control airfoils stimulated by the X-wing program provides a whole new foundation for investigation of such possibilities and should be explored.
Internal Noise
Internal noise is also of very high priority for civil applications. For this problem, active noise suppression using canceling techniques seems to be a promising new approach and initial investigations of this possibility appear encouraging.
Aerodynamic Interaction
As discussed above, developing the analytical tools to address the aerodynamic interaction of rotor and airframe requires attention to complement wind tunnel test programs recently undertaken. A special subset of this problem is the development of better concepts for rotor head drag reduction on conventional helicopters at high-speeds and for rotor/empennage interaction improvement in low-speed flight.
Major Challenges/Innovative Approaches—Tiltrotors
Wing Download
With the first production tiltrotor prototype still under development, opportunities to improve tiltrotors are plentiful. At the top of the list is a means for reducing the wing download of the hovering tiltrotor. One obvious possibility is the use of flaps, but the opportunity for more radical solutions that might derive from a clearer understanding of the interactions should also be investigated.
Propulsion Efficiency
Ranking in importance with the wing download problem is propulsion efficiency, which could be attacked by refined aerodynamics. NASA should apply the kind of thinking that went into the advanced turboprop design with a "clean piece of paper" approach to the problem of significantly improving and extending the propulsive efficiency/speed boundaries.
Geometries, operating revolutions per minute, aerodynamics, and structural dynamics deserve attention. A more radical proposal is to take advantage of variable-diameter rotor concepts that attack the basic problem facing the tiltrotor, namely, that a rotor sized for efficient hover is far too large for efficient high-speed flight.
Other aerodynamic and dynamic problems that also need to be explored are
-
external noise reduction in the helicopter mode, particularly in approaches (this is probably amenable to the same aerodynamic research and development required for conventional helicopters);
-
technology to allow steep-gradient and variable-speed approach envelope expansion to minimize noise footprint;
-
active control for whirl flutter prevention with less wing weight penalty and—by allowing a more flexible, thinner wing—raising the Mach divergence limits and hence the cruise speed;
-
active control for ride quality optimization, by recognizing that civil tiltrotors will spend more time at lower altitudes than will long-range jets (a flight dynamics/electronic control problem); and
-
active control to allow smaller empennages, perhaps even canards, that will have less rotor/airframe interaction and lower weight (about one-half of the V-22 fuselage vibration is generated by rotor wake impingement on the tail surfaces).
Opportunities Common to Both Helicopters and Tiltrotors
Composites in Rotor Design
One opportunity for NASA to help improve the maintenance cost situation for both helicopter and tiltrotors is the exploitation of composites, especially composites to make possible efficient, bearingless rotors. Although such rotors offer much promise by greatly reducing the number of individual parts and bearings, bearingless designs can introduce vibration, aeroelastic stability, and flight dynamic problems. Although these appear to be mostly structural dynamics problems, they are typical of the sort of problem in which aerodynamics and structures cannot be separated.
This technology for conventional helicopters has been the subject of research for some years, but tiltrotors present several new challenges. Evaluation of such rotor concepts makes excellent use of the considerable investment in the upgraded 40' × 80' full-scale tunnel. Such
work must be complemented by an adequate program on composites manufacturing and qualification technology.
Aerodynamic Test Facilities
Finally, the top-priority facility requirement for both types of rotorcraft is to fill the gap identified above with regard to an acoustic wind tunnel capability. The need for such a facility has been recognized for at least five years and has also been strongly supported by the commercial fixed wing industry. Studies have been completed on several options. The most readily achievable solution appears to be the addition of acoustic treatment for the 40' × 80' full-scale wind tunnel. Funding for this facility has been the top-priority request for construction of facilities from the Ames Center, but it has not survived the cut at higher levels. Top-priority consideration of this facility upgrade is strongly recommended for the next construction-of-facilities funding cycle.
Resources Required for Rotorcraft
Resources currently devoted to rotorcraft work are significantly below those applied to rotorcraft in the first half of the 1980s and need to be expanded to levels more comparable with this period. The discussion above defines the agenda in the aerodynamics area—and to a degree, because of the overlaps, in the structural dynamics and controls arena as well. To summarize, for helicopters, NASA should
-
develop analytical tools for forecasting rotorcraft noise;
-
in conjunction with the FAA, establish criteria for noise footprint allowable for neighborhood and city-center vertiports;
-
develop control and human factor solutions to allow steep-gradient, variable-speed descents and takeoffs;
-
explore opportunities for rotor noise reduction;
-
correlate and validate analytical tools for vibration prediction and trade-off analysis;
-
explore design techniques for rotor vibratory excitation suppression;
-
explore techniques for internal noise suppression, including the use of noise-canceling means
-
develop analytical techniques for assessing aerodynamic interference among rotorcraft rotors, airframes, and empennage.
For Tiltrotors NASA should
-
develop and evaluate methods for reducing wing download in a hover;
-
develop and evaluate concepts to improve tiltrotor propulsion efficiency;
-
find ways to reduce external noise in the hovering mode;
-
develop control and human factor solutions to allow steep-gradient, variable-speed descents and takeoffs; and
-
explore the use of active control for (1) whirl flutter suppression, (2) ride quality optimization, and (3) empennage reduction (relaxed longitudinal stability).
For both helicopters and tiltrotors, NASA should
-
explore the application of composites for rotor aerodynamic optimization;
-
develop a high-quality acoustic testing capability for the full-scale 40' × 80' wind tunnel at Ames; and
-
revitalize industry/NASA program on all elements of rotorcraft noise. In the mid-1980s the "NR2" program run by NASA, the FAA, and the American Helicopter Society provided a very effective means of coordinating in-house and government-sponsored work on helicopter external noise. Although some of that activity is continuing, its level no longer brings together the critical mass of government and industry engineers that provided so much vitality to the program.
WIND TUNNEL, FLIGHT, AND AIR-BREATHING PROPULSION TEST FACILITIES
The classes of aeronautical vehicles expected to meet commercial and military needs in the next 30 years fall in the range from low speeds to high supersonic speeds. These vehicles have been discussed in detail in previous chapters. The wind tunnels and air-breathing propulsion test facilities that will be needed to meet the design and testing requirements of these vehicles are discussed in the following sections. A discussion of flight testing and the use of CFD in vehicle design is also included.
Existing Facilities
Wind Tunnels
Over the range from low to high supersonic speeds there are some 90 major wind tunnels in the United States and another 70 in foreign countries, including Canada, France, Germany, Japan, the Netherlands, and the United Kingdom.11,12 Facilities with the greatest dimensions and Reynolds numbers are noted below; their ability to meet test requirements is discussed in later sections.
The largest wind tunnels are
-
subsonic: NASA Ames' 40' × 80' and 80' × 120'; NASA Langley's 30' × 60'; Canada's 30-foot; U.K. Royal Air Establishment 5 meter; Japan's 6 meter; and the Dutch/German DNW with three interchangeable test sections, of which the largest is 9.5 meters;
-
transonic: NASA Ames' 14 foot and 11 foot; NASA Langley's 16 foot and its Transonic Dynamic Tunnel (also 16 foot); the U.S. Air Force's Arnold Engineering Development Center's 16T (16 foot); and France's S-1 (26 foot);
-
supersonic: NASA Ames' 9' × 7' and 8' × 7'; NASA Lewis' 10' × 10' and 8' × 6'; U.S. Air Force Arnold Engineering Development Center's 16S (16 foot) and Aerodynamic and Propulsion Test Unit (16-foot dia.); Rockwell's 7 foot; and France's S-2 (6 foot).
Wind tunnels with the largest Reynolds number (given in parentheses in millions), based on effective chord length, are
-
subsonic: NASA Langley's 7.5' × 3' Low Turbulence Pressure Tunnel (30); NASA Ames' 40' × 80' (17) and 80' × 120' (10); U.K. RAE's 5 meter (8); Germany's DLR cryogenic tunnel (8); and France's F-1 (7.5);
-
transonic: NASA Langley's National Transonic Facility (120) and Transonic Dynamic Tunnel (TDT) (14); NASA Ames' 11-foot tunnel (10); and France's ONERA S-1 (10);
-
supersonic: McDonnell Douglas' 4-foot Polysonic (200) and 4-foot Trisonic (120); Vought's 4-foot High-Speed (150); Rockwell's 7 foot (130); Lockheed's 4-foot Trisonic (120); Canada's NAE 3-D (120); the Netherlands' 4-foot SST (120); and India's 4 foot (100). The McDonnell Douglas, Lockheed, and Vought wind tunnels have a speed range up to Mach 5. NASA Langley and the Department of Defense Wright Laboratory both have high Reynolds number Mach 6 wind tunnels. Because much larger model sizes relative to test section dimensions can be tested at supersonic speeds, the Reynolds numbers noted are significantly higher than for subsonic and transonic wind tunnels;13 however, the Reynolds numbers for complete supersonic aircraft configurations are at least twice as high as those noted above, which are based on root chord. A comparison of the Reynolds number capabilities of major subsonic, transonic, and supersonic wind tunnels is shown in Figures 7-5 through 7-7.

FIGURE 7-5 Comparison of major subsonic tunnels.
Air-breathing Propulsion Facilities
Major air-breathing propulsion facilities can be divided into three categories: propulsion wind tunnels, altitude engine test facilities, and engine/propulsion component facilities.14
The wind tunnels are large facilities in which engine burn tests and propulsion/airframe integration tests can be run. A drawback of wind tunnels for engine testing is their inability to provide true temperature simulation over wide operating conditions. There are seven such tunnels in the United States including NASA Ames' 40' × 80' and 80' × 120', Lewis' supersonic 10' × 10' and 8' × 6', the Arnold Engineering Development Center (AEDC) supersonic 16T and 16S, and Boeing's 9' × 9'. Foreign tunnels include Canada's 10' × 20', France's transonic S-1, and the Netherlands' DNW.
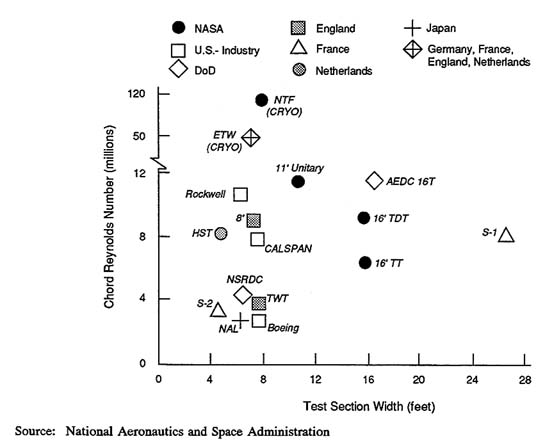
FIGURE 7-6 Comparison of major transonic tunnels.
Of some 60 altitude engine test facilities in the world, the one with the greatest capability by far is the AEDC Aeropropulsion Systems Test Facility with two 28-foot diameter cells, 85 feet long, mass flows exceeding 2,000 pounds per second, a broad temperature range, and speeds up to Mach 3.8.
There are 46 engine/propulsion component facilities in the United States for testing turbines, compressors, and combustors; the only foreign ones are in Japan and Belgium. These facilities are smaller and simpler than the other two categories.15
NASA owns approximately one-third of the major test facilities in the United States and one-fifth of those in the world. Most of NASA's facilities are more than 20 years old and are heavily utilized. Many are in need of repair, have marginal productivity, and need updated
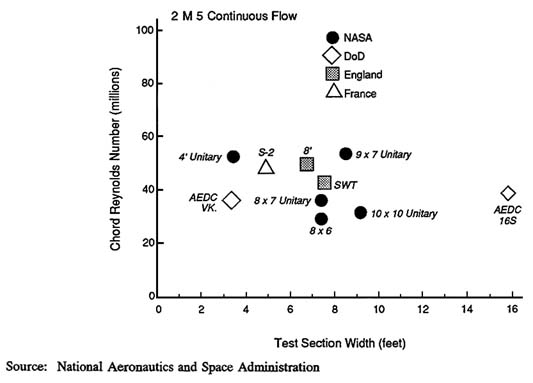
FIGURE 7-7 Comparison of major supersonic tunnels.
control and data systems.16 To overcome these deficiencies, NASA has undertaken a major facility revitalization program of which the first phase—returning them to operational status—is approaching completion. It is important that the revitalization program be continued to bring these facilities to the state of the art and then broaden their capabilities.
Flight Test Facilities
The national flight research assets include the flight testing range and related ground facilities and the aircraft in NASA's research fleets stationed at Ames-Dryden Flight Research Facility, Ames-Moffett, Langley, and Lewis Research Centers. Current research aircraft are listed in Table 7-2.
TABLE 7-2 Current Research Aircraft
Center |
Aircraft |
Capability |
NASA Ames-Dryden Research Facility |
PIK 20E Sailplane General Dynamics F-16 Lockheed F-104 (2) Grumman X-29 McDonnell Douglas F-15 Eagle Boeing B-52 McDonnell Douglas F-18 Hornet Convair 990 |
Glider Supersonic Supersonic Supersonic high alpha Supersonic Transonic Supersonic Transonic |
NASA Ames-Moffet Research Center |
Bell XV-15 British Aerospace YAV-8B Harrier Boeing/DeHavilland QSRA Sikorsky UH-60 Blackhawk (2) Bell TH-1S |
Tiltrotorcraft VTOL STOL Rotorcraft Rotorcraft |
NASA Langley Research Center |
Piper PA-28R Arrow Boeing 737-100 Learjet 28/29" Rockwell OV-10 Bronco |
Subsonic Transonic Transonic Subsonic |
NASA Lewis Research Center |
DeHavilland DHC-6 Twin Otter Rockwell OV-10A Bronco |
Subsonic Subsonic |
Test Requirements for Future Systems
Common to all speed regimes is the requirement for full-scale (high) Reynolds number facilities and flight capability, not only for high-lift devices and high-angle-of-attack configurations at low speeds, which are highly sensitive to Reynolds numbers, but also for conventional aircraft because of the emphasis on drag reduction. There is also a need for very accurate, nonintrusive instrumentation with high resolution for spatial and temporal measurements.
At low speeds the requirements are for flight and ground facilities to test takeoff and landing of conventional aircraft; high-lift devices (short-takeoff-and-landing vehicles), terminal area noise (engine, control surfaces, airframe); rotorcraft; and vehicles with expanded flight envelopes (e.g., high angle of attack). There is particularly strong emphasis on reducing the noise of flight systems, necessitating test facilities with very low background noise of their own.
In the transonic and supersonic regimes, large facilities are needed for propulsion/airframe integration and aeroacoustic studies. Also, low-disturbance supersonic
facilities and flight research aircraft are needed for laminar flow control and boundary-layer transition studies required for vehicles such as an HSCT.
Large air-breathing propulsion facilities are needed to test full-scale turbojet engines integrated into the airframe up to high supersonic speeds.
Adequacy of Existing Test Facilities to Meet Requirements
Low Speeds
Such wind tunnels as NASA Ames' 80' × 120' and 40' × 80', the Dutch/German DNW, the U.K. 5 meter, and France's (ONERA) S-1 (8 meter) meet many of the low-speed test needs; however, none can meet the range of full-scale Reynolds numbers required. An important high Reynolds number capability will be added when NASA restores the Ames 12-foot Pressure Wind Tunnel to operate at 6 atmospheres and speeds up to Mach 0.6, but it will still be far short of the full-scale Reynolds number required. NASA Ames' 80' × 120' is well-suited for testing VTOL powered lift, full-scale rotorcraft, and high-lift devices for takeoff and landing, and is one of the few facilities suitable for full-scale high-angle-of-attack tests; however, it is limited to a Mach number of 0.15 and utilizes very large (full-scale) and, therefore, relatively expensive models.
For aeroacoustic testing, DNW offers the best capability to study noise generated by engines, airframes, and rotors. In the United States, consideration is being given, and an approach defined, toward fitting NASA Ames' 40' × 80' wind tunnel with a thick acoustic lining that will make it the largest facility capable of noise tests on full-scale aircraft and rotorcraft. However, this will not meet the requirements for research on noise reduction at higher climb-out and cruise/climb flight conditions, which are increasingly important challenges for the future.
Transonic Regime
The only facility with full-scale Reynolds number capability is NASA Langley's cryogenic National Transonic Facility with an 8.2' × 8.2' test section; however, its reliability and productivity to date have been relatively low. It is currently being upgraded. A major facility expected to become operational in the mid-1990s is the European Transonic/Cryogenic Wind Tunnel near Cologne, Germany. It will have a test section of 2.4 m × 2.4 m and cover the speed range from Mach number 0.15 to 1.2, with Reynolds numbers based on effective chord length up to 50 million, which is adequate to meet most future test requirements. Special attention in the development of the European Transonic/Cryogenic Wind Tunnel has been given to high productivity and reliability. The extreme cooling to cryogenic temperatures of models and instrumentation used in these facilities imposes special requirements and handling techniques.
Supersonic Regime
Although several supersonic wind tunnels have a Reynolds number capability (based on model size) exceeding 100 million, these are based on wing sections, which are rather large relative to tunnel dimensions, and not the full vehicle. None of these facilities reach the full-scale Reynolds numbers needed for a HSCT or supersonic military systems. In terms of low-disturbance supersonic wind tunnels to study laminar flow control and boundary layer transition, NASA presently has in operation a Mach 3.5 tunnel and is developing a new facility with Mach 3.5 and Mach 6 nozzles. Other low-disturbance wind tunnels are being planned. For supersonic laminar flow research, flight test aircraft play a vital role in technology development and validation by providing access to the real atmospheric disturbance environment. In addition, it is important that large-scale aircraft be available for laminar flow research to provide answers to critical high Reynolds number issues.
Air-breathing Propulsion
The Aeropropulsion Systems Test Facility at the Arnold Engineering Development Center provides a unique capability for full-scale propulsion/airframe integration and combustion tests up to Mach 3.8. Other engine test facilities are inadequate to meet future full-scale requirements. However, one should bear in mind that, even in the Aeropropulsion Systems Test Facility, only segments of a complete vehicle can be tested but these would include parts of the airframe as well as the engine.
Computational Fluid Dynamics
Computational fluid dynamics has become an increasingly important complement to wind tunnels as a tool in the design of new aircraft. Each does different things best. Together they provide more detailed and complete information than wind tunnels alone. This vital role for CFD stems from the tremendous advances over the years in speed and memory size of supercomputers, as well as improvements in numerical algorithms. Among current supercomputers, the Cray 2 has an effective speed exceeding 200 million floating point operations per second (MFLOPS). The more recent Cray YMP has four times that speed (i.e., about 1,000 million floating point operations per second MFLOPS).
Comparable advances are projected to continue for several years, and it is important that they be channeled toward facilitating the application of CFD to airplane design. Experience gained by the airframe industry in the utilization of CFD in recent years has served to identify areas of future development in computational technology.
In the early 1980s NASA undertook the development of a Numerical Aerodynamic Simulation facility as a means of providing a continually updated capability with the latest available high-speed processors, for the purpose of solving the basic flow equations and with the intent of enhancing the application of CFD to aerospace vehicle design. Achievement of these goals requires a refocus of objectives. In the area of hardware—mainframes, communications,
and workstations—NASA's Numerical Aerodynamic Simulation facility has had a pathfinding role and is positioned to continue as such.
In the area of algorithm research and code development, the main focus in the past was principally on solving increasingly complex and complete forms of the basic flow equations. In the future, the focus needs to be expanded to include other factors that are essential toward the effective application of CFD to airplane design. In particular, there is a need for CFD capabilities that
-
can handle the flow about arbitrary geometries;
-
resolve all the important physical length scales;
-
provide reliable accuracy, when used by a design engineer, with sufficient credibility to support engineering decisions;
-
can be rapidly set up and executed (in one day or less); and
-
are economically viable (i.e., the real computing costs for the tens or hundreds of runs typically needed to solve a design problem are justifiable and acceptable).
It is expected that the next decade will witness the emergence of CFD as the critical technology for aerodynamic design. There should be a dramatic change and shortening of the design process, which will enhance and enable concurrent engineering and the optimization of air vehicle systems in terms of overall economic performance. This will require a significant advance in CFD algorithm research and code development.
Such developments are heavily dependent on a close working relationship between NASA and the aeronautical industry to enhance the relevance of NASA research and enable a rapid translation of research advances into application to the design process.
Recommendations for Test and Computational Facilities
This section of this report defines a course for NASA, industry, and academia to achieve competitiveness in aerodynamics. Specific investment needs are described to strengthen the U.S. science and engineering infrastructure and technology validation efforts. The fact that critical technology initiatives planned by NASA and industry have not been implemented demonstrates that the problem is not a lack of ideas and plans but, rather, the priority given to aeronautics.
Experimental facilities and methods, along with computational capabilities, comprise the infrastructure upon which advances in technology can develop and flourish. The future ability of the United States to remain competitive in aeronautics is directly dependent on the quality of its experimental and computational facilities, which, along with flight testing, are the design tools for new aircraft. Economic and technical compromises must be made to determine where each of these tools fits into the design process. The three must serve in a complementary fashion, and the extent of use of any one of them is dependent on its ability to provide certain types of data more effectively than the other two. Finally, precompetitive technology validation through cooperative efforts among government, industry, and academia must be substantially increased if the United States is to remain competitive in aeronautics.
The key aerodynamic technologies that require increased investment for competitiveness include
-
aerodynamic cruise performance, including subsonic and supersonic laminar flow control technology;
-
aircraft propulsion/airframe integration for both subsonic and supersonic aircraft;
-
low speed and high lift for subsonic configurations, including wake mechanics, wake vortex, and measurement technology;
-
computational fluid dynamics for aircraft design, including validation of codes;
-
low speed and high lift for supersonic configurations; and
-
aerodynamics of rotorcraft.
Throughout this report, references are made to needs for a variety of improved ground and flight experimental and computational capabilities. It is important that NASA receive the support and direction required to provide the United States with experimental and computational capabilities that will enable the aeronautical community to develop competitive or superior products in all flight regimes.
The following are specific ground-based experimental capability recommendations to NASA:
-
To vigorously pursue its facility revitalization program beyond the present phase, toward raising its facilities to the state of the art and then broadening their capabilities.
-
To generate an intensive program to develop high-resolution, nonintrusive instrumentation for spatial and temporal measurements.
-
To proceed with all haste in fitting its Ames' 40' × 80' wind tunnel with an acoustic lining essential for noise testing on full-scale vehicles.
-
To develop a low-speed, low-disturbance test capability that can operate at full-scale Reynolds number (based on chord length of at least 50 million) in the range from Mach number 0.1 to 0.5. Because of dimensional constraints, such a facility would have to be pressurized; also, consideration in its design might be given to the possibility of using heavy gases instead of air for aeroelastic scaling or as a means of boosting Reynolds numbers to the required values. Mixtures of heavy gases in proportions to provide the proper scaling of physical variables have been successfully used in testing turbine and compressor stages at realistic conditions of engine operation. A possible alternative to using a heavy gas as test medium would be to operate with air at moderate cryogenic temperatures—down to -150ºF—based on the experience gained in operating the National Transonic Facility.
-
To develop a supersonic, low-disturbance test capability that can operate at a full-scale Reynolds number of 400 million to 500 million over the range from Mach 2 to 6 to meet test requirements for an HSCT and military systems. A pressurized test section would be needed to meet the stringent Reynolds number requirement.
The first important point regarding facilities in general is to ensure high reliability because it is crucial to the value of their data, but good productivity must also be ensured by adequate staffing and by efficient means of moving test models in and out of tunnels. Furthermore, data acquisition and processing equipment must be upgraded periodically to keep these valuable test capabilities current.
Regarding aeronautical flight experimental capabilities, NASA should (1) vitalize the flight research capability and in-flight technology validation efforts in all speed regimes, and develop advanced measurement technologies for flight research. To carry out these recommendations for flight capability, NASA must structure the management of flight efforts to strengthen the integration of flight and ground-based research. NASA must plan for the future requirements for flight to include experimental aircraft, platform test-bed aircraft, and ground and flight infrastructure capabilities.
Finally, in the area of computational technology it is essential that NASA, on a continuing basis, acquire and maintain state-of-the-art computing hardware and develop the CFD algorithms and software that are key to the application of computational technology to aerodynamic design. This includes an aggressive pursuit, with the input of industry, of advances in the development and verification of both design and analysis CFD codes.
RECOMMENDED READING
Epstein, A.H., G.R. Guenette, and R.J.G. Nirton. 1984. The M.I.T. Blowdown Turbine Facility. ASME Paper 84-GT-116. Washington, D.C.: American Society of Mechanical Engineers.
Kerrebrock, J.L., A.H. Epstein, D.M. Haines, and W.T. Thompkins. 1974. The M.I.T. Blowdown Compressor Facility. ASME Paper 75-GT-47. Washington, D.C.: American Society of Mechanical Engineers.
National Research Council. 1983. The Influence of Computational Fluid Dynamics on Experimental Aerospace Facilities—A Fifteen Year Projection. Washington, D.C.: National Academy Press.
Poisson-Quinton, Ph. 1990. EUROMART (European Cooperative Measures for Aeronautical Research and Technology) Survey Results. France: ONERA.