Use of Materials Balances to Estimate Aggregate Waste Generation in the United States
Robert U. Ayres and Leslie W. Ayres
One can view each industrial sector as a transformation process, where raw material inputs or purchased commodities from upstream sectors and "free goods" from the environment are converted into products for downstream sectors and wastes. This conversion process is subject to the materials-balance constraint not only in the aggregate, but also element by element. In other words, the sum of the weights of all inputs must exactly equal the sum of the weights of all outputs. When both inputs and outputs are known, it is possible to estimate wastes, making due allowance for processes utilizing the free goods (i.e., air, water, topsoil). Of course, in reality, there are often significant uncertainties with regard to either inputs or outputs, or both. These arise from statistical inconsistencies, stock adjustments, imports, and exports. In other work, we have attempted to take all of these into account.
It is important to explain what we mean by macrolevel in this context. In general, large-scale mass flows exceed by many orders of magnitude the flows of the most highly toxic pollutants, including trace elements. In our balancing efforts, we have attempted to construct input-output tables for major process stages. Thus, in the case of agriculture and forest products, we try to balance the flows of carbon, oxygen, hydrogen, and major nutrients. At this level of detail, it is not possible to account precisely for minor flows (e.g., of pesticide residues). Studies accounting for minor flows would have to use different methodology based much more on detailed chemical and metallurgical process data than on economic data.
To avoid unnecessary and distracting biological complications, we treat biomass as a produced good of the agricultural and forestry sectors, even though much of it is arguably free. Unfortunately, this leaves us with the problem of
accounting for water, as both an input and output, which cannot be done with great precision. Fortunately, great precision is probably not necessary in this case. Labor and capital inputs, such as machinery, and fuel or electric power for operating the machinery, are not considered explicitly in this paper. However, it should be borne in mind that a considerable fraction of aggregate industrial output is actually capital (and operating) input to other sectors.
Our immediate intention is to classify outputs as either economic commodities or missing mass. In subsequent work, the ''missing mass" will be further classified based on the level of waste treatment and final disposal medium (air, water, or soil). This means we need to be quite careful in accounting for the consumption of oxygen (from air) in oxidation processes and for the consumption or production of water in hydration, dehydration, dilution, dissolution, and so on. We selected 1988 as the year of reference for this study because it was the last year for which we had reasonably good international data at the time we began the work. Unfortunately, 1988 was a very atypical year for U.S. agriculture, as we note below.
Agriculture1
Inputs to the agriculture sector consist of sunlight, water, carbon dioxide from the air, nitrogen fixation also from the air, topsoil, and some chemicals (e.g., fertilizers and pesticides). Commodity outputs are harvested crops. (Dairy products and meat are considered separately in the next section.) Missing mass, in the aggregate, consists mainly of crop wastes, runoff, evapotranspiration, and oxygen, a by-product of photosynthesis. Other losses include soil erosion, nitrogen (and phosphorus) carried away by water sources, and gaseous emissions.
The production process in agriculture (and also forestry, considered below) can be estimated crudely from the following basic equation of photosynthesis:
CO2 + H2O + photon ⇒ CH2O + O2.
Plants fix carbon in daylight and release part of it (about half) at night. Water carries nutrients and metabolic products and provides evaporative cooling. There is a rough average proportionality between carbon fixation rate (gross photosynthesis) and evapotranspiration, but there is no fixed relationship between water content and metabolic process; some plant parts are very high in water content, others much less so. In general it seems reasonable to assume that raw biomass contains 50 percent water by weight on average, whereas refined or processed food or feed commodities are considerably drier. In cases where actual data are lacking, we assume 25 percent water content for processed "dry" commodities. Unfortunately, official statistics are not informative on this point.
Raw products of U.S. agriculture include truck crops (fruits, vegetables), tree crops, and field crops (grain, oilseed, hay and alfalfa, sugar beets, sugar cane,
TABLE 1 Agricultural Production in the United States, 1988 (million metric tons)
|
Production |
Consumption |
||||
Commodity |
Raw |
Finished |
Exports |
Imports |
Raw |
Finished |
Beef and veal |
17.82 |
10.88 |
0.31 |
1.09 |
11.62 |
11.20 |
Lamb and mutton |
0.32 |
0.15 |
0.00 |
0.02 |
0.18 |
0.18 |
Pork |
9.91 |
7.11 |
0.09 |
0.52 |
7.51 |
4.87 |
Poultrya |
12.95 |
|
|
|
|
6.37 |
Eggsb |
4.44 |
|
|
|
|
3.86 |
Dairy products |
65.86 |
64.41 |
|
|
|
64.41 |
Subtotal |
111.30 |
|
2.77 |
1.26 |
|
59.90 |
Food grainsc |
56.55 |
|
44.26 |
|
35.40d |
17.37 |
Feeds and fodders |
|
|
11.37 |
|
|
|
Feed grains and productse |
147.06 |
|
55.21 |
|
|
|
Oilseeds and productsf |
49.16 |
|
26.90 |
|
|
|
Hay |
114.31 |
|
|
|
|
|
Sugar cane |
27.13 |
2.88 |
|
1.21 |
|
3.40 |
Sugar beets |
22.51 |
2.97 |
|
|
|
3.40 |
Other field productsg |
5.03 |
|
1.57 |
|
|
3.46 |
Corn syrup |
|
|
|
7.64 |
|
|
Subtotal |
421.75 |
139.31 |
|
|
|
35.27 |
Vegetables |
25.14 |
|
|
|
|
22.27 |
Potatoes |
16.17 |
|
|
|
|
14.77 |
Fruits |
25.60 |
|
|
|
|
11.51 |
Nuts |
0.55 |
|
|
|
|
|
Fruits, nuts, and vegetables |
4.06 |
6.74 |
|
|
||
Coffee, cocoa |
|
|
1.48 |
|
|
3.40 |
Subtotal |
67.47 |
|
4.06 |
8.21 |
|
51.94 |
Fish |
3.26 |
|
0.48 |
3.37 |
4.77 |
1.40 |
Vegetable oils |
|
6.40 |
1.30 |
1.35 |
|
6.66 |
SUMMARY |
||||||
Animal products |
111.30 |
|
2.77 |
1.26 |
|
90.87 |
Field products |
421.75 |
|
139.31 |
|
|
35.27 |
Vegetable products |
67.47 |
|
4.06 |
8.21 |
|
51.94 |
Fishery products |
3.26 |
|
0.48 |
3.37 |
|
1.40 |
Vegetable oils |
6.40 |
|
1.30 |
1.35 |
4.77 |
6.66 |
TOTAL |
603.71 |
|
147.92 |
14.19 |
|
186.15 |
a Poultry conversion at $0.33/lb. b Egg conversion at 0.77 kg/dozen. c Food grains = wheat, rice, rye. d The difference in consumption of raw and finished food grains is used for beer and distilled spirits. e Feed grains and products = corn and sorghum for grain, barley, oats. f Oil seeds and products = soy beans, peanuts, cottonseed, flax seed. g Other field products = dry beans and peas, cotton lint, tobacco. NOTE: Table does not display stock changes, particularly large in 1988. SOURCES: Bureau of the Census (1990, 1991) and United States Department of Agriculture (1990, 1991). |
potatoes, cotton, tobacco). Harvested output of all field crops, including hay, in 1988 was 421.75 million metric tons (MMT).2 Truck crops totaled 67.5 MMT. Total weight of harvested crops was 489 MMT (Table 1).3 It should also be noted that corn plants harvested whole for silage, or "hogged" on the farm, are not included in the grain production figures. This material, which is fed to animals, is classed as "harvested roughage"; it amounted to 68 MMT in 1988. Total biomass harvested by humans and animals including grazing was 885 MMT.
According to one estimate, the average ratio of above-ground crop residues remaining on the land to harvest weight is about 1.5 for cereals (straw), 1.0 for legumes (straw), 0.2 for tubers (tops) and sugar cane (bagasse), and 3.0 for cotton (stalks) (Smil, 1993). On this basis, total residues left above ground in 1988 would have been around 400 MMT. Total above-ground biomass production was about 1,285 MMT. In the United States, most of the crop residues are left on the land; a small fraction, about 20 percent, is burned for fuel or used for other purposes (Smil, 1993). (In China and India, by contrast, as much as two-thirds of crop residue production is burned as fuel in household cooking.)
Biomass is a mixture of cellulosic fiber, carbohydrates, fats, proteins, and water, the latter accounting for about 50 percent by weight. Hence, we estimate that the dry weight of the biomass produced in 1988 was about 642 MMT. For each 100 units of dry output (CH2O basis), the photosynthetic process equation implies that 146.7 MMT CO2 (containing 40 units of carbon) were initially extracted from the air, 60 units of water were converted, and 106.7 units of oxygen were returned to the atmosphere. Overall, for 1988, water inputs—not including water required for evapotranspiration—were about 1,027 MMT, and carbon dioxide inputs were about 1,002 MMT. Oxygen produced by the photosynthesis process in agriculture would have been about 685 MMT. The overall flows for U.S. agriculture in 1988 are summarized graphically in Figure 1.
One other air pollutant, methane, is worth mentioning. Most animals have anaerobic organisms in their guts that convert a small amount of the food they consume into methane, typically 1-2 percent on an energy basis. However, this percentage is larger for cattle and sheep, ranging from 5.5 to 7.5 percent, depending on the quality and quantity of feed. Taking these factors into account, Crutzen et al. (1986) have estimated annual methane output of 60 kg per head of cattle and 8 kg per head of sheep. The U.S. cattle population in 1988 was 99.6 million; the sheep population was 10.5 million. Methane emissions from these sources amounted to 0.68 MMT.
It should be noted that the agricultural sector uses large amounts of fertilizers and pesticides. The nitrogen (N) content of ammonia used for fertilizer consumed domestically was 11.2 MMT in 1988, or 76 percent of all the synthetic ammonia produced in the United States that year. Large quantities of urea (about 0.33 MMT), a fertilizer material, are also used for animal feed supplements. Domestic agriculture consumed 33.5 MMT of phosphates containing 10.8 MMT P2O5. Many of these substances find their way directly or through animal excreta into surface water and groundwater. Much of the N content of animal feed ends up in
urine, either on pastures or at feedlots, resulting in both air and water pollution. We do not have an accurate estimate of the quantities involved, but probably two-thirds of the urine is generated at feeding stations.
Fertilizers and pesticides, direct chemical inputs to agriculture, are not counted explicitly as pollutants, although their use results in pollution. Animal wastes are a major pollution problem, especially in the vicinity of animal feedlots and large-scale poultry producers. Of 100 units of nitrogen in fertilizer, roughly 50 are taken up by harvested crops, of which 47 are subsequently consumed by animals, and 42 of these are eventually excreted as waste (Crutzen, 1976). Most of this waste is generated at feedlots because fertilizer is seldom used on grazing land, and the nitrogen uptake by grazing animals is largely left behind as manure or urine. About 24 units of nitrogen find their way to rivers, lakes, and groundwater, of which 10 units are direct runoff from the soil, 8 come from animal excreta at feeding stations, and 6 from human sewage. Thus, about 18 percent of nitrogen in agricultural fertilizer reappears within a few weeks or months as waterborne pollution, although only 10 percent is due to direct fertilizer loss. Because 11.5 MMT N were used in fertilizer and feed supplements in 1988, this implies an overall waterborne nitrogen-waste flow of 2.76 MMT.
Schlesinger and Hartley (1992, table 4) estimated annual NH3 emissions per head at 15.5 kg from cattle and horses, 2.4 kg from sheep, 2.35 kg from pigs, and 0.21 kg from poultry. Based on 1988 populations of 99.6 million cattle, 55.5 million pigs, 10.9 million sheep and lambs, and 5.7 billion chickens and turkeys, this totals 2.91 MMT. Fertilizer itself is also a source of ammonia emissions; the emission factors for urea and ammonium sulfate spread on the soil surface are estimated at 0.2 and 0.1, respectively; for other fertilizers—including anhydrous ammonia injected directly into the soil—the emission rate is lower (around 3 percent) (Schlesinger and Hartley, 1992). In 1988, 2.49 MMT N in urea were used as fertilizer in the United States along with 0.340 MMT of nitrogen in ammonium sulfate and 6.84 MMT N from other sources. Altogether, animal metabolism and fertilizer use generated nitrogen emissions of 3.79 MMT (as ammonia). This represented nearly 33 percent of the 11.6 MMT (N content) of ammonia equivalent that was used as fertilizer. Of this, about 8 percent was a direct loss.
The rest of the nitrogen unaccounted for in the applied fertilizer (about 32 percent) is embodied in root and stem material that is not harvested or is harvested directly by animals and remains with the soil (20-25 percent), or is reconverted to nitrogen gas and returned to the atmosphere by denitrifying bacteria in the soil (5-10 percent). For every 16 units of nitrogen emitted as N2, on average 1 unit is emitted as N2O, a potent greenhouse gas, but these emissions tend to be episodic. Recently, the use of nitrogenous fertilizer has come to be recognized as one of the major sources of N2O buildup. Worldwide, an estimated 0.7 MMT N2O are emitted annually from this source (Schlesinger, 1991). The United States was responsible for roughly one-eighth of worldwide nitrogenous fertilizer use in
1988 and probably a similar proportion of N2 Oemissions, together the equivalent of 0.055 MMT N content.
The above estimates do not take into account the relatively small quantities of other chemical elements embodied in the crops, notably nitrogen, phosphorus, and other minerals taken up from the soil or, in the case of nitrogen, fixed by bacteria. It is of interest, however, that the three major chemical elements in dry plant tissue are carbon, hydrogen, and oxygen, which account for 95 percent of the total mass. Nitrogen accounts for another 2 percent, phosphorus for 0.5 percent, potassium for 1 percent, and sulfur for 0.4 percent. These are the major nutrients that are depleted by harvesting and must be replaced by the addition of fertilizers. The remaining 1 percent of plant mass consists of other mineral elements (Table 2) that are readily available from the soil. The flows of nutrients (nitrogen and phosphorus) in U.S. agriculture are summarized in Figure 2.
In 1988, 133 MMT of grain, vegetables, and oilseeds (mostly soya beans) were exported, not including 11.4 MMT of "feeds and fodders," which are from the processing sector. The remainder was consumed directly or indirectly within the United States. Final consumption of all food products (not including beverages) for 1988 was 186 MMT, plus about 20 MMT for grain-based beverages, alcohol, cotton, wool, and other products. Indirect consumption (as animal feed) accounted for most of the difference between gross production and final consumption.
According to the U.S. Department of Agriculture (USDA) (1992), U.S. livestock in 1988 were fed 119.4 MMT of feed grains and 3.7 MMT of food grains
TABLE 2 Chemical Composition of Plants
Element |
Percent by Weight |
Oxygen |
45 |
Carbon |
44 |
Hydrogen |
6 |
Nitrogen |
2 |
Potassium |
1 |
Calcium |
0.6 |
Phosphorus |
0.5 |
Sulfur |
0.4 |
Magnesium |
0.3 |
Manganese |
0.05 |
Iron |
0.02 |
Chlorine |
0.015 |
Zinc |
0.01 |
Boron |
0.005 |
Copper |
0.001 |
Molybdenum |
0.0001 |
Total |
99.9011 |
(mostly wheat). Other harvested animal feeds included 123 MMT of hay and alfalfa, 4.76 MMT of sorghum as silage, and approximately 68 MMT of harvested roughage (such as cornstalks) mixed with other feeds, for a total of 319 MMT of harvested feeds. By-products of the food processing industry such as grain mill by-products (e.g., gluten), oilseed meal, brewers and distillers dried grains, meat and fish meal, dried milk, dried beet pulp, and molasses accounted for an additional 33.4 MMT of animal feeds (United States Department of Agriculture, 1992, table 3).4 Assuming animal intake of pasturage (mainly by cattle) to be about 200 MMT, we can account for total animal feed consumption in 1988 of 552.4 MMT, not including water, salt, urea, or other minor inputs.
Animal feed concentrates in the United States average 79 percent digestibility. From this, we can conclude that 21 percent of the mass of animal feed concentrates (156.3 MMT) fed to dairy cattle, beef cattle in feedlots, hogs, and poultry is passed through immediately in feces. Harvested roughage, or silage and hay (196 MMT), has lower digestibility, probably around 60 percent. This implies 40 percent passes through in feces. Therefore, annual manure output from on-farm and industrial animal feeding operations amounts to about 100 MMT. In addition, USDA (1992) estimates that animal intake from pastures is about 200 MMT. Assuming 60 percent digestibility, roughly 80 MMT of manure is probably left on pastures. This figure could be too low; the digestibility of pasturage may be as low as 40 percent.5
Of the total annual manure output of about 180 MMT, it appears that 100 MMT is generated in confinement, and of this, 75 percent (75 MMT) is probably recycled to croplands (Smil, 1993). The remainder of the manure from feedlots (25 MMT, about 50 percent water) is lost to runoff or in other ways. The 80 MMT of manure left on pastures is returned directly to the soil—but not to croplands per se—and does not constitute a waste.
As to the outputs of the livestock sector, a total of 111.3 MMT can be accounted for as the gross weight of animal carcasses and dairy products produced for the market. (See below.) Adjusting for the "excess" water content of raw milk (87 percent water), we assume that the sector produces about 81 MMT of equivalent animal products having the same average moisture content as feeds (50 percent). As noted above, feed inputs equal 552 MMT and manure outputs (50 percent moisture basis) are 180 MMT. Simple arithmetic (552 - 180 - 81) reveals that 291 MMT are lost through metabolic (respiration) processes.
An estimated 50 percent of this lost mass (approximately 145 MMT) is carbohydrate (CH2O) metabolized for energy. This implies that animals consume 155 MMT (1.067 x 145) of oxygen and produce 213 MMT (1.47 x 145) CO2. The oxidation process also generates 87 MMT (0.6 x 145) of water as vapor in addition to the 115 MMT of water contained in the feed and not otherwise accounted for. Most of this ends up in manure or urine. The water balance is more complicated, of course, because we have not allowed for the water consumed and re-excreted by the animals.
The greatest mass movement from agriculture is the loss of topsoil due to wind and water erosion. A detailed study of topsoil loss in agriculture was carried out by the U.S. Soil Conservation Service in 1982 (Brown and Wolf, 1984). The study found that 44 percent of U.S. cropland was losing topsoil at an unsustainable rate (i.e., faster than the natural rate of soil formation). Topsoil loss in 1982 was estimated at 1,530 MMT. This amount of loss can be assumed to be roughly constant year to year, although optimists believe that the erosion-loss rate is declining as a consequence of increasing use of no-till methods of cultivation. Also, it must be pointed out that eroded material is not necessarily carried out to sea; it may be redeposited on the same field or in the bed of a nearby stream.
To summarize, we estimate overall annual waste from U.S. agriculture as follows: topsoil erosion, 1,500 MMT; undigested and unrecycled feedstuffs (feces) from animals at feeding stations (not including grazing animals on pastures), 25 MMT (50 percent moisture) or 12.5 MMT (dry weight). The latter is mostly undigested cellulose, but includes about 4 percent (0.5 MMT) nitrogen and 1 percent (0.125 MMT) phosphorus. Urine apparently accounts for roughly 42 percent of the total nitrogen content of synthetic fertilizer, or about 4.8 MMT; but this is only the fertilizer contribution. The total must be about three times higher. About a quarter of this (1.2 MMT from fertilizer, 4 MMT total) is volatilized immediately as ammonia; around 2.8 MMT from fertilizer (9 MMT total) ends up in watercourses; the rest goes into groundwater or is recycled back to the land. Ammonia emissions to the atmosphere, direct from fertilizer use, seem to be about 1 MMT N, or 10 percent of inputs, but volatilization losses from manure and urine add another 4 MMT. Other sources (organic decay) add a further contribution. The total for U.S. agriculture is probably around 6.5 MMT per year. Methane emissions to the atmosphere from grazing animals in the United States were apparently about 0.68 MMT (Figure 1). A rough balance for nitrogen and phosphorus is shown in Figure 2.
Food and Feed Processing6
The food and feed processing sectors entail a number of activities, including grain and oilseed milling, meat and dairy processing, cotton processing, oil products, sugar production, fermentation industries, baking, confectioneries, and canning and freezing. Unfortunately, USDA does not clearly separate these activities or identify their inputs and outputs.
We estimate inputs to the food processing sector (361 MMT) as the gross agricultural production of harvested crops (489 MMT) less harvested crops fed to animals (123 MMT grains and 114 MMT hay) less exports (excluding exports from stockpiles, 133 MMT), plus animal products (111 MMT), fish (3.3 MMT), and net imports of foodstuffs (14 MMT).
The consumption of domestic food products (flour, prepared cereals, pack-
aged rice, etc.) from all grain mills in 1988 amounted to 17.37 MMT. This does not include grain consumed by the fermentation industries, which produce both alcoholic beverages and fuel alcohol. We estimate that about 19 MMT of grains, mostly corn, were used for fermentation products in 1988. In addition to grain products, 6.4 MMT of vegetable oils and 7.64 MMT of corn syrup were produced by grain and oilseed mills. The fermentation industries, in turn, produced 2.2 MMT of beverage alcohol and 5 MMT of ethanol for fuel, 1 MMT of animal feed concentrates, and an estimated 1 MMT of beverage carbohydrates. To make up the balance, we estimate outputs of 7 MMT CO2 and 3 MMT of water vapor.
Cotton is a major agricultural product that contributes little to feed and nothing to food. In 1988, the United States produced a net of 9.2 MMT of raw cotton. This was ginned to yield 3.36 MMT of cotton fiber (lint), 5.5 MMT of cottonseed, and 0.27 MMT of linters. Linters are a fibrous material used for felting and cellulosic chemical manufacturing and so are not wasted. The cottonseed was allocated to mills and "other uses," including exports. Mills purchased 4.38 MMT of seeds, of which 3.38 MMT were actually crushed (United States Department of Agriculture, 1992, table 141). The mill product was 0.56 MMT of oil, 1.53 MMT of high-protein cottonseed oilcake, used for animal feed, and 1.29 MMT of milling waste. (The latter is included with overall milling waste in Figure 1.)
Sugar cane weighing 27.13 MMT was reduced to 2.88 MMT of refined cane sugar; similarly, sugar beets weighing 22.51 MMT yielded 2.97 MMT of beet sugar. (About 0.69 MMT of lime was also used in the latter process.) Sugar refining also yielded about 0.59 MMT of molasses (equivalent dry weight), mostly fed to animals. The remainder of the sugar cane waste was mostly cellulosic bagasse. The sugar beet process produces large quantities of pulpy material; about 1 MMT (dry) of this was used for animal feed in 1988 (United States Department of Agriculture, 1992, table 73). The mass disappearance from these two processes alone amounted to about 42.1 MMT. At least half of this mass loss, perhaps as much as 60 percent, or 25 MMT, is water vapor from the various evaporation stages in sugar production. The remaining dry mass is probably burned for energy recovery, although some residues may be discharged into rivers by sewage plants.
Truck crops (vegetables and berries) and tree crops (fruits and nuts) accounted for a harvest weight of 67.5 MMT. Exports took 4.06 MMT and imports added 8.21 MMT, for a total domestic supply of 71.6 MMT. Final consumption, on an as-purchased basis accounted for 51.9 MMT. The difference, 20 MMT, was presumably waste, at both food processing plants and retail stores. We estimate that 60 percent of this mass loss (12 MMT) was evaporative water loss from freeze-drying (e.g., of orange juice) and other processing. The bulk of the food process waste goes into waterways or municipal waste facilities. Some is recovered for other uses, and a small amount may be burned for energy.
Animal products in the United States can be divided into red meats, poultry, and eggs and dairy. The live weight of animals slaughtered for red meat in 1988
was 28.05 MMT. Salable weight of red meat, after processing, was 18.14 MMT, a reduction of roughly 10 MMT, or nearly 36 percent. By-products of meat processing include lard and tallow (about 3.8 MMT),7 hides (1.02 MMT undressed),8 dog and cat food, glue, bone meal, blood meal, meat meal, and tankage. The last two items are utilized in animal feed concentrates (2.3 MMT in 1988; United States Department of Agriculture, 1992, table 73). About 2.7 MMT remains unaccounted for. Some of this may be pet food, for which we have no explicit data. We conjecture that most of the missing mass is evaporative water loss in the production of meals and concentrates.
Exports of red meat products in 1988 amounted to 0.4 MMT, and imports, mostly of beef, amounted to 1.63 MMT. Thus, domestic supply of red meat was 19.37 MMT. However, final consumption of meat (''as purchased") was only 16.25 MMT. The difference of 3.16 MMT is waste fat and bone, largely generated by meatcutters in retail shops. This waste ends up ultimately in municipal landfills.
In the case of poultry, live weight was 12.95 MMT in 1988. Dressed carcass weight of poultry for the United States was either 9.5 MMT or 10.07 MMT.9 This implies a by-product and waste flow at the processing plant of 3.0-3.5 MMT, part of which (2.0-2.5 MMT) is probably recycled as animal feed. The rest, mostly feathers, is dumped or burned. Final consumption of poultry ("as purchased") was 6.37 MMT in 1988. Thus, a further loss of 3.1-3.5 MMT presumably occurred at the retail level. The latter ends up in municipal landfill or in waterways (as biological oxygen demand).
The grain and oilseed milling sector is rather complex. Marketed grain and oilseed milling products consist of vegetable oils (6.4 MMT), flour (17.4 MMT), and corn syrup (7.6 MMT), a total of 31.4 MMT. The imputed output of feed concentrates, by this calculation, is 30.8 MMT (62.2 - 31.4). (We calculated above that 31.6 MMT must have been produced. The match is quite close.)
In summary, we have identified mass losses from the domestic food processing sector as follows: grain and oilseed milling, 9.7 MMT; fermentation, 3.0 MMT; sugar milling, 42.7 MMT; vegetable and fruit canning and freezing, 20.7 MMT; meat and poultry packing, 1.0 MMT (plus about 6.3 MMT in retail shops); dairy processing, 26.1 MMT; egg marketing, 0.6 MMT; and fish packing and retailing, 4.6 MMT. For the sector as a whole, including retail shops, losses total 110 MMT, plus an additional 6.8 MMT of carbon dioxide from fermentation. However, some of this lost mass was not wasted but was converted into animal feeds.
Of the 110 MMT of mass disappearance identified in 1988 (Figure 1), it appears that at least 66.2 MMT consisted of water vapor from evaporative processes in the manufacture of cheese and dried milk products, sugar and corn syrup production, drying and freeze-drying of fruits (such as oranges for juice, prunes, and raisins), and from the production of meat meal and fish meal. An additional 34.5 MMT of mass loss was solid waste of vegetable origin from sugar beets and
sugar cane, fruits and vegetables, and grain milling. Some of this consisted of fruit and vegetable skins and stems, nut shells, pits and seeds, inedible leaves, spoilage, and so forth. Usually, these wastes would be generated in quantities too small to be dried and burned efficiently. However, of the dry sugar and grain milling losses (about 27 MMT) a small amount (about 0.1 MMT) was fed to animals. The same was true for part of the missing mass (11.6 MMT) from meat and fish processing.
Even the bulky and "dry" food processing wastes still contain quite a bit of water, probably about 25 percent. If the 27 MMT of bulky combustible waste biomass of vegetable origin is assumed to have been burned for energy recovery, and if the 20 MMT in dry mass is assumed to be chemically similar to cellulose, the CO2 generated would be around 29.4 MMT, consuming about 21.3 MMT of oxygen and producing about 12 MMT of water vapor in addition to the 7 MMT embodied in the organic material. Of course, the same amount of CO2 would be generated by natural decay processes, as long as they occur in aerobic conditions.
The material losses that we have identified as likely waste are "dry" in the sense that they do not include the weight of washing, cooking, or process water. They also do not assume a priori mass reduction by combustion of biomass for energy recovery. In this connection, a survey by Science Applications International Corporation (SAIC) (1985) commissioned by the U.S. Environmental Protection Agency (EPA) attempted to identify dry wastes from the industrial sectors. The SAIC estimate of dry weight of wastes from the food and feed processing sector was 6.3 MMT (based on 1976 data). This strongly suggests that combustible wastes were, in fact, mostly burned for mass reduction. A significant fraction of the incombustible organic wastes of animal origin (9.3 MMT) and vegetable origin (7.1 MMT) were actually downstream in the retail sector. Thus, our analysis is consistent with SAIC's results.
Forestry and Wood Products10
Wood products are derived from timber tracts, which belong to the forestry sector or are leased from government. As in the case of agriculture, the primary inputs are land, water, and carbon dioxide from the air. Major outputs are timber and oxygen; minor outputs include gums, barks, and maple sap. Several important natural resins and solvents (e.g., turpentine, "naval stores") are derived from gums. Downstream chemical products based on wood distillates include acetone, methyl alcohol, pine oil (pinenes), terpenes, tall oil, and tanning extracts.
Neglecting the minor products, we can construct a rough mass balance for the timber tracts. The data given below imply that the total mass of raw product that was harvested in 1988 was 342 MMT on an air-dried (15 percent moisture) basis, which implies a dry weight of 290 MMT, of which 2 percent consisted of mineral "ash" (see below) and the remainder, 284 MMT, was roughly equivalent to cellulose. The calculated carbon content is thus 114 MMT, which requires an
input of 367 MMT of carbon dioxide from the air and 163 MMT of water for photosynthesis. Total oxygen generated was 206 MMT. Assuming the timber had an original moisture content of 48 percent, total water input must have been 545 MMT. Subtracting the water content of the air-dried wood output (51 MMT) from the original water content of the harvested roundwood (268 MMT) implies a water loss from wood dehydration of 217 MMT.
Trees have an estimated carbon-nitrogen-phosphorus ratio of 800:10:1 (Deevey, 1970). Because most of the nutrients are embodied in the bark and foliage, this is an overestimate for harvested wood. However, if it were correct, the nitrogen content of the wood removed from the forests would be on the order of 1.5 MMT, while the phosphorus content would be on the order of 0.15 MMT. As noted below, the phosphorus content of wood ash is about 1 percent, and the ash itself amounts to 2 percent of the total mass of undebarked wood. This implies a total mineral, or ash, content of 6 MMT for the wood harvested and a probable phosphorus content on the order of 0.06 MMT, which is only 40 percent of the loss rate implied by the Deevey C:N:P ratio. Not all of this ash is removed from the forest as some debarking operations are carried out at the logging site.
The total mass of roundwood consumed by U.S. lumber and plywood mills in 1988 was 155.8 MMT. The mass of lumber produced in 1988 was about 49.7 MMT (Ulrich, 1990, table 7). The mass of plywood and veneer produced was 11.1 MMT; hardboard, insulating board, and particleboard amounted to 8.8 MMT. Total processed wood products added up to 69.6 MMT. Allowing for 43.7 MMT of wood chips from lumber mills used for pulping, exports of 6.9 MMT, 11.8 MMT to other uses, and fuel use of 25.8 MMT, there were 4.9 MMT of unutilized waste, equal to about 3 percent of inputs.
The total weight of inputs to pulp was 142.6 MMT, which consisted of just over 105.7 MMT in domestic pulpwood, and 43.7 MMT in chips from lumber mills. U.S. domestic woodpulp production in 1988 was 57.9 MMT (Bureau of the Census, 1991, table 1195).11 Domestic production of pulp was essentially entirely from domestic resources.12 Net U.S. exports of woodpulp in 1988 were 0.535 MMT, while chemical uses of dissolving-grade pulp amounted to 1.24 MMT. However, virgin pulp available for domestic paper production was 56.8 MMT. There is a small statistical discrepancy of 0.7 MMT.
Wastepaper collected for recycling in 1988 was reported to weigh 23.8 MMT.13 To obtain a match between inputs and outputs of the paper sector, we calculate that 17.7 MMT of recycled pulp must have been consumed, of which 4.9 MMT was from internal waste and the rest was postconsumption wastepaper. Allowing for internal recycling, exports, and other uses, 14.2 MMT of wastepaper would have been repulped. About 10 percent (1.4 MMT) of this mass, consisting mostly of inorganic fillers and coatings, would have been lost in the repulping process (United States Congress, Office of Technology Assessment, 1984, figure 24), leaving 12.9 MMT as secondary pulp for paper and paperboard production. Thus, total domestic pulp supply, including internal recycling, was
around 74.9 MMT in 1988. Adding 5 MMT of fillers and other chemicals14 and subtracting 4.9 MMT for internal recycling implies that domestic output of paper and paper products that year was 75.1 MMT.
United Nations data for pulp are subdivided by pulping process (United Nations Statistical Office, 1988). Mechanically produced pulp (5.39 MMT) was virtually entirely used for newsprint, of which domestic production was 5.36 MMT. The other pulp types were, in decreasing order of quantity, sulfate or Kraft pulp (43.53 MMT), semichemical pulp (3.95 MMT), and sulfite pulp (1.415 MMT). Dissolving-grade pulp for chemical use (e.g., in rayon manufacturing) amounted to 1.24 MMT. Again, there is a discrepancy between U.N. and U.S. statistics.
The 142.6 MMT of pulping feeds contained around 21 MMT, or 15 percent, moisture. The 57.9 MMT of pulp output included only 5.8 MMT, or 10 percent, moisture. Overall, then, the apparent mass disappearance between pulpwood and pulp in 1988 was 92.2 MMT, of which 15.2 MMT (21 - 5.8) was presumably water. This would have left 77 MMT bone-dry weight of waste, including ash and chemicals. The bone-dry organic wastes (70 MMT) consisted of lignin, hemicelluloses, and resins. Small amounts of lignin were recovered for use as lignosulfonates; virtually none of the hemicelluloses were recovered for chemical use.15
Most of the waste organic material was burned on site to recover energy and chemicals. We do not have data for 1988, but in 1991, the American Forest and Paper Association (AFPA) estimated that 75.3 MMT of the dry waste organic material content of "black liquor" was used as fuel.16 The energy recycling figure in 1988 was presumably about 2.5 MMT smaller, or 72.8 MMT, based on relative pulp production levels. The AFPA numbers are as close to ours as can reasonably be expected, given the approximations made in our calculation.
All of the pulping processes except the mechanical ones use chemical reagents, notably sodium hydroxide or sulfurous acid, to dissolve the lignin and separate it from the cellulose fibers in the wood. In principle, these chemical reagents are mostly recovered and recycled internally. In practice, of course, recovery is incomplete and some makeup chemicals are required. In fact, makeup requirements and imputed overall losses and wastes are quite considerable.
The sodium sulfate consumed by the U.S. pulp and paper sector in 1988 was 0.48 MMT (Bureau of Mines, 1989, tables 3-5, 12). Similarly, soda ash consumed by the sector was 0.11 MMT. The total elemental sulfur actually consumed was 0.008 MMT. Consumption of lime by the sector was 1.14 MMT. The industry consumed 0.856 MMT of sulfuric acid. Most of these chemicals appear to have been used in pulping.
Other chemical inputs to the pulp and paper industry were used primarily in bleaching. Most virgin chemical pulps for paper are bleached. In 1988, the primary bleaching agents were elemental chlorine (Cl2), caustic soda, and chlorine dioxide. The latter is manufactured in-house from sodium chlorate, because chlorine dioxide is explosive and too dangerous to ship. In 1988, the paper and
pulp industry was the second largest user of chlorine, taking 1.5 MMT, or 14 percent, of total U.S. chlorine output (United States Bureau of Mines, 1989, p. 849). In 1988, the U.S. pulp and paper industry consumed 2.3 MMT of caustic soda, or 24 percent of production (United States Bureau of Mines, 1989, p. 849). It also consumed 0.341 MMT of sodium chloride (salt) (United States Bureau of Mines, 1989, table 18). The other chemical used in large quantities is sodium chlorate. Production of this compound in 1974 was reported to be 0.19 MMT, of which 70 percent was used for pulp bleaching (Lowenheim and Moran, 1975). U.S. production in 1988 was 0.242 MMT, and consumption was probably somewhat higher, thanks to imports. The 70 percent share attributable to pulp bleaching in 1974 is probably a minimum for 1988.17 On this basis, we estimate that 1988 consumption of sodium chlorate by the pulp sector was at least 0.2 MMT.
The chemicals described above (total weight 7 MMT) were not embodied in the final product and so must be counted as part of the production waste stream. It follows from materials-balance considerations that the annual discharges of chemical wastes from the pulp and paper industry must be roughly equal to the annual inputs, element by element. As it happens, annual "dry" wastes (e.g., sludges) were reported to be 7.7 MMT in the early 1980s (Science Applications International Corporation, 1985). This is much smaller than our estimate of 16 MMT (bone-dry) in losses from primary pulping and bleaching. However, our figures are more plausible because they include not only chemicals (7 MMT) but ash (approximately 1.5 MMT) and some fiber. They are also consistent with mass balance.
Bleaching wastes are mostly 90 percent sodium chloride, but an estimated 10 percent of the chlorine used is chemically bound to lignins and other organic materials in the pulp. This material constitutes a significant part of the process waste. Roughly 6 percent of the mass of the raw pulp is lost during bleaching. The bleaching effluent contains significant quantities of chlorinated organic compounds with very high molecular weights. In fact, 70-95 percent of spent chlorination and alkali extraction liquors have molecular weights greater than 1,000. Such compounds cannot be separated, quantified, or identified by present means. However, measurable traces of dioxins and furans are found among these wastes (Holmbom, 1991).
Kraft-process emissions of greatest environmental concern are noncondensible sulfur-containing gases (hydrogen sulfide, methyl and ethyl mercaptans, dimethyl sulfide, etc.). These are generated at the rate of about 2.5 kg/ton of pulp (International Bank for Reconstruction and Development, 1980). For sulfate pulp in toto, uncontrolled emissions of sulfur-containing gases would have been about 0.1 MMT. The EPA has estimated airborne effluents (excluding CO2) from the sector to be about 1.15 MMT (United States Environmental Protection Agency, 1991).
A partial list of chemicals used in the paper industry (as opposed to pulping) and embodied in the product includes clay (kaolin) for filling and coating, titanium dioxide for whiteness, and aluminum sulfate (alum) to improve the ink-
absorbing quality of printing paper. Allowing for 5 MMT of fillers and other chemicals embodied in paper products, total inputs to U.S. paper mills in 1988 added up to 80 MMT. Paper and pulp products produced domestically from woodpulp amounted to 69.53 MMT according to U.N. data and 75.1 MMT according to U.S. data.18 The difference is not easily explained.
Within the forest products sector, we can account for about 155 MMT (15 percent moisture basis) of wood and wood wastes burned for fuel in 1988, which is somewhat less than half of the harvested amount. This consisted of 57 MMT harvested for fuelwood (roundwood), 26 MMT wood chips and scrap from lumbering and wood products operations, and 73 MMT of pulping wastes. Of course, the heat energy from the latter two categories of wastes was recovered for use within the industry. Combustion would have required about 74 MMT of oxygen from the air and generated 132 MMT of carbon dioxide and 96 MMT of water vapor.
Wood combustion produces another waste product, wood ash. The combustion of undebarked wood chips and scrap yields 1-2.5 percent ash; debarked wood chips and sawdust yield 0.5-1.4 percent ash (Obernberger, 1994, table 2). We assume that fuelwood averages 2 percent ash (or a total of 1.2 MMT), whereas industrial wood and pulp average 1 percent ash content. Altogether, in addition to wastes already mentioned, we must add 1.8 MMT wood ash. The composite mass flows for the U.S. timber products sector, together with lumber and pulp and paper in 1988, are summarized in Figure 3. Imports and exports are not shown explicitly, although both are significant. The flows are normalized for U.S. consumption of the intermediates, lumber and wood products, and pulp. Thus, the upstream and downstream activities are indicated without reference to actual location. However, there are substantial additional imports of final paper products, but these are not shown.
Roughly 30 percent of the paper and paperboard consumed in the United States was collected for recycling in 1988. The unrecycled fraction of final consumption, amounting to 59.1 MMT, was either burned or disposed of in landfills. Ultimately, all of the unrecycled material is converted to either CO2 or methane (from anaerobic decay in landfills). If all the decay were aerobic, this would result in 86.6 MMT of CO2. However, anaerobic decay is probably more prevalent.
Mining (Metal Ores) and Quarrying19
There are two main types of waste associated with mining: earth displaced in the process of searching for and removing ore (overburden) and unwanted contaminants (gangue) removed on-site by screening, washing, settling, flotation, centrifuging, and so on. The material shipped to the next stage of processing is, typically, a concentrate that is fed into a downstream process, smelting for metals or combustion for fuels.20 Smelting wastes are discussed in connection with the
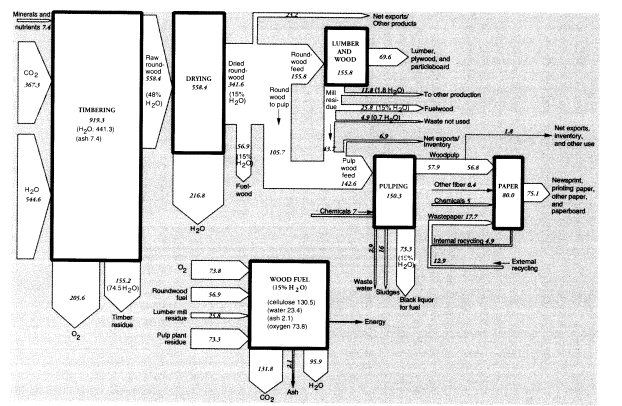
Figure 3
Mass flows in the U.S. timber, pulp, and paper industries, 1988 (million metric tons). Calculated by the authors from various sources, including Ulrich (1990), United Nations Statistical Office (1988), Bureau of Mines (1988, 1989), Bureau of the Census (1990), and United States Department of Agriculture (1992).
metallurgical industry, and combustion wastes are discussed separately in connection with fossil fuel combustion.
The Bureau of Mines estimates that mineral exploration and mine development activities (not including those targeting energy fuels) in 1988 generated 190 MMT of waste material, mostly from overburden stripping. Total overburden moved by U.S. mines (excluding coal mines) was 1,241 MMT; overburden moved to supply U.S. metals consumption, adjusted for both imports and exports, was 1,431 MMT.
Mining and quarrying activities consumed 1.87 MMT of industrial explosives, of which 85 percent was ammonium-nitrate based. We have calculated that about 5 percent of the explosive mass was probably converted to N2O, 14 percent to NO, and 5 percent to NO2. This implies N2O emissions of 0.09 MMT and NOx emissions of about 0.36 MMT from explosives.
Total concentration wastes for metals mined and concentrated domestically, including uranium (discussed below), were about 780 MMT. Adjusting for imports and exports reduces the total to 730 MMT. The most common physical concentration process is froth flotation. It is used, especially, to separate sulfide minerals of copper, lead, zinc, molybdenum, and silver from lighter minerals such as silicates, aluminates, and carbonates. Froth flotation is also used to concentrate phosphate rock and, to a minor extent, to clean coal. The most recent data available are for 1985 (Bureau of Mines, 1987). In that year, 380 MMT of mineral ores were concentrated by flotation, yielding 71.5 MMT of concentrates and 309 MMT of dry equivalent mineral wastes. There were 947 billion gallons, or 3,580 MMT, of water used in the process. Wastes from flotation are generally disposed of in ponds, mostly in dry areas. There was 0.63 MMT of chemical reagents used in concentration activities. Grinding mills required 8 billion kW of electricity and 0.134 MMT of iron rods and balls to break up the lumps of ore.
Aluminum and iron ores are not concentrated by flotation. In the case of aluminum, the ore is bauxite, which is a relatively pure mineral that already contains about 30 percent aluminum. Aluminum is further concentrated to relatively pure Al2O3 by the so-called Bayer process, then reduced by electrolysis rather than carbothermic smelting. In 1988, 8.2 MMT of bauxite ore were concentrated to 4.6 MMT of alumina (and some calcined bauxite) in the United States. Almost all of the bauxite was imported. Primary aluminum production in the United States consumed 3.2 MMT of imported alumina.
Iron ore mined in the United States is concentrated for blast furnaces by two processes: pelletizing at the mine and sintering. The latter process is carried out near the blast furnace because it utilizes significant quantities of iron-rich reverts, such as mill scale and dust, from later stages in the iron and steel production process. Blast furnace feed, or concentrates, average 63 percent iron, whereas domestic iron ore is only about 20 percent iron. In 1988, 197 MMT of crude iron ore were concentrated into 57.5 MMT of furnace feed, leaving 140 MMT of wastes.
Large amounts of nonmetallic minerals are mined or quarried domestically. By weight, stone (1,150 MMT, including limestone) and sand and gravel (863 MMT) top the list of these minerals. Imports and exports are comparatively small. Unlike the case of metals, overburden wastes are small in relation to production (except for clay, for which waste amounts to 35.7 MMT). Domestic concentration wastes are also negligible, except for phosphates (179 MMT), potash (8.9 MMT), and soda ash from trona (7.0 MMT).
Phosphate rock mining and processing are extremely important activities, because phosphate fertilizers are absolutely essential for modern agriculture. Unfortunately, the ore is not of very high grade and is contaminated, especially with cadmium, fluorine, and uranium. In the United States, 451.8 MMT of raw materials were handled to produce 224.1 MMT of crude phosphate rock in 1988. The difference was presumably overburden, which was mostly left in previously mined areas. The crude ore was concentrated, mainly by flotation, to 45.4 MMT of concentrated fluorapatite mineral—roughly (CaF)·Ca4(PO4)3—which was, in turn, treated by sulfuric acid to yield fertilizer-grade phosphoric acid (13.8 MMT phosphorus pentoxide [P2O5]). This refining operation is considered to be part of the chemical industry and is not discussed further here.
Uranium mining in the United States produced about 15 MMT of ore in 1980. This was reduced, mostly by flotation, to 19,500 metric tons (MT) of U3O8 concentrate, or yellow cake, which yielded 4,740 MT of refined uranium oxide (nuclear fuel). About 3,200 MT of ore are needed to produce 1 MT of concentrated UO2 pellets (LeBel, 1982, table 6.1). Uranium production has been declining sharply; production in 1991 was 0.58 MMT of ore and 1,150 MT of yellow cake, a decrease of 96 percent from 1980. Uranium mining added 15 MMT to the 1980 figure for concentration waste, but due to declining demand, waste amounted to about 1 MMT in 1988. (We do not have an exact figure for that year.)
Mine wastes from metallic and nonmetallic mineral production within the United States in 1988 can be summarized as follows. For metal ores, overburden wastes were 1,192 MMT and concentration wastes were 784 MMT, if alumina and crude phosphate rock processing is included, or about 965 MMT and 600 MMT, respectively, if it is not (alumina and phosphate rock are considered products of the chemical industry). The metals system is discussed further below and summarized diagrammatically in connection with metals smelting and refining.
For nonmetallic minerals excluding coal, overburden wastes were 47 MMT and concentration wastes were 15.9 MMT (excluding phosphates). The nonmetallic minerals that are ultimately transformed into inorganic chemicals (phosphates, potash, and soda ash) are discussed further below in connection with chemicals.
The total of overburden wastes for metals and nonmetallic minerals amounted to 1,239 MMT; total concentration wastes were 800 MMT, essentially dry weight, including alumina and phosphates (Tables 3 and 4). Total mineral mining wastes in the United States are actually about 2,050 MMT, excluding water used for
TABLE 3 Production and Waste Allocation for Primary U.S. Metal Production, 1988 (1,000 metric tons)
|
U.S. Domestic Mine Production |
U.S. Domestic Concentrate Production |
U.S. Primary Metal Production (domestic and foreign ores) |
||||||
Metal |
Total Material Handled (A) |
Ore Treated or Sold (B) |
Overburden (A - B) |
Production (metal content) |
Production (gross weight)a (C) |
Concentration Wastes (B - C) |
Concentrate Consumption (gross weight)a (D) |
Primary Production (total) (E) |
Smelting/ Refining Losses (D - E) |
Bauxite/ |
8,246b |
1,107b |
7,140 |
|
|
|
|
|
|
Aluminum |
|
8,970c |
|
|
4,575 |
4,395 |
7,730 |
3,944 |
3,786 |
Copper |
523,446 |
218,631 |
304,814 |
1,341 |
5,364 |
213,267 |
5,794 |
1,406 |
4,388 |
Gold |
536,146 |
117,934 |
418,212 |
0.201 |
0.201 |
117,934 |
392 |
0.138 |
392 |
Lead |
9,707 |
6,450 |
3,257 |
385 |
481 |
5,969 |
83,694 |
392 |
98 |
Molybdenum |
127,006d |
72,212 |
54,794 |
43 |
172 |
72,040 |
103 |
26 |
77 |
Platinum group |
34,189 |
11,396e |
22,793 |
0.005 |
0.005 |
11,396 |
0.0003 |
0.0003 |
|
Silver |
48,444 |
15,876 |
32,568 |
1.661 |
1.661 |
15,874 |
2 |
1.718 |
|
Zinc |
21,149 |
9,106e |
12,043 |
244 |
432 |
8,674 |
429 |
241 |
188 |
Uranium oxidef |
22,000 |
15,200 |
6,800 |
|
20 |
15,180 |
20 |
5 |
15 |
Nonferrous total |
1,330,333 |
467,912 |
862,420 |
|
11,046 |
460,334 |
14,960 |
6,016 |
8,944 |
Iron total |
300,278 |
197,766 |
102,512 |
|
57,515 |
140,251 |
83,694 |
49,242 |
34,452 |
TOTAL |
1,630,611 |
665,678 |
964,932 |
|
68,561 |
600,581 |
98,654 |
55,258 |
43,396 |
a Where direct figures for gross weight of concentrate were unavailable, they were calculated by applying reasonable concentration ratios to the metal content. b Bauxite at U.S. mines. Included in total of "ore treated." c Crude bauxite ore, dry equivalent. Includes net imports. Not included in "ore treated" total. d Assumes 3:1 ratio material handled to ore, as with gold/silver. e Zinc data have been subtracted from "other" in 1989 Minerals Yearbook to construct approximate platinum data. f 1980 data. SOURCE: Bureau of Mines (1988, 1989). |
TABLE 4 Production and Waste Allocation for U.S. Industrial Mineral Production from Domestic and Foreign Ores, 1988(1,000 metric tons)
Mineral |
Total Material Handled (A) |
Ore Treated or Sold (B) |
Domestic Production (C) |
Exports (D) |
Imports (E) |
Apparent Consumption (C - D + E) |
Overburden Loss (A - B) |
Concentration Losses (B - C) |
Abrasives, natural |
232 |
156 |
156 |
|
|
156 |
76 |
0 |
Barite |
404 |
404 |
404 |
0.205 |
1,207 |
1,611 |
0 |
0 |
Clays |
83,370 |
44,633 |
44,515 |
3,535 |
33 |
41,013 |
38,737 |
118 |
Diatomite |
3,420 |
695 |
629 |
147 |
0 |
482 |
2,725 |
66 |
Feldspar |
649 |
649 |
649 |
12 |
287 |
924 |
0 |
0 |
Gypsum |
18,325 |
14,869 |
14,869 |
246 |
8,782 |
23,405 |
3,456 |
0 |
Mica |
130 |
130 |
130 |
6 |
12 |
136 |
0 |
0 |
Perlite |
586 |
586 |
585 |
0 |
0 |
585 |
0 |
1 |
Phosphorus |
451,778 |
224,075 |
45,389 |
0 |
0 |
45,389 |
227,703 |
178,686 |
Potassium salts |
12,247 |
11,884 |
2,999 |
579 |
6,964 |
9,384 |
363 |
8,885 |
Pumice |
423 |
374 |
353 |
1 |
28 |
380 |
49 |
21 |
Salt |
34,470 |
34,470 |
34,470 |
802 |
4,966 |
38,634 |
0 |
0 |
Sand and gravel |
863,640 |
863,640 |
863,531 |
1,837 |
357 |
862,051 |
0 |
109 |
Soda ash |
15,728 |
15,728 |
8,738 |
2,238 |
257 |
6,757 |
0 |
6,990 |
Stone (estimate) |
1,151,000 |
1,150,000 |
1,148,533 |
3,304 |
3,300 |
1,148,529 |
1,000 |
1,467 |
Talc, soapstone, pyrophilite |
1,179 |
1,234 |
1,234 |
382 |
80 |
932 |
-54 |
0 |
Vermiculite |
3,393 |
1,769 |
275 |
18 |
32 |
289 |
1,624 |
1,495 |
TOTAL |
2,640,974 |
2,365,295 |
2,167,459 |
13,108 |
26,305 |
2,180,656 |
275,679 |
197,836 |
SOURCE: Bureau of Mines (1988, 1989). |
flotation. It is interesting to contrast this number with the only other published estimate we could find, for 1985, of 1,400 MMT (Science Applications International Corporation, 1985). The SAIC figure is far too low because it supposedly included the coal mining sector, which we discuss below.
Mineral Fuels: Coal Mining and Oil and Gas Drilling21
Coal mining is the largest single source of waste materials. For every short ton of coal moved, 6.5 tons of mostly overburden wastes are produced (Anonymous, U.S. Department of Energy, personal communication, 1994). Because national soft coal production in 1988 was 862.1 MMT (weight at the mine), total materials handled in coal mining, exclusive of the coal itself, were on the order of 5,600 MMT. This is more than three times the amount of topsoil lost by erosion. Coal mining is also a source of methane; methane is trapped in the coal seams and released when the coal is pulverized. Later, we consider methane production from all fossil-fuel-related activities.
Some utility coal is washed to remove pyrites and ash, resulting in a significant further production of waste. In 1975, about 41 percent of soft coal was cleaned, resulting in 16 tons of coal refuse for every 100 tons of coal washed, for an 84 percent yield.22 By 1988, more low-sulfur western coal was mined and only about 30 percent of midwestern coal was cleaned. In 1988, therefore, we assume that 4.8 tons (0.3 x 16) of sulfurous refuse were produced at the mine per 100 tons of coal mined. Given that 862 MMT were shipped, approximately 900 MMT must have been mined, generating beneficiation wastes of about 47 MMT, give or take 10 MMT. Sulfurous refuse is a significant cause of acid mine drainage. The 1983 Census of Manufactures reported that coal mines discharged 470 MMT of water, including washing water (Bureau of the Census, 1983). Combustion emissions are discussed below.
In 1988, 86.2 MMT of U.S. coal were exported and 1.94 MMT were imported. Roughly 42 MMT of coal went to coke ovens, producing about 30 MMT of finished coke, 7.6 MMT of coke oven gas, 3.9 MMT of tar and breeze, and small quantities of other by-products, including ammonium sulfate. There were also minor fugitive emissions, mainly from the coke quenching process. The mass flows and wastes in the coal system are shown in Figure 4.
Petroleum and natural gas production involve relatively little waste, except water. During 1988, the U.S. oil and gas industry drilled 25,000 wells encompassing 124 million feet of holes. Assuming 6-inch pipe for the holes, and 5.5 liters of material removed per linear foot, this drilling would have generated 682 million liters total. A liter of water weighs 1 kg, and we assume drilling wastes displaced by pipe have an average specific gravity of 3, so the weight of displaced materials was about 2 MMT. Another 4-5 MMT of material was removed and displaced by the drilling mud (allowing for water content). We therefore estimate a total of 6-7 MMT of drilling wastes.
Drilling muds constitute a much larger source of waste. Drilling muds are, on average, 86 percent water, much of which is taken from the wells themselves, 3 percent oil, 2 percent polymers, and 9 percent other materials (United States Congress, Office of Technology Assessment, 1992). The latter include clay, barite, and chrome lignin sulfonates. It should be noted that petroleum drilling accounts for virtually the entire national consumption of the mineral barite, or 1.4 MT. Consumption of clays, notably bentonite and fullers' earth, accounted for 1 MMT. On this basis, drilling muds must have weighed at least 25 MMT. EPA has estimated that drilling fluids used in 1985 weighed 57 MMT (United States Congress, Office of Technology Assessment, 1992). Additional ''associated wastes" amounted to 2 MMT, most of which are stored in ponds, where the water gradually evaporates.
EPA estimated that 3.7 billion tons of "produced waters" were generated by drilling activities in 1985 (United States Congress, Office of Technology Assessment, 1992). About 62 percent of this water was reinjected in oil and gas recovery operations, leaving 1.4 billion tons, or 1,270 MMT. Produced waters are usually saline and therefore constitute a disposal problem of some magnitude. (Most of the water is injected into wells.) The excess of produced waters would help to reconcile the water data for the mining sector as a whole. The 1983 Census of Manufactures reported that about 700 MMT of water were used for cooling in the gas-fractionation process (Bureau of the Census, 1983).
Natural-gas distribution by pipeline is a source of methane leakage to the atmosphere. In the United States in 1988, it is estimated that 17.15 MMT, equal to 3.5 percent of total production and 4.6 percent of the total quantity transported, disappeared from the system (International Energy Agency, 1991). We estimate that half of this was used to drive compressors whereas the other half, approximately 8 MMT, leaked into the atmosphere. Further losses occur in local distribution.
Petroleum Refining23
Total output of crude oil in the United States in 1988 was 402.6 MMT. Exports were 0.6 MMT, and imports were 269.05 MMT, for a total domestic crude oil supply of 671.0 MMT. Reported inputs of crude oil to domestic oil refineries were 680.687 MMT, leaving a discrepancy of 9.1 MMT. In addition, refineries consumed 17.15 MMT of natural gas as fuel, 16.230 MMT of natural gas liquids, and 22.585 MMT of intermediate feedstocks. Of the latter, 16.166 MMT were imported and 6.319 MMT were internal transfers of "gasoil" to be upgraded. Subtracting the gasoil amount from both inputs and outputs leaves a total of 730.23 MMT of net inputs (Table 5).
Crude oil is desalted before refining. Water pollution from this process contains emulsified oil as well as salts, ammonia, sulfides, and phenols. Also, this process involves considerable water use. Refinery products include noncon-
TABLE 5 U.S. Energy Statistics, 1988 (million metric tons)
|
Production |
Exports |
Imports |
Consumption |
||||
Commodity |
Raw |
Finisheda |
Raw |
Finished |
Raw |
Finished |
Raw |
Finished |
Refinery Inputs |
||||||||
Crude oil |
402.585 |
|
0.634 |
|
269.053 |
|
680.687 |
|
Feedstocks |
|
|
|
|
|
16.864 |
22.585 |
|
Natural gas liquids |
|
51.325 |
|
1.617 |
|
7.108 |
16.230 |
|
Refinery Products |
||||||||
Liquid petroleum gas |
|
15.906 |
|
|
|
|
|
56.272 |
Motor gas |
|
297.439 |
|
1.069 |
|
19.351 |
|
315.690 |
Aviation gas |
|
1.020 |
|
|
|
0.020 |
|
1.074 |
Jet fuel |
|
63.935 |
|
1.362 |
|
3.802 |
|
66.893 |
Kerosene |
|
4.347 |
|
0.054 |
|
0.173 |
|
4.689 |
Diesel |
|
143.258 |
|
3.419 |
|
12.943 |
|
146.315 |
Residual fuel oil |
|
56.789 |
|
11.044 |
|
32.818 |
|
61.429 |
Naphtha |
|
6.170 |
|
0.479 |
|
3.216 |
|
8.864 |
Petroleum coke |
|
36.131 |
|
15.344 |
|
0.110 |
|
20.709 |
Other |
|
54.073 |
|
2.626 |
|
5.865 |
|
57.072 |
Total Petroleum |
402.585 |
679.068 |
0.634 |
35.397 |
269.053 |
78.298 |
719.502 |
739.007 |
Coal and coke |
862.066 |
29.397 |
86.203 |
0.992 |
1.936 |
2.439 |
801.647 |
30.844 |
Natural gas |
||||||||
(18.02 kg/TJ) |
424.990 |
335.028 |
|
|
|
2.870 |
|
302.100 |
Total other fuel |
1,287.056 |
364.425 |
86.203 |
0.992 |
1.936 |
5.310 |
801.647 |
332.940 |
TOTAL |
1,689.640 |
1,043.493 |
86.837 |
36.389 |
270.989 |
83.610 |
1,521.149 |
1,071.947 |
a Finished values may exceed raw values because "finished" refers to refinery products whose inputs may have been imported. SOURCE: International Energy Agency (1991). |
densible refinery gases amounting to 34.072 MMT and salable products weighing 679.068 MMT, or 672.749 MMT after subtracting the 6.319 MMT of gasoil that was internally recycled. Petrochemicals are also derived to some extent from "light ends," dissolved volatiles that result from petroleum refining.24 Crude oil contains relatively little of these materials. A typical U.S. refinery using Texas or Louisiana crude oil might yield 1.3 percent light ends (as refinery off-gas) by volume from the initial distillation (Gaines and Wolsky, 1981). However, subsequent refining processes such as catalytic cracking, catalytic reforming, and delayed coking also yield large quantities of light ends. Most of these by-product volatiles are used internally within the refinery complex. The C4 gases (butylene, isobutane, and n-butane) are mostly alkylated or blended directly into gasoline. The C3 gases (propane, propylene) are collected and liquified under pressure for use as domestic fuel (i.e., liquid propane gas). The mixed C1 and C2 gases (methane, ethane, and ethylene) are mainly used as fuel for steam generation to provide heat energy for the refinery itself. Large amounts of hydrogen-rich off-gases are produced in refineries, but these are mostly used for hydrotreatment of naphtha or for hydroforming within the refinery. Similarly, catalytic reformate, derived from naphtha, is the major source of aromatic feedstocks, known as BTX (benzenetoluene-xylene), although most of this material is blended into gasoline to increase the octane number.
Nevertheless, light ends also constitute a source of aliphatic petrochemical feedstocks. In brief, light alkane feedstocks such as ethane (C2H6), propane (C3H8), and butanes (C4H10)—along with some naphtha and heavy gas oil—are dehydrogenated in a pyrolysis furnace within the refinery complex to yield ethylene (C2H4), propylene (C3H6), butadiene (C4H6), butene, butylene (C4H8), and other C4 olefins. In 1988, crude petroleum-based feedstocks consisted of liquified petroleum gas (22.459 MMT), naphtha (8.864 MMT), and light ends (1.12 MMT). (See section on organic chemicals, below.)
In summary, apparent mass losses during refining in 1988 amounted to 55.58 MMT (728.33 - 672.75), or 7.6 percent of input mass. In other words, the efficiency of mass conversion was 92.4 percent. Presumably, virtually all of the missing mass consists of carbon dioxide, carbon monoxide, or hydrocarbons, including fugitive volatile organic compounds (VOCs). The EPA estimated airborne effluents from the sector at 2 MMT (United States Environmental Protection Agency, 1991); we assume this figure does not include carbon dioxide. This is consistent with materials-balance arguments. VOCs from petroleum refining include significant quantities of BTX and other aromatics, many of which are carcinogenic.25
Crude oil contains small quantities, on the order of 0.1 percent depending on its origin, of sulfur and mineral ash. For example, Venezuelan oil is particularly high in sulfur. The petroleum refining industry recovers sulfur from crude oil and produces sulfuric acid as a by-product (2.4 MMT H2SO4 or 0.786 MMT S). Most of this sulfuric acid is used within the refinery for bleaching. However, over half
(1.3 MMT) of the spent acid is recovered and sold. Most of the ash in crude oil probably remains with the refinery solid wastes and sludges. Assuming the crude oil contains 0.1 percent ash, there would be some 0.7 MMT of solid waste. The spent sulfuric acid (2.1 MMT) is presumably neutralized, either by reaction with some of the alkaline minerals (NaO, KO, MgO, CaO) in the crude oil ash, or by added lime.
Refineries also use materials purchased from other sectors in the refining process, including salt (0.72 MMT) and clays (0.122 MMT), which subsequently reappear mostly in solid or liquid wastes. Consumption of salt is reported, but its use is unclear; it may be a precursor to in-house caustic soda production (Gaines and Wolsky, 1981).
Mass flows in the petroleum, gas, and refinery sectors are shown in Figure 5. As noted above, the mass loss in refineries amounted to 55.6 MMT in 1988, or 7.6 percent of the mass of hydrocarbon inputs. This loss is partly fugitive emissions (VOCs), estimated to be 2 MMT, but most of these emissions are flared or recovered for refinery heat and power. Assuming that the missing mass consists mostly of molecules of the form CNH2N+2we can safely predict carbon content of between 80 and 85 percent, or about 45 MMT. This corresponds to an atmospheric oxygen intake of 120 MMT, eventual CO2 output of roughly 165 MMT, and water-vapor output of 76.5 MMT.
Dry wastes from the petroleum refining sector were about 1.25 MMT in 1981 (Science Applications International Corporation, 1985). Given the fact that neutralized sulfuric acid wastes alone would account for considerably more than this, we estimate the solid wastes from refineries to be 3-4 MMT (i.e., three times more than the SAIC estimate). EPA's estimate of total nonhazardous waste produced by the sector in 1985 was 150 MMT. Because the missing mass in the sector was only 55.6 MMT, including purchased inputs, and most of this must have been combustion products and VOCs, it is clear that most of the waste mass counted by EPA must have been water.
Chemicals
The chemical industry is far too complex to describe in adequate detail in the space available here. Our discussion is inevitably somewhat superficial. The major distinction is between inorganic and organic chemicals. The latter are derived mostly from natural gas, natural gas liquids, or petrochemical feedstocks.
Inorganic Chemicals26
Inorganic chemicals are derived either from nonmetallic minerals such as sulfur, phosphates, potash, soda ash, and salt or from the atmosphere. A few inorganics are derived from metal ores or metals. A summary diagram for phosphates, potash, and soda ash, beginning with extraction and beneficiation, is given
in Figure 6. The most important inorganic chemicals other than the three noted above are ammonia, sulfur (sulfuric acid), and salt (chlorine and sodium hydroxide) (Figure 7). The major groupings are discussed in the following sections. Others are mostly derived from these. For example, nitric acid and urea are both made from ammonia.
Domestic production of ammonia in 1988 was 12.544 MMT (N content). Net imports (imports minus exports) plus stock changes increased apparent domestic consumption of ammonia to 14.745 MMT (N). In addition, there were significant imports and exports of nitrogen-containing chemicals. The major net import items were urea (0.483 MMT N) and ammonium nitrate (0.091 MMT N), while major net export items were ammonium phosphates (1.150 MMT N) and ammonium sulfate (0.155 MMT N). In all, fertilizers accounted for nearly 80 percent of the supply of fixed nitrogen (Figure 7).
The nitrogen content of monomers embodied in plastics and resins in 1988 added up to 0.669 MMT. Nitrate and nitro-explosives, excluding amines, accounted for about 0.777 MMT (N). Urea fed to animals accounted for 1.55 MMT (N); unspecified uses of nitric acid, including phosphate rock processing and steel pickling, accounted for 0.135 MMT (N). Other identifiable final uses, including dyes, rubber chemicals, herbicides and pesticides, and sodium cyanide used in the gold mining industry, added to 0.153 MMT (N). Process losses are probably at least 2 percent. (Nitrogen wastes are less than they might otherwise be, however, because ammonia-bearing waste streams are easily neutralized by sulfuric acid to produce a useful by-product, ammonium sulfate fertilizer.) We estimate that process losses altogether account for 0.3-0.35 MMT (N). There is some possibility of undercounting of the use of nitrogen in mixed fertilizers where published data seem to be spotty. However, lacking further information, we assume the remaining "missing" nitrogen (about 0.4 MMT) is allocated mostly to household cleaning agents and other consumer products. In summary, we can account for about 0.737 MMT of fixed nitrogen embodied in products of the synthetic organic chemicals sector and on the order of 0.16 MMT of nitrogenous losses associated with organic synthesis, for a total of 0.9 MMT.
In terms of environmental pollution, the 2 percent loss rate suggested above is insignificant compared with dissipative uses of nitrogenous chemicals. Apart from fertilizers and animal feeds, these include industrial explosives, pesticides and herbicides, dyes, surfactants, flotation agents, rubber accelerators, plasticizers, gas conditioning agents, and so on. In fact, except for plastics and resins (and plasticizers), it is safe to assume that virtually all nitrogenous chemicals are soon dissipated in normal use, but mainly by other sectors or final consumers. In the case of plastics and fibers, the dissipation is merely slower.
Sulfuric acid (37.7 MMT in 1988) is derived from elemental sulfur; 11.584 MMT of sulfur were produced in 1988, most of which (10.3 MMT) was used to produce sulfuric acid, which is the starting point for most sulfur-based chemicals (Figure 7). Elemental sulfur is also recovered from natural-gas processors and
petroleum refineries. In the latter case, most (0.958 MMT) of the sulfur was used on site, but almost half of the spent acid (0.43 MMT S) from refineries was later reclaimed. Sulfuric acid was recovered from copper, zinc, and lead smelters (1.125 MMT S), but much of that (0.543 MMT) was used in the acid-leach process of mining operations. In the case of copper mines, copper sulfate is recovered from the leach piles and recycled, but much of the leaching acid remains in the ore heaps, where it presumably reacts with other minerals and remains as insoluble sulfates.
By far the largest use of sulfuric acid is for processing phosphate rock (8.404 MMT S). This use was noted above. Another important use of sulfuric acid (0.288 MMT S) is in the sulfate (Kraft) pulping process, also discussed above. The pickling process used to clean rolled steel prior to galvanizing or tin-plating used 0.074 MMT S as acid, of which 0.022 MMT was recovered. Sulfuric acid containing an additional 0.024 MMT S was used by other metallurgical processes, mainly metal plating. Automotive batteries accounted for a further 0.051 MMT, of which 0.036 MMT was reclaimed. The above uses plus exports add up to 11.162 MMT of embodied sulfur, or greater than 90 percent of the total. The remainder, 1.172 MMT of embodied sulfur, either is used elsewhere in the chemical industry or is used for unidentified nonchemical purposes.
Excluding phosphates and sulfuric acid itself, about 5.04 MMT of sulfuric acid (1.645 MMT S) and 0.684 MMT of elemental sulfur were consumed by the nonphosphate chemical industry in 1988. Industrial inorganic chemicals, including pigments, consumed about 0.9 MMT S, mostly as acid. Of the sulfur used in chemicals, 0.566 MMT was eventually converted into ammonium sulfate fertilizer, mostly as a by-product of other chemical processes that use sulfuric acid (e.g., caprolactam, a nylon monomer, and hydrogen cyanide). Of the rest, 0.170 MMT was embodied in aluminum sulfate, mainly for the paper industry; 0.185 MMT S was in the form of by-product sodium sulfate, consumed in pulp manufacture. Apparently, 0.460 MMT of elemental sulfur was used in "other" agricultural chemicals. The organic side of the chemical industry consumed at least 0.7 MMT S, mostly as acid. Of this, drugs and pesticides accounted for only 0.02 MMT and detergents for 0.06 MMT. The major uses were for the manufacture of organic chemical intermediates and synthetic rubbers and plastics. However, except for drugs, pesticides, and detergents, virtually no sulfur is embodied in organic chemicals. Hence, at least 0.6 MMT S was consumed and lost in organic processing. In addition, there was 0.824 MMT S as sulfuric acid and 0.297 MMT elemental sulfur in the "unidentified and export" category. For reasons discussed below, we believe that most of this was also consumed in the organic chemical industry.
These waste flows were in several chemical forms, including H2S, SO2, ammonium bisulfate, calcium sulfite, and calcium sulfate. (To mention one example, hydrofluoric acid manufactured in 1988 would have accounted for about 0.24 MMT S and generated calcium sulfate waste.)
Phosphate rock is the only source of phosphorus chemicals, including fertilizers. The starting point is fertilizer-grade phosphoric acid (13.833 MMT P2O5 content).27 Of 1988 production, exports—mostly ammonium phosphates—accounted for 2.608 MMT, leaving 10.549 MMT for domestic consumption. Most of the latter, 9.329 MMT, or 88.4 percent, was converted into "wet process" phosphoric acid (H3PO4). Elemental phosphorus production in the United States in 1988 was 0.32 MMT (0.73 MMT P2O 5 equivalent), of which 85 percent was reconverted to pure furnace-grade phosphoric acid for chemical manufacturing. Some of this is used to make triple superphosphate fertilizer, but about 40 percent was used to manufacture sodium tripolyphosphate (STPP, Na5P3O10), a detergent builder. Production of this chemical in 1988 was 0.497 MMT, with a P2O5 equivalent of 0.309 MMT. The detergent industry has been shifting to an alternative, tetrasodium pyrophosphate, which contains less phosphorus. Some phosphoric acid is used as a flavoring agent in the food and soft drink industry.
A minor but growing use of phosphorus is in the manufacture of lubricating-oil additives such as zinc dithiophosphate. This use accounted for 0.015 MMT of phosphorus metal in 1974; we estimate 0.02 MMT in 1988, corresponding to about 0.05 MMT P205 equivalent.
The starting point for organic phosphate synthesis is phosphorus trichloride (PCl3). Production figures are not published, but assuming 1 percent of chlorine output goes to PCl3 production (see discussion of chlorine below), we conclude that about 0.03 MMT of phosphorus metal, or 0.07 MMT P2O5, would have been required. The trichloride is later converted to phosphorus oxychloride (POCl3) by direct reaction with chlorine and phosphorus pentoxide P2O5. The oxychloride, in turn, is the basis of organic phosphate esters that now have many uses. The most important of these uses is in the manufacture of the plasticizer tricresyl phosphate. Phosphate esters are also used as flame retardants and fire-resistant hydraulic fluids. The United States used 0.043 MMT (P2O5) of phosphate esters in 1990 (International Trade Commission, 1991). Usage in 1988 was probably similar.
All of the uses mentioned above are inherently dissipative. No more than 0.2 MMT of elemental phosphorus is embodied in chemicals used to manufacture other chemical products, mainly detergents.
Elemental chlorine and sodium hydroxide (NaOH, or caustic soda) are coproduced by electrolysis of sodium chloride (salt), mainly in the form of brine (Figure 7). In 1988, U.S. salt production was 35 MMT, of which 18.1 MMT was consumed by chlor-alkali producers. The United States produced 10.21 MMT of chlorine and 9.55 MMT of sodium hydroxide (Chemical and Engineering News, 1992).28 The wastes from this process, mostly spent brines, amount to about 15 percent of the weight of the products, or 3 MMT. The mass balance is made up from about 5 MMT water on the input side and 0.3 MMT hydrogen gas released from the electrolytic cells. The latter is generally burned on site for energy recovery.
Major uses of chlorine in the United States in 1988 included chemicals manufacturing (76 percent), water and sewage treatment (5 percent), pulp and paper bleaching (14 percent), titanium dioxide manufacturing from rutile (3 percent), and miscellaneous, including silicon processing (2 percent). The use of elemental chlorine for bleaching in the pulp and paper industry has become a very contentious subject in recent years, due to the discovery of dioxin traces in bleached paper products. As a consequence, whether justified or not, this bleaching process has been largely phased out in Europe and may soon be phased out in North America. The likely alternative process is oxygen bleaching using chlorine oxide from sodium chlorate29 or hydrogen peroxide.
Chemical end uses of chlorine in 1988 were as bleaches such as calcium and sodium hypochlorite (7.8 percent); other inorganics like phosgene (2 percent) and phosphorus trichloride (1 percent); ethylene dichloride, or EDC (40.5 percent); chlorinated methanes (9 percent); chlorinated ethanes (5 percent); epichlorohydrin (1 percent); ethyl chloride (3.5 percent); chlorinated benzenes (1.5 percent); chloroprene (1 percent); and miscellaneous (3 percent, including hydrochloric acid [HCl] used outside the industry). These total to about three-quarters of U.S. chlorine output.
One of the major chlorine intermediates is HCl. Nine percent of HCl is made by direct chlorination of hydrogen, but most HCl, about 91 percent, is recovered as a by-product of one of the chlorination processes, especially the chlorohydrin process for propylene oxide production. The latter process consumed 8.3 percent of U.S. chlorine output in 1988, but this chlorine was entirely recycled internally as HCl. The other major source of HCl is the process that converts EDC to vinyl chloride monomer (VCM). HCl is also consumed by a parallel process that produces EDC by hydrochlorination of ethylene. These two processes are deliberately combined. Other end uses of HCl include ethyl chloride (for tetraethyl lead production, now nearly phased out) and hypochlorite bleaches.
By far the biggest single intermediate is EDC, the intermediate leading to polyvinyl chloride (PVC). However, PVC accounts for only 24 percent of produced chlorine; part of the chlorine contained in EDC is reclaimed again as HCl. EDC also has other end products, such as trichloroethylene and perchloroethylene. Some is also exported. Another important intermediate is epichlorohydrin, an intermediate to epoxies; phosgene (COCl2) is an intermediate to isocyanate pesticides and urethanes. Chlorinated benzenes are also intermediates to a variety of products.
Virtually all uses of chlorine are dissipative, with the major exception of PVC, which is used for structural purposes (e.g., water and sewer pipes, siding, window frames, calendered products, and bottles). PVC, from vinyl chloride monomer, accounts for 24 percent of U.S. elemental chlorine output.
Direct chlorination processes are relatively inefficient. Hence, recycling of waste streams is commonplace and a fairly large proportion of the input chlorine eventually becomes a production waste for manufacturing other downstream
chemicals. For example, in the production of VCM from ethylene dichloride, the loss rate is around 3 percent (Manzone, 1993). About 60 percent of this waste stream consists of nonvolatiles, or heavy ends, that are recycled into chlorinated solvents; 40 percent is volatiles that are destroyed by incineration, with some recovery of hydrogen chloride. In general, a 3 percent loss rate for direct chlorination processes seems realistic.
The other halogens are bromine, fluorine, and iodine. The last of these is not used in significant quantities. Bromine consumption in the United States in 1988 was 0.163 MMT. Exact figures are unavailable, but the Bureau of Mines estimated that about 25 percent was used in drilling fluids, mostly as calcium and zinc bromides, and 15 percent was used in water treatment as a biocide for slime control. Fire retardants (tetrabromobisphenol-A and decabromodiphenyl oxide, known as halons) accounted for about 30 percent of total usage. About 15 percent was used in agriculture as a soil fumigant, methyl bromide, whereas 18 percent was consumed as ethylene dibromide, which is added to leaded gasoline as a scavenger to prevent lead deposition on valves. (This use was being phased out in 1988 and is now [1998] negligible.) An unknown but small amount was used to manufacture a red pigment (pigment 168) for metallized paint for automobiles. Evidently, around 60 percent was used in organic chemicals, half olefin based and half aromatic (e.g., phenol) based. All uses of bromine are dissipative.
Fluorine consumption in the United States was 0.551 MMT in 1988, but this included nonchemical uses such as fluxes for the steel industry. Synthetic cryolite for the aluminum industry may have used some hydrofluoric acid (HF), although for this purpose the U.S. industry is converting to the use of by-product fluosilicic acid from phosphate rock processing.
Most chemical uses of fluorine begin with HF, produced by reacting sulfuric acid and fluorspar (CaF2). U.S. production of the acid in 1988 was 0.195 MMT, consuming roughly 0.24 MMT (S content) of sulfuric acid and generating calcium sulfate as a waste. Some HF was used in petroleum refining (as an alkylation catalyst), and some was used in uranium refining (uranium hexafluoride, UF6). An increasing amount is being used in semiconductor manufacturing. However, probably most of the fluorine was consumed in the manufacture of chlorofluorocarbons (CFCs) and hydrochlorofluorocarbons (HCFCs), notably CCl3F, or CFC-11 (0.1 MMT containing 10 percent F); CCl2F2, or CFC-12 (0.175 MMT containing 24 percent F); and CHClF2, or HCFC-22 (0.148 MMT containing 34 percent F). Altogether, these three CFCs accounted for about 0.092 MMT flourine, or over 0.10 MMT HF. Other CFCs and the fluorocarbon polymers (e.g., Teflon©) presumably accounted for most of the rest.
In 1988, as noted above, 9.55 MMT of sodium hydroxide (caustic soda) were produced as a coproduct of chlorine production. We have no precise breakdown for 1988. Major uses of caustic soda in 1973 were in the chemical (46 percent) and pulp and paper industries (16 percent) for the preparation of alumina by the Bayer process and to make synthetic cryolite for aluminum manufacturing (6
percent); in petroleum refining (6 percent), dyeing of textiles (4 percent), and rayon manufacturing (3 percent); in the production of soap and detergents (3 percent) and cellulose acetate (2 percent); and for miscellaneous purposes (14 percent, including exports) (Lowenheim and Moran, 1975, p. 742). By 1988, the pulp and paper industry had increased its share to 24 percent (2.7 MMT), and the aluminum industry had consumed just under 4 percent (0.37 MMT), a slight decline.
Taking into account alumina and soap and detergent manufacturing, around 48 percent (4.5 MMT) of caustic soda was probably absorbed by the chemical manufacturing sector. Most sodium-containing inorganic chemicals such as sodium silicate or sodium dichromate start from less-expensive sodium carbonate (soda ash), rather than sodium hydroxide. Sodium is not a significant component of synthetic organic chemicals, with one exception: sodium salts of coconut oil acids (0.275 MMT) and tallow acids (0.46 MMT), which are major components of liquid detergents. (We cannot readily estimate the average sodium content of these, but we conjecture that it is less than 10 percent, which implies a 0.2-0.3 MMT Na2CO3 equivalent.) This is consistent with the 3 percent share noted above. Otherwise, virtually all of the produced sodium hydroxide was dissipated within the chemical sector itself, mainly for acid neutralization. Therefore, we estimate that dissipative losses of caustic soda within the chemical industry was about 4.2 MMT.
Soda ash (sodium carbonate) is another alkali sodium chemical that was once manufactured synthetically by the Solvay process. However, sodium carbonate is now extracted from brines and evaporite deposits from the western United States. Of U.S. production in 1988, 2.117 MMT were exported (net). Domestic uses of sodium carbonate amounted to 7.6 MMT, of which 1 MMT was taken from stocks. Traditionally, about half of sodium carbonate use is in glass manufacturing. Other uses include in alkaline cleaners (12 percent), pulp and paper (2 percent), flue-gas scrubbing (2 percent), and water treatment (1 percent). The glass industry uses about 0.28 MT of soda ash per metric ton of glass produced.
Around 22 percent (1.9 MMT) of soda ash is used in other mostly inorganic chemical manufacturing. Important sodium chemicals that use sodium carbonate as a feedstock include STPP, of which 1988 production was 0.497 MMT (0.124 MMT Na); sodium silicate (0.736 MMT); and sodium cyanide (0.154 MMT). All of these sodium-containing chemicals are dissipated in final use.
Aluminum chemicals, notably alumina and aluminum sulfate, were mentioned above. However, alumina, although classed as an inorganic chemical, is really a feedstock for aluminum refining and need not be discussed further here. Aluminum sulfate, produced by reacting alumina with sulfuric acid, is used in the paper industry.
Silicon chemicals of importance include sodium silicate, silicones, and silanes, which are used in the production of ultrapure polycrystalline or amorphous silicon for semiconductors. The major inorganic silicon chemical is sodium silicate. Organic silicon chemistry is highly specialized and there are few data.
However, it is estimated that production of silicone resins for synthetic rubber amounted to 0.0947 MMT in 1990. Figures for 1988 were probably similar.
Compounds of iron, chromium, copper, lead, titanium, and zinc also have important chemical uses, especially for pigments. Titanium dioxide has already been mentioned in connection with chlorine. It is the most important metallic pigment, used for most exterior paints as well as in paper. U.S. production in 1988 was 0.926 MMT, mostly from ilmenite. For each ton of TiO2 produced, 1.2 tons of waste are generated, implying 1.11 MMT of waste from this source in 1988.
Iron oxide is a red pigment that comes largely from natural sources. Ferrous chloride and ferrous sulfate are by-products of steel pickling with hydrochloric and sulfuric acids, respectively. Ferrous chloride is used to some extent as a soil conditioner. The supply of ferrous sulfate, in low-grade forms, is much greater (2-4 MMT) than the demand for it. The compound is used to some extent to make iron oxide, to manufacture ferrites, as a catalyst, and in sewage treatment. However, much of it must be disposed of as waste.
Copper sulfate (0.0342 MMT) is the basis of most copper chemicals (fungicides, algicides, pesticides, catalysts, flotation reagents, etc.). It is made by reacting scrap copper with sulfuric acid. Its uses are dissipative, mainly in agriculture and wood preservatives.
Chrome-containing chemicals are mostly derived from sodium dichromate (0.145 MMT Cr2O3). Their largest use in 1988 was in wood preservatives, in combination with arsenic and copper. Use in preservatives accounted for 0.047 MMT of sodium dichromate equivalent, or 43 percent of 1991 demand (Roskill Ltd., 1991). Chromic acid is used for electroplating and metal treatment (15 percent of 1991 demand) and as the base for producing other chromium chemicals. Leather tanning accounted for 9 percent of U.S. dichromate demand in 1991. Tanning employs chromium (III) sulfate to protect the leather from attack by microorganisms. Chromium pigments (green, yellow) were a major use in the early 1980s, but dropped to just 8 percent of domestic demand by 1991. (Use as pigments in 1988 was about 0.014 MMT.) Virtually no copper or chromium was used in the manufacture of synthetic organic chemicals, except as catalysts. All chemical uses of chromium except for electroplating are essentially dissipative.
Lead sulfates and oxides are primarily pigments but are also the basis for other lead chemicals such as tetraethyl lead. They are still produced in fairly large, though decreasing, quantities. Lead oxides for pigments, including litharge, red lead, and white lead, accounted for 0.551 MMT, gross weight, of which 0.522 MMT was lead. Tetraethyl (TEL) and tetramethyl lead were once produced in very large quantities as gasoline additives. Their production and use have declined sharply since 1970 as a result of environmental regulation. Based on the ratio of ethyl dibromide to TEL in earlier years, we estimate that U.S. production of these additives in 1988 was approximately 0.035 MMT, almost all
of which was lead itself. These additives are classed as synthetic organic chemicals. Fuel uses of TEL are obviously dissipative.
The following zinc chemicals were produced in 1988: zinc oxide (directly from ore by the so-called French process), 0.0345 MMT; zinc sulfate, 0.013 MMT; and zinc chloride, 0.085 MMT. Zinc oxide is used mainly in tire manufacturing and as a pigment. Zinc chloride is mainly used as an electrolyte in dry cells. Minor quantities of zinc were used in pesticides and to manufacture catalysts. Except for these uses, zinc is not consumed in the production of synthetic organic chemicals. All final uses are dissipative.
Synthetic Organic Chemicals30
Most organic industrial chemicals are based on petrochemical (hydrocarbon) feedstocks. There are three basic categories: (1) paraffins (alkanes), which are saturated aliphatic (straight or branched-chain) hydrocarbons, the most important of which are methane, ethane, propane, isobutane, and n-butane; (2) olefins (alkenes), unsaturated aliphatics with one or more double bonds (e.g., ethylene, propylene, butylene, butadiene); (3) cyclics and aromatics (e.g., benzene, toluene, xylenes, cyclopentane, cyclohexane, and naphthalene). There is a fourth, miscellaneous, group of nonhydrocarbons, including oxygenated compounds of organic origin, cellulose, fatty acids, and related chemicals.
Some of the primary feedstocks of alkanes and aromatics, totaling 32.44 MMT in 1988, were derived from natural gas liquids (22.46 MMT), refinery off-gas (1.12 MMT), and naphtha (8.864 MMT) (International Energy Agency, 1991). Separate data are no longer collected for ethane, propane, and butane, probably due to the prevalence of mixed streams generated and converted within the petroleum refining sector.
For our purposes, it is convenient to exclude the C2-C4 alkanes (ethane, propane, isobutane, and n-butane) from consideration, because virtually all organic chemical products, except methanol, are derived from the corresponding olefins. The latter, in turn, are almost entirely used for chemical conversion. Primary products for chemical conversion, including methane, C2-C4 olefins, C5 and ''other" aliphatics (including methane), and aromatics, consumed in the United States amounted to approximately 63.6 MMT in 1988, including net imports of 7.64 MMT, according to the Bureau of Mines (1991). The remainder was derived from petroleum refineries (32.44 MMT, see previous section) and natural gas (23.5 MMT, estimated).
Not all of this material was converted into petrochemical products. For example, U.S. refineries produced 10.61 MMT of benzene, toluene, and xylenes (known as BTX), but Chemical and Engineering News (1997) lists only 4.08 MMT as "chemicals"; the implication is that 6.5 MMT were used by the refineries as gasoline additives. In addition, refineries produce significant quantities of hydrogen from the dehydrogenation process. We have no exact figures, but chem-
istry suggests that hydrogen would have accounted for about 10 percent of the input mass, or 6 MMT. Most of this was presumably used for other refinery operations, especially hydrogen reforming and hydrogen desulfurization. Some of the input material, mostly gas, was burned to provide energy for the dehydrogenation and cracking furnaces. Again, we have no precise data, but 5 percent (3 MMT) seems a reasonable estimate.
A further 1-2 percent of feedstocks (0.6-1.2 MMT) may have been lost as VOC emissions. Even so, we cannot fully account for the outputs. For example, it is not clear from the data whether natural gas consumed for ammonia production is or is not included. (Urea, made from ammonia, is included as an organic chemical product.) Methanol is certainly one of the primary products, but most methanol is imported, and the domestic product (1.85 MMT in 1988) could not account for very much of the 8.8 MMT of "missing" feedstocks.
To simplify somewhat, we consider the "true" feedstocks to the organic chemical industry to be C2-C5 olefins (33.35 MMT, approximately), aromatics (BTX and naphthalenes, 5.78 MMT, excluding the BTX diverted to gasoline additives), and methanol (4 MMT). The grand total of hydrocarbon feedstocks and methanol appears to have been 43.1 MMT in 1988. Some of this production, especially C4-C5 and higher-order aliphatics, was not actually used to manufacture other chemicals. Some was used as an octane booster in gasoline or as a solvent; some was converted to hydrogen, mostly used in the refining process, or to carbon black.31 However, most downstream synthetic organic chemicals are derived from the above-mentioned sources or the previously discussed inorganic intermediates. Olefins, in particular, are almost immediately and completely converted to polymers or other chemical intermediates such as alcohols and/or resins. In addition, we must account for miscellaneous organics such as glycerol (about 0.25 MMT, derived from animal or vegetable oils), fatty acids from vegetable oils used in liquid-detergent manufacture (0.735 MMT), and soluble cellulose used for cellulose acetate but not rayon (0.5 MMT).32
We also include specified fractions of the major inorganics discussed above. The latter include nitrogen chemicals, chlorine chemicals, sulfuric acid, and sodium hydroxide not used for other purposes and accounted for elsewhere. The last two reagents, in particular, are used in great quantities, but very little of the reactive element in either case is embodied in final products.
As regards chemicals, the situation is confused by imports, exports, and byproducts at various stages. In the case of ammonia, over 90 percent goes to fertilizers, explosives, synthetic fibers, plastics, and other identified inorganics. We can account for 0.737 MMT (N content) embodied in organic chemicals, plus about 0.16 MMT of associated process losses in 1988. So, a total of 0.9 MMT N was consumed in making synthetic organic chemicals in 1988, mainly plastics and fibers. Total weight of ammonia used would therefore have been about 1.1 MMT. For sulfur, the amount embodied in organic products was very small (0.08 MMT), but the amount used dissipatively in the industry was at least 0.6 MMT
and, thanks to the large amount unaccounted for, could have been as much as 1.9 MMT, of which as much as 1.45 MMT could have been in the form of sulfuric acid (Bureau of Mines, 1989). This would correspond to about 4.5 MMT of the acid. In the case of chlorine (see above), we saw that about 6.6 MMT were used within the chemical industry to make organic chemicals or final products. As regards caustic soda, it appears that 4.2 MMT were used for acid neutralization within the chemical industry. In addition, small amounts of fluorine (0.18 MMT), bromine (0.1 MMT), and phosphorus pentoxide (0.075 MMT) were used.33
Uncertainties in sulfuric-acid and caustic-soda requirements can be reduced, based on the knowledge that all acids and alkalis must be neutralized. Moreover, apart from small amounts of hydrochloric, nitric, and hydrofluoric acid, sulfuric acid is the dominant source of acidity (H+), while caustic soda and ammonium hydroxide are essentially the only sources of balancing hydroxyls (OH). However, ammonium sulfate is virtually all recovered in fertilizer, and both N and S have already been accounted for. Thus, virtually all other sodium and sulfur inputs must end up in waste streams (largely as sodium sulfate), because they are not embodied in products. The basic neutralization reaction is
2NaOH + H2SO4 →Na2SO4 + 2H2O.
The molecular weight of sulfuric acid is 98 g mole whereas the molecular weight of caustic soda is 40 g mole. Because the reaction requires two moles of caustic soda per mole of sulfuric acid, it would consume 1.22 mass units of sulfuric acid per unit of caustic soda. Thus, if 4.2 MMT of caustic soda was neutralized in the organic sector, we would have needed 5.15 MMT of sulfuric acid.34
Based on the above analysis, we argue that, in the synthetic organic chemicals sector, the ratio of sulfuric acid to caustic soda, in mass units, must be close to 1.22. Because the maximum amount of sulfuric acid available for organic synthesis processes, including acid unaccounted for, was 4.5 MMT, we conclude that not much more than 3.7 MMT of caustic soda could have been used in the same processes. (The remainder of the caustic, about 0.5 MMT, must have been used in the inorganic chemical sector.)
Adding these (Figure 8), we arrive at a grand total of 61 MMT of produced chemical inputs to organic synthesis in 1988. Oxygen is needed for a number of downstream oxidation processes, such as production of ethylene and propylene oxides; ethanol, isopropanol, and butanol; phthalic anhydride; terephthalic acid; and oxy-chlorination of ethylene to EDC.
A survey of the major products of the synthetic organic sector reveals that the oxygen content of final product chemicals averages close to 10 percent, which would amount to a total of about 4 MMT oxygen (O). We can account for 1.85 MMT O embodied in the input methanol. There is also some oxygen in cellulose and fatty acids. Some oxygen is carried into the reactions by the oxidizing agents nitric and sulfuric acid (HNO3 and H2SO4). But nitric acid is itself produced by
oxidation of ammonia, and sulfuric acid is the oxidized form of sulfur (dissolved in water). We estimated above that 1.45 MMT S, or 4.5 MMT of sulfuric acid, were utilized in organic synthesis in 1988. This would include 2.9 MMT O. We must also allow for 3.7 MMT NaOH used in organic synthesis processes, of which 1.4 MMT was oxygen. Altogether, this adds up to 6.15 MMT O, which is somewhat more than the amount actually embodied in final products.
In principle, no additional oxygen is needed, except to combine with carbon and/or hydrogen in the feedstock to generate energy to drive the endothermic syntheses. In practice, however, very little of the oxygen embodied in caustic soda or sulfuric acid ends up in the products. Rather, it ends up as water in the neutralization reaction. Thus, to arrive at a final oxygen content of 3.9 MMT, as indicated, we must assume that at least 2 MMT have been extracted from the atmosphere in various processes. This does not include the oxygen needed to oxidize all the missing mass to its final form, however.
Adding these, we arrive at a grand total of 61 MMT of produced chemicals and 2 MMT of oxygen as inputs to organic synthesis in the United States in 1988, not including oxygen that is used for combustion purposes and finishes as carbon dioxide. The major outputs, in terms of sales, of the organic chemicals industry amounted to 39.1 MMT in 1988 (and 39.5 MMT in 1989), not including urea. The categories are listed in Table 6.
Subtracting the weight of identified products from the weight of inputs, we find that the missing mass was around 23.9 MMT, not including the mass of any oxygen combined with carbon as process wastes. The situation is summarized graphically in Figure 8. The approximate composition of the waste stream can be estimated from the composition of the inputs; however, it is clear that water, sodium sulfate, and carbon dioxide must account for most of the waste. The remainder consists of various other salts, including some NaCl, and VOCs. A more detailed breakdown would be possible if we knew the inputs more accurately.
Primary Metals Smelting and Refining35
We have conceptually divided the processes of mining, concentration (winning), reduction (smelting), and refining. There are four stages of separation or recombination. The first two, being physical in nature, are assigned to the mining sector or the quarrying sector. They were discussed above. The last two, being chemical in nature, are assigned to the primary metals sector. At each separation stage, wastes are left behind and a purified product is sent along to the next stage. In principle, the wastes can be determined by subtracting outputs from inputs.
Unfortunately, from the analytic point of view, appropriate published data are rarely available. There are significant imports and exports of concentrates and crude metals (and even some crude ores), but trade data are often given in terms of metal content rather than gross weight. Domestic data are also incom-
TABLE 6
End-Use Organic Chemical Products: U.S. Production and Sales, 1989 and 1990 (million metric tons)
|
Production |
Sales |
||
Chemical Product |
1989 |
1990 |
1989 |
1990 |
TOTAL |
|
503.3880 |
|
39.1078 |
Dyes |
0.174 |
0.1170 |
0.146 |
0.1040 |
Organic pigments |
0.050 |
0.0530 |
0.043 |
0.0450 |
Medicinals |
0.130 |
0.1440 |
0.204 |
0.1070 |
Flavor and perfume materials |
0.064 |
0.0600 |
0.038 |
0.0370 |
Rubber processing chemicals |
0.176 |
0.1790 |
0.129 |
0.1360 |
Pesticides |
0.572 |
0.5570 |
0.461 |
0.4420 |
Thermosetting resins |
|
4.3095 |
|
3.1770 |
Thermoplastic resins |
|
25.2013 |
|
22.0939 |
Polymers for fibers |
|
2.3585 |
|
1.3791 |
Polymers (water soluble) |
|
0.3097 |
|
0.2647 |
Elastomers |
|
2.2331 |
|
1.5551 |
Plasticizers |
|
0.8907 |
|
0.8265 |
Surfactants |
|
5.8487 |
|
2.7181 |
Antifreeze |
0.920 |
0.9009 |
|
0.9000 |
Chlorofluorocarbons |
0.417 |
0.3083 |
|
0.3000 |
Solvents |
|
|
|
1.2000 |
Chelating agents |
|
0.1372 |
|
0.1015 |
Fuel additives |
|
4.2247 |
|
1.9356 |
Lube oil and grease additives |
|
0.3872 |
|
0.3436 |
Textile chemicals (excluding surfactants) |
|
0.0224 |
|
0.0198 |
Miscellaneous chemicals |
|
2.0966 |
|
1.4219 |
SOURCE: International Trade Commission (1992). |
plete, due to information withheld for proprietary reasons. Thus, in a number of cases, we have been forced to work back from smelting or concentration process data to estimate the input quantities of concentrates. Our summary was given in Table 3. It excluded ferroalloys, of which U.S. production was about 1 MMT, because of the extreme complexity of the subsector.
Inputs to the U.S. primary metals sector consist of concentrates (either produced in the mining sector or imported), fuels, fluxes, and processing chemicals. Because we have accounted for inputs to and wastes from fossil fuel combustion in an above section, those quantities are not included in our accounting of wastes from primary metals smelting and refining. CO is a major pollutant of smelting processes, but it results from partial oxidation, which is later completed in the atmosphere. (Thus, the materials-balance approach is not applicable for estimating CO emissions.) Major purchased inputs, other than concentrates, are fluxes. The most important are limestone and dolomite. In 1988, approximately 9.6
MMT of limestone and dolomite were used, mostly in blast furnaces. Data published by the Bureau of Mines indicate that these materials were calcined on site and consumed as lime (4.8 MMT). Other inputs reported by the Bureau of Mines include salt (0.33 MMT), manganese ore (0.123 MMT), and fluorspar (0.137 MMT).
The production of primary metals from concentrates is normally accomplished by carbothermic reduction (smelting with coke) or electrolysis. By far the major product by weight is pig iron. U.S. blast-furnace output in 1988 was 50.9 MMT. This material has an iron content of 94 percent and it is almost entirely used for carbon steel production by the basic oxygen process. (There was a small amount of open-hearth production in 1988, which has now ended. Electric steel "minimills" use scrap almost exclusively.)
Blast furnace inputs in 1988 included about 3 MMT of scrap iron and steel, whereas sinter also utilized about 6 MMT of upstream reverts (dust, mill scale). Therefore, accounting for the virgin ore is somewhat complex. However, the iron content of U.S. ores in 1988 was reported as 57.515 MMT. Blast furnace inputs (pellets) averaged about 63 percent iron, 5 percent silica, 2 percent moisture, and 0.35 percent other minerals (phosphorus, manganese, alumina). The remainder was oxygen.
In the reduction process, the oxygen combines with carbon (actually carbon monoxide) from the coke. About 0.5 MT of coke was used per metric ton of pig iron, along with 0.142 MT of miscellaneous materials, mostly fluxes (lime and limestone) for the sinter plants and to make the molten slag flow easily. Slag consists of the silica and other nonferrous minerals in the sinter and pellets and the materials in the fluxes. Total iron blast furnace slag production in the United States was 14.2 MMT, or 0.28 MT of slag per metric ton of pig iron. However, slag is no longer considered a waste, because virtually all slag produced is marketed for a variety of uses. Subsequent refining of pig iron and scrap iron to carbon steel is done in a later refining stage, normally the basic oxygen furnace. Steel furnaces produced an additional 5 MMT of slag in 1988.
As noted, the oxygen in the iron-bearing concentrates reacts in the blast furnace with carbon monoxide. The reduction process requires excess CO, so the emissions (blast-furnace gas) consist mostly of unreacted CO. Although combustible, it is of relatively low heating value. Currently, most blast-furnace gas is used elsewhere in the integrated steel complex as fuel (e.g., for preheating blast air), although some is used as fuel by nearby electric power plants. The capture of gaseous emissions from blast furnaces is not 100 percent efficient, so some CO escapes. However, considering the iron/steel process as a whole, all of the carbon (from coke) is eventually oxidized to CO2. In 1988, the steel industry accounted for 182 MMT of CO2 from coke, which is included in the grand total from fossil fuel combustion, discussed below. (In addition, the steel industry used some other hydrocarbon fuels.)
Coke ovens and steel-rolling mills are significant sources of hazardous wastes, even though the coke-oven gas is efficiently captured for use as fuel, and
about 0.055 MMT of ammonium sulfate (N content) is produced as a by-product. This material is used as fertilizer. Coke is cooled by rapid quenching with water, and some tars, cyanides, and other contaminants are unavoidably produced. Unfortunately, materials balances cannot be used to estimate these wastes. However, they probably constitute a significant fraction of both water and airborne wastes from the primary iron and steel sector.
Also, in the rolling process, steel is cleaned by an acid bath (pickling), resulting in a flow of dilute waste water containing ferrous sulfate or ferrous chloride, depending on the acid used. The excess acid is usually neutralized by the addition of lime. In 1988, about 0.215 MMT of 100 percent sulfuric acid (0.074 MMT S content) was used for this purpose, producing 0.25-0.30 MMT of ferrous sulfate mixed with calcium sulfate. Ferrous sulfate can, in principle, be recovered for sale to the water treatment industry. However, the market is insufficient to absorb the quantity potentially available, and most of it ends up as waste.
Light metals, mainly aluminum and phosphorus, are reduced electrolytically. The oxygen in the alumina reacts with a carbon anode made from petroleum coke. The reaction emits 0.65 MT of CO2 per metric ton of primary aluminum produced. In addition, primary aluminum plants emit about 0.02 MT of fluorine per metric ton of aluminum, partly as HF and partly as particulates, the latter due to the breakdown of cryolite (the electrolyte used in the process, an aluminumsodium fluoride) at the anode. Total airborne emissions (3,944 MMT) from primary aluminum production in the United States were, thus, 2,564 MMT of CO2 (already counted), 0.08 MMT of fluorides, and about 0.17 MMT of particulates (Al2O3).
In the case of heavy metals from sulfide ores (copper, lead, zinc, nickel, molybdenum, etc.), the smelting process is preceded by, but integrated with, a roasting process whereby the sulfur is oxidized to SO2. Roughly 1 MT of sulfur is associated with each MT of copper smelted, 0.43 MT of sulfur per MT of zinc, and 0.15 MT of sulfur per MT of lead. Ninety percent of this sulfur is captured and immediately converted to sulfuric acid. In 1988, 1.125 MMT (S content) of by-product sulfuric acid were produced at U.S. nonferrous metal refineries, as follows: copper (0.946 MMT S), zinc (0.136 MMT S), and lead/molybdenum (0.043 MMT S). In terms of sulfuric acid (100 percent H2SO4), 3.54 MMT of byproduct acid were produced.
In the case of copper, most of the acid (1.2 MMT) was used by mines for heap leaching copper. Leaching now accounts for about 30 percent of copper concentrates produced in the United States. Leached copper sulfate is subsequently reduced electrolytically, without an intermediate smelting stage. In the case of copper smelting, typical concentrates fed to the roaster/smelter consist of about 35 percent Cu, 35 percent S, and 30 percent other minerals. In addition, about 0.25 MT of limestone flux is added per ton of blister copper. Thus, slag production amounts to roughly 0.55 MT per metric ton of primary copper, or 0.77 MMT in 1988.
In the case of zinc, a typical concentrate would be about 55 percent Zn, 27 percent S, and 16 percent other minerals. For lead, the corresponding numbers appear to be about 60 percent Pb, 9 percent S, and 21 percent other. Thus, assuming flux per unit of slag ratio to be the same as for copper (1.2:1), slag output should have been roughly 0.3 MT per metric ton for zinc and 0.38 MT per metric ton for lead. This implies total slag output of 0.06 MMT for zinc smelting and 0.14 MMT for lead smelting. Total slag production for the three main nonferrous metals was thus roughly 1 MMT. Carbon monoxide and carbon dioxide emissions are not known exactly, but they are quite small in comparison with other sources. The waste numbers for other metals are relatively insignificant.
Altogether, based on mass-balance considerations, we estimate smelting and refining wastes for primary metals, including CO2, to have been 43.4 MMT in 1988, including the weight of limestone, manganese, calcium fluorite, and other materials used in the blast furnaces and refineries. (This includes about 14.2 MMT of iron, or blast-furnace, slag, although most of this material is marketed commercially, mainly for road ballast.) In addition, there were about 5.2 MMT of steel-furnace slag, a denser material with a fairly high iron content.
As noted above, much of the sulfur in sulfide copper, lead, zinc, and molybdenum ores is also recovered for use and sold as sulfuric acid (1.125 MMT S content in 1988). Subtracting the blast furnace slag and the by-product sulfuric acid, we get 28.1 MMT residual waste. Of this, only about 1 MMT was solid nonferrous slag; the rest was the oxygen content of the original ores combined with carbon (from coke), released as CO2.36 We have not included the wastes from coking, which we have not estimated. The major airborne emissions other than CO2 are probably CO and particulates. In both cases, blast furnaces are the major sources. The coking quench waters and some spent acids used for pickling constitute the major waterborne wastes.
Mass flows and wastes for the metallic mineral processing industries and the metallurgical industries, taken together, are summarized in Figure 9 (ferrous) and Figure 10 (nonferrous). These values are normalized to U.S. production of the refined metals. Some of the flows are imputed from others. For example, pig iron (94 percent Fe) contains roughly 6 percent C, which implies a carbon content of 3 MMT. The oxygen required to burn this carbon away was therefore approximately 8 MMT, implying a CO2 output of 11 MMT for steel production in 1988. In the case of iron blast furnaces, we assumed that all of the input coke, less the 3 MMT of C embodied in pig iron, was converted to CO2. This consumed 63.4 MMT 02 and generated 87.1 MMT CO2. However, some oxygen was captured from the iron oxide in the ore. So, balancing inputs and outputs, we calculate that the additional oxygen taken from the air must have been 31.5 MMT. Scrap flows are very approximate, partly because scrap industry statistics are poor and partly because we have lumped stock adjustments and scrap flows for convenience.
For comparison, Science Applications International Corporation (1985) estimated the 1983 nongaseous wastes from iron and steel production at 6 MMT and
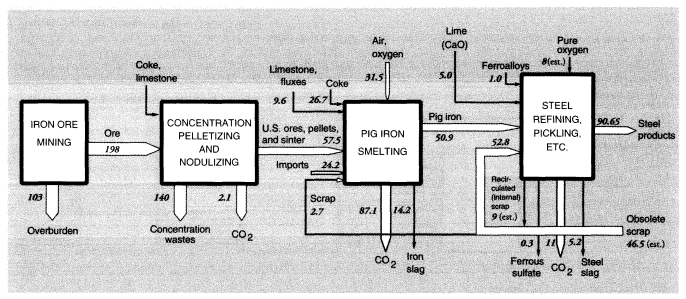
Figure 9
Mass flows in the U.S. iron and steel sectors, 1988 (million metric tons). Calculated by the authors from various, sources, including Bureau of Mines (1988, 1989) and United States Environmental Protection Agency (1991). NOTE: Scrap consumption in iron and steel production is probably underestimated by up to 4 million tons. Recirculated scrap may be underestimated by a similar amount.
from nonferrous metals at 6.5 MMT. Their estimates were not specifically designated as dry, so some water content can be presumed. The EPA estimates airborne emissions from the primary metals sector as a whole to be 2.8 MMT, including particulates and CO but not including CO2 (United States Environmental Protection Agency, 1991). Both sets of estimates are roughly consistent with our calculations.
Stone, Clay, and Glass37
As discussed above, overburden and concentration losses for nonmetallic minerals other than phosphorus in 1988 amounted to 47.1 MMT and 36.5 MMT, respectively. The outputs of the stone, clay, and glass sector include refractories, glass, and portland cement. All three are durable products used in structures or long-lived products. We do not have detailed quantitative data on glass production. As for clays, domestic production in 1988 was 43.9 MMT. Production of clay and refractory products, including clay used in Portland cement, was virtually identical. Some of these uses (e.g., fillers, binders, absorbents, drilling mud, filters) are essentially dissipative.
Portland cement manufacture is an important industry. Total U.S. production in 1988 was 66.5 MMT. Most of the input materials were natural minerals already discussed (limestone being by far the most important, 73 MMT), but small quantities of fly ash and blast-furnace slag also were used. Total nonfuel inputs were 11 MMT, and the mass lost in cement manufacturing was 44.5 MT. The major fuel consumed was coal (9.5 MMT), although some plants used oil or gas. Emissions are primarily CO2 and particulates. The total weight of emissions from fuel was already counted above. However, CO2 emissions from limestone calcination created an additional 35 MMT, or about 10 MMT C content, in waste. This still leaves nearly 10 MMT of missing mass. It is likely that some of this consists of particulate emissions from cement kilns, although this is probably not the complete explanation. There may be some internal recycling.
Lime (CaO) is made by calcining limestone. In 1988, U.S. production was 13.2 MMT (consuming 29.5 MMT of limestone and releasing 16.3 MMT CO2 to the atmosphere). Uses of lime are extremely diverse and not well documented. The use of lime to treat stack gas was mentioned above. In many cases, limestone can substitute for lime (e.g., in glass manufacturing, soil stabilization, desulfurization). It must be emphasized that calcination of limestone releases CO2 at a rate of 1.2 MT per metric ton of CaO.
It appears that the major waste emissions from this sector, exclusive of losses in quarrying and concentration, are primarily related to combustion of fossil fuels and calcination of limestone and gypsum, which yields CO2. However, Science Applications International Corporation (1985) estimated dry wastes from the sector to be more than 18 MMT in 1983. EPA's latest estimate of airborne emis-
sions, primarily particulates and CO, is about 1 MMT (United States Environmental Protection Agency, 1991).
We have no estimate of water use by the stone, clay, and glass sector. However, EPA estimated total wet wastes from the sector to be 560 MMT (United States Environmental Protection Agency, 1986). This seems quite high, given that most processes in the sector are dry.
Fossil Fuel Consumption38
Combustion of fossil fuels produces a variety of wastes. This is particularly true for coal. On the average, U.S. coal has a sulfur content of 1.9 percent; coal burned by electric utilities averages 2.3 percent sulfur, whereas coking coal is 1 percent sulfur. The latter is mostly recovered as ammonium sulfate. Coal burned in the United States emits about 16 MMT of sulfur (32.1 MMT SO2). Most of this sulfur dioxide is released to the atmosphere.
In 1988, 1.24 MMT of lime (CaO) and 1.035 MMT of limestone (CaCO3) were sold for use in removing sulfur from furnace stack gases. The limestone was equivalent to 0.495 MMT of lime. Because CaO has a molecular weight of 56 and SO2 has a molecular weight of 64, the total amount of limestone and lime used in scrubbers accounted for only 1.96 MMT of sulfur dioxide, or about 6 percent of the total emitted. None of the sulfur from coal burning was recovered for further use. (It is disposed of in landfills as a mixture of wet calcium sulfite CaSO3 and calcium sulfate CaSO4.) EPA estimated that flue gas desulfurization by utilities produced 14.4 MMT of solid wastes in 1984 (United States Environmental Protection Agency, 1988, 1991). The mineral content of these wastes, even in 1988, was evidently no more than 3.7 MMT. The remainder was presumably water of hydration. (The mineral gypsum has the formula CaSO4 · 2H2O.)
If all the sulfur in U.S. coal were to be captured by wet scrubbers using lime, total U.S. lime production would triple to 26 MMT, which would require an additional 55 MMT of limestone to be quarried. All of it would, of course, be converted almost directly into a waste stream.
Coal contains a small but significant percentage of fuel-bound nitrogen (about 1 unit per 68 units of carbon). Most of this is emitted as nitric oxide (NO) but some may be emitted as nitrous oxide (N2O), one of the greenhouse gases. However, experts disagree about the amount of nitrous oxide produced by this process. More important, coal combustion in high-temperature boilers, used to generate electric power, produces a significant quantity of NOx emissions, about 10 MMT/yr (United States Environmental Protection Agency, 1986). Virtually all anthropogenic NOx (about 20 MMT/yr in 1980 and probably a similar amount in 1988) is attributable to the burning of fossil fuel.
Coal also contains significant quantities of mineral ash, equivalent to mineral shale. The average ash content of U.S. coal, as burned, is approximately 10 percent (Torrey, 1978). Actually, utilities alone seem to have collected and dis-
posed of 62 MMT of ash in 1983. Assuming constant proportions of ash in coal used and complete ash recovery, the weight of disposed ash would have risen to 76 MMT by 1988, which would account for almost all of the ash in the utility coal. However, although the efficiency of recovery of fly ash from electrostatic precipitators is in the neighborhood of 99.8 percent for the most modern units, some utilities are not so well equipped. Fly ash not captured in 1988 probably amounted to at least 1 MMT. The ash content of coking coal, which is selected in part for its low ash content, ends up in metallurgical slag. The ash content of coal used as a fuel in the cement industry ends up as part of the cement itself. In fact, the cement industry also uses a small amount of fly ash as a raw material. Coal ash contains significant quantities of heavy metals. Although most fly ash is captured, the waste ash must be disposed of somehow. Moreover, the more volatile trace metals such as arsenic and mercury still escape as vapor and recondense downwind of the stack.39
Finally, the carbon in coal, along with the carbon in other fuels, is converted by combustion into CO2. The Carbon Dioxide Information Analysis Center (1990) at Oak Ridge National Laboratory estimated that the carbon content of these fuels was 1,288.6 MMT, or 84.7 percent. Of this, 493 MMT was from solid fuels (coal), generating 1,810 MMT CO2. This includes the CO2 from carbothermic reduction processes using coke.
With the exception of electric power generation, most fuels are petroleum products or natural gas. Natural gas is mostly used for domestic purposes and space heating, although some is used in industry. Petroleum products are mainly used for transportation, although some heavy oils are used for industrial boilers or electric power production. The transportation system is of interest because there are so many complex mass flows involved, other than the straightforward consumption of fuel. We summarize this system, for private automobiles only, in Figure 11.
The sum total of all fossil fuels consumed in the United States in 1988 was 1,521 MMT (Table 5). We assume that all of the fossil fuel carbon was converted to CO2 (4,726 MMT in 1988), not including calcination processes (lime and cement manufacturing), which are counted separately.
Combustion processes also result in some releases of methane to the atmosphere, but more methane escapes to the atmosphere during production and transmission. One study allocates 11.86 MMT of methane releases in the United States in 1988 to all of these activities together (Subak et al., 1992). The study does not provide a breakdown for the United States among production, transportation, and combustion. However, for the world as a whole, the breakdown was coal mining (62 percent), oil and gas extraction (14.8 percent), gas distribution (17 percent), firewood combustion (4 percent), and other fossil fuel combustion (2.3 percent). For the United States, firewood combustion would be a negligible source of methane, coal would be less important than it is globally, and natural gas would be more important than it is globally.
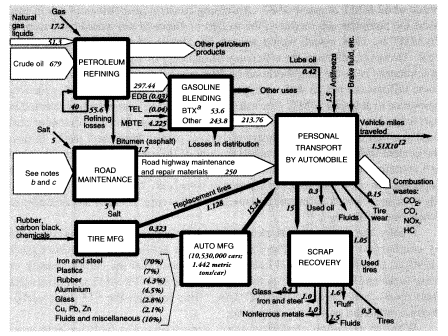
Figure 11
Mass flows associated with private automobiles in the United States, 1988 (million metric tons). Calculated by the authors from various sources, including International Energy Agency (1991), Bureau of Mines (1988), and Ecoplan International (1992).
aBenzene-toluene-xylente.
bThirty-three percent of total road/highway expenditure is for maintenance and repair. Materials use per dollar is equal for new construction and for maintenance and repair. Fifty percent of all road/highway depreciation is attributable to automobile use.
cTotal estimated materials used for road/highway construction, repair, and maintenance: bitumen, 16 MMT: Portland cement, 10 MMT; steel, 35 MMT; slag, 15 MMT; sand and gravel, 600 MMT; and crushed stone, 840 MMT.
Summary
It may be interesting to summarize our results by waste category as well as by industry. Overburden moved by mining, mostly stripping, amounted to over 6,800 MMT in 1988. By contrast, topsoil loss in agriculture was on the order of 1,500 MMT. (In addition, the construction industry probably moves comparable amounts of topsoil.) Mineral concentration activities, mostly by froth flotation, produced waste (tailings) on the order of 900 MMT (600.6 MMT metals, 140.7 MMT nonmetals, 47 MMT coal cleaning, 57 MMT drilling wastes, 57.2 MMT
phosphates and alumina) dry weight. In addition, about 3,600 MMT of water was used for flotation, most of which was evaporated in ponds, leaving semisolid sludges. Waste water discharged into rivers and streams by the mining industry amounted to 2,840 million gallons per day, or 3,900 MMT for the year.
By contrast, the weight of solid wastes from metallurgical conversion and fossil fuel combustion processes, including metallurgical reduction (smelting), amounted to only about 146.4 MMT. We have included in this category 76 MMT of fly ash and bottom ash from thermal power generators and 14.4 MMT of flue gas desulfurization waste but excluded 14.4 MMT of iron/steel slag that have commercial uses.
Organic pretreatment wastes are more difficult to account for. Crop residues, mostly recycled to land, amounted to about 360 MMT. Timber residues from logging operations amounted to 155 MMT, mostly burned or recycled to forest soils. (In some countries, both agricultural and timber residues are collected and burned as fuel, but this is relatively rare in the United States.) About 180 MMT (50 percent dry) of animal wastes—manure, urine, and dead animals—were produced, of which an estimated 155 MMT were probably recycled to cultivated land and the remainder lost in other unspecified ways. An additional 110 MMT of organic wastes (50 percent dry) were generated in the food processing sector and disposed of in various unspecified ways, including waterways. About 5 MMT were lost in the wood products and pulp and paper sectors.
Gaseous combustion products constituted another very large waste stream. We estimate gross emissions of 5,046 MMT CO2, of which 4,726 MMT were from fossil fuel combustion. However, thanks to a take-up of 1,002 MMT by the agricultural sector and 368 MMT by the forestry sector, net emissions of CO2 were 3,759 MMT. (By the same token, industrial activities, mainly fuel combustion, consumed 5,393 MMT of oxygen, whereas agriculture and forestry produced 891 MMT of oxygen, for a net consumption of 4,732 MMT.) Other gaseous emissions included 32 MMT SO2 from coal and EPA's estimate of 20 MMT NOx from fossil fuel combustion. Our methodology is not well suited to estimating fugitive or particulate emissions. However, we note that petroleum refineries may have emitted as much as 4.3 MMT of hydrocarbons that are not accounted for anywhere else.
Process water contaminated by acids or other wastes was also emitted in significant quantities by the petroleum refining and metallurgical sectors. The quantitative values discussed above are summarized in Table 7.
TABLE 7 Summary of Estimated U.S. Dry-Waste Streams, Excluding Water, 1988 (million metric tons)
|
Lost Mass |
|||||||||
|
Dry Organic |
Dry Inorganic |
Emission to Air |
|||||||
Sector |
Combustible |
Noncombustible |
Soil Overburden |
Concentration Wastes |
Process Wastes (ash, slag, etc.) |
H2O |
CO2 |
O2 |
CH4, VOC |
N,S |
Agriculture |
+360a |
25 |
1,500 |
|
|
-1,027 |
-1,002 |
-156 |
0.7 |
12(N) |
|
+155b |
|
|
|
|
+202 |
+213 |
+685 |
|
|
Food processing |
? |
? |
|
|
|
66 |
6.8 |
|
|
|
|
|
|
|
|
|
(+19)c |
(+29.4)c |
(-21.3)c |
|
|
Forestry, pulp, paper |
4.9 |
|
|
|
18.1 |
-545 |
-368 |
-74 |
|
|
|
|
|
|
|
|
+314 |
+132 |
+206 |
|
|
Mining |
|
|
9625d |
600.6d |
|
|
|
|
|
|
|
|
|
275.7e |
140.7e |
|
|
|
|
|
|
|
|
|
5,600f |
47f |
|
|
|
|
9.8 |
|
|
|
|
6-7g |
57g |
|
|
|
|
|
|
Petroleum refiningh |
|
|
|
|
|
(76.5)c |
(165)c |
(-120)c |
2.0 |
|
|
Lost Mass |
|||||||||
|
Dry Organic |
Dry Inorganic |
Emission to Air |
|||||||
Sector |
Combustible |
Noncombustible |
Soil Overburden |
Concentration Wastes |
Process Wastes (ash, slag, etc.) |
H2O |
CO2 |
O2 |
CH4, VOC |
N,S |
Chemicals |
|
|
|
57.2 |
22.9i |
|
|
|
1.0 |
|
Primary metals |
|
|
|
|
0.3j |
|
|
|
|
0.3 (S) |
|
|
|
|
|
3.0k |
|
|
|
|
|
Stone, clay, glass |
|
|
|
|
10 |
|
51.3 |
|
|
|
Fossil fuel and |
|
|
|
|
92 |
2,088 |
4.726 |
-5.393 |
6 |
10 (N) |
electric power |
|
|
|
|
|
|
|
|
|
14 (S) |
TOTAL |
520+? |
25+? |
8,346.7 |
902.5 |
146.3 |
1,098 |
3,759.1 |
-4,732 |
19.5 |
36.3 |
a Crop residues, normally recycled to land. b Animal manure, normally recycled to land. Not including emissions from free-ranging animals. c Values in parentheses are emissions or consumption ( - ) from energy recovery. These values are not included in totals. d Metal ore mining in the United States. e Nonmetallic mineral mining in United States, excluding alumina and phosphate concentration wastes. f Coal mining, not including coke-oven emissions. g Petroleum and gas drilling. h Including natural gas processing and transmission. H2O, CO2, and O2 emissions (consumption) based on combustion of process wastes for energy. i Process wastes of the organic chemical sector are partly combustible and partly incombustible. Detailed breakdown not available. j Iron and steel slag are by-products with many uses. concentration wastes are included with the mining sector. k CO2 emissions are included with fuel combustion NOTES: Plus ( + ) signs refer to production. Minus ( - ) signs refer to consumption. VOC = volatile organic chemical. |
Notes
-
1.
Where specific citations are not given, basic data for this section are from Hoffman (1991), United States Department of Agriculture (1992), and Bureau of Census (1988).
-
7.
See United Nations Statistical Office (1988) tables on "Lard," ISIC 3111-31, and "Oils and fats of animals, unprocessed," ISIC 3115-07.
-
8.
See United Nations Statistical Office (1988) table on "Hides, cattle and horses, undressed—total production," ISIC 3111-311. This refers to fresh weight, prior to tanning.
-
10.
Unless otherwise specified, data in this section are from Bureau of the Census (1991).
-
11.
These data are essentially consistent with Ulrich (1990); however, Ulrich's table 51 appears inconsistent with Ulrich's table 7 as regards imports and exports of pulp. Table 7 includes pulp imputed to downstream paper and paperboard products. We account for imports and exports of downstream products separately.
-
13.
Of this, 5.4 MMT were exported and 0.6 MMT was used for other purposes (Bureau of the Census, 1991, table 1194).
-
14.
Actually, this is a lower limit, because it includes only inorganic materials (kaolin, alum, etc.) that we have been able to account for explicitly from published sources.
-
the enzyme. Therefore, the current challenge is to bioengineer a strain that completely lacks the gene.
-
19.
Data on materials handled are from Bureau of Mines (1989, Volume 1, tables 10, 11). Other data in this section on metals and minerals come from individual chapters in the same source.
-
21.
Data on materials handled are from Bureau of Mines (1989, Volume 1, tables 10, 11). Other data in this section on metals and minerals come from individual chapters in this same source.
-
23.
All data in this section are extracted from International Energy Agency (1991, pp. 664-665).
-
24.
Light ends are compounds with boiling points in the range of butane (about 0 °C) and below. Methane and the light alkanes (C2-C 4) fall into this category.
-
26.
Unless otherwise specified, the basic data for this section are from Bureau of Mines (1989).
-
27.
Phosphorus pentoxide dissolved in water is phosphoric acid, the active ingredient in most phosphate fertilizers (e.g., superphosphates). It is not used, generally, in pure form.
-
29.
Sodium chlorate used to bleach paper pulp is almost unique among chlorine chemicals. It is not manufactured from elemental chlorine but is made directly from sodium chloride (salt).
-
33.
Although about 0.2 MMT of phosphorus was used in detergents, most of it was inorganic: STPP and tetrasodium pyrophosphate.
-
35.
Unless otherwise specified, data for this section are from Bureau of Mines (1989, 1991).
-
36.
Assuming that the iron in ore is mostly in the form Fe2O3, the 57.5 MMT of iron content in ore (1988) would be combined with 25.55 MMT of oxygen.
-
37.
Unless otherwise specified, data for this section were taken from United States Bureau of Mines (1989).
-
38.
Unless otherwise specified, data for this section were taken from United States Bureau of Mines (1989).
References
Brown, L. R., and E. C. Wolf. 1984. Soil Erosion: Quiet Crisis in the World Economy. Worldwatch Paper (60). Washington D.C.: Worldwatch Institute.
Bureau of Mines. 1987. Minerals Yearbook. Washington, D.C.: U.S. Government Printing Office.
Bureau of Mines. 1988. Minerals Yearbook. Washington, D.C.: U.S. Government Printing Office.
Bureau of Mines. 1989. Minerals Yearbook. Washington, D.C.: U.S. Government Printing Office.
Bureau of Mines. 1991. Minerals Yearbook. Washington, D.C.: U.S. Government Printing Office.
Bureau of the Census. 1983. Census of Manufactures. Washington, D.C.: U.S. Government Printing Office.
Bureau of the Census. 1988. Statistical Abstract of the United States: 1988, 108 ed. Washington, D.C.: U.S. Government Printing Office.
Bureau of the Census. 1990. Statistical Abstract of the United States: 1990, 110 ed. Washington, D.C.: U.S. Government Printing Office.
Bureau of the Census. 1991. Statistical Abstract of the United States: 1991, 111 ed. Washington, D.C.: U.S. Government Printing Office.
Carbon Dioxide Information Analysis Center. 1990. Trends '90: A Compendium of Data on Global Change. Oak Ridge, Tenn.: Oak Ridge National Laboratory.
Chemical and Engineering News. 1992. Chemical earnings. Volume 70.
Chemical and Engineering News. 1997. Chemical earnings: Japanese chemical producers generally fared well in 1996, but petrochemicals ate into profits. Volume 75.
Crutzen, P. J. 1976. The nitrogen cycle and stratospheric ozone. Paper presented at the Nitrogen Research Review Conference, National Academy of Sciences, Fort Collins, Colo., October 12-13.
Crutzen, P. J., I. Aselman, and W. Seiler. 1986. Methane production by domestic animals, wild ruminants, other herbivorous fauna, and humans. Tellus 38B:271-284.
Deevey, E. C. 1970. Mineral cycles. Scientific American 223:148-158.
Ecoplan International. 1992. New Developments in Tire Technology: Technological Change and Intermaterials Competition in the 90s and Beyond. Multi-Client Industry Report. Paris: Ecoplan International.
Gaines, L. L., and A. M. Wolsky. 1981. Energy and Materials Flows in Petroleum Refining. Technical Report (ANL/CNSV-10). Argonne, Ill.: Argonne National Laboratory.
Hoffman, M. S., ed. 1991. The World Almanac and Book of Facts. New York: Scripps-Howard.
Holmbom, B. 1991. Chlorine Bleaching of Pulp: Technology and Chemistry, Environmental and Health Effects, Regulations and Communication. Case study. April. Turku/Abo, Finland: Abo Akademi.
International Bank for Reconstruction and Development (IBRD). 1980. Environmental Considerations in the Pulp and Paper Industry. Washington, D.C.: IBRD.
International Energy Agency. 1991. Energy Statistics of OECD Countries 1980-1989. Paris: Organization for Economic Cooperation and Development.
International Trade Commission. 1992. Synthetic Organic Chemicals 1992. Washington, D.C.: U.S. Government Printing Office.
LeBel, P. G. 1982. Energy Economics and Technology. Baltimore, Md.: The Johns Hopkins University Press.
Lowenheim, F. A., and M. K. Moran. 1975. Faith, Keyes, and Clark's "Industrial Chemicals," 4th ed. New York: Wiley-Interscience.
Manzone, R. 1993. PVC: Life-Cycle and Perspectives. Urbino, Italy: Commett Advanced Course.
Obernberger, I. 1994. Characterization and utilization of wood ashes. Technical paper. Institute of Chemical Engineering, Technical University, Graz, Austria.
Roskill Ltd. 1991. Chromium. London: Roskill Ltd.
Schlesinger, W. H. 1991. Biogeochemistry: An Analysis of Global Change. New York: Academic Press.
Schlesinger, W.H., and A.E. Hartley. 1992. A global budget for atmospheric NH3. Biogeochemistry 15:191-211.
Science Applications International Corporation (SAIC). 1985. Summary of Data on Industrial Nonhazardous Waste Disposal Practices. Washington, D.C.: SAIC.
Smil, V. 1993. Nutrient flows in agriculture: Notes on the complexity of biogeochemical cycles and tools for modeling nitrogen d D. voand phosphorus flows in agroecosystems. Undated working paper.
Subak, S., P. Raskin, ann Hippel. 1992. National Greenhouse Gas Accounts: Current Anthropogenic Sources and Sinks. Boston, Mass.: Stockholm Environmental Institute.
Torrey, S., ed. 1978. Coal Ash Utilization: Fly Ash, Bottom Ash and Slag. Pollution Technology Review Series, No. 48. Park Ridge, N.J.: Noyes Data Corp.
Ulrich, A. H. 1990. U.S. Timber Production, Trade, Consumption and Price Statistics 1960-88. Miscellaneous Publication (1486). U.S. Forest Service. Washington, D.C.: U.S. Forest Service, U.S. Department of Agriculture.
United Nations Statistical Office. 1988. Industrial Statistics Yearbook: Commodity Production Statistics 1988 II. New York: United Nations.
United States Congress, Office of Technology Assessment. 1984. Wood Use: U.S. Competitiveness and Technology, Vol. II-Technical Report. OTA-M-224. Washington, D.C.: Office of Technology Assessment.
United States Congress, Office of Technology Assessment. 1992. Managing industrial solid wastes from manufacturing, mining, oil and gas production, and utility coal combustion. Background paper (OTA-BP-O-82). Washington, D.C.: Office of Technology Assessment.
United States Department of Agriculture. 1990. Agricultural Statistics. Washington, D.C.: U.S. Government Printing Office.
United States Department of Agriculture. 1991. Agricultural Statistics. Washington, D.C.: U.S. Government Printing Office.
United States Department of Agriculture. 1992. Agricultural Statistics. Washington, D.C.: U.S. Government Printing Office.
United States Department of Commerce. 1992. Current Industrial Reports: Inorganic Chemicals. Washington, D.C.: U.S. Department of Commerce.
United States Department of Energy. 1980. Technology Characterizations. Technical Report DOE/ EV-0061/1. Washington, D.C.: U.S. Department of Energy.
United States Environmental Protection Agency, Office of Solid Waste. 1986. Waste Minimization Issues and Options. NTIS PB-87-114369 (EPA-530-SW-86-041). Washington, D.C.: U.S. Environmental Protection Agency.
United States Environmental Protection Agency. 1988. Solid Waste Disposal in the United States. Report to Congress (EPA-530-SW-88-01 1). Washington, D.C.: U.S. Environmental Protection Agency.
United States Environmental Protection Agency, Office of Solid Waste. 1991. 1987 National Biennial Report of Hazardous Waste Treatment, Storage and Disposal Facilities Regulated Under RCRA. NTIS PB-87-114369 (EPA-530-SW-91-061). Washington, D.C.: U.S. Environmental Protection Agency.