7
DIRECTIONAL DRILLING AND TUNNELING
Introduction
Tunneling and drilling operations fall into two broad categories: (1) operations in which excavation is carried out by attacking the rock face selectively, and (2) operations that use a device to advance the whole cross section of the excavation simultaneously. The first category includes all drill-and-blast and manual methods, and flexible mining machines such as roadheaders or continuous miners. These methods allow a tunnel of any cross section or any curvature to be driven, provided the machine and its mucking system can negotiate the curve. They are typically used in mining operations where great flexibility in size, cross section, and curvature of the excavation is needed.
The second category consists of excavations in which the whole face is advanced simultaneously, and includes those driven by tunnel boring machines (TBMs), raise borers, and all small-diameter holes drilled by the use of a drill bit. Such holes are almost always of circular cross section, because the excavation method consists of rotating some form of cutter head against the rock face. The drive mechanism for the cutter head is normally quite bulky and is rigidly attached to a cutter head because of the need to transmit the required power. Such drilling assemblies tend to be long relative to their diameters and tend to fit tightly in the hole. Changing the direction of the hole is then a matter of making the cutter head cut sideways and getting the drive mechanism to follow. This operation, whether for a shallow exploratory core hole for prospecting purposes, a production oil well, or a full-size freeway tunnel, has certain basic requirements, even though the equipment used in each case may be very different.
In each operation, the hole direction is changed either by exerting a sideways force on the rock cutting assembly or by tilting the cutting
structure so that its axis is inclined to that of the existing borehole or tunnel. If a sideways force is used, it is obtained by reaction of the drilling assembly against the wall of the hole or tunnel, and the deviation is achieved by the ability of the cutting structure to cut sideways as well as forward (Millheim and Warren, 1978; Millheim and Apostal, 1981).
A drilling assembly that exerts a large sideways force, coupled with a cutting structure having substantial sideways cutting ability, will produce a sharply curved borehole. If the hole curvature is generated by tilting the cutting structure, the degree of turn will be determined by the tilt and the effective positions of contact of the rest of the drilling assembly with the hole wall (Figure 7.1). Conversely, straight holes are drilled by rigid drilling assemblies provided with cutter heads or drill bits that have no sideways cutting teeth and that fit snugly in the hole.
Directional Tunneling
Tunnel boring machines excavate a constant cross section of tunnel (usually circular), and the excavating head is not free to move sideways with respect to the main machine body. In driving a tunnel with a TBM, the body of the machine is held in the tunnel by one or more pairs of grippers. In principle, two steering methods are available, either by exerting a sideways force or by tilting the cutting head. In a typical TBM, there is a set of grippers, guides, or side supports close to the cutting head, which is used to position the head, and another set further back that is used to brace the machine against the reaction from the cutting feed force. The preferred method of steering consists of yawing the axis of the machine by displacing the main beam with respect to the rear gripper unit, with the result that the machine pivots about the forward gripped region. No sideways force is applied to the cutter head, so the machine axis is always tangential to the curve of the tunnel.
To achieve a sharper turn, sideways force can be applied to the cutter head by extending one of the forward side supports so that it bears against the tunnel wall (Robbins Co., 1993). In this way, the cutter head is forced to cut sideways as well as forward (Figure 7.2). In this ''crabbing" mode, the machine axis is no longer tangential to the curve, and care must be taken not to damage the machine by forcing it too hard into the side wall.
In the last few years, there has been a rapid development of microtunneling machines, or moles. These are unmanned machines,
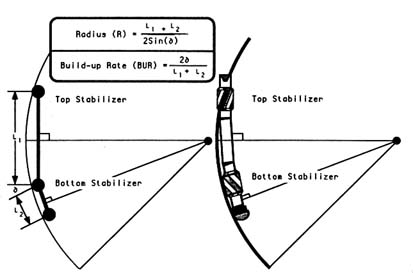
FIGURE 7.1
Hole curvature determined by the position of contact points with the hole wall (Karlsson and others, 1989).
capable of driving tunnels of, typically, 6 to 30 inches in diameter. They have been developed mainly in Japan (Akiba and Yamada, 1989; Hayashi and Miyata, 1989; Moria and Sawaguchi, 1989) and Germany (Beaumont, 1989) for sewer work. The machines consist of a powered cutter head and steering assembly that is pushed forward by a jacking system from a launching pit. As the tunnel advances, sections of temporary or permanent lining are fed in and pushed forward behind the mole by the jacking unit. Maximum tunnel length is up to 500 ft (Hayashi and Miyata, 1989). The excavation method is by pressure/thrust, auger, water pressure balance, slurry shield, or other methods. The machines operate in a variety of relatively soft soils, although some are provided with crushing heads that will cope with gravel and small boulders. Some of the machines are steerable and typically use a system of hydraulic jacks to tilt the cutter head in the required direction.
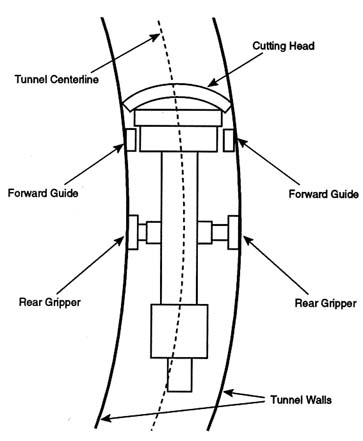
FIGURE 7.2 Plan view of a TBM turning in a "crabbing" mode (after Robbins Co., 1993).
Large TBMs obtain steering information by observing the position of a laser beam spot cast on a target mounted on the machine, the laser source being mounted on a fixed support some way to the rear of the tunnel. Several manufacturers offer such systems (Anon., 1988).
A disadvantage of the laser system is that the laser must be within line of sight of the tunneling machine, and it is therefore not well adapted to surveying tunnels with numerous or sharp curves. At present, steering adjustments to the machine are carried out manually, but automated systems are under development (Gibson, 1993). The Japanese have an
alternative system using gyroscopes, also with manual implementation of the steering information (Miyazaki, 1993). For the same reasons, the gyroscopic system seems better adapted to the remotely operated microtunneling machines that drive tunnels a couple of feet or so in diameter. A disadvantage of the gyroscopic system is that it must be reset periodically, for example, by removing it from the tunnel so it can "see" a reference satellite.
Directional Drilling of Boreholes
Reasons for Directional Drilling
Directional drilling (e.g., Cooper, 1994) is not new. Since the earliest times, boreholes were made to deviate by placing tapered wedges or "whipstocks" in the borehole to force the bit sideways into a new direction, and it was known that different bottom-hole assemblies (BHAs) had a tendency either to increase or to decrease the inclination of the hole. Most developments in directional drilling started in the petroleum industry and then spread to other fields. Pioneering work was carried out in oil well drilling by John Zublin, H. John Eastman, and others during the 1950s in drilling directional drainholes from existing wells (Stormont, 1953; Eastman, 1954). Significant work was also done during the 1960s in directional drilling from Huntington Beach, California. However, progress was slow until the mid-1980s, when it was realized that significant increases in productivity could be obtained by orienting the borehole correctly in the reservoir (Reiss, 1987). Simultaneously, it was realized that substantial economies could be obtained in offshore operations if, by extending the horizontal reach of the production wells, the area accessed from any platform could be increased (Wilson and Willis, 1986) or the number of platforms needed to exploit a reservoir could be reduced (Tolle and Dellinger, 1986).
Since the mid-1980s, a large amount of work has been done to investigate all aspects of directional drilling. In addition to the control of direction, other important issues include surveying methods; borehole stability and cuttings removal in inclined boreholes; the reservoir engineering aspects of horizontal wells; and the various special problems associated
with completion and production, such as the cementing of liners, gravel packing, and fracturing.
Directionally drilled wells fall into three main categories. In the first category, the task is to reach locations that are not accessible through straight, vertical holes. For example, unfavorable surface topography may exist, such as the presence of buildings, hills, or water above the target location. Alternatively, a directional well may be drilled to avoid undesirable locations in the subsurface, including fault zones or regions of known "difficult" rock (e.g., salt, swelling shales, and high-pressure regions). It may be advisable to drill a directional well from a safe distance to intersect a blown-out well. In exploration drilling, several deviated test bores may be drilled from the same upper section of the hole in order to save on drilling costs and avoid moving the rig.
In the second category, the objective is to reach a substantial distance horizontally away from the drilling location. This technique, known as "extended reach" drilling, is used to allow many parts of the reservoir to be accessed from one location. The major application of extended reach drilling is in offshore operations, where it is used to reduce the number of platforms needed. Recently, extended reach drilling has become of interest for land operations, where environmental concerns or urban space restrictions may impose land use demands. An area of growing interest for extended reach drilling is to access offshore oil fields from a shore-based location, resulting in reduced environmental impact and reduced cost associated with land-based drilling.
In extended reach drilling, maximum reach depends on the target depth, as well as maintenance of good borehole conditions and a sufficiently steep angle to allow the drilling assembly to slide forward so as to apply weight to the bit. The technology is advancing rapidly. The current world record extended reach well, drilled in the North Sea, accessed a target at a horizontal distance of 23,917 ft (4.53 miles) at a depth of about 9,000 ft (Anon., 1993b). The length of the hole was 28,743 ft (5.44 miles).
The third category consists of wells in which the part of the well that lies in the reservoir is given a particular orientation so as to increase productivity. For example, in a vertically thin reservoir, a horizontal hole can contact a greater part of the reservoir than a vertical one, increasing the drainage contact area and delaying the water or gas coning. The reservoir geometry helps determine whether to use a horizontal or vertical well; a horizontal well is more productive and thus more favorable than a vertical well as the reservoir width increases and the height decreases.
Actual values have been estimated by Joshi (1987a, b, 1988; Figure 7.3). For example, for the same density of wells per unit of land surface (30-acre spacing), a 1,000-ft-long horizontal well has about twice the productivity of a vertical well if the reservoir thickness is 400 ft, and this figure increases about five times if the reservoir height decreases to 100 ft. When the reservoir thickness is 25 ft, the productivity becomes seven times that of a vertical well. In addition, drilling a horizontal hole in a tight but fractured reservoir so as to intersect the maximum number of fractures, which are usually vertical, can greatly increase productivity (Reiss and others, 1984; Reiss, 1987; Haas and Stokley, 1989).
In some circumstances, one or more wells are drilled horizontally into the producing formation from a main vertical well. These are often referred to as "drainholes," whereas a single borehole drilled horizontally
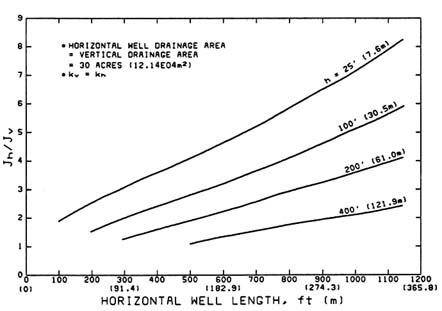
FIGURE 7.3
The ratio of productivity indices for horizontal and vertical wells for different horizontal well lengths and reservoir heights (Joshi, 1987a).
into the producing formation is referred to as a horizontal well. As with extended reach drilling, the technology is advancing rapidly. Texaco recently claimed a record for a pair of horizontal drainholes that extended 5,332 and 4,100 ft from a single vertical well (Anon., 1993c).
Limitations to Borehole Reach and Turning Radius
In drilling any hole, it is essential that sufficient thrust be transmitted to the bit to make it advance. In an extended reach hole, this requirement becomes one of making the contact between the drilling assembly and the hole wall as friction free as possible, allowing for the flattest "sail angle." (For the record-breaking hole recently drilled in the North Sea, this was 82 degrees from the vertical; Anon., 1993b.) For hole angles flatter than this and for horizontal holes, the drilling assembly has to be pushed forward by the action of a thrusting section of heavy pipe or collars located further up the hole in a more steeply inclined interval (Figure 7.4).
Drill pipe located between the thrusting section and the drill bit must then operate in compression and is subject to buckling (Lubinski, 1950). In an inclined hole, the buckling is not as severe as it would be in a vertical hole. This is because of the stabilizing effect resulting from the pipe being held by gravity in the trough formed by the lower side of the hole (Dawson and Paslay, 1984). Buckling forces the pipe against the hole wall and thus reduces the efficiency with which the thrust force can be transmitted. In addition, buckling (and bending the drill string to negotiate the curve) induces flexural fatigue, particularly if the pipe is made to rotate, as is required if the drill bit is rotated from surface.
To strengthen the pipe against buckling, it is made thicker and often is provided with "wear knots" of wear-resistant alloys (Figure 7.4). However, the thicker the pipe, the greater is its weight, and the greater is the drag force it exerts on the hole wall. Furthermore, the thicker the pipe, the smaller is the curvature through which it can be bent before the axial stress in the pipe reaches the fatigue limit. These considerations have led some to suggest the use of aluminum, which has a lower modulus and a lower density (Glagola and Wong, 1986); however, its use is not yet widespread.
It is clear that different compromises must be accepted in combining reach with hole curvature, and several different engineering solutions have

FIGURE 7.4 Typical arrangements for horizontal and directional drilling (Logan, 1988).
been developed to fill particular requirements. In general, holes that have sharp radii of curvature are drilled at a smaller diameter and achieve less horizontal displacement. Drilling methods for small-radius curves seldom entail rotating the bit from the surface, and use downhole motors or unconventional methods for breaking the rock. Holes with large radii of curvature reach further and may often be drilled by rotation from the surface by using conventional full-size drilling tubulars.
Several considerations govern the choice of curve radius and therefore the drilling method. For extended reach wells, the maximum reach is attained with large tubulars and gentle curvature. However, a hole of gentle curvature necessarily has a long curved section that must start a substantial distance above and horizontally displaced from the target. This may not be convenient for several reasons, including the following:
-
Precision of response in steering: A hole with gentle curvature will have a long curved section. The curve may intersect several strata on the way to the target, each causing a different turning response in the
-
BHA. Correction of the trajectory will take a long distance, so it may be difficult to have information early enough to direct the well accurately to the target.
-
Uncertainty of target position: In many cases, the exact depth of the target is uncertain, and decisions concerning the steering of a large-radius curve may have to be made hundreds of feet above the target before its position is clearly known.
-
Avoidance of geologic difficulties: Another disadvantage of a long curved section is that substantial footage will be drilled at high inclination in nonreservoir rock. This is likely to be the reservoir caprock, such as a weak or water-sensitive shale (Hourcard and Bannerman, 1990). Reducing the turning radius of the hole will reduce the distance to be drilled in the problem strata and, because the kick-off point will be lowered, may allow some strata to be avoided entirely by the curved section.
For the above reasons, holes are often drilled with two curved sections joined by an inclined straight interval (Schuh, 1989; Figure 7.5). This allows the turning tendency of the BHA to be assessed during the drilling of the first curve and the straight section to be shortened or lengthened to allow the second curve to hit the target exactly. In addition, the straight section may be continued down to intersect the target horizon at a steep angle (Austin and others, 1988; Stacey and others, 1992). This will allow the driller to determine its exact depth, and perhaps to recover cores or log the well. Once this information is known, the well may be plugged back and the second curve drilled with high precision to target. For wells drilled with sharp curvature, the vertical section of the well may itself be continued into the target and the kick-off points determined after the productive interval has been located and logged (Austin and others, 1988; White, 1989).
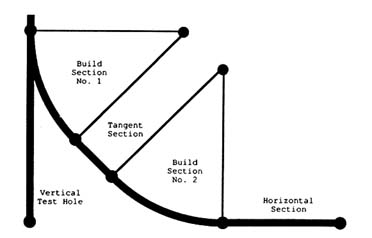
FIGURE 7.5 Well profile showing two build sections with a straight portion between, and the initial test hole to determine reservoir depth (Karlsson and others, 1989).
Methods for Directional Drilling
Early techniques for directional drilling used whipstocks of various types to force the bit sideways. In soft ground, a bit with one oversized nozzle was used to erode one side of the hole preferentially (while not rotating) to achieve the same effect. A borehole may have its inclination changed in the vertical plane (but not in azimuth)1 by the judicious placement of stabilizers behind the bit. A stabilizer placed close to the bit, followed by another a substantial distance away will allow the section of collar between them to sag toward the bottom of the hole. This will tip the bit upward and result in the bit drilling so as to increase the deviation from vertical. This is known as "building angle." Conversely, a first stabilizer located a distance behind the bit will allow the bit to hang down and drill
toward the vertical. This is known as ''dropping angle." Figure 7.6 shows sketches of these configurations for a flexible BHA.
Such "pendulum assemblies" rely on the borehole having some initial inclination, and are simple to use in terrain for which the building and dropping characteristics of each assembly are known. These methods rely both on titling the bit face in the new direction and on forcing it sideways, and therefore combine the two fundamental methods for changing direction. The degree of curvature that may be achieved is quite low, typically 1 to 5 degrees per hundred feet, and the use of pendulum assemblies is generally restricted to full-size (greater than 6 inches) drilling assemblies.

FIGURE 7.6 Arrangement of stabilizers to build, drop, or hold angle (Logan and others, 1987).
To obtain greater curvature, gain better control of the turning radius, and be able to change the azimuth of the hole, several specific engineering solutions have been developed. Because of the compromises in balancing turning radius against reach and the resultant implications for borehole diameter discussed above, no one drilling method is satisfactory for all radii of curvature. It is customary to distinguish among these as long-, medium-, short-, and ultra-short-radius methods (Figure 7.7).
Long-Radius Methods
Long-radius methods use conventional drilling tubulars and are applied in hole diameters 6 inches or larger (Bosio and others, 1987). Curvatures of 2 to 5 degrees per hundred feet are typical, resulting in turning radii of 300 to 1,000 ft or so. Pendulum angle building or dropping
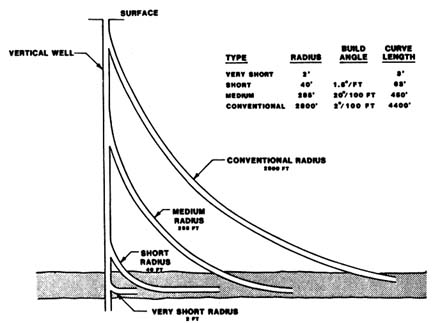
FIGURE 7.7 Long-, medium-, short-, and ultra-short-radius boreholes (Logan and others, 1987).
assemblies may be used to change the inclination of an already inclined hole. To change azimuth or to gain more precise control on the initial kickoff, drilling is carried out with a combination of downhole motor and "bent sub." The latter is a section of drill collar that has a bend of a few degrees between the top and bottom connections, which both forces sideways and tilts the motor section located below it. To change the direction of the hole, pipe rotation is stopped, and the drill pipe position is adjusted from the surface until the bent sub is oriented so that the "tool-face orientation" (i.e., the angle between the projection of the bend axis and the high side of the hole on the hole bottom) is set correctly. The motor is then started, and drilling is allowed to proceed. Periodic measurements are made of hole direction and inclination, with adjustments to the tool face angle as necessary. If it is desired to drill straight ahead, this may be achieved without removing the directional drilling assembly, by applying a slow rotation (some tens of revolutions per minute) to the drill stem from the surface. The motor and bent sub will continue to drill while rotating, in effect drilling a very fine spiral that is indistinguishable from a straight hole.
Different motors are available. For drilling with mud, turbines or positive displacement motors (PDMs) are available. The former were the first to be introduced, but produce their best power output at rotary speeds that are too high for most present bits (with the exception of some diamond bits). PDMs have undergone substantial development (Makohl and Jurgens, 1986) and are now generally preferred. For air drilling, downhole hammers are commonly used (Whiteley and England, 1985), and recently there have been substantial developments in PDMs for air drilling (Shale, 1991; see also Lattimore, and others, 1987; Yost and others, 1987).
It should be realized that drilling with a motor and bent sub costs more than drilling with a pendulum assembly, which is preferred if no changes in azimuth are needed. The response of a pendulum assembly is sometimes difficult to predict and changes as the lithology changes. Recently, however, stabilizers have been introduced that are adjustable from the surface, thereby allowing changes to be made to the building or dropping tendency without having to remove the BHA from the hole (Eddison and Symons, 1990).
The great advantage of drilling with gentle curvature is that the full range of drilling and completion equipment can negotiate the curve. Not only does this allow all logging and other tools to reach the bottom of the well, but the well may be cased along its whole length. This allows
selective completion of particular intervals, as well as the control of hole collapse, sand production, and other problems.
Medium-Radius Methods
Medium-radius methods use drilling assemblies that are capable of rates of turn of 5 to 30 degrees per hundred feet, resulting in radii upward of a few hundred feet (20 degrees per 100 ft gives a radius of 287 ft). The dividing line between long- and medium-radius methods is not precise, and is best thought of in terms of the completion practice; a long-radius well can normally be drilled and completed with any of the conventional casing and completion methods, whereas a medium-radius well has too sharp a curvature to accommodate many standard completion tubulars. A medium-radius well will frequently be drilled with an open hole section at the end or will require special treatment. Since the maximum curvature allowable in a casing depends on its diameter, the distinction between long- and medium-radius wells will therefore be somewhat dependent on hole diameter.
Many manufacturers offer drilling assemblies that are capable of drilling medium-radius wells. These are bent sub/motor combinations that frequently involve the use of adjustable bend devices so that the degree of bend, and hence the rate of turn, can be adjusted in the field. The adjustment may be made by altering a single bend or by using various types of double bend that can be combined to enhance or cancel each other so as to generate different rates of turn (Figure 7.8 ). For examples of the use of these different systems, see Edlund (1987), Barrett and Lyon (1988), Karlsson and others (1989), Sheikholeslami and others (1989) for Hughes Christensen equipment; Rehm and Garcia (1989) for Becfield; Reiss and others (1984) for Telepilote; and Anon. (1989) for a description of several systems.
An interesting feature of the Hughes Christensen "Navigation Drilling System" is that whereas most of the bent sub/motor combinations have the motor axis displaced from the main axis of the drilling assembly, and therefore push the bit sideways as well as tilting it, the Navigation Drilling System uses a double bend to tilt the bit from below the motor, thus causing the deviation of the hole to occur mostly by the tilt of the bit. This is claimed to give more consistent steering.

FIGURE 7.8 Equipment for drilling medium-radius curves (Sheikholeslami and others, 1989).
Short-Radius Methods
A short-radius drilling method described by Parsons and Fincher (1986) is capable of rates of turn of 1.5 to 3 degrees per foot, resulting in the borehole becoming horizontal in 30 to 40 ft of drilled hole for a system operating with a 4.5-inch bit, or in 50 to 60 ft for the 6.25-inch-bit system.
The equipment consists of an orientable whipstock that is lowered into a previously drilled vertical hole, a directional drilling assembly, and a straight drilling assembly (Figure 7.9).
After the whipstock has been placed and oriented in the hole, the directional drilling assembly is lowered. This consists of a nonrotating external tubular guide, through which is passed a flexible drive tube supported on bearings at either end. The guide has slots milled in it to cut about two-thirds of its circumference and is then bent so that it forms a springy curve of 20- to 40-ft radius, depending on the guide diameter. This guide is sufficiently flexible to be forced straight to enter the vertical hole, but in this state it exerts about 1,000 lb of sideways force, so that upon leaving the whipstock, the assembly drills ahead along a curve. In front of the guide is a conventional bit, while to the rear of the guide are lengths of flexible drive pipe, composed of interlocking steel elements that allow torque to be transmitted even though the pipe can flex. (The flexible pipe has a polymeric liner to make it leakproof, so as to carry the drilling mud.)
In operation, the directional drilling assembly is made to drill ahead until the desired degree of inclination is achieved. It is then removed and replaced by a straight drilling assembly that is allowed to drill forward until the desired length of hole is drilled, usually 200 to 400 ft (maximum 900 ft). A clutch arrangement allows the orientation of the guide to be adjusted initially, but the azimuth of the hole cannot be changed easily once it is started because the flexing of the guide is limited to one plane.
The accuracy of the azimuth is typically about ± 20 degrees, although when drilling multiple wells, experience allows better predictive capability. Inclination can, of course, be controlled by drilling more or less of the curve. Additional equipment for coring is available (Eaton, 1990). This method has been used successfully in several applications in the oil industry (Keelean and others, 1989) and for coalbed methane recovery (Logan and others, 1987).
Ultra-Short-Radius Methods
Ultra-short-radius drilling methods capable of producing horizontal drainholes directly from an underreamed length of a vertical wellbore have been described by Dickinson and Dickinson (1985) and by Dickinson and others (1989). An erectable whipstock placed in a 22-inch-diameter underreamed section of a 7-inch diameter vertical hole turns a length of
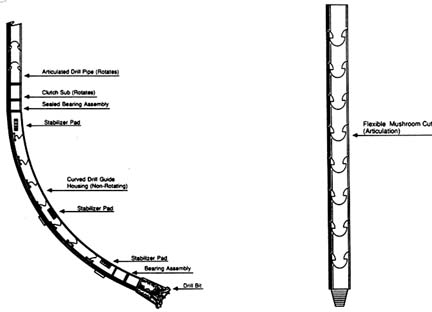
FIGURE 7.9 Equipment for drilling short-radius curves: left, the guide; right, articulated drill pipe (Keelean and others, 1989).
1.25-inch-diameter electric resistance welded tubing from vertical to horizontal with a radius of 1 to 2 ft. At the forward end of the tubing, a jet nozzle allows high-pressure water to be directed at the rock to be drilled, while the pressure of the water inside the tubing feeds it forward into the hole created by the water jet. A horizontal drainhole 1.5 to 2.5 inches in diameter is thus created, which, under favorable circumstances, extends a hundred or more feet from the vertical well (Dickinson and others, 1992; Figure 7.10).
After the hole is drilled, it may be gravel packed, and the tubing may be perforated and severed electrochemically (Dickinson and others, 1987). This allows the whipstock to be turned and/or lifted so that more radial holes may be drilled. A means for steering the tubing as it exits the whipstock, described by Dickinson and others (1992), consists of a sensing device and equipment for allowing vertical deviation control by selectively opening side ports near the forward end of the tubing. Side forces generat
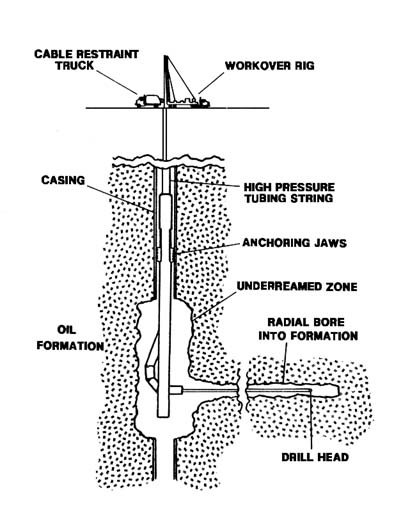
FIGURE 7.10 Ultra-short-radius system (Dickinson and others, 1987).
ed by the exit of high-pressure water from the ports force the drilling head up or down (Figure 7.11). This steering method is of interest because it does not generate the steering force by pressing some part of the drilling assembly against the hole wall. This steering method has also been used elsewhere (Ritchie and others, 1989).
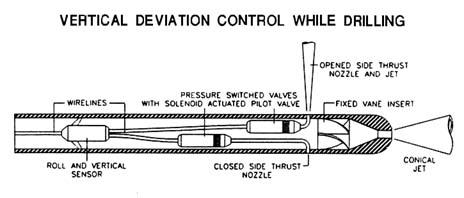
FIGURE 7.11 Directional control obtained by the use of side-thrusting water jets (Dickinson and others, 1992).
Methods Using Coiled Tubing
Recent work has involved the drilling of directional and horizontal holes in which the drilling assembly is attached to a coiled tubing unit rather than to conventional drill pipe. This technique is particularly interesting in reservoirs where there are open fractures that have different reservoir pressures. An example is the Pearsall Field in Texas, in which the producing formation is the Austin Chalk. In this formation, successive vertical fractures may have different fluid pressures, so that if mud density is increased to control high pressure in one fracture, it may result in lost circulation in the next. Conversely, if the mud density is reduced, lost circulation will be reduced, but the well will flow from the high-pressure fractures. Water is the preferred drilling fluid because it does not cause plugging of the fractures at excess pressure and is economical if circulation is lost. It is not, however, dense enough to control pressure by its own hydrostatic head, so drilling is carried out with the wellhead under pressure.
An appropriate diverter system removes the returned fluids, which are then separated. Oil is removed, and the water is returned as the drilling fluid. This is known as "flow drilling." Because of the low bottom-hole pressures, it results in rapid penetration, as well as early revenue from the produced oil.
Under normal circumstances, the well would have to be killed before a trip, which is costly, time consuming, and can cause formation damage.
However, if drilling can be carried out from a coiled tubing unit, the operation can be done under pressure through a snubbing unit without the necessity of killing the well. Fultz and coworkers demonstrated drilling from a coiled tubing unit inside a casing (Fultz and others, 1990) and subsequently described drilling in an open hole (Fultz and Pittard, 1990). This work has recently been followed by the successful drilling of a directional producing well (Ramos and others, 1992). It is expected that these developments will open interesting new possibilities in drilling directional wells.
Directional Drilling in the Near Surface
A large segment of the directional drilling industry is concerned with drilling in the near surface for physical infrastructure purposes, such as the laying of services between buildings and under roads, rivers, or other obstacles. The requirements are characterized by a need for good directional control and for penetration in relatively soft terrain. A subsidiary requirement is that since much of the work is done near inhabited areas, the drilling equipment and methods are preferably nonintrusive. Applications range from the placement of cables from the street to an individual house to the passage of large pipelines under rivers. The latter activity has grown rapidly in recent years; beginning in the late 1970s, about 50 projects totaling 60,000 ft are reported to have been completed by the end of the decade. In 1988, 200 projects, with a total length of 200,000 ft were completed (Hair, 1989a). A world record was recently claimed when a 4,150-ft length of 42-inch gas pipeline was pulled and pushed under the Sacramento River (Anon., 1993a). Another recent job involved pulling 2,000 ft of 48-inch line under the Noord Hollands Canal (Spiekhout and others, 1993). A maximum length of crossing was reported as approximately 6,000 ft of 8-inch line, under the St. Lawrence River near Trois-Rivières (Hair, 1989a).
A rapidly growing application for near-surface directional and horizontal drilling is in the field of environmental investigation and remediation. Special requirements in control, recovery of samples, and cleanliness have to be addressed (BDM International, 1993), and some interesting experiments have already been tried (Kaback and others, 1989). Leo Duffy, former Assistant Secretary of Energy, stated that the use of horizontal wells at the Department of Energy Savannah River Site saved
$125 million, compared to a conventional pump-and-treat scheme for the removal of pollutants (Anon., 1992).
The drilling of large-diameter river crossings is usually carried out by use of a slant rig that is able to push a drill pipe forward at a shallow angle, typically 8 to 12 degrees. The normal method of operation is to drill a pilot hole of a few inches' diameter, using jetting or a conventional directional drilling assembly to change direction. Drilling is normally straightforward—the main consideration being that the operation is frequently carried out in unstable ground composed of unconsolidated sands or clay, although applications in hard rock have been described (McKenny and Knoll, 1989).
In soft ground, drilling may be carried out by using a drill pipe rotating inside a ''washover pipe" that is periodically advanced to catch up with the drilling assembly. The washover pipe carries the return mud and cuttings back to the surface so that erosion of the borehole is minimized and the hole is prevented from collapsing. In such a case, the drilling rig is provided with the means to advance and rotate the drill pipe and washover pipes independently. When the hole breaks through on the far side of the crossing, a pulling head with a reaming barrel and fly cutter or "bullet nose" is attached, and this is pulled back through the hole to the starting point, drawing the pipeline behind it. Sometimes, more than one reaming pass may be carried out, resulting in a choice of final pipe pulling direction from either end of the hole (Szczupak, 1989).
Directional control is by motor and bent sub or, in soft ground, by the use of a bit with an eccentric jet nozzle, which can erode one side of the hole preferentially. The steering input may be obtained from a variety of sensors. These may be introduced into the hole (typically on wireline) while drilling is stopped to relay information to the surface ("survey tools"), or they may be made sufficiently robust to be kept in the hole while drilling is in progress. The latter, combined with steering equipment, allow directional changes to be made without interrupting the drilling operations, and are known as "steering tools." For a discussion of these techniques, see Pittard and others (1989).
Different physical principles are employed, including the use of magnetic, induction, and gravity sensing devices, or gyroscopes. Magnetic devices may use the natural gravitational field, or the position of the boring head may be measured by laying out a cable on the surface in a precisely known position above the path of the drill and passing a strong current through it. A magnetometer at the drill head then senses the field generated
and provides the necessary steering information. These principles are used in a variety of commercial devices, ranging from real-time measurement while drilling (MWD) to single- and multishot surveying devices to the various tracking methods that detect the position of the drill head from sensors on the surface above the boring head.
Finally, it is important to know the precise position of the "as-built" pipeline. For this application, "gyropigs" are being developed that will record directional data as they are pumped down the pipeline (Spiekhout, 1991). Generally, "in-hole" devices are used in the longer, deeper holes, either because the holes are too deep for the surface sensors to detect the drilling assembly accurately or because the surface locations are inaccessible. Surface detection methods are, however, much less expensive because they do not use complex or delicate "downhole" instruments that have to endure the drilling environment. They are therefore preferred for smaller, shallower holes.
For small-diameter and shorter boreholes, a range of augering and pipe-jacking devices is available. Various nonsteerable augers and "moles" have been developed, using one of three basic excavation methods. Augers excavate the ground and transport the dry cuttings to the rear of the hole by a rotating spiral conveyor. Augers are generally used for holes 8 inches or larger and are useful in loose ground. They can be combined with impact and rotary impact boring heads to deal with harder terrain (Anon., 1990). Moles either operate by wetting the ground to loosen it and then forcing their way forward, or use impact devices to hammer their way into the ground, pushing the soil to the side.
Several mole devices are of particular interest because they are steerable. One such device uses high-pressure jets (25 MPa [megapascals] at 0.03 m3/s) of a bentonite suspension to drill the hole (Ritchie and others, 1989). This pressure is said to be able to drill most soils but not to damage existing metal structures or concrete. For drilling in harder soils, carbide cutting teeth may be added. The cutter head has a transmitter that sends a signal to a surface locating unit, which is capable of detecting the drill head position at depths down to about 30 ft. The system uses the orientation of the jets in the drilling head to steer the tool.
A family of steerable devices has been developed as the result of a Gas Research Institute project, set up in 1984, that resulted in the development of three small-diameter guided boring systems (Hair, 1989b). The first comprises a pneumatic hammer attached to a rod pushing unit. The penetrating head has an oblique forward surface that causes it to
deflect sideways as it penetrates. Behind the head is a sleeve with a pair of spiral fins that engage in the hole wall. The sleeve can be locked in place on the boring head, in which case the penetrating head is forced along a spiral path with no net deviation. If the sleeve is unlocked, however, the head will not rotate, and the hole will be deflected in whatever direction the oblique head is set. For position detection and steering, the drilling head uses a solenoid, emitting a magnetic field that is detected by a surface unit.
The second device is a hydraulically powered rod pusher (Figure 7.12) that has an offset conical penetrating point at the forward end of a string of push rods. There is no drilling motor, and the string is advanced and steered by respectively jacking and rotating it from the jacking pit end (Stangl and Boeckman, 1989).
The third device is again a pipe-jacking system, but with a choice of drilling methods (Pittard and others, 1987; Stangl and others, 1988; Figure 7.13)—either an impact penetrator with oblique face similar to that described above, or a down hole air motor and bent sub developed by Maurer Engineering Co. (Houston) based on motors developed for the petroleum industry.
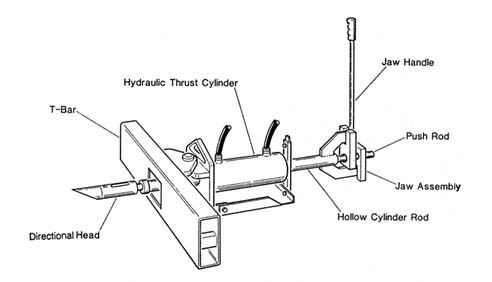
FIGURE 7.12 Rod pushing unit (Stangl and Boeckman, 1989).
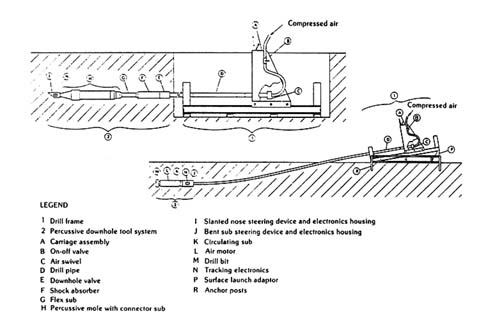
FIGURE 7.13 "True Trac" guided drilling equipment (Hair, 1989b).
Priorities for R&D
-
Directional tunneling: The great advantage of circular TBMs is that they excavate the whole tunnel face simultaneously and are therefore capable of much greater rates of advance than the selective machines. However, there will always be a demand for tunneling machines that are more flexible in terms of the diameter, and particularly the shape, of tunnels that are cut. In most cases, it is desirable to have a flat floor in order to allow access by wheeled or tracked transport (water and some rail tunnels being an exception). Designs that allow the driving of noncircular tunnels, but simultaneously permit excavation to proceed over most of the tunnel face, are of great utility. These will allow high power levels to be brought to the working face, with attendant high rates of advance. If mechanical excavation methods are used, a heavy and bulky drive system will be needed, which makes sharp turns difficult. This is the principal reason that TBMs are frequently used to drive transportation or water
-
tunnels, which are usually only gently curved but are seldom found in mines. Research should focus on designs that are more compact, to allow easier steering while at the same time allowing simultaneous excavation of the whole face. In the longer term, if a nonmechanical means for excavating the tunnel can be developed, it may not be necessary to have a large, rigid supporting structure, nor will it be necessary to maintain the circular cross section. Continued long-term research that focuses on novel excavation methods for directional tunneling should also be pursued.
-
Directional drilling: The subject of directional drilling covers many fields, each having its own particular demands. In general, there will always be a need for adaptable methods that allow holes of different diameters and degrees of curvature to be drilled with the same equipment. The wide range of methods available in the petroleum and civil engineering sectors, each with its own particular niche application, illustrates the need for the development of more general directional drilling methods that will have a wider range of use. Specific research needs for directional drilling include the following:
-
Directional drilling and sharp curves: Methods are needed to drill sharper curves in holes with larger diameters. Since one of the limiting factors in this case is the difficulty of making large-diameter tubulars (particularly casings) curve around tight turns, research should be undertaken to develop flexible casings and liners, or to develop methods for forming a curved casing in situ. For similar reasons, research is needed to develop drill strings that will transmit high loads around the curve and along the horizontal portion of the well, but will be resistant to buckling and to flexural fatigue. Lightweight alloys or novel composite materials offer interesting possibilities in this area.
-
Directional drilling and lubricating muds: Transmission of drilling forces to the hole bottom in near-horizontal wells will be aided by the development of smooth drilling assemblies, helped by highly lubricating muds. Research in this area should focus on muds that have good cuttings-carrying capacity. In the particular case of the growing market for environmental drilling, the muds should have low toxicity.
-
Drill bits: Since transmission of weight to the drill bit is critical in much directional drilling, particularly extended reach drilling, there is a need for research to develop drill bits that have high cutting ability at low weight on the bit. Such very aggressive bits may have to be
-
protected from the application of excessive weight if this becomes available, pointing to the need for a downhole system of weight and/or torque control.
-
Bottom-hole assemblies: An alternative approach to drill bits might be to develop a BHA that grips the hole wall and pulls itself along. This would eliminate the need for many of the specialized arrangements of collars uphole, compressive service drill pipe, and limitations to hole curvature that arise from having to transmit compressive forces around the curve. The committee recognizes that some work was undertaken in this area a few years ago and recommends continued research and development on BHA alternatives. For example, the use of coiled tubing for directional drilling deserves emphasis for continued development.
-
Directional sensing instrumentation: Research is needed to develop more accurate and cheaper direction-sensing instrumentation, particularly for equipment that can detect and steer the drilling equipment without the need to stop drilling operations. Thus, locating equipment mounted on the surface will be preferred over in-hole instruments. Current technology does not, however, allow accurate measurements to be made at great depths. Until such methods become available, downhole measurements will have to be maintained. For these, continuous measuring and transmitting systems (MWD) will be preferred (i.e., steering tools rather than survey tools), particularly if these are combined with the possibility of making a wide range of steering corrections.
-
Smart directional drilling: The committee endorses research efforts that combine geologic inputs with directional information to allow smart drilling, for example, to follow a particular oil-bearing formation at depth, or to seek or avoid stable or unstable, polluted or clean strata for directional services or environmental projects. Research should be undertaken to develop sensor/guidance systems that avoid service lines or other buried structures in the near surface. Ultimately, it may be possible to build "closed-loop" systems that take the appropriate avoiding actions and then return to the predetermined track without operator intervention.
-
Inclined borehole stability: Highly inclined boreholes are inherently less stable than those that are near vertical. This has long been recognized in the petroleum sector and is no less a problem in near-surface drilling. Research should focus on the stabilization of inclined boreholes, particularly in the near surface. The environmental drilling sector will have
-
particular requirements for low-toxicity, minimally invasive methods. Ground freezing while drilling may offer one solution.
-
Directional drilling in poor ground: Near-surface applications must deal with ground that not only is poorly cemented but contains a mix of strong and weak components, such as sand or clay with boulders. Not only does this type of ground give great problems with borehole stability, it also makes maintaining borehole direction extremely difficult, and tool wear in such mixed ground is notorious. Research should be undertaken to study and develop ways to drill satisfactorily in poor ground material.
References
Akiba, T., and Yamada, T., 1989, The Enviliner Microtunnelling system: NO-Dig 89, Fourth International Conference and Exhibition on Trenchless Construction for Utilities, London, ISTT, p. 243-245.
Anon., 1988, Underground microtunnel index: Underground, March, p. 28-31.
Anon., 1989, Horizontal systems growing more specialized, parts I and II: Offshore, v. 49 (Oct./Nov.), p. 36-43.
Anon., 1990, Trenchless technology today: Pipeline and Gas Journal, v. 216 (Feb.), p. 33-36.
Anon., 1992, Nuclear Waste News, v. 12 (7), p. 57.
Anon., 1993a, Pipeline river crossing record set in California: Oil and Gas Journal, v. 91 (5), p. 56.
Anon., 1993b, Statoil claims world record in extended reach: Oil and Gas Journal, v. 91 (7), p. 31.
Anon., 1993c, Texaco claims record for horizontal displacement: Oil and Gas Journal, v. 91 (9), p. 34.
Austin, C. E., Rose, R. E., and Schuh, F. J., 1988, Simultaneous multiple entry hydraulic fracture treatments of horizontally drilled wells: SPE 18263, SPE Annual Technical Conference and Exhibition, Houston, Tex., Oct. 2-5, Richardson, Tex., SPE, p. 811-826.
Barrett, S. L., and Lyon, R. G., 1988, The Navigation Drilling System proves effective in drilling horizontal wells in the Java Sea: SPE 17238, IADC/SPE Drilling Conference, Dallas, Tex., Feb. 28-Mar. 2, Richardson, Tex., SPE, p. 503-510.
BDM International, 1993, Evaluation of Alternative Technologies and Subsurface Confinement Barriers for Single Shell Tanks at Hanford, Morgantown, West Virginia, Report prepared for the U.S. Department of Energy, 226 pp.
Beaumont, T. C., 1989, UK experiences and developments of the Witte microtunelling machines: NO-Dig 89, Fourth International Conference and Exhibition on Trenchless Construction for Utilities, London, ISTT, p. 237-242.
Bosio, J. C., Fincher, R. W., Giannesini, J. F., and Hatten, J. L., 1987, Horizontal drilling—a new production method: 12th World Petroleum Congress, Houston, Tex., April, Chinchester, John Wiley and Sons, v. 3, p. 187-199.
Cooper, G. A., 1994, Directional drilling: Scientific American, v. 270 (5), p. 82-87.
Dawson, R., and Paslay, P. R., 1984, Drillpipe buckling in inclined holes: Journal of Petroleum Technology, v. 36 (10), p. 1734-1738.
Dickinson, W., and Dickinson, R. W., 1985, Horizontal radial drilling system: SPE paper 13949, SPE annual California Regional Meeting, Bakersfield, Calif., May 27-29, Richardson, Tex., SPE, p. 887-892.
Dickinson, W., Anderson, R. R., Dickinson, R. W., and Dykstra, H., 1987, Gravel packing of horizontal wells: SPE 16931, SPE Annual Technical Conference and Exhibition, Dallas, Tex., Sep. 27-30, Richardson, Tex., SPE, p. 519-528.
Dickinson, W., Anderson, R. R., and Dickinson, R. W., 1989, The ultrashort-radius radial system: SPE Drilling Engineering, v. 4 (3), p. 247-254.
Dickinson, W., Dykstra, H., Nees, J. M., Dickinson, E., 1992, The ultrashort radius radial system applied to thermal recovery of heavy oil: SPE Western Regional Meeting, Bakersfield, Calif., March 30-April 1, Richardson, Tex., SPE, p. 585-600.
Eastman, H. J., 1954, Lateral drainhole drilling: The Petroleum Engineer, v. 26 (12), p. B57-B73.
Eaton, N., 1990, Newly developed systems meet demands of coring: World Oil, v. 210 (3), p. 62-66.
Eddison, A., and Symons, J., 1990, Downhole adjustable gauge stabilizer improves drilling efficiency in directional wells: SPE 20454, 65th Annual Technical Conference and Exhibition, New Orleans, La., September 23-26, Richardson, Tex., SPE, p. 509-516.
Edlund, P. A., 1987, Application of recently developed medium curvature horizontal drilling technology in the Spraberry Trend area: SPE 6170, SPE/IADC Drilling Conference, New Orleans, La., March 15-18, Richardson, Tex., SPE, p. 1057-1063.
Fultz, J. D., and Pittard, F. J., 1990, Open hole drilling using coiled tubing and a positive displacement mud motor: SPE 20459, 65th Annual Technical Conference and Exhibition, New Orleans, La., Sep. 23-26, Richardson, Tex., SPE, p. 551-559.
Fultz, J. D., Pittard, F. J., Sawyer, F. D., and Farmer, F. D., 1990, Slim-hole drilling in harsh environments: IADC/SPE 19949, IADC/SPE Drilling Conference, Houston, Tex., Feb. 27-Mar. 2, Richardson, Tex., SPE, p. 333-340.
Gibson, J., 1993, Robbins Co, Kent Wash., Personal communication.
Glagola, M. A., and Wong, L. F., 1986, Aluminum drillpipe for directional drilling: SPE/IADC 14789, IADC/SPE Drilling Conference, Dallas, Tex., Feb. 10-12, Richardson, Tex., SPE, p. 553-560.
Haas, R. C., and Stokley, C. O., 1989, Drilling and completing a well in fractured carbonate, World Oil, v. 204 (4), p. 39-45.
Hair, J. D., 1989a, River crossing technology: Pipeline and Gas Journal, v. 215 (1), p. 29-35.
Hair, J. D., 1989b, Small diameter guided boring systems: Pipeline and Gas Journal, v. 215 (4), p. 18-24.
Hayashi, M., and Miyata, Y., 1989, Okumura—Markham super mini shield tunneling method: NO-Dig 89, Fourth International Conference and Exhibition on Trenchless Construction for Utilities, London,ISTT, p. 231-235.
Hourcard, M., and Bannerman, J., 1990, Beware of sloughing shales overlying horizontal holes: World Oil, v. 211 (1), p. 101-105.
Joshi, S. D., 1987a, A review of horizontal well and drainhole technology: SPE 16868, SPE Annual Technical Conference and Exhibition, Dallas, Tex., Sep. 27-30, Richardson, Tex., SPE, p. 339-354.
Joshi, S. D., 1987b, A review of thermal oil recovery using horizontal wells: In Situ, v. 11 (2/3), p. 211-259.
Joshi, S. D., 1988, A review of horizontal well and drainhole technology: SPE 16868, Rocky Mountain Regional Meeting, Casper, Wyo., May 11-13, Richardson, Tex., SPE, p. 89-108.
Kaback, D. S., Looney, B. B., Corey, J. C., Wright, L. M., and Steele, J. L., 1989, Horizontal wells for in situ remediation of groundwater
and soils: National Water Well Association Outdoor Action Conference, Orlando, Fla., May 22-25, 16 pp.
Karlsson, H., Cobbley, R., and Jaques, G. E., 1989, New developments in short-, medium-, and long-radius lateral drilling: SPE 18706, SPE/IADC Drilling conference, New Orleans, La., Feb. 28-Mar. 3, Richardson, Tex., SPE, p. 725-736.
Keelean, L., Harris, S. S., and Petronio, N., 1989, Short radius drilling technology utilizing mobile service/workover rig: SPE/IADC 18711, SPE/IADC Drilling Conference, New Orleans, La., Feb. 28-Mar. 3, Richardson, Tex., SPE, p. 765-772.
Lattimore, G. M., Carden, R. S., and Fischer, T., 1987, Grand Canyon directional drilling and waterline project: SPE/IADC 16169, SPE/IADC Drilling Conference, New Orleans, La., Mar. 15-18, Richardson, Tex., SPE, p. 1047-1056.
Logan, T. L., 1988, Horizontal drainhole drilling techniques used for coal seam resource exploitation, SPE 18524, SPE 63rd Annual Technical Conference and Exhibition, Houston, Tex., 2-5 October, Richardson, Tex., SPE, p. 711-723.
Logan, T. L., Schwoebel, J. J., and Horner, D. M., 1987, Application of horizontal drainhole drilling technology for coalbed methane recovery: SPE/DOE 16409, SPE/DOE Low Permeability Reservoirs Symposium, Denver, Colo., May 18-19, Richardson, Tex., SPE, p. 195-206.
Lubinski, A., 1950, A study of the buckling of rotary drilling strings: Drilling and Production Practice, API, p. 178.
Makohl, F., and Jurgens, R., 1986, Evolution and differences of directional and high-performance downhole motors: IADC/SPE Drilling Conference, Dallas, Tex., Feb. 9-12, Richardson, Tex., SPE, p. 189-196.
McKenny, F. S., and Knoll, W. G., 1989, Hard rock directional crossings problems solved with new directional drilling systems: NO-Dig 89, Fourth International Conference and Exhibition on Trenchless Construction for Utilities, London,ISTT, p. 211-216.
Millheim, K. K., and Warren, T. M., 1978, Side cutting characteristics of rock bits and stabilizers while drilling: SPE 7518, SPE Annual Technical Conference and Exhibition, Houston, Tex., Oct. 1-3, Richardson, Tex., SPE, v. 7 (4).
Millheim, K. K., and Apostal, M. C., 1981, The effect of bottomhole assembly dynamics on the trajectory of a bit: Journal of Petroleum Technology, v. 33 (12), p. 2323-2338.
Miyazaki, S., 1993, Personal communication.
Moria, H., and Sawaguchi, A., 1989, Microtunelling system with directional control and long distance driving: NO-Dig 89, Fourth International Conference and Exhibition on Trenchless Construction for Utilities, London, ISTT, p. 273-282.
Parsons, R. S., and Fincher, R. W., 1986, Short-radius lateral drilling: a completion alternative: SPE 15943, SPE Eastern Regional Meeting, Columbus, Ohio, Nov. 12-14, Richardson, Tex., SPE, p. 239-250.
Pittard, G. T., Macdonald, W. J., Kramer, S. R., Wasson, M. R., and Herben, W. C., 1987, Development and application of guided horizontal boring equipment for utility applications: NO-Dig 87, Second International Conference and Exhibition on Trenchless Construction for Utilities, London, ISTT, p. 2.5.1-2.5.8.
Pittard, G. T., McDonald, W. J., and Kramer, S. R., 1989, Instrumentation systems for guided boring: NO-Dig 89, Fourth International Conference and Exhibition on Trenchless Construction for Utilities, London, ISTT, p. 191-199.
Ramos, A. B., Fahel, R. A., Chaffin, M., and Pulis, K. H., 1992, Horizontal slim-hole drilling with coiled tubing: an operator's experience: IADC/SPE 23875, SPE/IADC Drilling Conference, New Orleans, La., Feb. 18-21, Richardson, Tex., SPE , p. 289-300.
Rehm, W. A., and Garcia, A., 1989, Horizontal drilling in mature oil fields: SPE/IADC 18709, SPE/IADC Drilling Conference, New Orleans, La., Feb. 28-Mar. 3, Richardson, Tex., SPE, p. 755-764.
Reiss, L. H., 1987, Production from horizontal wells after five years: Journal of Petroleum Technology, v. 39 (11), p. 1411-1416.
Reiss, L. H., Jourdan, A. P. L., Giger, F. M., and Armessen, P. A., 1984, Offshore and onshore European horizontal wells: Paper OTC 4791, Offshore Technology Conference, Houston, Tex., May 7-9, p. 137-144.
Ritchie, J., Enenbach, J., Kleiser, K., and Steutel, M. J., 1989, Use of the FlowMole GuideDril system in Europe: NO-Dig 89, Fourth International Conference and Exhibition on Trenchless Construction for Utilities, London, ISST, p. 283-289.
Robbins Co., 1993, Operating instructions for model 167-266/267 TBM: Robbins Co. Kent, Wash., p. 2.21-2.40.
Schuh, F. J., 1989, Horizontal well planning—build curve design: SPE 20150, Petroleum Technology into the Second Century, New Mexico
Tech, Socorro, N. Mex., Oct. 16-19, Richardson, Tex., SPE, p. 47-61.
Shale, L., 1991, Development of air drilling motor holds promise for specialized directional drilling applications : SPE 22564, SPE 66th Annual Conference and Exhibition, Dallas, Tex., Oct. 6-9, Richardson, Tex., SPE, p. 275-286.
Sheikholeslami, B. A., Schlottman, B. W., Sidel, F. A., and Button, D. M., 1989, Drilling and production aspects of horizontal wells in the Austin chalk: SPE 19825, SPE Annual Technical Conference and Exhibition, San Antonio, Tex., Oct. 8-11, Richardson, Tex., SPE, p. 575-590.
Spiekhout, J., 1991, Developments in directional drilling: Pipeline and Gas Journal, v. 215 (4), p. 54-57.
Spiekhout, J., Gorter, J., and Hartlief, W. H., 1993, Records set, drilling calculation refined in Dutch pipeline crossings: Oil and Gas Journal, v. 91 (1),p. 33-38.
Stacey, E. S., Rogers, C. T., Bowman, J. K., Noblett, B. R., and Cooney, M. F., 1992, Case history of a horizontal well using a high angle pilot hole: IADC/SPE 23880, IADC/SPE Drilling Conference, New Orleans. La., Mar. 18-21, Richardson, Tex., SPE, p. 331-340.
Stangl, G. A., Lee, D. W., and Wassen, M. R., 1988, Extended range horizontal boring using the TrueTrac directional boring system: NO-Dig 88, Third International Conference and Exhibition - Achievements in Trenchless Methods, Washington, D.C., ISTT, p. 319.
Stangl, G. A., and Boeckman, W. G., 1989, Field experiences with directional rod pushers: NO-Dig 89, Fourth International Conference and Exhibition on Trenchless Construction for Utilities, London, ISTT, p. 261-272.
Stormont, D. H., 1953, Increased drainage of oil into well by drainhole drilling: Oil and Gas Journal, v. 52, (11),p. 105-108.
Szczupak, J. R., 1989, Horizontal directional drilling applications: NO-Dig 89, Fourth International Conference and Exhibition on Trenchless Construction for Utilities, London, ISTT, p. 201-210.
Tolle, G., and Dellinger, T. B., 1986, Mobil identifies extended reach drilling advantages, possibilities in North Sea: Oil and Gas Journal, v. 84 (21),p. 78-86.
White, C. W., 1989, Drilling and completion of a horizontal lower Spraberry well including multiple hydraulic fracture treatments: SPE
19721, 64th Annual Technical Conference and Exhibition, San Antonio, Tex., Oct. 8-11, Richardson, Tex., SPE, p. 205-210.
Whiteley, M. C., and England, W. P., 1985, Air drilling operations improved by percussion bit/hammer tool tandem: SPE/IADC 13429, SPE/IADC Drilling Conference, New Orleans, La., Mar. 6-8, Dallas, Richardson, Tex., SPE, p. 61-70.
Wilson, R. C., and Willis, D. N., 1986, Successful high angle drilling in the Statfjord field:SPE 15465, 61st SPE Annual Technical Conference and Exhibition, New Orleans, La., Oct. 5-8, Richardson, Tex., SPE, 14 pp.
Yost, A. B., Overbey, W. K., and Carden, R. S., 1987, Drilling a 2000-ft. horizontal well in the Devonian shale:SPE 16681, SPE Annual Technical Conference and Exhibition, Dallas, Tex., Sep. 27-30, Richardson, Tex., SPE, p. 291-302.